phelpsa
|
posted on 7/12/04 at 05:24 PM |
|
|
Elastic band powered Dragster
What material to make the chassis out of?
My first DT project
The rules are:
Must be smaller than 400x150x150.
Choice of materials : Steel, ally, wood, perspex.
Adam
|
|
|
JoelP
|
posted on 7/12/04 at 05:26 PM |
|
|
i would make the part that holds the rubber band out of steel, anything else out of ally where possible. sounds fun!
the aim must be to store as much energy as possible and use it to propel as light a car as you can manage!
[Edited on 7/12/04 by JoelP]
|
|
phelpsa
|
posted on 7/12/04 at 05:28 PM |
|
|
It will be. Thanks Joel.
Was thinking about the weight of ally compared to perspex/wood.
Adam
|
|
splitrivet
|
posted on 7/12/04 at 05:47 PM |
|
|
I would go for balsa wood light easy to cut etc.
Its what we used to make rubber powered planes from.
Cheers,
Bob
I used to be a Werewolf but I'm alright nowwoooooooooooooo
|
|
JoelP
|
posted on 7/12/04 at 05:51 PM |
|
|
good point about balsa bob. i compared steel to wood etc but forgot to consider the ally alternatives!
variable wheel size, depending on the length track.
hey, wouldnt it be fun to have a LCB laggy band dragster race! kids get all the fun...
joel>>> off to toys'r'us now
|
|
scoobyis2cool
|
posted on 7/12/04 at 06:04 PM |
|
|
I did this as a first year uni project, we made ours out of balsa wood with big foamboard wheels - very light and low moment of inertia on the wheels.
We also put rubber bands around the wheels to make a basic tyre to give a bit more grip.
One thing to look out for is the way you design the power mechanism - if you're not careful the rubber band will put all its energy into getting
the car moving, and then wrap itself up the other way and slow the car down. Quite a few teams looked to be doing pretty well only to have their car
suddenly stop and reverse back along the track!
Pete
It's not that I'm lazy, it's that I just don't care...
|
|
Peteff
|
posted on 7/12/04 at 06:10 PM |
|
|
On the aeroplane tack
Drive it with a propellor and then it will freewheel after the laggy band runs down.
yours, Pete
I went into the RSPCA office the other day. It was so small you could hardly swing a cat in there.
|
|
Matthew_1
|
posted on 7/12/04 at 06:17 PM |
|
|
If you don't actually attach the laggy band to the rear axle, but just wrap in around once so it effectively holds itself on, then when you run
out of "tug" the band will just drop off and the car should carry on ?
|
|
phelpsa
|
posted on 7/12/04 at 06:29 PM |
|
|
Thats what I was going to do. A propellor would just be more weight.
Adam
|
|
Chris_R
|
posted on 7/12/04 at 07:08 PM |
|
|
I did it too when I was at school. the rear axel was a length of dowel with a blunted panel pin hammered through it. The elastic band was hooked onto
the pin which allowed it come loose when it had turned the axel the appropriate number of times.
A bit of slapstick never hurt anyone.
http://www.chris.renney.dsl.pipex.com/
|
|
scoobyis2cool
|
posted on 7/12/04 at 07:37 PM |
|
|
Yeah we did ours by hooking the band onto the axle so it would come loose, but some people tied theirs solid to the axle. idiots...
Pete
It's not that I'm lazy, it's that I just don't care...
|
|
phelpsa
|
posted on 7/12/04 at 07:58 PM |
|
|
Some good ideas coming. Any other tips?
Adam
|
|
Chris_R
|
posted on 7/12/04 at 08:02 PM |
|
|
Would a flywheel be any good?
A bit of slapstick never hurt anyone.
http://www.chris.renney.dsl.pipex.com/
|
|
Volvorsport
|
posted on 7/12/04 at 08:05 PM |
|
|
do it downhill?
an ABS or perspex chassis may be a little more sturdy than balsa , depends how long its got to last , wether the opposition has done it etc .
For wheel bearings , try to get the least friction , for a radio controlled car project , the axles i used were mounted in thin ally to reduce
friction as much as possible , fairy liquid may help , altho it can be too viscous , maybe water it down a bit , or use some small amoumts of
molybendum
|
|
MikeRJ
|
posted on 7/12/04 at 08:09 PM |
|
|
quote: Originally posted by phelpsa
Some good ideas coming. Any other tips?
Adam
Ever see "The great egg race" on TV? Fantastic series, like a mini version of Scrapheap Challenge but with far more emphasis on the
science aspect.
They had rubber powered dragsters, and one of them had a cunning plan for variable gearing. The rubber band was attached to a string which was wound
around a narrow pulley on the rear axle. When the dragster started, the gear ratio would be low to get good acceleration, and the further it went the
higher the gear ratio would get as the string unwound and made the effective dimater smaller.
Is the emphasis on maximum speed, distance or time?
[Edited on 7/12/04 by MikeRJ]
|
|
phelpsa
|
posted on 7/12/04 at 08:23 PM |
|
|
6 meters, quickest person wins.
Adam
|
|
MikeRJ
|
posted on 7/12/04 at 08:43 PM |
|
|
Does the power unit have to be in the car? I'm thinking big catapult 
|
|
phelpsa
|
posted on 7/12/04 at 08:47 PM |
|
|
Yep. Must be in the car.
Adam
|
|
MikeRJ
|
posted on 7/12/04 at 09:01 PM |
|
|
Well, just make sure you engineer it to extract all the energy from the rubber band. Is there a standard "control" rubber band that
everyone will be issued with, or is it a free for all? If so, obviously get the longest, thickest one you can.
You need to design the chassis so you can put the maximum amount of stretch into the whole band, not just part of it (i.e. don't wrap the rubber
band around the back axle, a big chunk of the band won't be doing anything usefull). If the band at max stretch won't fit in the length
of the vehicle, consider a low friction pulley arrangement to fold the band one or more times up and down the car. Use talcum powder to lubricate the
band on pulleys etc.
Be carefull how you attach the ends of the band, don't want any sharp edges that could cause failure.
Be very carefull working out the gearing. If you have it wrong the car will either sit spinning it wheels until most of the bands energy has gone, or
will trundle off the line like a tortoise.
|
|
JoelP
|
posted on 7/12/04 at 09:08 PM |
|
|
i was gonna mention a CVT type drive, with a cone shaped spinner. and maybe a bike pedal type device to allow it to free wheel after the band is
unwound.
does it follow a rail or is self centering an issue?
[Edited on 7/12/04 by JoelP]
|
|
phelpsa
|
posted on 7/12/04 at 09:21 PM |
|
|
I was thinking something like this. The peg would be enough to hold the elastic band on but not keep it on, so it would come of when it runs out.
Adam
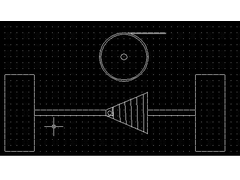 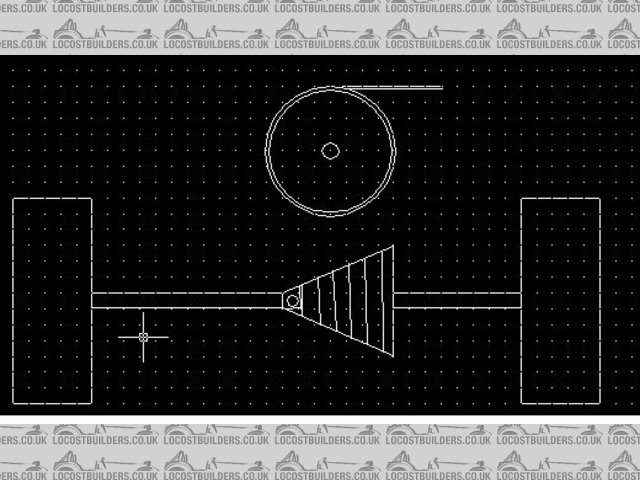 Rescued attachment untitled.JPG
|
|
phelpsa
|
posted on 7/12/04 at 09:23 PM |
|
|
P.S. the outer bit of the cone would act as a flywheel.
Adam
|
|
JoelP
|
posted on 7/12/04 at 09:38 PM |
|
|
its gonna take many experiment runs, to hone it to the track length. i wouldnt put extra weights in to make a flywheel - if the rubber band is spent
by the end, you havent wound it up enough! hence the flywheel is extra mass (both static and rotational).
bear in mind, in the diagram above, when the band has wound itself down to the narrow part, you need max torque to to keep it going. But the band will
barely have any pull left.
the benefit of twisting it end to end, is that it has a uniform 'powerband'. but then, the axis of rotation is wrong. and, its harder to
do the CVT approach.
also, if the band lasts til the end of the run, it doesnt matter if it gets wound back up in reverse.
|
|
phelpsa
|
posted on 7/12/04 at 10:01 PM |
|
|
I've got a couple of months to complete it so I expect there will be a lot of tests. I will have to try both approaches and see which one is
best. Just as I finished that post my DT teacher (who is on duty in the house) came in and said about torque being the problem and that I would have
to be very clever to get it right.
Adam
|
|
phelpsa
|
posted on 7/12/04 at 10:03 PM |
|
|
P.S. The outer would ACT loke a fly wheel but I wouldn't add anything to it.
|
|