blakep82
|
posted on 9/7/14 at 02:43 PM |
|
|
wiring the dash board
the wiring continues...
I'm hoping to try and get my dash board put together later, but wondering, whats the best way to connect groups of wires together (remember IVA
too) say for example gauge illumination, 3 seperate lights, in parallel, all connecting to one source.
choc block connectors? are they allowed? frowned upon? I don't really like them, but if they work...
anyone got any pics of the wiring on the backs of your dash boards?
I'm planning on having multi plugs to connect it all to the car, so everything goes to a multiplugs, then onwards to whatever
________________________
IVA manual link http://www.businesslink.gov.uk/bdotg/action/detail?type=RESOURCES&itemId=1081997083
don't write OT on a new thread title, you're creating the topic, everything you write is very much ON topic!
|
|
|
coozer
|
posted on 9/7/14 at 02:57 PM |
|
|
Up to you really, but I would say master live, master earth then you'll need the control wires for each gauge depending on the polarity and a
feed from the side lights for illumination. You are going to end up with quite a few. I soldered the joints and used heatshrink, then 2 x 12 way
connectors to join into the main loom.
Stick on cable ties to keep it tidy.
1972 V8 Jago
1980 Z750
|
|
Smoking Frog
|
posted on 9/7/14 at 04:41 PM |
|
|
Here's a pic of mine with the scuttle off. I'm sure there are better examples. Also have not passed the IVA yet.
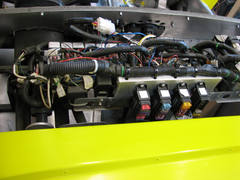 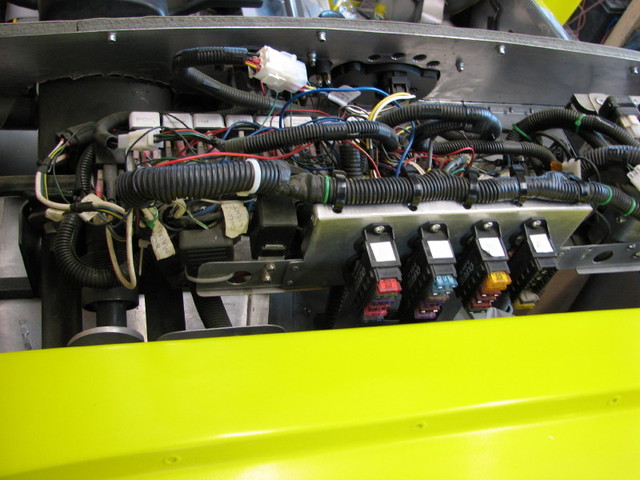 Dash Wiring
Try to make access as easy as possible. Daisy chain the +/- connections using two single wires and soldered joints. If it's just illumination
you don't need thick wires. Only use connectors that can be found on cars, no choc blocks. Wrap in split tubing where possible. And hope it
don't turn out like spaghetti.
|
|
FuryRebuild
|
posted on 10/7/14 at 07:18 AM |
|
|
+1
I worked out which was common to things like gauge lights, and soldered up a specific set of wires to eachother at the correct length to just run to
each guage. Similarly the signal wires weren't on this kind of bus arrangement, but were all specifically made to length. As a result, there was
the bare minimum of wires to each gauge, and I could trace it back to a specific fuse or relay. I also moved the fuses and relays out from behind the
dash and into the engine bay where they could be got to much more easily. In a race car, this lot sits on the dash and next time, I'll move to
solid state breakers.
Shrink-wrap is the only way to go, and don't forget that wiring tape is different from electricians tape. I used neither, but had all mine in
trunking (like the photo further down this thread). When I went through SVA, my inspector called his boss over and I thought "oh dear",
but he said to his boss: "you see, this is how you're meant to do it". All the trunking was p-clipped to the chassis at 300mm
intervals.
In my fantasy manufacturing head, I was going to see if I could make a little module that went onto the back of a gauge to make it addressable down a
serial bus. Then all you'd need to do is connect each gauge to a ribbon cable and a simple control box (microcontrollers all the way) and wiring
the dash takes minutes. Wiring is down, weight is down, complexity is down. It's not far away from canbus addressable dashpods in prod cars, but
with the creative flair we like to bring to our projects.
On another note, I found that the harsher environment of competition meant that electrical gauges used to fail, so I ended up migrating to VDO
mechanical ones where I could. Everyone's mileage varies.
quote: Originally posted by coozer
Up to you really, but I would say master live, master earth then you'll need the control wires for each gauge depending on the polarity and a
feed from the side lights for illumination. You are going to end up with quite a few. I soldered the joints and used heatshrink, then 2 x 12 way
connectors to join into the main loom.
Stick on cable ties to keep it tidy.
When all you have is a hammer, everything around you is a nail.
www.furyrebuild.co.uk
|
|
Irony
|
posted on 10/7/14 at 07:37 AM |
|
|
If I was doing this again I would approach it in a totally different method. Car Builder Solutions now do what they call military grade multi pin
adapters. These adapters go up to something like 48 pins. I would have three bus bars attached to the back of the dash. One for permanent live,
ignition live and one for earth. I'd then wire the dash to be removable by disconnecting just four cables.
|
|
FuryRebuild
|
posted on 10/7/14 at 07:40 AM |
|
|
I forgot to mention that - my dash now comes out on 3 connectors, and yes, if I did it again, I'd upspec the connectors to the millitary spec.
Saying that, I haven't had a connector failure (ford). Definitely stay away from standard bullet connectors.
quote: Originally posted by Irony
If I was doing this again I would approach it in a totally different method. Car Builder Solutions now do what they call military grade multi pin
adapters. These adapters go up to something like 48 pins. I would have three bus bars attached to the back of the dash. One for permanent live,
ignition live and one for earth. I'd then wire the dash to be removable by disconnecting just four cables.
When all you have is a hammer, everything around you is a nail.
www.furyrebuild.co.uk
|
|
Irony
|
posted on 10/7/14 at 09:41 AM |
|
|
quote: Originally posted by FuryRebuild
I forgot to mention that - my dash now comes out on 3 connectors, and yes, if I did it again, I'd upspec the connectors to the millitary spec.
Saying that, I haven't had a connector failure (ford). Definitely stay away from standard bullet connectors.
hmmm my car is riddled with bullet connectors. I have used proper crimpers and I have only had one problem with a bad connection so far. Then again
its not on the road yet. I am really quite unsatisfied with my wiring to be honest. Once the car is one the road my next winter project may well be
a complete rewire. It is my first ever time doing something like wiring a car and I believe it's safe - just a bit untidy behind the dash.
|
|
FuryRebuild
|
posted on 10/7/14 at 09:44 AM |
|
|
Don't beat yourself up - I went through quite a bit of learning as well. I paid for my first installation, and it was a tangled unfathomable
thing, and the dash wasn't demountable. I spent a few evenings changing it slowly and carefully, testing each connector as I went.
I'm looking for a good supplier of high-end lightweight wire and connectors, heat-shrink boots, etc.
quote: Originally posted by Irony
quote: Originally posted by FuryRebuild
I forgot to mention that - my dash now comes out on 3 connectors, and yes, if I did it again, I'd upspec the connectors to the millitary spec.
Saying that, I haven't had a connector failure (ford). Definitely stay away from standard bullet connectors.
hmmm my car is riddled with bullet connectors. I have used proper crimpers and I have only had one problem with a bad connection so far. Then again
its not on the road yet. I am really quite unsatisfied with my wiring to be honest. Once the car is one the road my next winter project may well be
a complete rewire. It is my first ever time doing something like wiring a car and I believe it's safe - just a bit untidy behind the dash.
When all you have is a hammer, everything around you is a nail.
www.furyrebuild.co.uk
|
|
blakep82
|
posted on 11/7/14 at 02:09 PM |
|
|
Some good idea there! Thank you
Will be looking for a bus bar type thing now. I've seen them on polevolt, so next time I order from them, I'll get one for -ve and an
insulated one for +ve.
________________________
IVA manual link http://www.businesslink.gov.uk/bdotg/action/detail?type=RESOURCES&itemId=1081997083
don't write OT on a new thread title, you're creating the topic, everything you write is very much ON topic!
|
|
adithorp
|
posted on 11/7/14 at 03:22 PM |
|
|
There is an argument that soldered connections can break/fracture. I think the jury is out on the truth of this but I don't use them because
I'm crap at soldering.
I try and use crimp terminals, but glue-lined/heat-shrink ones, rather than the standard (crappy) crimp connectors. The combination of glue and
heat-shrink gives a good, reliable and mostly waterproof joint.
"A witty saying proves nothing" Voltaire
http://jpsc.org.uk/forum/
|
|
FuryRebuild
|
posted on 11/7/14 at 03:30 PM |
|
|
All the videos I've seen on mil-spec don't solder - they crimp to just the right pressure only.
My soldering's good, but that's because (many years ago) I did an A-level electronics. Still, I'd crimp only this time.
quote: Originally posted by adithorp
There is an argument that soldered connections can break/fracture. I think the jury is out on the truth of this but I don't use them because
I'm crap at soldering.
I try and use crimp terminals, but glue-lined/heat-shrink ones, rather than the standard (crappy) crimp connectors. The combination of glue and
heat-shrink gives a good, reliable and mostly waterproof joint.
When all you have is a hammer, everything around you is a nail.
www.furyrebuild.co.uk
|
|