Spyderman
|
posted on 20/4/04 at 12:15 PM |
|
|
quote: Originally posted by NS Dev
Snip.
, but will point out that the caustic is available from common shops as a household chemical (won't say what/where due to the cautions above!!)
so anybody could use it and not realise the seriousness of the dangers.
Snip
I was bewildered when I bought some drain cleaner to find small aluminium filings in it.
Only when it had been poured into the drain and some warm water added did the penny drop! The immediate chemical reaction and consequent fumes made me
realise what I was using. Only then because I was familiar with the stuff, having used it in my work.
Just think how dangerous the product is, especially if hot water had been added. The stuff spits and boils violently, so you don't even need to
splash it onto yourself.
Do you really read the instructions of every product you buy? I know I don't! Just a cursory glance to see what is needed.
It is fine for things to be available to all as long as the necessary precautions are known. However using Caustic in that manner shocked me!
Terry

Spyderman
|
|
|
NS Dev
|
posted on 20/4/04 at 01:36 PM |
|
|
If you add the caustic to water it's usually not too bad, if you add water to the caustic then it's no joke!! But that's why it says
on the packaging about never adding the water to the caustic. However, the warning still doesn't prepare you for the resultant reaction!! (why
do I always have to try the opposite to the instructions just to see what happens!!)
|
|
gjn200
|
posted on 22/4/04 at 08:09 PM |
|
|
Dunno if anyones interested, but I use this..altrans
<- Me!
|
|
Andy S
|
posted on 24/4/04 at 08:12 PM |
|
|
Many thanks for posting the link this is a great method - only wish I had been enlightened during the winter so my bucket of gunge and charger could
have been working away in the freezing cold of my garage whilst I was warm indoors.
Soon running out of bits to clean and will have to resort to pulling stuff off the car
Andrew
|
|
ceebmoj
|
posted on 25/4/04 at 07:19 PM |
|
|
Hi, I thort that I had written my findings with this up but a quick look through this thread does not seam to shown up my results.
I made couple of alteration to the basic proses first of all a used backing soader because I was not happy with the risks of using the other
additives. The disadvantage is that you will get a lower current draw and hence it will take longer to clean the part.
The other thing I did was use an old pond / fish tank pump to cycle the water thought a filter watching the ammeter on my power supply shows that this
prevents the current from dropping over time and the solution in the to the main bath can be redirected to was over the part helping to dislodge rust
and scale.
However the biggest improvement I made was with the anode I started with a thin sheet of steal so that I could bend it to match the contours of the
part to be cleaned and based some hole is in it with a nail so that the rages points where all facing the part to be cleaned. This enabled a hire
current flow as the electrons find it easer to fall of the piece of metal at the points.
Blake
|
|
craig1410
|
posted on 25/4/04 at 11:09 PM |
|
|
Blake,
Intersting tips, thanks.
Only thing I would mention though is to watch out for using too many amps as I have read somewhere that this can be disadvantageous. IIRC, the article
said that some of the oxidised iron nearest to the surface of the solid iron can be reduced back to solid iron provided a relatively low current is
used initially. I think this is referring to the "black" iron oxide and not the red iron oxide which I think is not so practical to reduce
back to metal.
I guess the net effect of this will be to save more of the metal and hopefully reduce the amount of pitting which you are left with after the rust is
cleaned off. I usually use 4 Amps and leave the part overnight and this seems to do the job nicely. Also remember that higher currents will cause more
heating of the solution and will produce more gas so be careful and make sure you have adequate ventilation.
Cheers,
Craig.
|
|
ceebmoj
|
posted on 26/4/04 at 06:12 PM |
|
|
good point about the current all though I only use 2 to 4 amps (limited and monitored by the supply) depending on how I am feeling and how big the
part is but I get a fizz from it like you get from a fresh glass of coke. This fizzing will last for the length of time you are cleaning the part.
All of the parts I have cleaned have been left with a black covering witch can be removed with a wire brush. However the pond pump and filter means
that it is perfectly clean to work with before I did this it gets all crapped up and the current draw fall of slowing the cleaning proses.
|
|
ChrisS
|
posted on 27/4/04 at 11:14 AM |
|
|
Hi
Was wondering if anyone could clarify how big the electrode needs to be, or if it would be a benefit to have a large tube effectively using sheet
metal bent round a part for cleaning.
Ive seen details of an iron electrode being used and assumed this might be solid & quite small in diameter.
Also was wondering if it mattered how the electrode was positioned in the tank, either upright or laying down.
Although ive just realised that the connection probably needs to be out of the water DOH!
That stainless steel electrode stuff is quite worrying, is everyone sure its safe at all using iron or even mild steel?
Chris S.
|
|
craig1410
|
posted on 27/4/04 at 02:27 PM |
|
|
Chris,
On the safety aspect, I can only say that I am satisfied that I am perfectly safe when using plain mild steel anodes but you need to satisfy yourself
as obviously I don't want to give you any guarantees for potential legal reasons. Look at it this way, if there is no chromium in the steel or
solution then you shouldn't be able to come to any harm from chromium poisoning...
On the other subject of anode size and shape I will say this: The closer to the piece the anode is then the higher the current flow will be and
therefore the faster the process will go. Also, you will find that the rusty item will clean up where it is closest to the anode quicker than the bits
where it is farher away. For this reason a sheet of metal bent around the inside of the bucket is a good method as it gives good surface area and even
coverage of the piece. Where you have a hollow area such as the centre of a boss then perhaps a piece of concrete reinforcing bar in the middle might
be good to provide electric current to the inner circumference.
Hope this helps,
Craig.
|
|
ceebmoj
|
posted on 28/4/04 at 07:04 PM |
|
|
Criss
The electricity will take the esest path from anode to part (basically the shortest distance) so if you use some thing that you can bend to follow the
contours of what you want to clean to can acheave a lager are of the part is near the anode and hene a larger bit will get cleaned.
The only reason that I punch hole in my sheet is to produce a surface that has lots of small sharp high points on it as the electrons will fall off
easer (there are I am sure people who will shout me for that description)
|
|
NS Dev
|
posted on 28/4/04 at 08:02 PM |
|
|
sounds like a pretty good description to me!! more surface area for the electrons to fall out of!!
|
|
JH
|
posted on 13/5/04 at 06:16 PM |
|
|
Just been pointed in the direction of this post after asking a similar question in another part of the forum.
I was quite concerned about the suggestion of using stainless steel until I saw someone had already pointed out the dangers. What about a carbon
electrode? I'm no chemist, but when I was in school my slightly nutty chemistry teacher (who was missing a finger from a home made bomb gone
wrong in his teens) Stuck a pen in the earth hole of a mains socket to open the bottom two, plugged a carbon rod into each hole, connected each one to
a carbon rod suspended in a small glass of water with a tiny bit of salt added, then turmed the power on.
we all expected trouble, but it bubbled away nicely, not blowing any trips or fuses!
|
|
craig1410
|
posted on 13/5/04 at 10:03 PM |
|
|
JH,
You should be safe enough with mild steel anodes but they do corrode quite badly and leave a messy solution. Not a major problem mind you and a method
used by many on this forum with great results.
Carbon doesn't conduct very well compared to steel but it would probably work given that the solution is also not very conductive. I think the
biggest problem you may have is getting enough surface area of carbon to get enough current flowing and get an even coverage of the piece being
restored.
I'd say that if you are trying to restore mild steel then you are better off using a mild steel anode otherwise there is a chance of getting by
products from the reaction which might cause the steel to corrode again more quickly. From my knowledge of chemistry I would doubt that carbon would
produce any by products but you really need to be careful as the example of using stainless steel shows...
If you want to plate the steel afterwards then by all means look into Nickel plating.
Cheers,
Craig.
|
|
VinceGledhill
|
posted on 19/5/04 at 02:41 PM |
|
|
What about a copper electrode? Or copper sulphate used after the cleaning. From school I remember electro-plating things with copper sulphate.
Basically to plate something with copper simply use coper sulphate (must be obtainable from the chemists) the cathode (negative) should be connected
to the work to be plated and the positive in the solution.
Copper plated hubs instead of painted ones??? Polished up they would look great.... you would have to keep polishing them though.... duraglit out
every week
Regards
Vince Gledhill
Time Served Auto Electrician
Lucas Leeds 1979-1983
|
|
craig1410
|
posted on 19/5/04 at 07:43 PM |
|
|
Vince,
Hopefully someone with more chemistry knowledge than myself will respond but if I remember correctly, copper will oxidise very rapidly and is not a
very good plating compound to use on steel. Much better off with Nickel or Silver or Gold (yeah right for the latter two!). Nickel is commonly used
and I think you can buy commercial nickel plating kits.
If you are still keen on copper then take a look at your water pipes under your kitchen sink and tell me if you like the look of them! I know mine are
all dull and green in places which isn't very pleasing to the eye... The soldering flux causes very rapid corrosion if not removed after fitting
but even clean copper gets dull very quickly.
Cheers,
Craig.
|
|
welshy
|
posted on 1/7/04 at 08:55 AM |
|
|
To prevent the cathode from becoming all gunked up would it still work if you wrapped it in a shealth made from kitchen foil. You could then simply
replace the sheath!
|
|
blueshift
|
posted on 1/7/04 at 01:36 PM |
|
|
I wasn't taking seriously the ideas of copper plating, but hmm.. if you got a decent surface on something then copper plated it, buffed it up
then laquered it, might look kind of cool.
|
|
millenniumtree
|
posted on 8/7/04 at 03:03 AM |
|
|
According to this page (given earlier in the discussion)
"The copper connector of the battery charger must make good contact with the stainless steel but it must not touch the solution. If it does
touch, it will dissolve. The copper that dissolves will wind up depositing on the iron object being cleaned and cause it to rapidly rust"
http://www.holzwerken.de/museum/links/electrolysis_explanation.phtml
So that's a no on the copper!
Also, if two different metals are touching, sometimes one or both of them will oxidize MUCH faster than if they were not touching.
So if you copper-plated something it might look cool, but it may turn green (copper rust) much faster than normal.
[Edited on 8/7/04 by millenniumtree]
|
|
Skirrow
|
posted on 18/7/04 at 11:33 AM |
|
|
Can anyone help me with this, I have been using one of those little chargers that has a black squre thing that plugs into the wall. I'm only
getting 0.5 Amps which is doing something but it's painfully slow. I think the max output of the charger is 0.8 anyway.
What does I need to do to my PC power supply to get a higher current? I'm not that electrically minded so if someone could tell me what to do
with the jumble of coloured wires that come out of it it woule be helpful. I saw a post saying I should place a load resistor across +5v tp ground but
that doesn't mean a massive amount to me.
Cheers!
|
|
atomic
|
posted on 13/9/04 at 07:21 AM |
|
|
A WORD OF WARNING !
Before you try the rust removal if you havn't already.... Read this
"Many people using the electrolysis method for rust reduction swear by stainless steel, stating (incorrectly) that it's not consumed,
stays clean and seems safe.
Stainless steel is indeed consumed when used in the electrolysis process, although slowly. The main problem with using it is the hazardous waste it
produces. Stainless steel contains chromium. The electrodes, and thus the chromium is consumed, and you end up with poisonous chromates in your
electrolyte. Dumping these on the ground or down the drain is illegal. The compounds can cause severe skin problems and ultimately, cancer. Hexavalent
chromate is poisonous. These compounds are not excused from hazardous waste regulations where household wastes are.
These compounds are bad enough that government regulations mandate "elimination of hexavalent chromate by 2007 for corrosion protection."
Does your electrolyte turn yellow? That's a sign of chromates.
If you have been using stainless steel for the anodes (positive electrodes), wear rubber gloves when working with or near the liquids. If you need to
dispose of it, allow it to evaporate into powders and dispose of the powders in sealed containers during your local "hazardous waste clean-up
days".
|
|
craig1410
|
posted on 13/9/04 at 08:33 AM |
|
|
Hi,
Yes I pointed this out a while back but given the size of the thread it is certainly worth repeating.
Cheers,
Craig.
|
|
stephen_gusterson
|
posted on 13/9/04 at 08:34 AM |
|
|
see the movie erin brocovich for more info on hexavalent chromium. The whole movie is about its efects.
Plus you get to see Julia Roberts in short skirts and wonderbras.....
atb
steve
|
|
Northy
|
posted on 29/12/04 at 04:05 PM |
|
|
HELP!!
I've just spent over an hour trying to get this to work
I got some of the soda same as Mark got (shown below) and connected everything up. Nothing. The battery charger stays on trickle charge. No bubbles,
nothing.
One thing I'm curious of is how people have made a good contact to the part they're cleaning? I used a big croc clip and it seems to have
a good contact.
Please help,
Cheers
Graham
Website under construction. Help greatfully received as I don't really know what I'm doing!
"If a man says something in the woods and there are no women there, is he still wrong?"
Built 2L 8 Valve Vx Powered Avon
|
|
Northy
|
posted on 29/12/04 at 05:05 PM |
|
|
OOpppss heres the picture
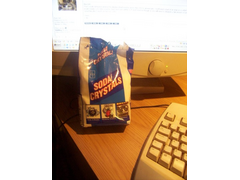 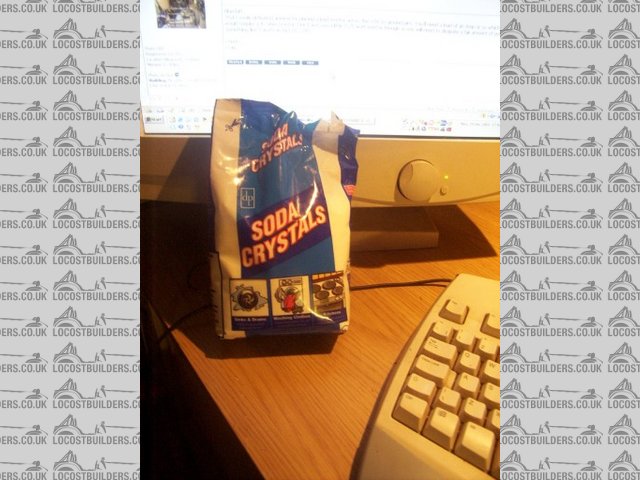 Rescued attachment Soda.jpg
Graham
Website under construction. Help greatfully received as I don't really know what I'm doing!
"If a man says something in the woods and there are no women there, is he still wrong?"
Built 2L 8 Valve Vx Powered Avon
|
|
craig1410
|
posted on 29/12/04 at 05:17 PM |
|
|
Some battery chargers won't produce any decent power unless they are actually attached to a battery. The one I have from Halfords is like this.
You may need to find an alternate source of 12 Volts. I have a laboratory power supply myself which can supply up to 18 Volts at 10 Amps.
Cheers,
Craig.
|
|