nike5
|
posted on 25/11/08 at 01:39 PM |
|
|
3 sided box section - triangle
Does anyone know where I can get a piece of 3 side box section (20mm x 20mm x 20mm).
It is for the front bulk head. The vertical of the transmission tunnel. I need it to give bell housing more clearance.
I have tried my local supliers, and metal supermarket.com
size 20mm x 20mm x20mm (or if it has 90degree angle the third size would be slightly longer).
Options I have.
1 - move engine forward (not an option)
2 - get some flat plate, bend it to 90 degrees, then weld a length of flat plate to form the 3rd side (heat from welding will distort)
3 - use box section, cut corner out of tube, and then weld flat plate to create triangle section where needed. (looked like the bodge that it was, so
looking for alternatives).
4 - move square vertical box section back along transmission tunnel 25mm. Then use a steel plate to form front bulkhead, and then fold it to follow
line of transmission tunnel.
5 - a triangle box sect would be ideal (especially if it had a 90 degree) but proving difficult to find
At this stage, unable to make transmission tunnel wider.
Sorry for long (first) post.
Kevin
|
|
|
nick205
|
posted on 25/11/08 at 01:56 PM |
|
|
WElcome to the forum Kevin
I've not seen triangular section tube before myself and I'd guess if you can find it it would be 60/60/60 deg and pricey.
What about using round tube or possibly T or U section steel (with bracing if need be) to get the clearance and maitain strength. Both T and U
section are readily available.
Any pics of what you're trying to do?
|
|
maartenromijn
|
posted on 25/11/08 at 02:13 PM |
|
|
Hi Kevin, welcome.
I had the same problem. I decided to move the vertical RHS 25mm back along the tunnel. I made gussets (I hope this is the correct English word) to
strenthen the construction.
Because of this modification the bulhead plate (1.6mm steel = 16 gauge) moved back 25mm as well. I have done this on the right hand side only,
shortening the cockpit by 25 mm.
I am looking for pics on my computer. If I have them, I will post them.
Oh, I run a 1.6 X-flow with a 4-speed gearbox from a Escort Mk1, 1974. Don't know type number of gearbox.
BLOG: http://thunderroad-super7.blogspot.com/
|
|
maartenromijn
|
posted on 25/11/08 at 02:23 PM |
|
|
It was the left hand side which I have modified. This is the best pic I have. If you look well you can see that the vertical member had moved
backwards into the tunnel 25mm.
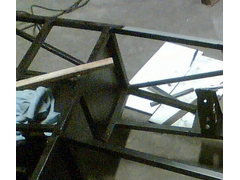 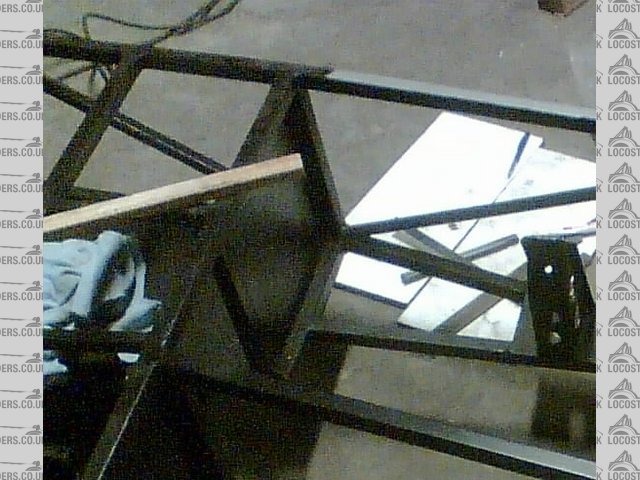 Rescued attachment Afb078 besneden.jpg
BLOG: http://thunderroad-super7.blogspot.com/
|
|
chrisg
|
posted on 25/11/08 at 02:29 PM |
|
|
You can get triangular steel bar
like this
but it'll be heavy, maybe you could drill it down the middle to take some of the weight out?
I think I'd probably use 3 seperate steel strips, you wouldn't have to fully weld it.
Cheers
Chris
[Edited on 25/11/08 by chrisg]
Note to all: I really don't know when to leave well alone. I tried to get clever with the mods, then when they gave me a lifeline to see the
error of my ways, I tried to incite more trouble via u2u. So now I'm banned, never to return again. They should have done it years ago!
|
|
pewe
|
posted on 25/11/08 at 02:36 PM |
|
|
Wouldn't 25mm angle iron with 25mm strip tack welded along the open length work?
Cheers, Pewe
Looking at my metal folder that's exactly how it's done - welded every 50mm or so presumably to stop it distorting.
[Edited on 25/11/08 by pewe]
|
|
nike5
|
posted on 25/11/08 at 02:46 PM |
|
|
Hi
maartenromijn - I think I see what you have done there.
You have moved the tube back 25mm and towards the side of car 25mm and the alloy pannels will be fitted to the opposite sides of the vertical tube.
As mine is on the drivers side, I will measure up to find out if I did this, whether it would effect the opperation of the clutch pedal.
Chrisg - I agree with you, it would be heavy to use a solid triangle bar, so will try to avoid this.
Pewe - just worried that while welding along long lengths, the heat would distort it. But I guess, if its welded becomes crocked, it is just strong
and crocked and serves the purpose.
|
|
DarrenW
|
posted on 25/11/08 at 02:55 PM |
|
|
quote: Originally posted by pewe
Wouldn't 25mm angle iron with 25mm strip tack welded along the open length work?
Cheers, Pewe
Might need a slightly wider strip.
|
|
Daddylonglegs
|
posted on 25/11/08 at 03:08 PM |
|
|
quote: Originally posted by pewe
Wouldn't 25mm angle iron with 25mm strip tack welded along the open length work?
Cheers, Pewe
Beat me to it!
Exactly my thoughts.
It looks like the Midget is winning at the moment......
|
|
maartenromijn
|
posted on 25/11/08 at 03:29 PM |
|
|
Maybe this sketch gives some light in the darkness.
Since I am building a LHD car, it might give problems with the pedals.
Also it might give problems with the clutch operation. I remember measuring the stroke of the clutch operation lever on the gearbox, so I hope I did
it correctly some 2 years ago...
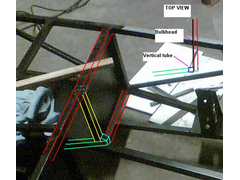 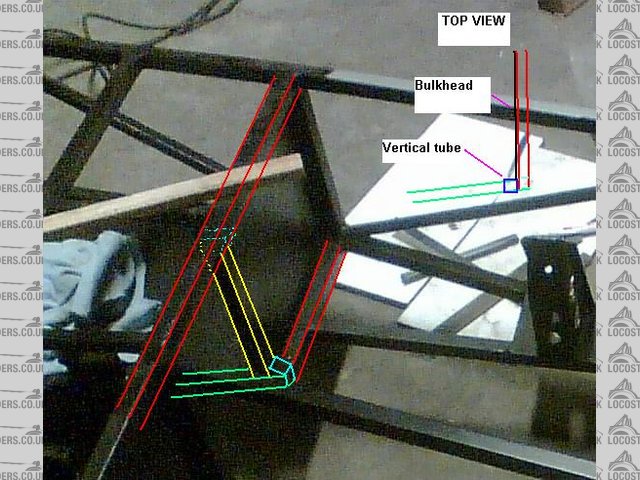 Rescued attachment TEKENING.JPG
BLOG: http://thunderroad-super7.blogspot.com/
|
|
mr henderson
|
posted on 25/11/08 at 03:47 PM |
|
|
quote: Originally posted by DarrenW
quote: Originally posted by pewe
Wouldn't 25mm angle iron with 25mm strip tack welded along the open length work?
Cheers, Pewe
Might need a slightly wider strip.
35.3553339mm
|
|
IDONTBELEIVEIT
|
posted on 25/11/08 at 05:53 PM |
|
|
quote:
Might need a slightly wider strip.
quote:
35.3553339mm
I'd use 25 x 25 x 3mm RSA and a strip 31.11
Are We There Yet, Are We There Yet!!!!
|
|
cjtheman
|
posted on 25/11/08 at 05:54 PM |
|
|
quote: Originally posted by nike5
Does anyone know where I can get a piece of 3 side box section (20mm x 20mm x 20mm).
It is for the front bulk head. The vertical of the transmission tunnel. I need it to give bell housing more clearance.
I have tried my local supliers, and metal supermarket.com
size 20mm x 20mm x20mm (or if it has 90degree angle the third size would be slightly longer).
Options I have.
1 - move engine forward (not an option)
2 - get some flat plate, bend it to 90 degrees, then weld a length of flat plate to form the 3rd side (heat from welding will distort)
3 - use box section, cut corner out of tube, and then weld flat plate to create triangle section where needed. (looked like the bodge that it was, so
looking for alternatives).
4 - move square vertical box section back along transmission tunnel 25mm. Then use a steel plate to form front bulkhead, and then fold it to follow
line of transmission tunnel.
5 - a triangle box sect would be ideal (especially if it had a 90 degree) but proving difficult to find
At this stage, unable to make transmission tunnel wider.
Sorry for long (first) post.
Kevin
hi
if at a 90 the third side would be 28.28
cheers
colin
|
|
IDONTBELEIVEIT
|
posted on 25/11/08 at 06:10 PM |
|
|
you havent taken into consideration the material thickness
quote:
if at a 90 the third side would be 28.28
Are We There Yet, Are We There Yet!!!!
|
|
MikeRJ
|
posted on 28/11/08 at 01:44 PM |
|
|
quote: Originally posted by nike5
3 - use box section, cut corner out of tube, and then weld flat plate to create triangle section where needed. (looked like the bodge that it was, so
looking for alternatives).
I don't think this is a bodge if you do it nicely. Use the same gauge steel (probably 16 gauge) and if you dress the welds you wouldn't
even know it had been welded.
This also allows the piece to remain square at either end where it's welded to the main structure, and you can then taper down in to a
triangular cross-section.
|
|