NS Dev
|
posted on 6/11/06 at 08:52 AM |
|
|
Chains, sprockets, bearings and taper-locs
Right, loads of questions.
Firstly, can anybody point me towards a good internet resource for chain specifications and torque capacity of taper-loc bush installations.
Next, are most motorbike chains the same pitch/spec as factory std? if so, what chain type are they.
Specifically what pitch/width etc of chain does an Aprilia RSV use?
Now for the big question, the engine installation I am deisgning will require the two bike engines to drive via seperate chains, onto a countershaft
with a sprocket at each end, mounted to the engine cradle on two bearings, with a duplex? sprocket in the middle, which then takes the drive on to a
further countershaft, again mounted in two bearings, with ford lobro flanges at each end to bolt the driveshafts up to.
My dilemmas are:
what bearings to use. I have seen a lot of installations that use pillow block bearings on slotted mounts to allow for chain tension adjustment. They
are a bit heavy, and I think pressed steel flange type bearings on vertical slotted flanges might be a better solution.
How to assemble the shaft!!! How can I mount 2 simplex and 1 duplex sprockets on 1 shaft, held solidly in 2 bearings and capable of transmitting 280hp
or so? Will keyways or taperlocs be strong enough to take the torque applied by each engine at the end sprockets, thus enabling me to slide the
bearings on to the shaft then fit the sprockets? Also, to fit sprockets to the shaft, is welding a sprocket mounting boss onto the shaft a big
nono..........I'm worried about shearing the shaft round the weld?
Then, for the output countershaft, how do I attach the drive flanges. Again I could weld them, but will that cause them to shear off, and also then I
can't get the bearings off!! Alternatively I could machine a taperloc sprocket down and drill it to turn it into a Lobro flange, and do it that
way, but are these things strong enough to with stand the torque of two v-twin 140hp engines????
I'm paranoid about snapping shafts as I have seen it happen a lot on grassers and am seeking to avoid it on mine!!!
PS looks like the machine will now be italian through and through............watch this space!
Retro RWD is the way forward...........automotive fabrication, car restoration, sheetmetal work, engine conversion
retro car restoration and tuning
|
|
|
Coose
|
posted on 6/11/06 at 11:26 AM |
|
|
I can easily answer your chain spec queries - bike chain sizing is very simple and is designated by a 3-figure number. For example - 530 - the
'5' is the pitch of one link in eighths of an inch. This means that the distance between roller pin centres is 5/8". The
'3' is the roller width in eighths of an inch, in this case 3/8". The '0' relates to side plate thickness. I'm not
sure how the number relates, but a 532 has thicker sideplates than a 530.
Have a look here for some specs!
Spin 'er off Well...
|
|
Bob C
|
posted on 6/11/06 at 12:39 PM |
|
|
Hi Nat,
taperlok gear is nice bolt-together stuff but its HEAVY, cast iron etc. Also I'm not convinced it's very suitable for the high torques and
torque reversals you get in an auto application - I think they would soon go loose & start to rattle.
I think in your position I'd get sporckets on a boss from your local machinery place (our local one is Congleton Bearings & they supply this
sort of stuff) or turn up your own boss that you can bolt a motorbike sprocket to. To mount tyhe sprockets on shaft ends I would turn a taper inside
the boss and outside the shaft & thread the shaft end so it all tightens nicely. For a ke you can drill along the shaft/boss taper & use a
(say) 6mm round bar as a key. That's how I made my propshaft middle bearing thing (and how old lotus elan wheels are held on)
The middle duplex chain thing I dunno - maybe you're stuck with taperlok there...
Some ideas anyway - hope it's useful
Bob
|
|
russbost
|
posted on 6/11/06 at 01:38 PM |
|
|
Nat, be wary of using shafts with locking slots machined in them - it dramatically reduces the torsional strength of the shaft - I put a post on here
a while back showing what I'd done to one of my axle shafts - they no longer have slots! Also long shafts will "whip" & vary
your chain tension.
Z cars have a nice installation they use on the back of the bike engined Mini - don't suppose they'd tell you where the bearings &
shafts come from tho' But I guess there's no harm in asking.
I have some pics of the Z cars setup if you want them just mail me.
Cheers Russ
I no longer run Furore Products or Furore Cars Ltd, but would still highly recommend them for Acewell dashes, projector headlights, dominator
headlights, indicators, mirrors etc, best prices in the UK! Take a look at http://www.furoreproducts.co.uk/ or find more parts on Ebay, user names
furoreltd & furoreproducts, discounts available for LCB users.
Don't forget Stainless Steel Braided brake hoses, made to your exact requirements in any of around 16 colours.
http://shop.ebay.co.uk/furoreproducts/m.html?_dmd=1&_ipg=50&_sop=12&_rdc=1
|
NOTE:This user is registered as a LocostBuilders trader and may offer commercial services to other users
|
NS Dev
|
posted on 6/11/06 at 02:24 PM |
|
|
Russ, what dia was that shaft that twisted and what grade of steel, out of interest?
Retro RWD is the way forward...........automotive fabrication, car restoration, sheetmetal work, engine conversion
retro car restoration and tuning
|
|
ned
|
posted on 6/11/06 at 02:29 PM |
|
|
Maybe way out of my depth here, but are there any bits that can be utilised from gearbox kart rear axles, they're solid, have bearing carriers
on the frame normally with key ways and can't remember the last time I saw a gearbox kart break a rear axle but that said the power/torque of
the rsv is a lot higher..
Ned.
beware, I've got yellow skin
|
|
NS Dev
|
posted on 6/11/06 at 02:34 PM |
|
|
mmmm, nice thinking! Certainly the bearing housings might be quite nice!
Re. strength, remember its two RSV's, not just one 
Any ideas what the common gearbox kart axle diameters are, I remember there are two main ones but can't remember what they were!
Retro RWD is the way forward...........automotive fabrication, car restoration, sheetmetal work, engine conversion
retro car restoration and tuning
|
|
Fred W B
|
posted on 6/11/06 at 03:36 PM |
|
|
Nowdays 50 mm kart axles are replacing 40 mm dia ones. If this seems huge, remember these axles are hollow, with wall thicknesses in the 2.5 to 3 mm
range
Even older karts used 25 and 30 mm (sometimes solid) shafts.
Regards
Fred W B
[Edited on 6/11/06 by Fred W B]
|
|
MikeRJ
|
posted on 6/11/06 at 04:19 PM |
|
|
quote: Originally posted by NS Dev
Then, for the output countershaft, how do I attach the drive flanges. Again I could weld them, but will that cause them to shear off, and also then I
can't get the bearings off!!
Just FYI this problem was solved by the bearing people some time ago:
http://www.wyko.co.uk/split_roller_bearings/split_plummer_block.asp
|
|
ned
|
posted on 6/11/06 at 04:27 PM |
|
|
I must be way out of date I was still thinking karts were using 30mm solid axles.
Ned.
beware, I've got yellow skin
|
|
russbost
|
posted on 6/11/06 at 06:03 PM |
|
|
Nat
I'm actually using 30mm kart axles & bearings, running about 137bhp (at the engine) thro each (the axles aren't joined, LH eng drives
LHR wheel, RH eng drives RHR wheel) - I haven't recently damaged anything, but I don't tend to be too brutal, too often with loads of revs
& dumping the clutch
One of the reasons I think I twisted the earlier axle with the keyway is that on a dry road I get virtually no wheelspin, hence the "wind
up" torque in the driveline is pretty massive, I would imagine with grasstrack your going to have a "release" in the form of
wheelspin fairly easily?
If I was doing it again I'd go for larger diameter axles & bearings, they have to be stronger.
I no longer run Furore Products or Furore Cars Ltd, but would still highly recommend them for Acewell dashes, projector headlights, dominator
headlights, indicators, mirrors etc, best prices in the UK! Take a look at http://www.furoreproducts.co.uk/ or find more parts on Ebay, user names
furoreltd & furoreproducts, discounts available for LCB users.
Don't forget Stainless Steel Braided brake hoses, made to your exact requirements in any of around 16 colours.
http://shop.ebay.co.uk/furoreproducts/m.html?_dmd=1&_ipg=50&_sop=12&_rdc=1
|
NOTE:This user is registered as a LocostBuilders trader and may offer commercial services to other users
|
gazza285
|
posted on 6/11/06 at 06:06 PM |
|
|
quote: Originally posted by MikeRJ
quote: Originally posted by NS Dev
Then, for the output countershaft, how do I attach the drive flanges. Again I could weld them, but will that cause them to shear off, and also then I
can't get the bearings off!!
Just FYI this problem was solved by the bearing people some time ago:
http://www.wyko.co.uk/split_roller_bearings/split_plummer_block.asp
Split roller bearings are very nice and easy to use. Now price them up and come up with another solution.
DO NOT PUT ON KNOB OR BOLLOCKS!
|
|
NS Dev
|
posted on 6/11/06 at 06:09 PM |
|
|
Right, no answers to the big problem of how to connect the sprockets to the shaft.....
what is the smallest diameter tube that I could sensibly weld the sprockets to and not have them come off?
I know it will work on 72mm dia as I have done it before with CV flanges.......
Would 45mm dia tube do for the shaft and weld on bosses to bolt bike sprockets on to?
I could then weld solid plugs into the ends of the tube stepped down to suit the bearings and put the bearings on each end of the shaft.
Downside would be putting the big duplex chain right in the middle of it all, putting a lot of bending load on the shaft, but the shaft will some
straight out from the bearings that way, and the sprockets are easy to replace.
would 45mm do it?? If so, what min thickness do you think?
I have a load of 3.2mm wall 45mm CDS, but I fear this will be a tad weedy! Overall length between bearings will be around 500mm
Retro RWD is the way forward...........automotive fabrication, car restoration, sheetmetal work, engine conversion
retro car restoration and tuning
|
|
NS Dev
|
posted on 6/11/06 at 06:12 PM |
|
|
lol yep I know I ain't using split rollers
Retro RWD is the way forward...........automotive fabrication, car restoration, sheetmetal work, engine conversion
retro car restoration and tuning
|
|
froggy
|
posted on 6/11/06 at 06:19 PM |
|
|
28mm bar with sleeves to match up to the bearing blocks on mine 2 degree taper and 6mm keyway on mine and no problems so far although im just boning
it round the estate at work as i havent got any arches on it yet
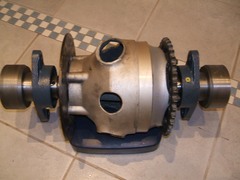 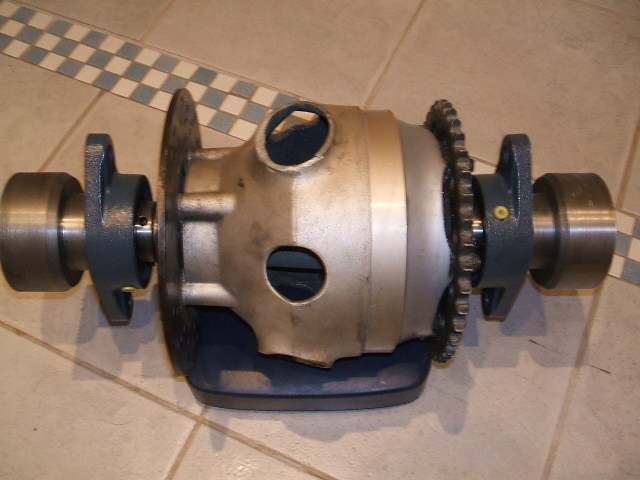 Rescued attachment chain drive 002.jpg
|
|
NS Dev
|
posted on 6/11/06 at 06:26 PM |
|
|
what chain u using, 525??
Retro RWD is the way forward...........automotive fabrication, car restoration, sheetmetal work, engine conversion
retro car restoration and tuning
|
|
froggy
|
posted on 6/11/06 at 07:03 PM |
|
|
530 and i had to buy a splitter from m+p costs £50 but makes it easier to set the adjustment up withoiut having a huge travel
|
|
tks
|
posted on 6/11/06 at 08:03 PM |
|
|
mhhh
talking about chains..
do you remember your thoughts about my chain??
it was 5/8 wasn't it!?
anyway i welded the sprockets! wy?
the axle is cheap and if it fails you won't be able to repair it.
also the sprockets are super cheap
sow wy making the shaft and sprocket etc. any expensiver?
what i did was i maked a axle wich starts at bearing diameter then goes up to sprocket diameter and then it has a nice flange to rest the sprocket
onto.
then i welded it at both sides at the same side and lenght!
you could do this with both sprockets.
also with bolts!!
i would make the bearing part just a alloy splitcase and normal ball bearings just a rear wheel sierra size
my bearing each can have 18Kn dynamic.
i use 2 of them on each axle..
static they can have 11Kn
max revs are 6500rpm
but with a primery reduction of 1,8 in a bike you wont have a problem.
lubrication would be an issue if you cant make it like mine all in one unit.
i just poped it up with 1 litre of industiral reduction/gearing oil.
i use 30mm at lowest point and the bearing has 40mm that axle will spin fast then it means you won't need huge axles..
anyway the last one from the diff would need it!
i would use 60mm in the last one and 40 in the first one wy?
wy not?
sprockets are cheap
chain is cheap
bearings are cheap (cheaper as a sprocket)
material is also cheap
its just man hours!!!
that the reason my case was expensive
total material bill was just 35euro's!! ex vat
Tks
The above comments are always meant to be from the above persons perspective.
|
|
tks
|
posted on 6/11/06 at 08:07 PM |
|
|
mhhh
rereading your post..
i would use 4 bearings!
2 near the flanges and 2 near the sprockets.
would use 2 taperd ones like in the rear sierra hub and 2 normal adjustbale ones near the sprocket.
then the axle cant bend in a ideal world you just start at inner taperd bearing then you go bigger rough.. then you go bigger fine (for last left
bearing) then you go bigger to fit sprocket etc..
Tks
The above comments are always meant to be from the above persons perspective.
|
|
gazza285
|
posted on 6/11/06 at 08:07 PM |
|
|
I can't see the problem with taperlock bushes, apart from the weight penalty. We use them on all sorts of gear, most of it probably similar to
what your familiar with Nat, and have very little trouble with them if they have been fitted correctly. As Russbost said, the only worry is getting
the shaft strong enough. I'd be inclined to use a few more bearings though, a shaft with two being pulled and one pulling is bound to suffer
some flexing if mounted on just two, it'd be nice to have at least one by the duplex sprocket and one at each end.
The second shaft is easy, just use a diff with a duplex bolted on to the crownwheel mount, as per some of the BEC middys, and your Ford lobros are
easy.
DO NOT PUT ON KNOB OR BOLLOCKS!
|
|
russbost
|
posted on 6/11/06 at 10:22 PM |
|
|
Forgot to say my axle is hollow 30mm, tube is about 6mm thick.
I made my own sprocket carriers by welding suitable tube (about 4mm thick from memory) to the axle then welding a flange to carry the drive sprocket
onto this. Set it all up in the lathe to weld so it was all square, biggest problem was drilling the flange & drive sprocket & keeping them
concentric.
If your shaft is going to be longer than 30cm I would add an extra pair of supporting bearings or it will flap about like a willie in a shirt
sleeve.
You still then have the problem of fitting the joints to the ends, but if you're using a large (say 50mm) shaft you could make up some fairly
deep plugs to go up inside the shaft on a very light interference fit then bolt through in 2 places at right angles to each other to locate perhaps? I
welded mine but as the shafts are separate I have one bearing on each which I have to break a weld if it ever needs changing
I no longer run Furore Products or Furore Cars Ltd, but would still highly recommend them for Acewell dashes, projector headlights, dominator
headlights, indicators, mirrors etc, best prices in the UK! Take a look at http://www.furoreproducts.co.uk/ or find more parts on Ebay, user names
furoreltd & furoreproducts, discounts available for LCB users.
Don't forget Stainless Steel Braided brake hoses, made to your exact requirements in any of around 16 colours.
http://shop.ebay.co.uk/furoreproducts/m.html?_dmd=1&_ipg=50&_sop=12&_rdc=1
|
NOTE:This user is registered as a LocostBuilders trader and may offer commercial services to other users
|