MikeR
|
posted on 11/4/06 at 11:01 PM |
|
|
joining wires
Simple question. Whats the best way to join two wires?
For example, existing steering column plug with 3" wire on it. What is the best way to join it to my wiring loom?
Strip 2cm of each, tin, twist along side each other, solder and then cover with heat shrink tube?
Or ????????
|
|
|
esn163
|
posted on 11/4/06 at 11:10 PM |
|
|
thats what we've done seems to work OK. Strip wires, twist each, tin each seperately then heat the two up together to join them works well. Then
used heat shrink and / or insulating tape where heat shrink couldn't be used
Ed
[Edited on 11/4/06 by esn163]
Indy Build Photos
** Build pages **
Photo Bucket Pics
|
|
Dusty
|
posted on 11/4/06 at 11:40 PM |
|
|
If the wires are clean then they can be twisted together without tinning and then soldered with a flux cored solder. Makes for a thinner join but it
will still be stiff. I've just had a major tidy up of my loom and fitted fuel injection and thats how I'm doing joins.
|
|
Kissy
|
posted on 12/4/06 at 06:34 AM |
|
|
Try not to let solder capillary too far up the wires at it will render them likely to fracture in time. Use adhesive lined heatshrink if you can
(RS), it seals the joint + you can place cable markers inside prior to recovering the tubing.
|
|
ReMan
|
posted on 12/4/06 at 07:55 AM |
|
|
All these suggestions are fine for the application. You could also use these in-line heatshrink crimp joints.(Not very locost though)
I used all thes4 methods in different places on my loom, depending on space , movement etc
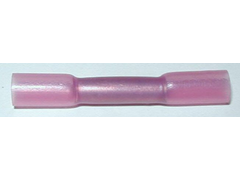 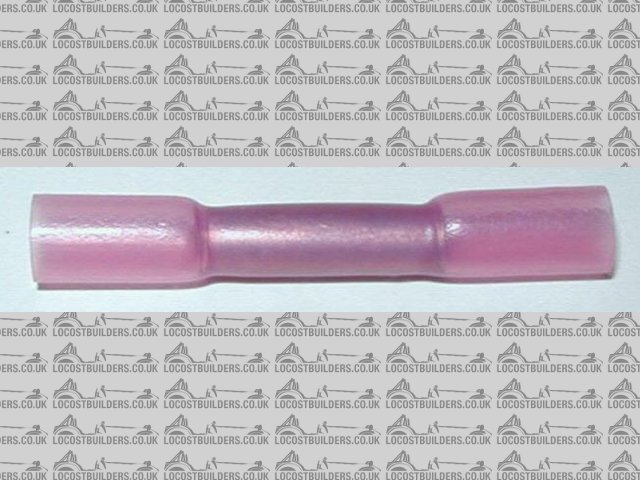 Rescued attachment rhs.jpg
www.plusnine.co.uk
|
|
RazMan
|
posted on 12/4/06 at 08:03 AM |
|
|
A couple of tips here:
If you want to use crimps, get a top quality crimp tool - the cheapies are very unreliable. A good one will cost £30 ish but well worth it.
If you solder, take the centre out of an insulated crimp butt connector and poke the wires in each end, solder and finish with heatshrink tubing. The
more wires you need to join, just use a larger butt connector (red, blue or yellow) This produces a good strong joint.
For grouped wires (ie. wiper motor, lights etc) use a multiway connector. This allows easy fault finding later.
[Edited on 12-4-06 by RazMan]
Cheers,
Raz
When thinking outside the box doesn't work any more, it's time to build a new box
|
|
02GF74
|
posted on 12/4/06 at 08:32 AM |
|
|
quote: Originally posted by Kissy
Try not to let solder capillary too far up the wires at it will render them likely to fracture in time. Use adhesive lined heatshrink if you can
(RS), it seals the joint + you can place cable markers inside prior to recovering the tubing.
has anyone know this to happen in a car? I thnk the time will be so long that you need not worry about it...
Strip the wires, about 6 mm, the push one lot of strands into the other lot, twist so the wires ahve good contact then a bit of flux and solder up.
Oh, an put some haeatshrink tubing before you solder 
|
|
nitram38
|
posted on 12/4/06 at 08:48 AM |
|
|
If you are joining an existing 'part' to the loom permenantly, then that is a very bad idea!
What if your indicator or lighting stalk goes on the fritz?
Out comes the soldering iron again.
Why not just find the same kind of comnnector as the donor uses and put that on your loom?
That way it will be a simple job to unplug it if your switches fail.
Soldering is a bit of a bodge in this situation!
|
|
Peteff
|
posted on 12/4/06 at 09:41 AM |
|
|
existing steering column plug with 3" wire on it.
I think he has that covered Martin.
yours, Pete
I went into the RSPCA office the other day. It was so small you could hardly swing a cat in there.
|
|
Hornet
|
posted on 12/4/06 at 09:53 AM |
|
|
I had same situation, removed the 3" wires from the original plug, removed the ends carefully, soldered them onto new wires and refitted them to
the original plug.
Hey presto.... no joins.
|
|
MikeRJ
|
posted on 12/4/06 at 10:25 AM |
|
|
quote: Originally posted by 02GF74
quote: Originally posted by Kissy
Try not to let solder capillary too far up the wires at it will render them likely to fracture in time.
has anyone know this to happen in a car?
I've seen it happen lots of times. Soldering can be problematic if the loom is subject to vibration or movement. All the stress from bending
happens at the point that the solder has flowed up to, so the wire can break very quickly.
Splicing into part of the loom under the dash is going to be fine, soldering a connector that plugs onto an engine sensor is asking for problems.
|
|
nick205
|
posted on 12/4/06 at 12:17 PM |
|
|
I prefer to fit proper crimped bullet terminals male/female to each wire and then connect. Crimps are far more reliable than soldered joints and
easier to service if need be in the future.
Crimp terminals are very cheap if you buy from somewhere like Vehicle Wiring Products and I have had perfectly good results with the budget
"plier" type crimping tools.
If you look at modern production car looms, there are very few if any soldered wire joints in them.
Just my 2p's worth 
|
|
MikeR
|
posted on 12/4/06 at 01:41 PM |
|
|
I've deliberately kept the old loom for my engine bay. Any connectors should be done feet away from the actual device. Also looking at making
the entire loom detatchable for future upgrades (like Fuel Injection).
|
|
nitram38
|
posted on 12/4/06 at 02:02 PM |
|
|
quote: Originally posted by Peteff
I think he has that covered Martin.
oops !
I mis-understood. Wrong end!
You can also use insulation tape if you have not got any heatshrink, but use a small tie wrap either end of the tape to stop it un-rolling with
time.
If you are using loom tape afterwards, do not bother with the ties
|
|
MikeR
|
posted on 12/4/06 at 05:43 PM |
|
|
Just to clarify, should i solder a crimp?
Always wondered this, sort of thought it would give a better connection so would be better.
|
|
darrens
|
posted on 12/4/06 at 06:27 PM |
|
|
quote: Originally posted by MikeR
Just to clarify, should i solder a crimp?
Always wondered this, sort of thought it would give a better connection so would be better.
If you solder after you crimp you weaken the join. Better to crimp only or solder only.
|
|
caber
|
posted on 12/4/06 at 10:09 PM |
|
|
The bottom line is if you can solder well a solder joint is the best method of permenantly joining two wires, if you can't use a crimp with
proper pliers of the ratchet type. You can also use screw terminal block. If you do use this tin the end of the wires first and make sure the terminal
is screwed down hard, this will stop the screws coming loose. It is possible to get two part terminal strip that plugs together this can be handy to
make multipole connections though I would tywrap the two parts together, I have done this in my Land Rover and it has worked a treat.
Caber 
|
|
C10CoryM
|
posted on 13/4/06 at 03:07 AM |
|
|
This topic always brings a debate no matter who you ask.
A couple companies issued TSBs saying do not solder splices on vehicles. As has been stated, the solder can cause wires to break in areas under
vibration/flex (everywhere on a car). GM went so far as to produce a heatshink/connector similar to the one pictured above. With todays vehicles
wire breaks can cost a LOT of hours in diagnoses. Engineers avoid splices as much as possible now for this reason. They are also more labour
intensive than a machine splice.
Anyhow, at our shop we crimp and heatshrink using good crimpers and good heatshrink. If you do wiring, buy good crimpers. Not only do they work
better, they are easier on the hands. The good heatshrink will shrink smaller/tighter and has a glue in it to prevent any water intrusion. Even if
you chose to solder, use good heatshrink. Even I buy the good stuff and Im pretty cheap .
Cheers.
"Our watchword evermore shall be: The Maple Leaf Forever!"
|
|
MikeR
|
posted on 13/4/06 at 05:15 PM |
|
|
thanks for all the advice folks.
Still don't understand why if i crimp i shouldn't solder the wires afterwards but i'll take the advice
Think i'll be crimping. So where is the cheapest place to buy a decent crimp as i've got three pairs of the cheap ones.
|
|
RazMan
|
posted on 13/4/06 at 07:43 PM |
|
|
Polevolt page 42 Part Number TT73
Cheers,
Raz
When thinking outside the box doesn't work any more, it's time to build a new box
|
|