irvined
|
posted on 7/9/09 at 01:56 PM |
|
|
Solidworks Mates
I have a solidworks question:
I've create a rod-end assembly - its basically a ball, inside a cavity, and its mated using a concentric mate using the faces of the ball and
cavity so that the ball can rotate along all axises, as would a rod end in real life. This all works perfectly fine when viewing the assembly.
However, when I use this assembly as part of say a suspension arm, the mate becomes fixed, and I can't move the ball independently of the rod
end, subsequently I have a suspension assembly that I can't assemble.
What is the correct way to achieve what I'm trying to do? I expect that I either need a different type of mate. If I put it all in one assembly
then I get the desired effect, but obviously that sort of defeats the point of sub assemblies.
http://irvined.blogspot.com
|
|
|
m8kwr
|
posted on 7/9/09 at 02:10 PM |
|
|
Just so i am right, photo below show what i have done, and the movement
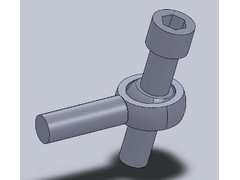 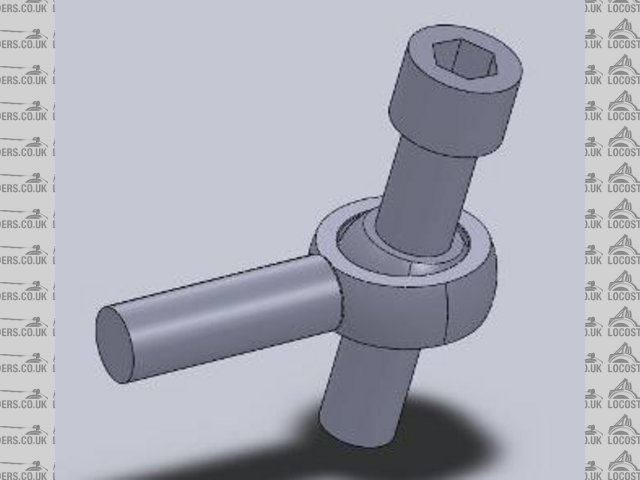 Description
 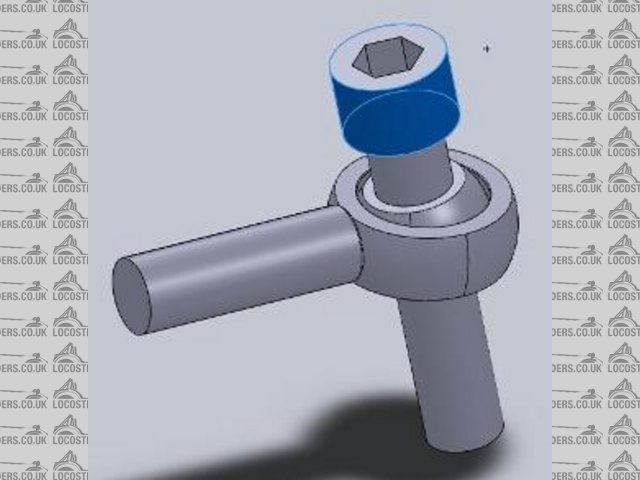 Description
I had a similar problem to yours, but i had created a part as whole rose joint. BUt then i thought about it, and created 2 parts to create the
assembly - so it could be that simple.
In your assembly you need a fixed part.
I have also put limits on the movement of the rose joint, so parts can not go through each other, so when i get around to making the complete
suspension assembly it should move exactly like it i made it (well thats the plan)
If you want U2U me your email address and i will send you my parts so you can mess about with them, and i also have a suspension parts made up, which
may assist you if you are yet to create them...
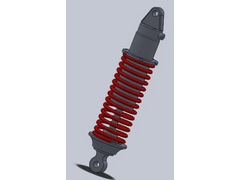 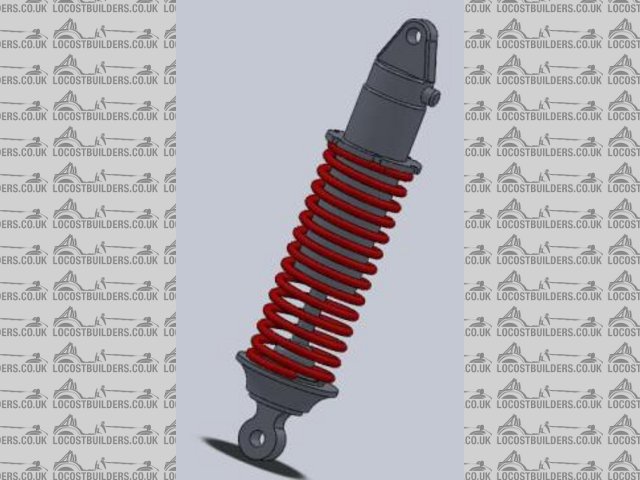 Description
Also what version are you using???
|
|
balidey
|
posted on 7/9/09 at 02:15 PM |
|
|
in your top level assy, find the sub assy in the tree, right click (or click the tab dependnig on version) and you should see the component
properties, then tick the Solve as flexible, ie untick the solve as rigid.
[Edited on 7/9/09 by balidey]
|
|
Moorron
|
posted on 7/9/09 at 02:20 PM |
|
|
quote: Originally posted by balidey
in your top level assy, find the sub assy in the tree, right click (or click the tab dependnig on version) and you should see the component
properties, then tick the Solve as flexible, ie untick the solve as rigid.
yep i second this, its a setting in the main top assembly not your rod end assembly. For some reason it defaults to fixed and means you cant move it.
i remember the day when in solidworks 2001 your did this but had the same sub assembly twice in your main assembly and it all went bad if you tried to
mate this bits differently to each other. in other words your could only mate one sub assembly up without getting errors
[Edited on 7/9/09 by balidey]

Sorry about my spelling, im an engineer and only work in numbers.
|
|
balidey
|
posted on 7/9/09 at 02:20 PM |
|
|
here....

|
|
Moorron
|
posted on 7/9/09 at 02:21 PM |
|
|
wopsie looks like i edited your qoute! hehe
Sorry about my spelling, im an engineer and only work in numbers.
|
|
balidey
|
posted on 7/9/09 at 02:23 PM |
|
|
quote: Originally posted by Moorron
. i remember the day when in solidworks 2001 your did this but had the same sub assembly twice in your main assembly and it all went bad if you tried
to mate this bits differently to each other. in other words your could only mate one sub assembly up without getting errors
Yep, I remember that well. Number of my models had sub-assy's called RAM1, RAM2, RAM3 etc and they were all the same, just copies of each other.

|
|
irvined
|
posted on 7/9/09 at 02:35 PM |
|
|
You guys rock,
Setting it to flexible is indeed the way forward, spent hours trying to work that one out.
http://irvined.blogspot.com
|
|