kb58
|
posted on 19/12/06 at 05:27 PM |
|
|
Wow.
Mid-engine Locost - http://www.midlana.com
And the book - http://www.lulu.com/shop/kurt-bilinski/midlana/paperback/product-21330662.html
Kimini - a tube-frame, carbon shell, Honda Prelude VTEC mid-engine Mini: http://www.kimini.com
And its book -
http://www.lulu.com/shop/kurt-bilinski/kimini-how-to-design-and-build-a-mid-engine-sports-car-from-scratch/paperback/product-4858803.html
|
|
|
NDC790
|
posted on 19/12/06 at 06:57 PM |
|
|
SMURK
|
|
Uphill Racer
|
posted on 20/12/06 at 11:48 PM |
|
|
Wasn't the post "Open to suggestions"?
Not lets have a spat, slanging match or stand off?

|
|
Dick Bear
|
posted on 21/12/06 at 04:21 AM |
|
|
You are absolutly right Uphill Racer.
Hopefully the dust has settled and we ALL can get down to offering ideas ans suggestions without condemnation.
I'm certainly ready to get back to a level playing field.
Cheers,
Dick Bear
www.marketpointproductions.com
|
|
Syd Bridge
|
posted on 21/12/06 at 10:06 AM |
|
|
The monocoque has been around and in successful use for decades, if not more.
Most LeMans cars of the 60's-90's were ali mono's. And not sandwich, either. Just folded sheets. Some still are.
The carbon mono's in use are just ali designs, with the material changed. I know, I make them!! The cfrp monos could be much more considerate of
the material, but the 'people that be' are used to seeing ali, so that's the shape they think things 'should' be.
Lotus use an ali mono, and if you inspect one closely, it's not 'rocket science'. It's not very much science at all!! The glue
is generic off-the-shelf. The curing process dates back generations, as does the metal forming process.
Some may be overwhelmed by something they see as different. But, when you deal with these things as often as I do, they become fairly pedestrian.
Mr. Bear is to be commended for venturing to do what he is attempting. None of the technologies are new, just some of them to him, and obviously to a
lot of you who are reading this.
Open your minds, and be prepared to learn 'HOW' to do something, and not tell someone how they can't.
Cheers,
Syd. 
|
|
mcerd1
|
posted on 21/12/06 at 12:35 PM |
|
|
Just a thought....
When I was at Uni doing mech. eng. (nearly 4 years ago now ) we touched on most of the subjects covered so far, but I'm not going to go into
'steel vs alloy' or fatuge as such (I really hated fatuge at Uni - and now I do structural steelwork, its much easier when things
don't move )
Other than the Comet (which was stress consetrations from the lage sqare windows) there was another earlier high profile case (or several) that
propmted some of the first proper studies into fatuge - the Liberty ships
If you don't know already, they were an old ~1900 style ship re-designed to be build quickly in the US for WWII (I think the record was less tha
5 days) they were some of the worlds first fully welded ships - they had square hatch holes (to make them easier to build) and made form the cheepest
steel avalible - being welded nothing to stop a crack growing once it started - in the most extreme cases the ships literaly snaped in two and most
had problems in cold water/ weather (there is still 1 modded one left in SF I think)
Anyway 3 things came from this:
1 - stress consetrating features that I'm sure most people know about - as it was put to us 'square corners = bad'
2 - limiting crack grow - if a crack forms it will grow till it reaches the edge of the plate or component
if your car has a fully welded chassis then it could in theory snap in two - if your panels are rivited or bolted on it should stop and the only way
it can spread futher is to form a new crack in the next panel (of course bolts and rivets can also be stress consentrators them self )
3 - Material Grades some materials are better than others, not just in ultimate strength but also in fatuge resistance (as well as corossion,
workability.... and so on) - high strength or cheep alloys of alloy and steel will tend to be more britle (especialy at low temps.)
Dick, I'm sure that you are already aware of most of this (especially how different materials & grades behave) but I didn't see it
mentioned already
As for how to design your car,
its general accepted engineering practice to design as far as you can (sensably) on paper (or computer) then build models/ prototypes to see if your
right
-Robert
ps - You might guess spelling isn't my strong point
[Edited on 21/12/06 by mcerd1]
|
|
Dick Bear
|
posted on 22/12/06 at 02:51 PM |
|
|
Hey guys,
This is great. Just what is needed. Information based on education and years of experience.
Thanks! It's all going into the storehouse for referencing as I begin the monocoque design and build process.
Good stuff!
Just got told the amount that will be required to paint the McBearen (ouch!). Perhaps I should have put some of my effort into learning to paint!
Dick Bear
www.marketpointproductions.com
|
|
NDC790
|
posted on 22/12/06 at 06:50 PM |
|
|
Bonding?
I'm interested in the bonding side of the ally tubs, is this something that could be done in a home build i.e. in a garage? What are the
materials, where do you get them, how do you cure them, cost? that kind of stuff.
Also, is there any point in bonding ally pannels to a powder coated steel frame, I would assume the frame would be less substantial as normal space
frame?
Anyone done or know of anything like this?

|
|
DIY Si
|
posted on 23/12/06 at 03:15 AM |
|
|
I think some of the vhb tapes may be usable in things like this, but Syd will know more about that than me. Bonding to a powder coated anything seems
a waste of time, as it will only be bonded to the coating, not to the metal, as you may well require. I doubt that the powder would be enough to
ensure a good connection.
“Let your plans be dark and as impenetratable as night, and when you move, fall like a thunderbolt.”
Sun Tzu, The Art of War
My new blog: http://spritecave.blogspot.co.uk/
|
|
locostv8
|
posted on 24/12/06 at 10:49 PM |
|
|
quote: Originally posted by Dick Bear
... one participant on this forum who is obviously less than enamored with my efforts and felt it necessary to accuse me of being stubborn, ignorant,
unaware, a liar, careless, having a death wish, an endangerment to others, an opportunist, arrogant, and dangerous ...
Dick Bear
But what does he realy think??
About the paint. I'm not a painter or body person so I plan on doing the tub of the LC inside and out with a light coat of Linex bedliner which
is a failry light poly. The main thing I feel uncomfortable is the chemical side of painting and will have a friend who is a painter help me with
that side. As long as you don't use a metalic you can always wet sand out bobos and the worst case is paint stripper and not making the same
mistake the second time, sides there are many other mistakes to be made. As long as there is sufficent coat you can generaly wet sand and polish.
Kudos on your work so far. I being generaly chicken and with the hp involved a couple of extra lbs won't hurt me anyhow with a street car plan
on sticking with welded steel LC but who knows what is next. At the risk of offending someone here use the RH Lightweight as an example and do
everything better than they did and you should be OK.
You live just down 77 from me I would be honored to get together sometime to see your work.
jh
[Edited on 12/1/07 by locostv8]
http://wrangler.rutgers.edu/gallery2/v/7slotgrille/hssss/
|
|
3GEComponents
|
posted on 11/1/07 at 11:03 PM |
|
|
Dick,
Have you seen here for ideas?
http://www.chaparralcars.com/2e.php
Gives some good pictures.
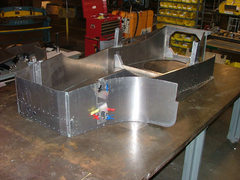 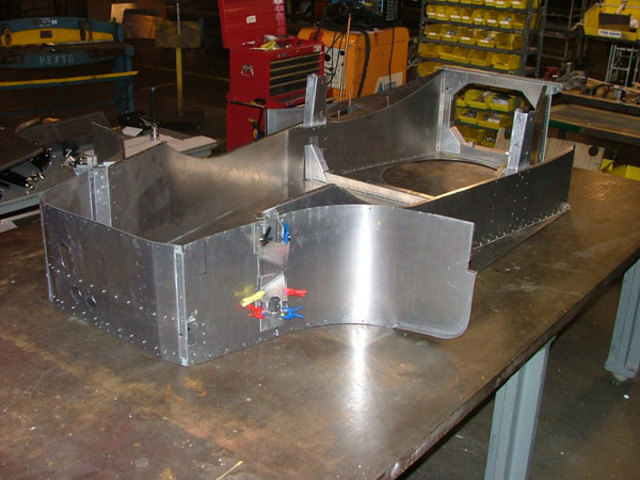 Rescued attachment carbuild3.jpg
|
|
andylancaster3000
|
posted on 12/1/07 at 01:53 AM |
|
|
To add to this, without meaning to make enemies here, I don't think that the "just give it a go'' attitude is entirely unjust
or unsafe. This whole forum originates from a car build where such an attitude is the whole idea. From how I see it, it is no different with new ideas
such as the monocoque. If people didn't try different things there wouldn't be such a fantastic variety of machinery around today. A lot
of the time, basic common sense with a decent understanding, you can't go too wrong!
Anyway… the point of my post. If I could point you in the direction of my posts on this thread:
http://www.locostbuilders.co.uk/viewthread.php?tid=58053&page=2
To add: The ally is 18gauge (I can't tell you what grade, it is important) and the steelwork is zinc plated to avoid any accelerated corrosion
issues
[Edited on 12/1/07 by andylancaster3000]
|
|
kb58
|
posted on 13/1/07 at 04:56 PM |
|
|
quote: Originally posted by andylancaster3000
To add to this, without meaning to make enemies here, I don't think that the "just give it a go'' attitude is entirely unjust
or unsafe. This whole forum originates from a car build where such an attitude is the whole idea. From how I see it, it is no different with new ideas
such as the monocoque. If people didn't try different things there wouldn't be such a fantastic variety of machinery around today. A lot
of the time, basic common sense with a decent understanding, you can't go too wrong!
[Edited on 12/1/07 by andylancaster3000]
Have you ever gone scuba diving? You know how they have the decompression tables, where you have to stay at a certain depth for some time to avoid the
bends? Guess how that table was developed. Volunteers (or prisoners) tried different decompression times in order to find out at what point the bends
occurred. It was found out through trial and error. So, is there room to try new things? Yes, a person can try decompressing less time than what the
table recommend, and they might get away with it, or it may kill them.
The situation is no different here. A builder can try building a car with material that has already been proven to have issues, and they might get
away with it, or it might kill them (or in this case, kill other people too.)
The "just give it a go" attitude here is excellent, as long as it doesn't result in an unsafe design. My whole rant is to not ignore
the past, not ignoring what's already known and understood. Trying a "new idea" such as the 50-year old monocoque design is not
new!
I'm sorry if you feel there are enemies here. There are not, only people concerned for the safety of others, and who point out that the
short-comings of this "new" design were understood decades ago. Learn from it.
[Edited on 1/13/07 by kb58]
Mid-engine Locost - http://www.midlana.com
And the book - http://www.lulu.com/shop/kurt-bilinski/midlana/paperback/product-21330662.html
Kimini - a tube-frame, carbon shell, Honda Prelude VTEC mid-engine Mini: http://www.kimini.com
And its book -
http://www.lulu.com/shop/kurt-bilinski/kimini-how-to-design-and-build-a-mid-engine-sports-car-from-scratch/paperback/product-4858803.html
|
|
Syd Bridge
|
posted on 13/1/07 at 06:09 PM |
|
|
You've gotta wonder what the chassis designers at Lotus would be thinking, if they read this thread???????????????
All those Elises and Exiges with those ali mono chassis??????? Must be time to scrap the lot of them!
Cheers,
Syd. 
|
|
Peteff
|
posted on 13/1/07 at 06:14 PM |
|
|
I'll agree with that.
They're only held together with Airfix glue, how can they be safe
yours, Pete
I went into the RSPCA office the other day. It was so small you could hardly swing a cat in there.
|
|
kb58
|
posted on 13/1/07 at 08:08 PM |
|
|
Designed by knowledgable engineers and with no rivets.
Mid-engine Locost - http://www.midlana.com
And the book - http://www.lulu.com/shop/kurt-bilinski/midlana/paperback/product-21330662.html
Kimini - a tube-frame, carbon shell, Honda Prelude VTEC mid-engine Mini: http://www.kimini.com
And its book -
http://www.lulu.com/shop/kurt-bilinski/kimini-how-to-design-and-build-a-mid-engine-sports-car-from-scratch/paperback/product-4858803.html
|
|
Dick Bear
|
posted on 14/1/07 at 04:52 AM |
|
|
Thanks J Roberts for the link.
After looking closely at the series of photos and being fully aware of my friend kb58's cautions conserning tub construction I have to admit
that that C2 tub looks very skimpy. Rivets (and I assume adhesive of some sort but I didn't see any evidence) fastening what appears to be
1/8" aluminum panels with just a few cross members with the suspension connection points not showing any appearent bulking of materials .... I
am amazed!
Since my decision to explore further the making of a Monocoque I have collected a large photo collection of Monocoques from evry web site I can find.
These are monocoques that are being built today and I must say, the Chaparral version is by far the lightest weight found to date. No one can ignore
the fact that Jim Hall was a great driver and a pioneering engineer with vision and although his DNF record left something to be desired in Can-Am no
one serious about competition vehicles can poo-poo his design talent. Add to that the fact that he is still around to offer this
"Continuation" program and one would have to admit that his equipment (tubs) performed safely under the most cruling situations
imaginable.
Engineers like Jim Hall and a host of intuitive designers like him have forgotten more about chassis, suspensions and materials than most of us will
ever know. Learning from their advances in design technology is one aspect of what we are all about.
However, I still find it hard to believe that the tub shown in J Roberts link and being built according to original engineering specs of the C2 is as
light weight as it seems to be from the photos. Especially when you consider that the engines that drove these rockets were not the light weight
aluminum blocks of today and each generated horsepower that few, if any of us, will have the honor of piloting no matter what kind of chassis we dream
about.
Simply amazing.....!
Dick Bear
[Edited on 14/1/07 by Dick Bear]
www.marketpointproductions.com
|
|
Syd Bridge
|
posted on 14/1/07 at 01:27 PM |
|
|
quote: Originally posted by kb58
Designed by knowledgable engineers and with no rivets.
I think you'll find more than the odd rivet and mechanical fastener in a Lotus!
And Mr. Bear has ben offerred my services if he wishes to avail himself of them. Well, if I'm considered knowledgeable enough for such a mundane
task!!
When Mr.Bear has acquainted himself with the basics of designing a chassis, I'm sure he will be able to produce an item which is at least the
equal of any of the opposition being most vocal here.
We all had to start somewhere.
Cheers,
Syd.
[Edited on 14/1/07 by Syd Bridge]
|
|
3GEComponents
|
posted on 15/1/07 at 01:32 PM |
|
|
OK, the Chapperel may be a bit on the "light" side, but that shouldn't rule out this type of chassis construction. That chassis was
designed in an era when the car wasn't expected to do more than a season (if lucky).
In Staniforths book the single seater monocoque was made from 16 gauge sheet, and the builder noted that after a trip to Pilbeam or somewhere, that he
may have over built it.
As long as the suspension loads are directed into the corner of boxes, or into bulkheads, as pictured below, you will be amazed at how thin the
material used can actually be. Just take a look at any modern bicycle frame for instance, tube butting has been used for years to reduce weight
without saraficing strength, some steel frames are as thin as 0.9mm in the centre!
Go for it Dick, take up Syd on his offer!
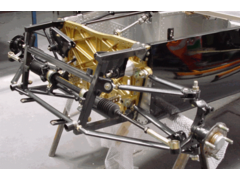 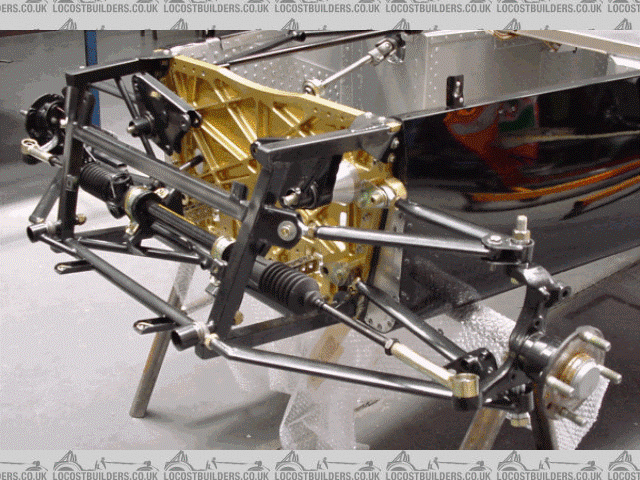 Rescued attachment Image11.gif
|
|
kikiturbo
|
posted on 15/1/07 at 02:42 PM |
|
|
elise chassis has rivets here and there, which enable better contact while curing the glue + prevent joint peeling off in a case of an accident..
I had a word with a guy that is building lemans type prototypes (spice I believe) and they are using an typical alloy monocoque method with a special
glue and rivets.... I would suggest you look into special glues for this application...
|
|
locostv8
|
posted on 15/1/07 at 06:08 PM |
|
|
If you look at the bottom plate it is quite thick. I would imagine the design puts most of the lode to this plate. I worked for an electric motor
manufacturer a while back that was looking into automotive/aircraft adhesives, the engineer said that the metal would tear before the adhesive would
delaminate.
http://wrangler.rutgers.edu/gallery2/v/7slotgrille/hssss/
|
|
3GEComponents
|
posted on 15/1/07 at 09:57 PM |
|
|
My guess would be there's nothing thicker than 16 gauge on the chassis.
|
|
Dick Bear
|
posted on 15/1/07 at 10:00 PM |
|
|
Well make no mistake, I’m going to do it and the really strange fact is that my doing so is not unusual in any way. There are numerous large and
small shops creating fantastic products using monocoque design technologies. That is what has surprised my the most over the last several weeks….
Seeing the discouragement of some in an almost defeatist attitude seemingly to ignore the reality of 50-60 year of monocoque design from airplanes to
racing, ships to deep divers. Quite frankly, none of the extremes experienced in either of these environments will be experienced by the
sport/handling vehicle I’m planning to design and build. I truly appreciate all the honest concern and I value the input but I’m convinced that they
are wrong as, it seems, many other quite capable designers do.
Rivets, no rivets. Adhesive, no adhesive. My Lord, the space shuttles and space station use rivets and adhesives in addition to “ fatal design
system” known as monocoque. Goodness sakes, very airplane in the world today uses that technology. Ships, submarines and deepwater diving vehicles
are based on that lightweight, strong and proven design. Without it, none of the accomplishments made in flight, space or on the sea and under it by
these vehicles in the last 60-years could have been accomplished. What’s the big deal? I just don’t get it. Sure there have been failures. Sh@t
happens even to those who are qualified to place a PE after their name but should those failures prevent us from moving forward? I think not!
Syd and I have had conversations about my using his expertise and once the program gets going I’ll surely take him up on his generous offer to assist
and guide me through the sticky spots.
This is so bazaar. Rather than having a discussion on what would result in the best solution, the discussion has been centered on weather or not a
monocoque system is safe, feasible and responsible. I’d truly be a fool if I entered this process committed to being irresponsible or having a desire
to create an unsafe product. Trust me, I have not fallen off the log enough times [yet] to be foolish enough to willfully destroy myself or anyone
else in the process. I’ve made mistakes, like we all have in our building efforts. My feeling about that is, “No harm, No penalty” and it’s time to
move on.
Thanks to all of you have entered into this with links and ideas for development. I hope you will continue to share your knowledge and discoveries
with everyone on the site.
Dick Bear
www.marketpointproductions.com
|
|
JoelP
|
posted on 15/1/07 at 10:38 PM |
|
|
in that picture above, the bottom actually looks thick due to the lip folded into the front. As said, its probably no thicker than the rest.
|
|
Volvorsport
|
posted on 15/1/07 at 10:41 PM |
|
|
GRP moncoque with integral roll cage - you have to guess the body style going over it .
and those special rivets are self piercing rivets - the new jaguar uses them aswell .
its £3.5k for the basic tooling - if i was to be building moncoques for a while id definitely be having one .
www.dbsmotorsport.co.uk
getting dirty under a bus
|
|