AdamR
|
posted on 23/3/10 at 10:11 AM |
|
|
DIY V8 headers
Thought I'd show a couple of pics of the headers I've been cobbling together.
I'm a bit concerned about them cracking, as other builders seem to have had problems with that happening. My headers are particularly complex, so
have lots of welded joints. As I've used MIG, each weld has needed some dressing to get a smooth joint - so the wall thickness around each weld
probably varies quite a lot too.
So... two questions: Where am I likely to see cracks appearing, and what can I do to strengthen the headers to prevent the cracking before it
happens?
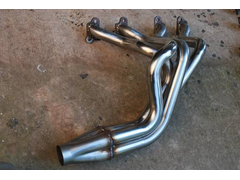 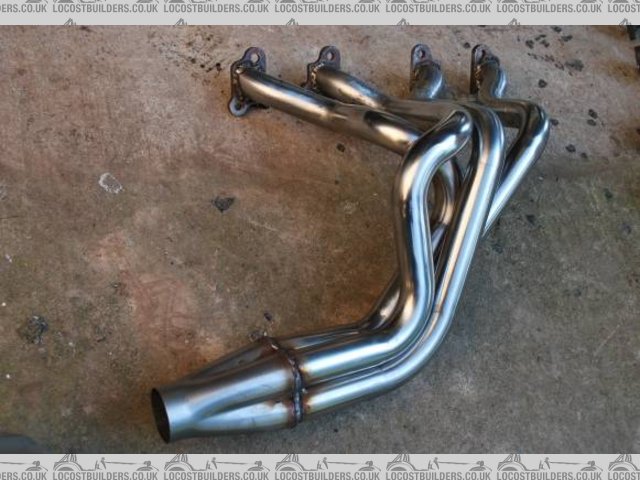 Headers2
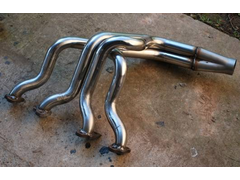 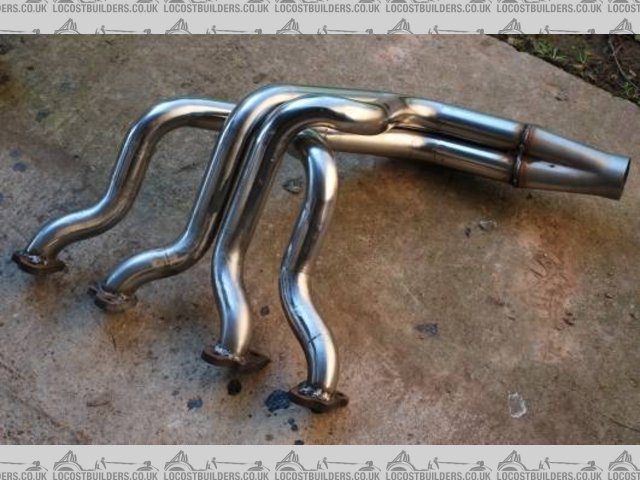 Headers4
|
|
|
turbodisplay
|
posted on 23/3/10 at 10:16 AM |
|
|
Between the flange and the pipes is the first port of call. It looks good what you have done, and it will ruin the looks, but you need strip to spread
the load out. A few strips from the flange to 50 - 75mm along the pipe.
Darren
[Edited on 23/3/10 by turbodisplay]
|
NOTE:This user is registered as a LocostBuilders trader and may offer commercial services to other users
|
Irony
|
posted on 23/3/10 at 10:16 AM |
|
|
More importantly when you get it right how much would you charge me for a set? I am building a V8 and will need exhausts in the future. hehe
|
|
MK9R
|
posted on 23/3/10 at 10:17 AM |
|
|
How about adding a brace to the end of the header that goes back to the engine so there is no movement fighting the header? Then use somekind of flexi
joint between the header and rest of the exhaust
Nice job by the way!!
[Edited on 23/3/10 by MK9R]
Cheers Austen
RGB car number 9
www.austengreenway.co.uk
www.automatedtechnologygroup.co.uk
www.trackace.co.uk
|
|
cadebytiger
|
posted on 23/3/10 at 10:55 AM |
|
|
that is amazing!
|
|
wilkingj
|
posted on 23/3/10 at 11:00 AM |
|
|
What material is it all made from?
If its ALL stainless, is it all the same grade?
Are there any Ordinary steel to Stainless welds?
Did you use the correct filler rod for the materials being welded (even for the stainless joints)?
I ask, as if you weld ordinary steel to Stainless and use the wrong filler rods, then you get embrittlement, as it makes it very hard, and will then
crack with the stress (ie getting hot and cold as its an exhaust).
I am no expert, but I know this is the case for dissimilar metal welding, especially stainless and ordinary steel.
(I was thinking of the flanges, as they look like ordinary steel)
I would ask 907, as he is the expert on these matters.
Other than that it looks good.. a nice job.
1. The point of a journey is not to arrive.
2. Never take life seriously. Nobody gets out alive anyway.
Best Regards
Geoff
http://www.v8viento.co.uk
|
|
AdamR
|
posted on 23/3/10 at 01:37 PM |
|
|
Thanks for the positive feedback! The headers certainly took a lot of effort to create, which is why I don't want them to break after a few
hundred miles of action.
Re material, the tube is 304 stainless, the flanges are mild steel, recycled from an old set of headers. All welded with stainless wire - I think 308
grade, though not 100% sure as it doesn't say on the pack.
Flange->pipe joints can be improved as per turbodisplay's suggestion. Anything else?
The idea of bracing the end of the header is interesting but might be a bit difficult to engineer.
[Edited on 23/3/10 by AdamR]
|
|
FASTdan
|
posted on 23/3/10 at 04:41 PM |
|
|
Thats really well done - especially considering your using a MIG. 
|
NOTE:This user is registered as a LocostBuilders trader and may offer commercial services to other users
|
Canada EH!
|
posted on 23/3/10 at 05:37 PM |
|
|
You could put some spot welds were the pipes cross each other, will tend to keep the flanges supported, might not look pretty though.
|
|
robinj66
|
posted on 23/3/10 at 09:25 PM |
|
|
Extremely well done - they look superb
|
|