Ray Mc
|
posted on 27/2/05 at 08:09 PM |
|
|
standard flywheel lightnening
I am planning to lighten the standard cast flywheel from my 1.8 CVH. I intend to do it myself to save some money.
The engine is only going to be mildly tuned. I can either skim some weight off the flywheel using a lathe, or skeletonise it using a mill and dividing
head.
The problem is trying to work out how much i can aford to reduce the moment of inertia, and still keep the flywheel structurally safe.
Has anyone done this themselves, without having to go to a specialised engineering firm? How much weight is sensible to remove? 10%? Will it need to
be balanced again (is there much of an tolerance of balance) ?
Ray
[Edited on 27/2/05 by Ray Mc]
|
|
|
gazza285
|
posted on 27/2/05 at 08:36 PM |
|
|
Do not make it into a skeleton flywheel, as these are steel items not cast iron. If you skim it it will need balancing, and you'll have to keep
a machined radius on all edges to prevent cracks propagating. Obviously the more weight removed from the outside the better, but not to the structural
detriment of the flywheel. For the cost of what is involved, the risks involved, and the fact that it will need to be rebalanced after you've
finished with it anyway, you might as well take it to a decent machine shop and have it done for you.
|
|
Ray Mc
|
posted on 27/2/05 at 08:58 PM |
|
|
Thanks for your reply. Are flywheels not cast steel? I had ment skeletonising it on the outside only, so as just to leave the gears for the starter. I
have a good amount of toolroom experience and have full access to a machine shop, thats why i was thinking about doin it myself. Balancing should only
cost around £30 but machine shop time is very expensive.
Im in huddersfield too, anywhere local to get it done ?
http://www.pumaracing.co.uk/flywheel.htm
|
|
flak monkey
|
posted on 27/2/05 at 09:08 PM |
|
|
Standard flywheel is cast iron. Too brittle to make into a skeleton wheel. It tells you what you can safely remove in the Des Hamill book. Maybe
someone could scan it in and post it.
The aftermarket skeleton flywheels are steel as already said.
David
EDIT: Actually wait a sec and i will scan mine....
[Edited on 27/2/05 by flak monkey]
Sera
http://www.motosera.com
|
|
flak monkey
|
posted on 27/2/05 at 09:16 PM |
|
|
This pic is actually of the pinto flywheel... But it may be of some use... the dimensions on the right hand drawing show the minimum thickness
to turn down to.
Just for info the standard flywheel is 6.5kg...with the lightening shown its reduced to 4kg.
David
[Edited on 27/2/05 by flak monkey]
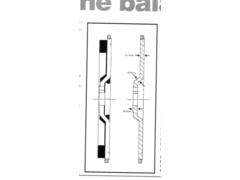 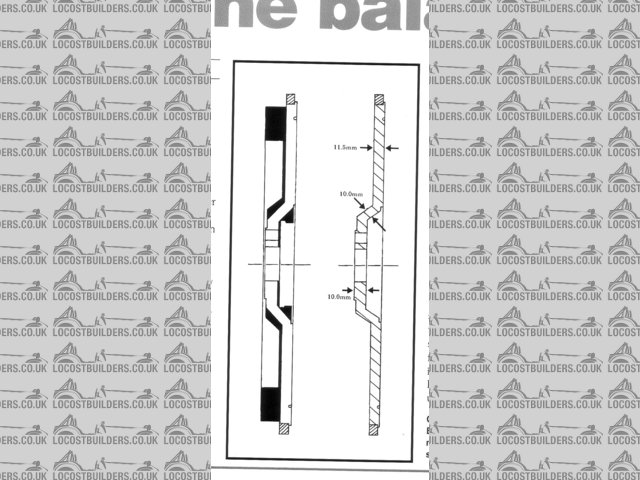 Rescued attachment flywheel lightened.jpg
Sera
http://www.motosera.com
|
|
gazza285
|
posted on 27/2/05 at 09:31 PM |
|
|
Bradford Grinders are probably the cheapest locally and have always done a good job for me.
http://www.bradfordgrinders.co.uk/index.htm
|
|
mangogrooveworkshop
|
posted on 27/2/05 at 09:50 PM |
|
|
If you get it wrong it goes big time!!!!! and nothing stops it as it eats its way thru metal, legs, ali and what ever.
|
|
flak monkey
|
posted on 27/2/05 at 09:58 PM |
|
|
Yes remember a 350mm flywheel spinning at juts 4000rpm has a peripheral speed of 165mph...
Not a lot will stop chunks of metal going that fast, including the bell housing, tunnel and you...
If in doubt...buy a professional steel lightened flywheel!
David
Sera
http://www.motosera.com
|
|
cidersurfer
|
posted on 27/2/05 at 10:01 PM |
|
|
quote: Originally posted by mangogrooveworkshop
If you get it wrong it goes big time!!!!! and nothing stops it as it eats its way thru metal, legs, ali and what ever.
Damn right, unless you know what you're doing it's a no brainer. This is what happens, good job it was a left hooker...
[Edited on 27/2/05 by cidersurfer]
shimming solid lifters is a job for a friend...
|
|
Ray Mc
|
posted on 27/2/05 at 10:23 PM |
|
|
I think everyone who engineers/builds anything, has to realise what their own engineering abilitys are, and work accordingly.
A similar danger exists if the wishbones, propshaft are poorly made?
|
|
cidersurfer
|
posted on 27/2/05 at 10:47 PM |
|
|
Ray
You are correct. 15 years of engineering experience and 5 years before that studying it here. Highly stressed items, such as the flywheel, prop,
wishbones, etc are too easy to get wrong with catastrophic results. There a lots of engineered designs out there which are compromised for various
reasons as manufacturers may use the same item for a variety of applications. If you know what you're doing go for it. I'd always get
somebody to check it though, measure it twice and cut it once!
[Edited on 27/2/05 by cidersurfer]
shimming solid lifters is a job for a friend...
|
|
Mark Allanson
|
posted on 27/2/05 at 10:53 PM |
|
|
quote: Originally posted by cidersurfer
Ray
You are correct. 15 years of engineering experience and 5 years before that studying it here. Highly stressed items, such as the flywheel, prop,
wishbones, etc are too easy to get wrong with catastrophic results. There a lots of engineered designs out there which are compromised for various
reasons as manufacturers may use the same item for a variety of applications. If you know what you're doing go for it. I'd always get
somebody to check it though, measure it twice and cut it once!
[Edited on 27/2/05 by cidersurfer]
At least then it will take your feet off with qualifications 
If you can keep you head, whilst all others around you are losing theirs, you are not fully aware of the situation
|
|
Mark Allanson
|
posted on 27/2/05 at 10:58 PM |
|
|
Ford didn't make the flywheel heavier just to make the car more unresponsive, it is carefully calculated to give the best compromise between
performance and ease of gear changing.
OK, in a lighter car you can get away with a slightly lighter flywheel, but not by much
If you can keep you head, whilst all others around you are losing theirs, you are not fully aware of the situation
|
|
cidersurfer
|
posted on 27/2/05 at 10:59 PM |
|
|
Nice island, err mount, no island, err....
Seriously though, it is too easy to get it wrong with highly stressed items, particularly when you're not proof testing it, and service life is
another thing...
[Edited on 27/2/05 by cidersurfer]
shimming solid lifters is a job for a friend...
|
|
Mark Allanson
|
posted on 27/2/05 at 11:15 PM |
|
|
I am a natural born coward with things that give a minor improvement, but have the ability to remove my feet 4" above the ankles. I think that
mounting a flywheel on the lathe and removing all the stress raisers is the most I would be prepared to do, even then it would probably destroy the
balance.
If you can keep you head, whilst all others around you are losing theirs, you are not fully aware of the situation
|
|
Ray Mc
|
posted on 27/2/05 at 11:49 PM |
|
|
The improvement in the angular acceleration of the flywheel can have fairly substantial gains when you take into account the tuning on the engine,
weight of the car etc.
The only part i am intrested in removing is the bulk on the outer rim of the flywheel(leaving the gears structurally safe). This is the safest part to
remove because it affects the structure least, but effects the moment of inertia/radius of gyration most. yes?
Providing the flywheel is clocked so that it is concentric to the axis of the lathe spindle and the face of the flywheel is also clocked so it is
running true to the lathe tool, then the balance of the flywheel should stay consistant, as you are removing material uniformly?
I suppose a way of checking it out would be to draw it up on solidworks and use the simulation ability to subject it to the forces involved an see
what factor of safety the computer rates it at, and check the stress diagram.
I had hoped someone had done this before and could give me some of their actual experience in how they went about it.
All said i probally look into prices of a steel flywheel that is already lightened or skeletonising a steel one it to suit the tuning of my engine,
and final car weight.
[Edited on 27/2/05 by Ray Mc]
[Edited on 28/2/05 by Ray Mc]
|
|
tomm
|
posted on 28/2/05 at 04:45 AM |
|
|
I've lightened several flywheels without any problems pinto/DOHC/and zetecs. though to be fair the max revs I've ever used are 7000. were
i to build a screamer, i'd use a steel flywheel too. but here are some figures,:
pinto can be reduced approx 2kgs
DOHC can lose at least 3.5kgs
1800zetec can lose 1.5kgs
it's important to have any corners radiused, and wherever posible take the weight from the o/s of the flywheel, I once bought an RJD pinto kit
which came with a lightened CI flywheel, it only weighed 3,6kg!! never had any probs. so yes it can be done, but common sense is obviously a useful
thign to have, err on the side of caution
|
|
britishtrident
|
posted on 28/2/05 at 07:35 AM |
|
|
Start with in a 1.4 cvh flywheel & clutch.
The clutch is a 7.5" dia same as 1.6 Xflo and Pinto flywheel is lighter also
|
|
NS Dev
|
posted on 28/2/05 at 08:31 AM |
|
|
Right, lets start at the top:
don't machine much off a std cast flywheel, I'll give my story after the practical and useful bit!
Second, steel flywheels are not made from cast steel, but from steel plate, usually either EN24T or EN16T, both of which have huge tensile
strength.
If you want to engineer your own flywheel and you have the machinery/skills, then just get a suitably oversized flame cut blank (oversized to remove
the heat affected zone from the flame cutting) cut from EN24T plate and machine it up from that.
Lastly, my story, somebody I used to know through rallying circles had built a VERY serious all steel crossflow engine, and bought a secondhand
"steel flywheel" for it. On one event he found to his cost that the "steel flywheel" was cast! It broke around the hub in the
centre when he missed a gear (tacho recall said 9500 rpm, but the limiter was 9000 anyway) and cut through the bellhousing, transmission tunnel,
clutch pedal, 1/2 way through the steering column, then changed direction and went back through the tunnel, through the remains of the bellhousing,
through the other side of the tunnel, through the inner and outer wings and across a field. All this was basically sawn through by the ring gear as
far as he could tell. Luckily his foot was not on the clutch at the time (he'd just come off it as the gear jumped out and hadn't put his
foot back on it by the time the flywheel came off!!!!!!!!) 
[Edited on 28/2/05 by NS Dev]
|
|