Theshed
|
posted on 9/5/13 at 06:14 PM |
|
|
Been playing and now have electrical questions
I need to make a great big under-tray out of Kevlar and since I know naff all about composites I thought I would try out vacuum bagging on something
smaller...many efforts later I now have a dashboard - well almost. Nearly finished - needs bonding in and a coat of clearcoat -I know the weave is
distorted in places but I will hide it with switches! It does make a difference to the BrrmmBrmm noises
So why the electrical section? I am starting to do some wiring. I want to make a high spec loom i.e. Circuit breakers/ Raychem shrinking/epoxy sealing
and those silly expensive mil spec connectors. I have found lots of info on most things but nothing about relays...
Questions
Does anybody know what relays (if any) are used in motorsport?
Would you fit a circuit breaker to the low current side of a relay or just the high side?
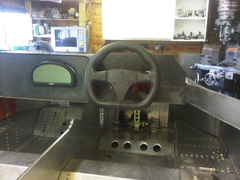 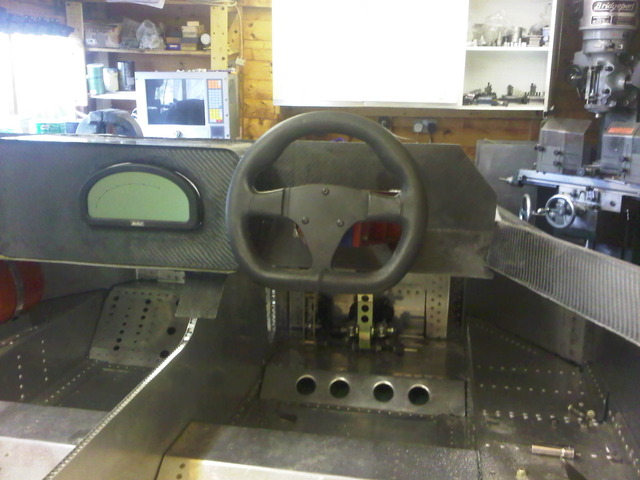 Description
|
|
|
daniel mason
|
posted on 10/5/13 at 05:18 AM |
|
|
take a look at sbd website. they do military spec looms and use very good components. they do recommend cable tying the relays to parts of the harness
to avoid vibration
|
|
Theshed
|
posted on 10/5/13 at 07:32 AM |
|
|
Many thanks - some good stuff there. It was the effect of vibration that was concerning me. I had wondered whether solid state relays were better.
That said at least I can afford the usual 4 pin square jobbies!
|
|
snowy2
|
posted on 10/5/13 at 07:35 AM |
|
|
whilst i admire the desire for the best its really overkill and it wont necessarily improve reliability. your more likely to have problems with the
connections at the far end of the wires next to the consumers (lights etc.). And just how much do you plan to use the car after the 3rd world war has
started? i can see why the old bill might want that sort of capability or even the military but on a little used kit car?
the fact is that adding all the circuit breakers and relays just add additional potential sites for problems as every connection needs to be of a very
high quality to gain any benefit, if your hoping to just crimp the terminals on the wires and forget them your wasting your time on the extra expense,
they need to be absolutely right every time their made.
If your doing it for the bragging rights crack on and knock your self out......you do know that gold plating kits are available and they improve the
look and reliability of terminals, its also very expensive but hey you want the best.
my own cars loom is very simple and 100% reliable what else could you ask for?
sometimes you are the pigeon, most of the time the statue.
|
|
MikeRJ
|
posted on 10/5/13 at 09:06 AM |
|
|
quote: Originally posted by Theshed
Many thanks - some good stuff there. It was the effect of vibration that was concerning me. I had wondered whether solid state relays were better.
That said at least I can afford the usual 4 pin square jobbies!
I personally wouldn't bother unless you have a specific need for an SSR, e.g. you want to drive a load with a PWM signal.
|
|
Matt @ TDF
|
posted on 11/5/13 at 10:59 PM |
|
|
Military spec gets banded about all the time with regards wiring looms and actually "Mil-Spec" is way, way behind what we are doing in
motorsport these days.
For a start no modern pro race car will be built using circuit breakers or relays anymore. It's all solid state power distribution from the
likes of Motec with their PDM range and Pi/Pectel/Cosworth with their IPS range. OBR also do a nice SSPD setup. This totally does away with any
fuse/relay/breaker combo and as such massively simplifies the wiring loom. With CAN switch panels etc. it's now possible to have a whole host of
switchgear that exits the dash panel as two wires. The ideal is to only put power where it is absolutely required, so no more running it halfway up
the car and back just to get to a switch/relay.
In the early to late 90's various types of relay and breaker were employed but for the most part any one worth their salt used Amphenol 12883
spec sockets with a matching relay to their requirements. These are bolt in and weather sealed although you really have to watch the inrush currents
on these as their peak rating is quite low compared to their constant. Circuit breakers were nearly always ETA 4120 type in banks. To be honest even
in those days we rarely used relays and generally did the whole lot on breakers as this could quite often be lighter than also wiring the low sides
etc. to relays. Race cars are usually pretty much on or off
Mid 2000's we moved to solid state relays for some things but would strip commercial stuff or build our own from components and pot them into
billet enclosures to meet spec.
Motorsport looms are generally constructed to Raychem System 25 standards using Type 55 or Type 44 wire. Glued transitions are standard. Deutsche
ASM's are the "standard" connector although some AS range is still used as required or for higher current stuff.
To tool up to build a system 25 spec loom you will spend over £2K in tooling alone! It really is way, way cheaper to pay someone that does it for a
living to construct a harness to this sort of spec, especially when you consider some connectors are over £200 each and as such you really don't
want to cock one up
FWIW a Motec PDM15 is less than a grand and for a 7 type car has all the capacity you'll ever need. It makes a lot of sense to go down this
route rather than spending 600 quid on breakers, 200 quid on sundries etc. etc. The real cost increase over old style stuff is only a couple of
hundred quid.
It's also worth considering that most decent level race cars aren't running looms full of AS connectors etc. Usually we'll use these
for connection to main controllers etc. and the rest will be DT/DTM as appropriate which whilst way more bulky are robust and dependable connectors
(you'll still need a very expensive crimp tool though) with Trident or Neptunes for bulkhead connectivity.
|
|
Matt @ TDF
|
posted on 11/5/13 at 11:02 PM |
|
|
Oh and for the stuff all us motorsport electronics guys are getting way excited about at the moment check out WIC (Wire In Composite) from Beru F1 and
similar. Now that is proper stuff - why run radio loom and HUD in a cable assembly when it can just be laid into the seat.....
|
|
Theshed
|
posted on 13/5/13 at 10:41 AM |
|
|
Sorry I have failed to follow my own post! Thanks for all the input. I have not considered a CAN bus style system. I will have a look but I think that
would be a little out of my league.
"Bragging rights..." not really. My car is not a "kit car" it is a folly of the highest order. It could not be used on the
road and so lights are not the biggest issue. It is a LMP car in style with the mechanicals of a 2002 Le Mans entry. It has a 750bhp engine and an
Xtrac transmission. Against that background frankly a little gold plating would be nothing. I want a very good system not necessarily the best but
certainly as reliable as possible.
Throughout the whole project I have tried to acquire the tooling I needed. I then (try) to learn to use it well. There have been many many cock ups
but some successes as well. I have collected a set of DMC crimp tools by waiting and watching on e-bay for a few hundred pounds. I know that a
professional would do a better job but that is true of all the other bits of the car and for me - not the point. I am not completely useless - I did
make my own CNC control system - but I am far less confident around electronics than say a machine tool.
Matt - many thanks - I will have a look at the relays you suggested - I could always change to a CAN system if I do not manage to crash at the first
corner!
|
|