daz89
|
posted on 26/9/18 at 11:35 AM |
|
|
properly keeping track of a vehicle project or restoration is too time intensive or complicated. agree or disagree?
Hi everyone,
just a quick one regarding vehicle restoration and projects, my poll is an agree/disagree on the subject of "properly keeping track of a vehicle
project or restoration is too time intensive or complicated"
By 'keeping track' I mean collating the information to be useful later (reassembly, re-ordering parts, remembering what has been done / is
left to do etc.)
also after you have submitted your poll answer, if you have any insights into why you agree/disagree please feel free to comment.
Thanks
|
|
|
Mr Whippy
|
posted on 26/9/18 at 12:00 PM |
|
|
when you get to near the end of your restoration...take your own poll I know what you'll vote  
here's a few hints -
1) Take loads of photos, can never have too many, make them bright and high resolution, put them in folders for each area of the car, dash, engine
etc... especially the engine hoses, pipes wiring etc
2) Never take off bolts, screws, clips etc and put them in jars, you will never remember where they all go, just screw them back into the part once
removed...will save your sanity that one
3) Store stuff you take off in named boxes and only put parts from say the engine in a box, don't mix it up with brake parts etc.
4) Create a spreadsheet and use it to track what your doing, google sheets has a free one that's excel compatible, doesn't need to be
complex, below is what I use, I have these for everything, cars, house, stove, work...everything
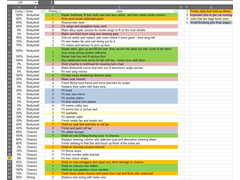 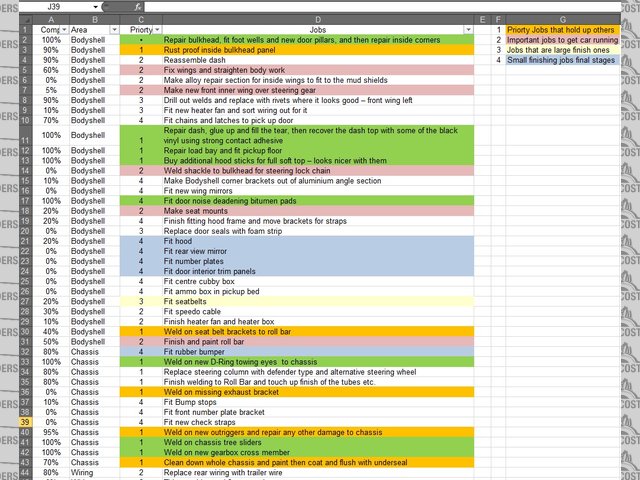 Description
Hope you've got lots of pennies and time
here's another one -
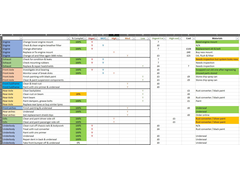 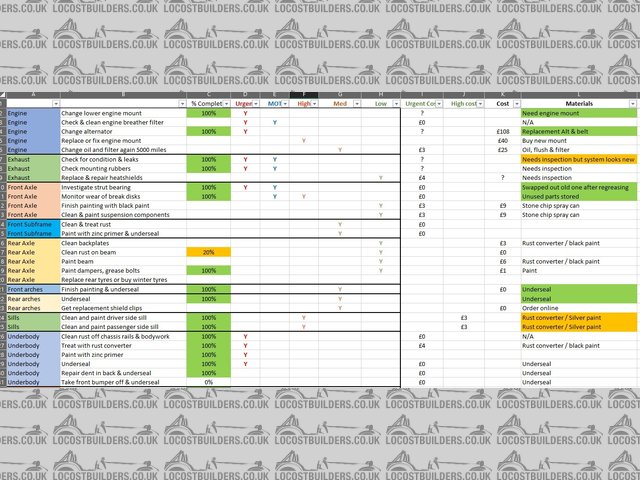 Description
I'm a engineering planner so my head is mince most of the time with just too many things to track
[Edited on 26/9/18 by Mr Whippy]
|
|
russbost
|
posted on 26/9/18 at 12:15 PM |
|
|
Agree with everything Mr Whippy has said, tho' I wouldn't bother with a spreadsheet I simply use pen & paper &, if necessary a
copier to copy/modify notes. A few hours "wasted" during stripping can save days upon days during re-assembly, if you don't have the
patience to do that then I would suggest don't undertake a restoration, it can be a very frustrating game where sometimes you feel as tho'
you are going backwards rather than forwards!
Good luck with the project whatever it is
I no longer run Furore Products or Furore Cars Ltd, but would still highly recommend them for Acewell dashes, projector headlights, dominator
headlights, indicators, mirrors etc, best prices in the UK! Take a look at http://www.furoreproducts.co.uk/ or find more parts on Ebay, user names
furoreltd & furoreproducts, discounts available for LCB users.
Don't forget Stainless Steel Braided brake hoses, made to your exact requirements in any of around 16 colours.
http://shop.ebay.co.uk/furoreproducts/m.html?_dmd=1&_ipg=50&_sop=12&_rdc=1
|
NOTE:This user is registered as a LocostBuilders trader and may offer commercial services to other users
|
Bluemoon
|
posted on 26/9/18 at 12:45 PM |
|
|
With Mr Whippy, it takes so long (years unless you are not working!!) that you will never remember where things go!! Lots of photos... Also the order
you do things should be taken into account.
|
|
nick205
|
posted on 26/9/18 at 01:05 PM |
|
|
Take plenty of photos as you go, including parts with brands and part numbers if you can.
Keep a spreadsheet of sources for parts with costs etc.
For me I don't really keep a tab on time spent on the project - I'm working for a living so there's other things to be doing.
Again for me (and the next owner) it was impotant to know brands and part numbers of parts used. With this information available you can source
replacements in the future.
|
|
Slater
|
posted on 26/9/18 at 02:33 PM |
|
|
I did the same as Mr Whippy, used a similar spreadsheet to log the details of the sierra donor stripdown, parts refurb and building of my kit. This
included the approx time taken and cost of each task. I even deducted the loose change I found under the seat in the donor!
I've kept the spreadsheet up to date with all the modifications and costs etc since getting it on the road.
So now I can tell you how much the whole project has cost and how long it took me, so far.....
Photos are very useful indeed.
Why do they call Port Harcourt "The Garden City"?...... Becauase they can't spell Stramash.
|
|
nero1701
|
posted on 26/9/18 at 06:59 PM |
|
|
quote: Originally posted by Slater
I did the same as Mr Whippy, used a similar spreadsheet to log the details of the sierra donor stripdown, parts refurb and building of my kit. This
included the approx time taken and cost of each task. I even deducted the loose change I found under the seat in the donor!
I've kept the spreadsheet up to date with all the modifications and costs etc since getting it on the road.
So now I can tell you how much the whole project has cost and how long it took me, so far.....
Photos are very useful indeed.
then minus 45% before you show the Mrs....
|
|
steve m
|
posted on 26/9/18 at 08:30 PM |
|
|
quote: Originally posted by nero1701
quote: Originally posted by Slater
I did the same as Mr Whippy, used a similar spreadsheet to log the details of the sierra donor stripdown, parts refurb and building of my kit. This
included the approx time taken and cost of each task. I even deducted the loose change I found under the seat in the donor!
I've kept the spreadsheet up to date with all the modifications and costs etc since getting it on the road.
So now I can tell you how much the whole project has cost and how long it took me, so far.....
Photos are very useful indeed.
then minus 45% before you show the Mrs....
Or be honest, as my car costs stands at just over 6k, and its been on the road for 20 years and that includes building it, Mots and maintenance, car
tax and insurance plus a few engines
steve
Thats was probably spelt wrong, or had some grammer, that the "grammer police have to have a moan at
 
|
|
nero1701
|
posted on 26/9/18 at 08:38 PM |
|
|
quote: Originally posted by steve m
quote: Originally posted by nero1701
quote: Originally posted by Slater
I did the same as Mr Whippy, used a similar spreadsheet to log the details of the sierra donor stripdown, parts refurb and building of my kit. This
included the approx time taken and cost of each task. I even deducted the loose change I found under the seat in the donor!
I've kept the spreadsheet up to date with all the modifications and costs etc since getting it on the road.
So now I can tell you how much the whole project has cost and how long it took me, so far.....
Photos are very useful indeed.
then minus 45% before you show the Mrs....
Or be honest, as my car costs stands at just over 6k, and its been on the road for 20 years and that includes building it, Mots and maintenance, car
tax and insurance plus a few engines
steve
Was typed a bit tongue in cheek Steve...
|
|
steve m
|
posted on 26/9/18 at 09:05 PM |
|
|
Me too, my Wifes a Medium, and knows about two days before im going to Lie ..................
[Edited on 26/9/18 by steve m]
Thats was probably spelt wrong, or had some grammer, that the "grammer police have to have a moan at
 
|
|
daz89
|
posted on 26/9/18 at 09:50 PM |
|
|
The question may have mislead slightly as I may not have worded it as well as I hoped (I didn’t want the question to lead too much as I wanted the
most honest feedback possible.) I feel that the process of recording a build could be streamlined massively to lessen the time spend and complexity of
keeping good records. I’m currently trying to get traction behind an idea that solves the issue, starting with identifying issues people currently
have. So thank you very much for your answers, and your comments have been particularly helpful (what else could I expect from members of the Locost
community?)
As a side note, I am looking to ask advice going forward, so if you feel that a solution towards streamlining the recording process of a build or
restoration interests you I would ask you to drop me a DM and I’ll add you to my test group, which will help me make sure that I’m heading the right
way (and will hopefully lead to you guys getting a new resource that assists you in the future.)
Thanks again for the feedback guys
|
|
Mr Whippy
|
posted on 26/9/18 at 11:56 PM |
|
|
I'm a big fan of google drive. You could set up a free account like mycarbuild@gmail and it then gives you a great storage area for all you car
build stuff, linked automatically to your photos, videos, documents, PDF's, spreadsheets etc. You get 15GB of free storage and you can then
share if you want to facebook etc many of the features tbh I haven't even tried there's so many to choose. We used to be in a world of
kids photo and document hell till we discovered it and now its all handled for us without having to think about it. Bliss
Have a look I'd recommend it
|
|
WallerZero
|
posted on 27/9/18 at 11:11 AM |
|
|
Of course its time intensive, the whole project is! I built my kit in the evenings and weekends, took pictures and wrote a blog whilst I was at work
lol. Since rebuilding with the V6 I haven't been able to keep it up to date at work due to job change and bigger workload so its a year behind
as I have a busy home life too. One day I'll catch up though.
In regards to logging things done, parts ordered, work instructions/methods etc, that comes in use when you need to do something. You'll thank
yourself when you forget which part is what on your hybrid clutch assembly or the gasket you forgot until you're there covered in oil that takes
2 weeks to order.
I see it as part of the project and as with any part, its up to the builder to decide if its worth it. Putting nuts on all the bolts is time
intensive...but you still do it
http://zachsgbszero.blogspot.co.uk/
|
|
b14wrc
|
posted on 27/9/18 at 11:15 AM |
|
|
Hey,
I have taken loads of photos and can't recommend that method highly enough........
I haven't kept any records of cost and time, to me the whole point of this project is for an as uncompromised raw car as possible. I even
"waste" hours just sitting in my garage thinking it through and playing with bits of card board to visualise what I want to do next with
the car!
Nothing better than a couple of hours in the garage with a Henry Westons Cider and some music working out the next steps of my project!
Rob
20vt powered rear engined locost
|
|
Mr Whippy
|
posted on 27/9/18 at 11:22 AM |
|
|
quote: Originally posted by b14wrc
I even "waste" hours just sitting in my garage thinking it through and playing with bits of card board to visualise what I want to do next
with the car!
Nothing better than a couple of hours in the garage with a Henry Westons Cider and some music working out the next steps of my project!
Rob
Usually "wasted" hours involves -
1) Constant pointless mock assembly to see how great it will look
2) standing about admiring how great it looks
3) sitting inside it going BRRRRUUUUMMM! thinking how great your going to look in it....
|
|
Irony
|
posted on 27/9/18 at 04:06 PM |
|
|
Take photos and sometimes videos if needed. I stripped my 4 barrel cars down and uploaded the videos to youtube for my references and they for some
reason have 2K views now.
I found it best if I was halfway through a job to jot down on a notepad where I was at the end of a garage session. I once wired in a 50m roll of
wire into the loom. Didn't go back to that job for a couple of weeks and then couldn't remember why I had wired it in. Never found out
and after six months I cut it out because I just couldn't remember why I put it there
|
|
StevieB
|
posted on 27/9/18 at 04:40 PM |
|
|
I'm doing a resto on a 1989 Suzuki RGV 250 at the moment (slowly).
I think it's entirely necessary to keep track of things. The work itself needs to be organised so it's a pleasure to work on and tracking
money and progress helps keep you motivated - put some milestones in place and celebrate when you hit one (engine in, engine start, first time the
lights work - however you want to divide it down and make an excuse to reward yourself with beer!).
Having done a few kits and bikes over the years, I've got a system of having many plastic boxes for sub assemblies to go into and make use of
small plastic bags to put fasteners into, which are then zip tied to the relevant parts. If there's anything peculiar, I take plenty of
photo's as I go and also make use of parts micro fiches from the internet (depends on the project - a BMW motorcycle is a dream to find the
fiches and part numbers, the Suzuki not quite so easy).
It's then a question of breaking the project into sections - engine, fuel system, electrics, front end, rear end, bodywork etc.
Bikes are much easier to work on than cars as they're much smaller and you therefore have a lot more space around you to neatly store parts.
A whiteboard in the garage helps - I use a Kanban system of To do, Doing and Done lists which I then use to make a parts list from the To Do section.
This means I can place the parts order on a Sunday night and usually have the parts in the garage ready to go by the next weekend.
Trello is a good app to make things more digital which is worth looking at. I use the whiteboard to note things as I work and then transfer into the
app every now and then. That way if I'm sat at work and have a free minute where I want to think about the build I have everything to hand
rather than trying to recall from memory.
I also try and keep track of cost and an eye on the total outturn on a spreadsheet - this helps me keep an eye on how much I need to scrimp and save
and ultimately how long the project is likely to take me and also when the big money hits will land (paintwork mainly, which is usually the final
throes of any bike rebuild).
I've found it works really well. However, I'm the sort of person who derives pleasure from working in an organised way and gets very
stressed the things aren't just so - this is all a hobby and therefore it shouldn't be a stressful experience in my book!
All of the above sounds a to more ideal than the reality - everything is well organised but progress is slow as I get little garage time at the
moment, hence the need to be organised so when I do go back in there I can quickly figure out where I left off.
|
|
StevieB
|
posted on 27/9/18 at 04:43 PM |
|
|
quote: Originally posted by Irony
I found it best if I was halfway through a job to jot down on a notepad where I was at the end of a garage session. I once wired in a 50m roll of
wire into the loom. Didn't go back to that job for a couple of weeks and then couldn't remember why I had wired it in. Never found out
and after six months I cut it out because I just couldn't remember why I put it there
When I built my first kit, I did all of the nylocks just finger tight so I could torque up later. Later was 4 years later and was figured out after
feeling the car was a bit of a sloppy handler on it's first ever outing (on track, pre-SVA).  
Hence why I'm quite organised now...
|
|
Mr Whippy
|
posted on 28/9/18 at 06:01 AM |
|
|
quote: Originally posted by StevieB
quote: Originally posted by Irony
I found it best if I was halfway through a job to jot down on a notepad where I was at the end of a garage session. I once wired in a 50m roll of
wire into the loom. Didn't go back to that job for a couple of weeks and then couldn't remember why I had wired it in. Never found out
and after six months I cut it out because I just couldn't remember why I put it there
When I built my first kit, I did all of the nylocks just finger tight so I could torque up later. Later was 4 years later and was figured out after
feeling the car was a bit of a sloppy handler on it's first ever outing (on track, pre-SVA).  
Hence why I'm quite organised now...
Perhaps the use of a coloured paint pen on tightened bolts will prevent that, you see this a lot in engineering
|
|
nick205
|
posted on 28/9/18 at 08:23 AM |
|
|
quote: Originally posted by StevieB
quote: Originally posted by Irony
I found it best if I was halfway through a job to jot down on a notepad where I was at the end of a garage session. I once wired in a 50m roll of
wire into the loom. Didn't go back to that job for a couple of weeks and then couldn't remember why I had wired it in. Never found out
and after six months I cut it out because I just couldn't remember why I put it there
When I built my first kit, I did all of the nylocks just finger tight so I could torque up later. Later was 4 years later and was figured out after
feeling the car was a bit of a sloppy handler on it's first ever outing (on track, pre-SVA).  
Hence why I'm quite organised now...
A note on the inside of the garage door to "tighten nuts before driving" is dirt cheap and hard to ignore 
|
|
StevieB
|
posted on 28/9/18 at 08:43 AM |
|
|
quote: Originally posted by nick205
quote: Originally posted by StevieB
quote: Originally posted by Irony
I found it best if I was halfway through a job to jot down on a notepad where I was at the end of a garage session. I once wired in a 50m roll of
wire into the loom. Didn't go back to that job for a couple of weeks and then couldn't remember why I had wired it in. Never found out
and after six months I cut it out because I just couldn't remember why I put it there
When I built my first kit, I did all of the nylocks just finger tight so I could torque up later. Later was 4 years later and was figured out after
feeling the car was a bit of a sloppy handler on it's first ever outing (on track, pre-SVA).  
Hence why I'm quite organised now...
A note on the inside of the garage door to "tighten nuts before driving" is dirt cheap and hard to ignore
I've taken to putting a similar note but on the steering wheel (or handlebars as the case may be). Anything to avoid that 'Did I bleed
the brakes' thought the first time you drive down the road!
Just the little things you learn along the way 
|
|
Mr Whippy
|
posted on 28/9/18 at 11:04 AM |
|
|
quote: Originally posted by nick205
quote: Originally posted by StevieB
quote: Originally posted by Irony
I found it best if I was halfway through a job to jot down on a notepad where I was at the end of a garage session. I once wired in a 50m roll of
wire into the loom. Didn't go back to that job for a couple of weeks and then couldn't remember why I had wired it in. Never found out
and after six months I cut it out because I just couldn't remember why I put it there
When I built my first kit, I did all of the nylocks just finger tight so I could torque up later. Later was 4 years later and was figured out after
feeling the car was a bit of a sloppy handler on it's first ever outing (on track, pre-SVA).  
Hence why I'm quite organised now...
A note on the inside of the garage door to "tighten nuts before driving" is dirt cheap and hard to ignore
Open the garage door, can't see message, phone rings...come back...drive off 
|
|
jps
|
posted on 28/9/18 at 11:54 AM |
|
|
A load of great hints and tips here - I myself started off with a fairly haphazard approach to things - although one reason for starting my blog was
to have a record for myself of what I had done. I started a Google Sheet close to starting my build primarily to keep track on costs and I also
started off with something of a 'just in time' to do list, i.e. I sketched out upcoming tasks just before I started them!!
When I decided at the beginning of this year that I was going to focus properly on making progress I decided it was important to be as efficient in my
effort as possible - so started to look at sequencing work so that I was not doing things like fit the suspension one week to do something then spend
time taking it back off the next week to do something else... I found that a bit complicated as there is no 'right' sequence, although
there are certain dependencies I felt it sensible to go with (finish all chassis welding before fitting GRP side panels for example..!)
As a result I have a programme of work like the example Mr Whippy has shown above, but with tasks grouped up to show the dependent stages. I do need
to spend a bit more time planning properly really, but for now I have a decent chunk of tasks to do which won't cause problems to be done at
this stage...
My original plan was also to adopt the 'sort the parts order for next weekend at the end of this weekend' approach - but I never manage to
get that organised!
Within my planning docs I have also grouped together build info - such as torque values, parts spec, etc. And I have also used it as a point to
collate links to things like forum posts which cover specific jobs i've got to do.
|
|
Mr Whippy
|
posted on 28/9/18 at 01:49 PM |
|
|
One thing I will say is don't spend to much time working on it, sounds daft but rather than spending 10...15 hours on a weekend burning yourself
out and ending up feeling like crap.
Much better I find is to go out and spend an hour or so each night picking one or two jobs that can be completed, then go back inside. Since
you're always getting jobs completed and you're not tired and each day progress continues to be made this keeps motivation high. This and
using a tracker that highlights jobs that are complete insures your focused and keen for the next job I even go to the extent if having a meal out
as a celebration once a big job is done 
|
|
froggy
|
posted on 28/9/18 at 02:05 PM |
|
|
Yep I Just have a whiteboard and keep doing a bit every night even if I can only do an hour , I don’t bother with build threads anymore just post the
odd interesting bit on fb which is quite nice now after 8 yrs to get the odd reminder of what I was doing most of which I’d forgotten
[IMG]http://i144.photobucket.com/albums/r187/froggy_0[IMG]
|
|