James
|
posted on 17/3/05 at 05:01 PM |
|
|
Welding Cast Manifold
Not really locost but:
While messing around under car spotted 3" long crack in underside of cast exhaust manifold.
Presumably there's bugger all chance of welding this up successfully?
Assuming that's the case- anyone know if all the manifolds on MK2 Golfs are the same?
Cheers,
James
------------------------------------------------------------------------------------------------------------
"The fight is won or lost far away from witnesses, behind the lines, in the gym and out there on the road, long before I dance under those lights."
- Muhammad Ali
|
|
|
Volvorsport
|
posted on 17/3/05 at 05:05 PM |
|
|
you can weld manifolds , theyre generally a better quality than just cast , i t does depend tho - sometimes you end up chasing the crack about - so
drill two holes , one at each end of it .
otherwise braze it , that will stop it leaking .
www.dbsmotorsport.co.uk
getting dirty under a bus
|
|
JonBowden
|
posted on 17/3/05 at 05:08 PM |
|
|
years ago I put a V8 in to a TR7. The (cast iron) exhaust manifold got in the way of the steering column. To fix this I ground out a section from the
manifold. Then some clever chap used a TIG to weld in a stainless steel patch.
So I guess a crack could be fixed in the same way.
Jon
|
|
JonBowden
|
posted on 17/3/05 at 05:10 PM |
|
|
Volvorsport - you beat me to it. I think you know a bit more about this than me.
Jon
|
|
britishtrident
|
posted on 17/3/05 at 05:10 PM |
|
|
I have seen a cast manifold bronze welded/brazed on a small block Chevy but I don't how long it lasted.
As for manifolds being the same check the down pipe numbers (Cats-direct http://www.cats-direct-shop.co.uk/car-exhaust-systems.php)
|
|
theconrodkid
|
posted on 17/3/05 at 05:18 PM |
|
|
its german so must be good quality ,i weld them with my arc welder
who cares who wins
pass the pork pies
|
|
nige
|
posted on 17/3/05 at 05:32 PM |
|
|
manifold
youcan get cast rods for arc welding
your best to heat up the cast first
if your going to have a go
i can get you a few rods from work to try
when you start this journey
you think it will be done in " no " time but then " no " turns into a " bloody " long time
|
|
MikeRJ
|
posted on 17/3/05 at 05:38 PM |
|
|
If you don't care what it looks like it's actually possible to plug up cracks in welds with a MIG. It's not a very prety sight
though...
|
|
James
|
posted on 17/3/05 at 06:19 PM |
|
|
Is it best to remove the manifold from the cylinder head before welding? The bolts are going to be a nightmare as it is anyway to take off. I'm
just worried about it warping the head slightly through the welded manifold 'pulling' on the side of the head.
If I want to get the head skimmed would I have to remove the manifold before they'll do the skimming?
Cheers,
James
------------------------------------------------------------------------------------------------------------
"The fight is won or lost far away from witnesses, behind the lines, in the gym and out there on the road, long before I dance under those lights."
- Muhammad Ali
|
|
theconrodkid
|
posted on 17/3/05 at 06:46 PM |
|
|
have to take mani off head along with anything likley to get swarf in/get in the way,what fixing have you got ,front pipe to mani?if its clips they
are a nitemare (luckily i have the tool somewhere)
who cares who wins
pass the pork pies
|
|
Liam
|
posted on 17/3/05 at 08:12 PM |
|
|
I got a MK2 8v GTi about to be weighed in. Would the manifold be any good? You can give me 1p to offset the money i loose weighing in less crap.
Liam
|
|
Liam
|
posted on 17/3/05 at 08:15 PM |
|
|
Speaking of welding cast, how shocking a practice is making a turbo manifold by welding a big flange and maybe some gussetts to a standard
manifold?
I'm sure Honda use only the finest cast iron and they are quite thick and heavy - not like some modern ones I've seen that are quite thin
and, all respect to 'em, look half decent and probably even flow ok...
Liam
|
|
craig1410
|
posted on 18/3/05 at 12:13 AM |
|
|
James,
I Mig welded my cast manifold for my Rover V8 following some advice by a few people (mainly Mark Allanson IIRC) In my case I was doing a complete cut
'n' shut so a crack should perhaps be a tad easier.
Again IIRC, there is a difference in the technique and likelihood of success between welding cast iron and cast steel. Mine was cast steel which is
easier. I managed to weld it with a 120Amp Clarke Mig with CO2 gas using a technique which Mark explained to me. For your purposes I think you just
need to cut a Vee groove with a grinder and weld a nice tidy and continuous weld down the middle. Drilling at each end sounds like a sound idea to
prevent cracking. If you do need to stop and restart the weld then Mark recommended grinding the edge of the weld down before restarting.
Oh, almost forgot, you need to get as much heat as possible into the manifold BEFORE starting to weld so you should remove the manifold from the car I
think. I heated it up with a little blowtorch until it was well over 100 degrees C (ie. It fizzled when I spat on it...) This is important to avoid a
cold start to the weld.
HTH,
Craig.

|
|
craig1410
|
posted on 18/3/05 at 12:40 AM |
|
|
James,
Here is the result of my efforts (before I tidied up the weld with the grinder...) It's not pretty but I am confident that it will be strong
enough to get the job done. I tended to keep the trigger pressed to ensure a continuous weld hence the excess build up in some areas. I took a lot
more care with the accuracy of the root weld before I started to fill in the Vee.
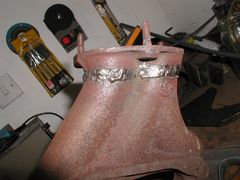 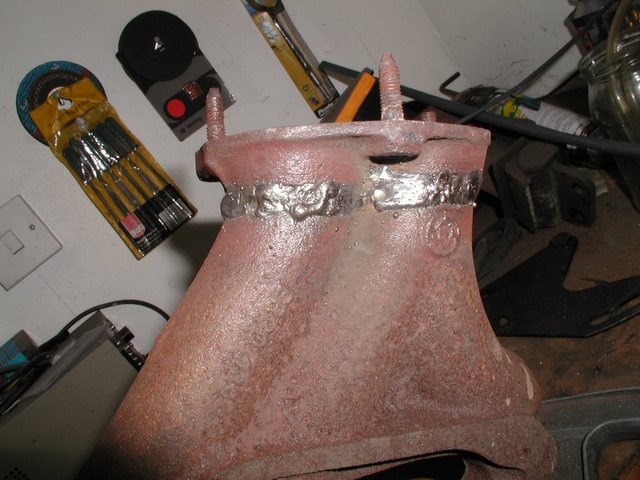 Welded Manifold
Cheers,
Craig.
|
|
James
|
posted on 18/3/05 at 11:47 AM |
|
|
Thanks for the advice everyone! I'll give welding it a go.
Liam,
I've sent you a u2u.
Everyone else,
Before Liam takes all the skin off his knuckles removing his one- anyone know if MK2 manifolds are all the same. Mine's the late model 1.8 with
carbs and many bits on it are the same as GTI but would be sensible to know for sure a knew one will fit!
Cheers,
James
[Edited on 18/3/05 by James]
------------------------------------------------------------------------------------------------------------
"The fight is won or lost far away from witnesses, behind the lines, in the gym and out there on the road, long before I dance under those lights."
- Muhammad Ali
|
|
NS Dev
|
posted on 18/3/05 at 12:59 PM |
|
|
quote: Originally posted by Liam
Speaking of welding cast, how shocking a practice is making a turbo manifold by welding a big flange and maybe some gussetts to a standard
manifold?
I'm sure Honda use only the finest cast iron and they are quite thick and heavy - not like some modern ones I've seen that are quite thin
and, all respect to 'em, look half decent and probably even flow ok...
Liam
I wouldn't do it that way. I have done this before by machining an adaptor block from mild steel, one side to match manifold outlet and one to
turbo, then milling and die-grinding the bore to suit each end.
|
|
Liam
|
posted on 18/3/05 at 05:11 PM |
|
|
quote: Originally posted by NS Dev
I wouldn't do it that way. I have done this before by machining an adaptor block from mild steel, one side to match manifold outlet and one to
turbo, then milling and die-grinding the bore to suit each end.
Ah haa!!! Clever!! Jolly good.
Liam
|
|