tks
|
posted on 14/10/05 at 01:26 PM |
|
|
mhhh
its sow hard to say!
don't we have some one over here who owns an..
torq wrench?
what if we make an bit to fit the shaft
and with our torque wrench we search for the value that you cant switch??
another one would be simply with an spring unster (an device with an linear spring) sow you can measure how much Newton is neccecary to operate an
gearbox.
i have to omit that my calcs maybe out of question due to the fact that i'm certanly not pulling with 90degrees at the lever..
sow then there is much more force needed to operate the thing.
what the minimum value of an torque wrench?
Tks
The above comments are always meant to be from the above persons perspective.
|
|
|
tks
|
posted on 14/10/05 at 01:31 PM |
|
|
mhh
ok, i think that we can buy them.
Then we will instead of hook it up directly make use of an transmission...
(we search for 2 teethed wheels and an belt, in that way we can also hide the motor perhaps better from debris etc.)
Do you but them or will i?
Tks
p.s. if they aren't of any use, i will find another project where i can use them...
The above comments are always meant to be from the above persons perspective.
|
|
Bob C
|
posted on 14/10/05 at 03:51 PM |
|
|
It's easy & cheap to make a positional feedback servo using a quad op-amp for control & an audio stereo amp chip to do the power - if
anyone's interested I'll dig the old circuit out (did it for controlling a waveguide attenuator on a sat. comms project - worked a
treat)
Cheers
Bob
|
|
tks
|
posted on 14/10/05 at 07:49 PM |
|
|
mhh....
We will first need to know that including transmission the force will be enough..
Than we know wich electronics we need (watts) then we can make an choice how to do it.....
think we need the middle one..
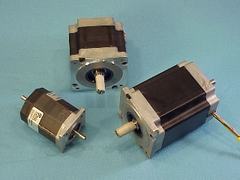 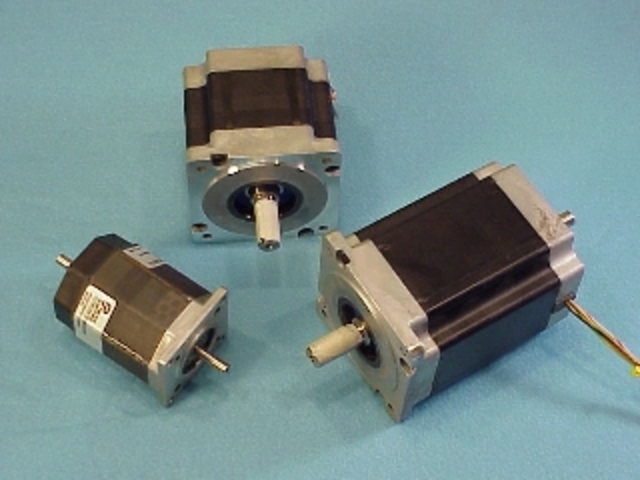 Rescued attachment Stepper.jpg
The above comments are always meant to be from the above persons perspective.
|
|
tks
|
posted on 17/10/05 at 12:26 PM |
|
|
how are the things..
is there any new news?
Solenoids?
Stepper motors?
Think i will do the test and buy one..
Cheers.
Tks
The above comments are always meant to be from the above persons perspective.
|
|
MikeRJ
|
posted on 18/10/05 at 04:33 PM |
|
|
I can't think of a less suitable actuator than a stepper motor for this application. Affordable steppers are for low/medium torque applications
that requires very precise positioning. They are difficult to drive above a certain speed, have low holding torque and no positional feedback as
standard (so if it skips a few steps we won't know).
For gear changes we need fast, meduim-high torque movement. Precision of movement is of secondary importance. A powerfull servo motor would be good,
but expensive. A cheap, servicable DIY solution is simply a geared motor (e.g. a windscreen wiper motor is very suitable) and limit switches.
A friend of mine built a twin engined Metro turbo, and gearchange on the rear engine was achived only through the above method, controlled by
microswitches on the gearlever mechanism. It did require a lot of setting up, but when it worked it changed gears very quickly and smoothly.
|
|
ceebmoj
|
posted on 18/10/05 at 09:56 PM |
|
|
hi,
it is also worth remembering that DC single winding motors will have a difrent torque avaloble at start up depending on the position of the coil
having said that a windscrean wiper motor as sigested would be good and rather than limit switches you could very easely add a rotary encoder to the
motors shaft witch would give you a good degree of controle.
it might be easer for a hobby builder however to build a system that uses a ac motor and and a H brige to get the same control you could sence the
speed and recolotions from the coils that way as well rather rhan using a rotary encoder.
|
|
davidwag
|
posted on 20/10/05 at 07:20 PM |
|
|
Hi,
Found a picture of LUK ASG gearchange actuator.
Look familiar??  
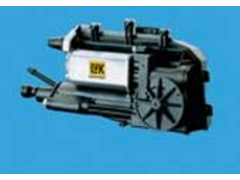 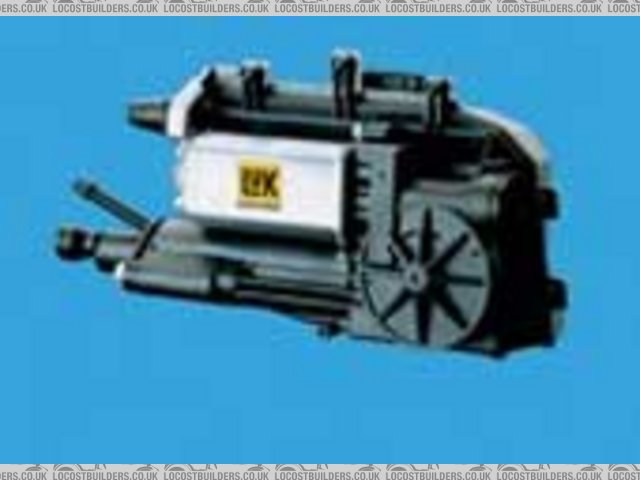 Rescued attachment asg.jpg
|
|
tks
|
posted on 20/10/05 at 07:24 PM |
|
|
pwww
for what kind of gearbox is that one??
looks for me like an truck example?
pff...
think we need to build an servo with a wiper motor/window motor scooter starter motor.
And add an rpm counter on it..
TKs
The above comments are always meant to be from the above persons perspective.
|
|
Rorty
|
posted on 20/10/05 at 09:28 PM |
|
|
What do mhhh, mhh, pwww mean? Are these some electronic acronyms I should be aware of?
Cheers, Rorty.
"Faster than a speeding Pullet".
PLEASE DON'T U2U ME IF YOU WANT A QUICK RESPONSE. TRY EMAILING ME INSTEAD!
|
|
ceebmoj
|
posted on 25/10/05 at 07:57 AM |
|
|
Hi a quick Google and look in other web forums admittedly games ones where there are a lot of 1337 (see http://en.wikipedia.org/wiki/Leet) 0wning
hacks seams to show that they are in reasonable use with here history being traceable to the Simsons or another animated series. So look out Oxford
dictionary hear we come.
There have be discussions in hear before about spelling, grammar and English in general. Witch have left me reasonably offended in the past. So how
about if you can read a post and understand the general idea or concept the author is trying to express post your reply to that question / idea and
steer away from what could be seen as offensive to others.
[Edited on 25/10/05 by ceebmoj]
|
|
tks
|
posted on 25/10/05 at 12:07 PM |
|
|
Sure
what does rorty mean? funny guy??
Tks
The above comments are always meant to be from the above persons perspective.
|
|
tks
|
posted on 27/10/05 at 07:43 PM |
|
|
ok
Well this is the old working situ.
What has happend is that the voltage regs wich gave the power to the servo where dead!
And the other one is almost dead.
i putted 2 in parrallell for more amps.
Think i will make an powersupply
In that way i can deliver to every board.
an nice non spikey 5volt or 12volt.
Or 6volts in case of the servo's.
Regards,
Tks
[Edited on 27/10/05 by tks]
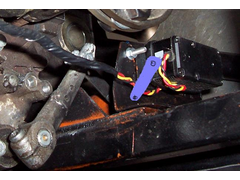 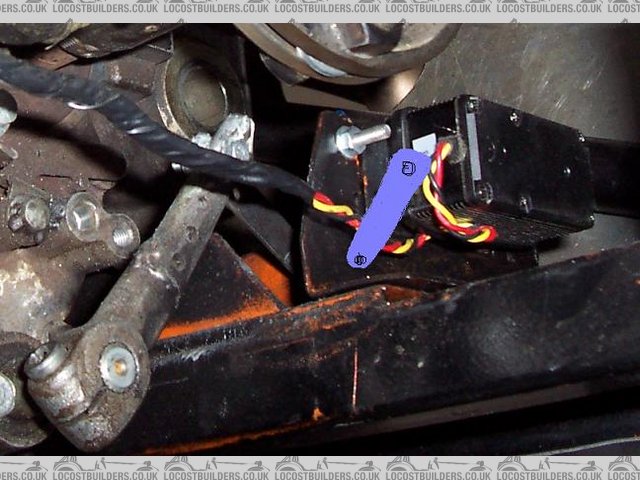 Rescued attachment ServoSitu.JPG
The above comments are always meant to be from the above persons perspective.
|
|
stu da rude
|
posted on 29/10/05 at 12:01 AM |
|
|
This thought had crossed my mind before too, a guy built one with two starter solenoids which didnt work; couldnt get them to engage/disengage with
any precision.
its here:
http://biketransplant.tripod.com
under electronic gizmos tab.
|
|
Bob C
|
posted on 29/10/05 at 06:17 PM |
|
|
The problem, I think, is that a solenoid can be programmed by an ecu & power amp. to give a specified 'impulse' to the gear lever, but
this is never going to overcome the fact that the impulse required varies with temperature, wear, speed, which gear it is (1st or 6th) and whether the
dogs are nicely lined up or not! I'd be interested to see how folk get on with servos - that could be the answer!
When you change gear with your foot you 'feel' it engaging, you don't just give the lever a kick!
cheers
Bob
|
|
tks
|
posted on 1/11/05 at 08:15 PM |
|
|
Bob
should foot be hand?
or what do you feel??
Clutch?
Tks
The above comments are always meant to be from the above persons perspective.
|
|
Bob C
|
posted on 2/11/05 at 12:05 AM |
|
|
On the bike it's your left foot - in a BEC it would be hand yes! I'm just saying, change gear manually & you have feedback (tactile),
a solenoid, even micro controlled, is just giving the lever an impulse - the gear may slip in or it may baulk, it must be very difficult to make it
reliable. At least a servo will do its damnedest to reach the detent position & this may be a crucial advantage. Or it may not!!!!
I'm vaugely hoping someone will do all the donkey work for us all & find out the hard way!
cheers
Bob
|
|
tks
|
posted on 2/11/05 at 01:00 PM |
|
|
well
the only thing i noticed is that when selecting first gear...
it makes an hard noise like Bangg!!
but i think its just the propshaft movement wich turns an quarter and then gives an bang in the box.
When it works i will make an video...with the noise..
This saying, my engine is now very quiet and when i tested the system it was louder... sow dunno how the system is now....
i'm sure that when the prop is fixed..(i mean the teeth in the diff are touching each other) the bang should be gone...
We will see, the failure of the system is due a power suply problem.
when i have time i will fix it.
Tks
maybe its the clutch touching when the oil is cold??
any way it sound like when you hit an bell
[Edited on 2/11/05 by tks]
The above comments are always meant to be from the above persons perspective.
|
|
madman280
|
posted on 24/11/05 at 02:54 AM |
|
|
http://www.mcmaster.com/ page 909 Sealed Linear Solenoids
|
|
tks
|
posted on 24/11/05 at 01:14 PM |
|
|
mhh
They do like indeed very much on the Kliktronic system....
But we have to say that it only likes 1inch travel.
And i think we need 1 inch up and 1 inch down.
it will depend also on the lenght of the gear lever offcourse...
also we need an certain amount of power!
Servo:
Don't know if i mentioed earlyer but my servo wasn't burnt! what whas gone where the 2 voltage regulators...
I have now hooked up 3 of them...
(3x1,5amp) with big cooling surface..
Now my system is again full operational....
Tks
will make a movi of it when i can sow we can judge the bling when it enters first gear....
The above comments are always meant to be from the above persons perspective.
|
|
tks
|
posted on 24/11/05 at 01:35 PM |
|
|
Bob (tactile)
Bob,
the tactile is very difficult to get,
The hardest point is getting the arm lengts just right saying you use every movement of the servo going from First gear to second... its the hardest
part of the making of the system.
Also my micro knows in wich gear it is.
For the safety and automatic calibration,
i builded an reset in, i connected the Neutral switch to the board.
Sow the micro knows when its in Neutral.
and resets his counter to 0.
Then when it fails to engage first gear.. he knows he is in 0 again. (it resets the counter it self).
When you move from first to second and it fails you are in Neutral then again he knows he failed....
Once in 2 nothing can go wrong.
2 and up never have failed during testing etc.! (i haven't driven in all the gears) but tested only up to 2nd.
the rest of the gears i tested with the wheels from the ground/ only with diff connected (no wheels)
the most difficult is to select first, because it needs the most force of all..and then you have the problem to go to 2nd because it requires the most
of travel of all... (you feel the chit? most power/most travel...)
i have had situations that i needed more force for First but could engage 2nd.
you can see on the pic that i'm pulling on an angle..its deff against me.
Sow for the rest of the community wich have an better situation they shouldn't care..
The board also has an Relais sow when you push clutch sow you can start while in gear etc.
(i didn't wanted to mess with the loom)
Regards,
Tks
I am uploading an Quicktime movi to an free server sow you all can see how i made the system. Please turn the sound of (its me who speaks) its in
dutch (i don't like to hear it).
Will post the link as soon as the 57MB file is there...
LINK TO FILE
[Edited on 28/11/05 by tks]
The above comments are always meant to be from the above persons perspective.
|
|