Gakes
|
posted on 8/4/08 at 06:09 AM |
|
|
Like I said before, this must be the best site ever. Anything is possible and this forum has all the right members
I thought it was possible, not just wetting myself How does the vacuum bag work??
 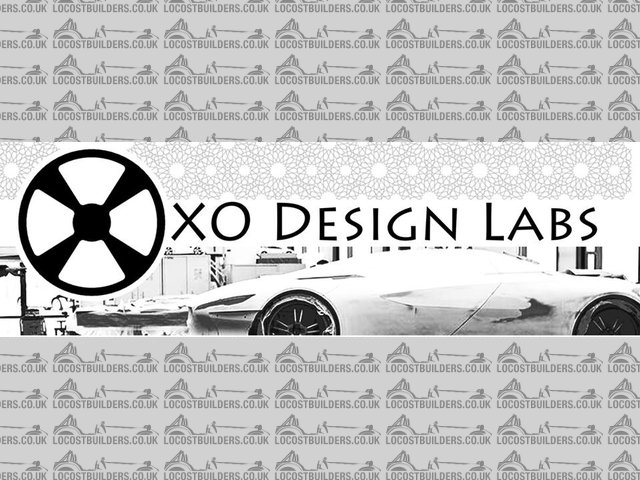 Description
|
|
|
Mr Whippy
|
posted on 8/4/08 at 07:32 AM |
|
|
I have books on building boats, it covers Carbon & Kevlar amongst a whole heap of other materials. It's very interesting to see just how
many down sides there are to these materials which are not often mentioned, Carbon especially sounds a right disaster in a crash (virtually turning to
dust in impacts) unless used in a honeycomb panel like in F1 etc.
Fame is when your old car is plastered all over the internet
|
|
D Beddows
|
posted on 8/4/08 at 07:39 AM |
|
|
quote:
It is by no means impossible for an amateur builder to design and manufacture something really effective (I think Syd Bridge has done something
similar in the past?).
Errrm I'd hardly call Mr Bridge an 'amateur builder' 
|
|
Phil.J
|
posted on 8/4/08 at 08:27 AM |
|
|
It is possible to buy both fibreglass skinned honeycombe panels and carbon skinned honeycombe panels in any thickness from a firm called
'Technical Resin Bonders'. These are easy to cut and can be bent within certain limits, and joined with adhesives and carbon cloth
reinforcement. Great construction materials for stiffness and light weight if a little on the expesive side (an 8' x 4' carbon skinned
honeycombe panel is around £900).
|
|
Delinquent
|
posted on 8/4/08 at 09:24 AM |
|
|
Hi Gakes,
My design was started with this in mind, and it is still something I am exploring. The biggest problem seems to be getting through regulations as you
have to prove to them that your design is strong enough. Something that was suggested to me by one of the SVA people was that when I create any
stressed part, I create a 2ft odd square piece from the mould then show it being loaded with comparable loads on the bench, so you don't have to
destruction test the entire structure! They will also expect to see FULL photographic evidence of layup methods, including mid-lay on areas that
include structural re-enforcements such as seat belt and suspension mounts.
Information is not exactly free flowing about how to go about this - I was being helped by a large supplier I was going to purchase all the materials
from, but they then went very quiet... now I'm left with half a design and some help from guys on here!
If you are looking at carbon, you'll also be wanting to look at kevlar in the mix to provide impact resistance in critical areas as well as
honeycomb or foam for stiffness. I'm considering a dense foam that is used in the F1 race boats - as the supplier said to me, if it can sustain
repeated loaded impacts with a high swell sea at 100mph+, it'll withstand most things!
Autoclaves are not necessary, a vac bag and elevated temp cure appear to suffice. Currently my plan is a mix of carbon, kevlar and honeycomb panels,
with metal inserts at critical load points, so I've made as many surfaces in the tub as flat as possible, held apart by curved areas to provide
geometric strength. Unfortunately I haven't got a brain big enough to do structural calcs so going to do some test parts!
Vac bagging is as simple as it sounds - stick the entire laid up part in a large poly bag, seal the end, stick vacuum tube in bag. The vacuum machine
itself isn't any old dyson though, you'll want a high capacity pump that is capable of sustaining a strong suck. I actually run 2 pumps -
one is a very high volume to quickly evacuate the majority of the air, the other is low volume but capable of almost -1 atmosphere pressure so does
the pressure bit well.
[Edited on 8/4/08 by Delinquent]
|
|
Syd Bridge
|
posted on 8/4/08 at 09:46 AM |
|
|
quote: Originally posted by D Beddows
quote:
It is by no means impossible for an amateur builder to design and manufacture something really effective (I think Syd Bridge has done something
similar in the past?).
Errrm I'd hardly call Mr Bridge an 'amateur builder'
  You been peeking in the door again! If you saw what I am doing today, I'd have to shoot ya!
Cheers,
Syd.
|
|
twybrow
|
posted on 8/4/08 at 11:47 AM |
|
|
quote: Originally posted by Mr Whippy
Carbon especially sounds a right disaster in a crash (virtually turning to dust in impacts) unless used in a honeycomb panel like in F1 etc.
But that can be used as a benefit. Look at the SLR crash cones. They are carbon epoxy and designed to absorb huge amounts of crash energy. It
doesn't yield in the same way as steel would, but that is not to say it is useless at impact.
|
|
Doug68
|
posted on 8/4/08 at 11:47 AM |
|
|
This is a thread on GT40s.com of a guy building a carbon GT40.
http://www.gt40s.com/forum/gt40-build-logs/24086-carbon-gt-mono.html
His day job appears to be making aerobatic aircraft, and he appears to know what he's doing. Note the lack of autoclave, plywood forms and
vacuum bags seem to be good enough for the job.
I suspect the hardest part of doing this sort of job properly is amassing the knowledge to do it properly.
Doug. 1TG
Sports Car Builders WA
|
|
dzine
|
posted on 8/4/08 at 12:56 PM |
|
|
CFRP - Go for it!
Gakes, you should really check out what Dennis is doing now with his DP1.
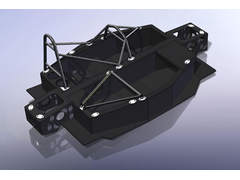 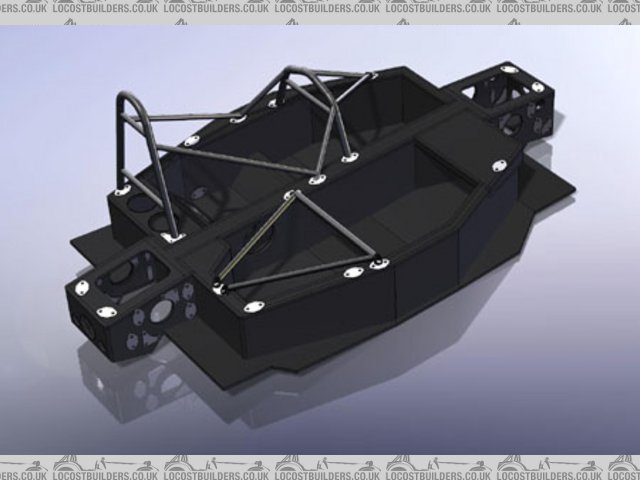 Rescued attachment dp1365.jpg
|
|
Puk
|
posted on 8/4/08 at 01:26 PM |
|
|
The thing that scares me about CF is that you can't easily tell when it has been damaged. Or badly cured for that matter. The aerospace industry
employ various forms of non destructive testing, which are not available to mere amateurs. Am I missing something, or are there locost test
techniques? Or is the risk engineered out by using high safety margins? Does anyone know why Westy give up on the CF chassis? Dennis P must have hit
that issue too, so maybe he has discovered a solution.
Presumably GRP chassis suffer from the same problem. Lotus built a GRP chassis on the first version of the Elan in the early 60s. They seemed to
abandon the concept but wasn't the Clan Crusader a Lotus design (that may have been a PR fib of course) - that had a GRP chassis IIRC. I guess
Davrian and GTM must have resolved the issue, at least sufficiently for SVA purposes - does anyone know how they do it???
Before you judge a guy, walk a mile in his shoes. Then when you judge him, you're a mile a way and you've nicked his shoes.
|
|
Delinquent
|
posted on 8/4/08 at 01:34 PM |
|
|
quote: Originally posted by PukI guess Davrian and GTM must have resolved the issue, at least sufficiently for SVA purposes - does anyone know
how they do it???
not me, and not for lack of trying either!!! For SVA purposes though it doesn't appear you need to be able to prove that the actual tub you are
putting through has cured properly or even been laid up correctly, only that the proposed lay up can take the stress.
|
|
jono_misfit
|
posted on 8/4/08 at 02:48 PM |
|
|
Sound.
Tap test with a coin. Where there is delamination etc you can hear the change in sound. F3, Formula renault, teams etc make use of this technique.
If you were being fancy you could use ultrasound to check it, although youd get reflections at every change in section and material. but i guess
you'd be looking for relative changes in the response spectrum.
At a guess they stopped selling them as they were so expensive and no-one bought them. It was designed by martin ogilvie im led to believe.
[Edited on 8/4/08 by jono_misfit]
|
|
Gakes
|
posted on 8/4/08 at 09:05 PM |
|
|
thanks guys,
Delinquent, very well explained and shows a very good understanding and lots of research!Bravo my friend, keep it up. we should be doing these leeps
of faith to keep us progressing.
Dzine, that is exactly what i am thinking of.its simple, stiff and superlight.
I started making a pipe roller today and will post sum pics of the progress soon.
 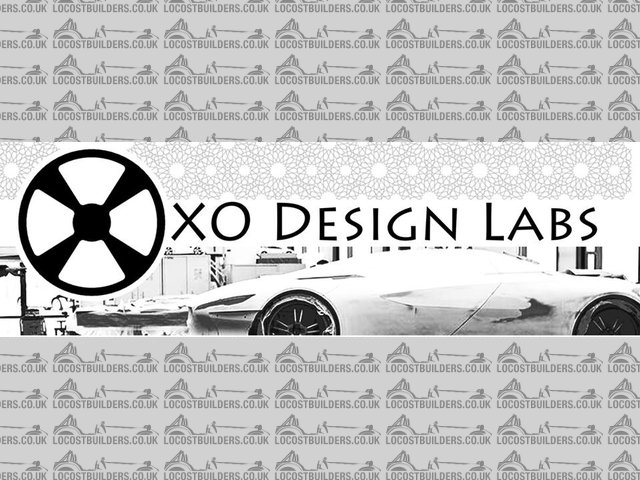 Description
|
|
Jo C
|
posted on 9/4/08 at 07:30 AM |
|
|
Go for it
It's easy to say...
Well i have been thinking of something similary for the last five years.
Carbon/kevlar/glass or ....
It is probably doable without a autoclave.
I think you could do it in glass (mini marcos, Midas and GTM rossa-libra) for ex.
The backside of doing it in the “backyard”, is the health issues.
Epoxi and the other chemicals are not good for you (some say no problem other do).
You could always dress appropriate for the task. The hard bit would be the rest of the family, getting bikes or a tool and by mistake touch something.
You have to be very carefully not to bring anything in to the house.
I have read some of the Hazard instruction on prepegs and it’s noting you want to take to bed….
nothing is impossible......
|
|
Benonymous
|
posted on 9/4/08 at 11:11 AM |
|
|
There have been plenty of responses to this thread and if you have a quick glance at the history of "alternative chassis materials"
threads, they all show robust levels of discussion.
Fact is, tubular steel, either RHS or round is a known quantity. This goes for constructors as well as the authorities.
CF is certainly the current "wonder material" the same as aluminium was in the 50's and 60's . The last robust thread on
chassis materials was the Aluminium chassis thread or maybe the latest aluminium thread that I saw.
The main thrust of the last ally thread was, "design for the material". Several examples were served up to indicate that a Seven chassis
would require a significant re-design for a change to aluminium.
With CF, there are a bunch of relevant factors. Primarily, if this is to be a road registered vehicle, the beak must be convinced that the chassis is
safe. There has been a significant post on this issue from Delinquent.
Another factor is design. CF has it's own set of requirements, all of which you'll have to become familiar with if you want to construct
anything with it.
As far as impact resistance is concerned, I'm reminded of a statement made by a chap I know who makes million dollar masts for racing yachts (I
kid you not) his take on CF is: "Carbon Fibre is incredibly strong for it's weight but when it fails, it snaps like a carrot" I
often think about this when riding my CF framed bike.
Finally. Building anything in CF can never be deemed "locost". The last time I checked, there was a worldwide shortage of CF cloth
especially in the 2K to 4K weights. Our friend Dennis (DP-1) appears to have relatively deep pockets but to he rest of us I think the prospect of
buying enough square metres of CF to make a car chassis might cause some distress.
As Jo C says "nothing is impossible" I'd add, "given enough time and money"
[Edited on 9/4/08 by Benonymous]
|
|
Alan B
|
posted on 9/4/08 at 11:39 AM |
|
|
Benonymous, I was looking to step into this one, but almost word for word you have voiced my feelings.
Regarding Dennis (DP1) I have a lot of respect and admiration for what he has achieved so far, but I'm pretty sure that his progress so far with
the CF tub is just the attractive Solidworks model shown on his site...I'm not saying it won't be a perfect tub, just that it isn't
one yet and that to look at the model and say something like "see look, it can be done" is a bit of stretch to say the least.....even more
so for locost-deep pockets.
I'm all for pushing envelopes....giving it a go etc......but without some realism there were will a lot of empty piggie banks and unfinished
projects.
So please by all means you CF tubbers prove me wrong....I know some will and hope you do, but for most of us will do well to heed the words of the old
design engineers motto....
When in doubt, make it stout, out of something you know about....   
|
|
Fred W B
|
posted on 9/4/08 at 11:40 AM |
|
|
I would add to the above excellent Benonymous post:
You must consider what would the benefits might be over a steel frame-
Lighter weight - how much actually?
Stiffer - are you going to spend mega bucks on proper multiway adjustable coilovers to take advantage of this stiffness?
Bling - how much is this worth to you?
To me it seems a hell of an increase in cost and hassle factor for any (maybe slight) improvement over a steel frame
Cheers
Fred W B
[Edited on 9/4/08 by Fred W B]
You can do it quickly. You can do it cheap. You can do it right. – Pick any two.
|
|
Wolf HR
|
posted on 9/4/08 at 02:23 PM |
|
|
Well, I intend to build glass-fibre sandwich monocoque chassis, and my guess is that it will be lightweight (the part shown should weigh less than
25kg) and cheap. Simple wet lay-up, no autoclaves and no nonsense (but I guess parts will have to be vacuum-bagged for post-cure)

The drawing doesn't show 4 Al bulkheads that will be glued to it to increase torsional stiffness, mount engine & suspension, and protect the
driver a bit...
As for strength- I've seen a specification for aircraft fuselage with similar layup, the difference beeing mine is (IIRC) 2x as strong and 8x
stiffer (and that's without tophat/box sections I used for siffening).
|
|
Gakes
|
posted on 9/4/08 at 04:43 PM |
|
|
thanks for all the tips guys. its particularly interesting to read about the negative aspects of CFRP, thanks.
Wolfr, excellent work my friend! I salute you. have you designed the rest of you car, cos id love to see your design progression. amazing work. I will
suggest, if u didn't think of it yourself, fill those openings with expandable foam for extra impact absorbtion. if u did think of that, gr8
design.
I think, and was always rooting for, the GRP sandwich is a good direction to go with for featherweight chassis, not forgetting to add in stiffness
where needed, as Wolfr also suggested.
Its gr8 to see where this discussion progressed to. thanks again guys.
 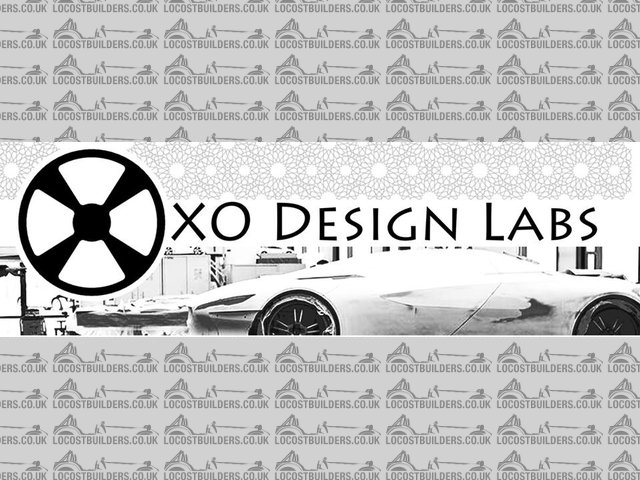 Description
|
|
Syd Bridge
|
posted on 9/4/08 at 06:43 PM |
|
|
I've watched this thread with interest.
'I've made one in the past'??? Well, more than a few, and the 'past' is present and ongoing. It's part of my
work.
Carbon is not a wonder fibre, but must be treated with due respect. Yes, it does crunch like a carrot when it goes. To use carbon, and other hitec
fibres, you must have a full knowledge of load paths, and resin properties. All of those snapped yacht masts are due to simple poor engineering, and
complete lack of it in most cases.
Wet layup carbon composites are little better than a good hispec glass item. To get the full benefit of carbon, or any of the modern fibres, then an
autoclave to cure the layup is imperative. If you haven't got access to a clave, then forget carbon.
In the pretty racecar tubs you see, with the nice weave showing, the real work is done by unidirectional fibres, hidden underneath.
If contemplationg glass, then I sincerely hope no CSM is involved. Otherwise, you just waste a lot of time and effort. Use as much unidirectional
fibre as possible, and orient it suitably. Put it outside of the best core material you can afford. NO foam that isn't PVC. Again, waste of
time. The two skins DO move against each other, and will quickly separate from a poor core choice.
I've said too much, but enough for you to be dangerous!
Cheers,
Syd.
|
|
iank
|
posted on 9/4/08 at 07:18 PM |
|
|
There has been an article in the last two Complete Kitcar magazines about a guy who built two (one for him, one for a mate) carbon fibre cars (kind of
GTM Libra but more wedgy shaped). Took him 15 years IIRC and he's now got an autoclave in his garage and a big pile of scrap panels. Learning
how to take advantage a new (to you) material takes a lot of time, money and hard earned experience.
Mr Bridge has been doing it for a lot of years - and if I really wanted to do it I'd get a quote from him. Unlikely to be cheap, but still much
much cheaper than doing it yourself from a standing start.
A steel spaceframe will be 90% as good, cost a couple of percent as much, and done in a couple of months. SVA man will just look at the welds and
make sure it's not horribly under-triangulated.
Finally don't underestimate how bad for your health epoxy resins can be.
--
Never argue with an idiot. They drag you down to their level, then beat you with experience.
Anonymous
|
|
tegwin
|
posted on 10/4/08 at 10:34 AM |
|
|
Have you looked at how the GTM libra is made?...
Thata a GRP monocoque with steel front and rear subframes.,.....
Doesnt look overly complex!
I guess the issue is knowing just how strong the GRP is....
------------------------------------------------------------------------------------------------------------------------
Would the last person who leaves the country please switch off the lights and close the door!
www.verticalhorizonsmedia.tv
|
|
rpmagazine
|
posted on 10/4/08 at 11:12 AM |
|
|
I currently drive a GRP chassied car
www.racemagazine.com.au
|
|
Delinquent
|
posted on 10/4/08 at 11:50 AM |
|
|
quote: Originally posted by tegwin
Have you looked at how the GTM libra is made?...
Thata a GRP monocoque with steel front and rear subframes.,.....
Doesnt look overly complex!
I guess the issue is knowing just how strong the GRP is....
may not look overly complex, but the complexity is in the actual matrix itself. What resin have they used, what weave, what orientation of the various
layers, what lay up thickness, what core...
I use carbon a great deal in my RC heli's - making a blade with a weave in one direction over another can be the difference between a sweet
flying machine or something that struggles to get off the ground and then is a mare to control with blades bending left right and centre.
|
|
Gakes
|
posted on 10/4/08 at 07:45 PM |
|
|
so true delinquent. I have read a bit on grp and cfrp chassis. the strength is in the layout, the specified plastics, and sometimes added structural
support.
Heres a few pics of the GTM LIBRA, interesting tub design. lots of box sections and corners for extra support:
 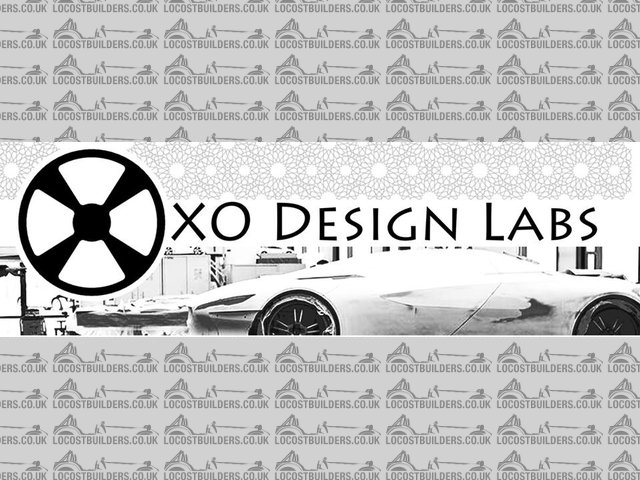 Description
|
|