want2race
|
posted on 30/1/07 at 05:10 AM |
|
|
Bonnet shaping and bending advice?
Firstly how did everyone cut it ? Does anyone know the starting dimensions needed?
and secondly, how did you bend it? I just ordered a piece of .060" ALi today and it was $60 so I would rather not stuff it up if possible
Thanks
~J
|
|
|
Humbug
|
posted on 30/1/07 at 07:23 AM |
|
|
Do a search on here, e.g.
http://www.locostbuilders.co.uk/viewthread.php?tid=57208&page=1
http://www.locostbuilders.co.uk/viewthread.php?tid=45423
http://www.locostbuilders.co.uk/viewthread.php?tid=13185
http://www.locostbuilders.co.uk/viewthread.php?tid=12355
just for instance!
|
|
Surrey Dave
|
posted on 30/1/07 at 08:24 AM |
|
|
bending!
My first bonnet was bent around my BOC Argoshield cylinder.
The bonnet I made last year was bent around a wooden telegraph pole as I no longer have a BOC cylinder.
|
|
David Jenkins
|
posted on 30/1/07 at 08:36 AM |
|
|
I glued together some cardboard sheets (art shop stuff) to make a template. Fitted the scuttle and nose cone, then taped the card over and marked it
out. I cut out a large hole for the downdraft carb, then glued on more card around the hole until it fitted the air filter properly. Took it off,
made allowances for bends and folds, then taped it onto the ali sheet and marked out.
I made the 90-degree bends along the side using a sheet metal bender at my friend's business (a very large machine!). The curves were bent
around a gas cylinder.
I didn't try to fold the front and rear edges - life's too short - I simply glued edging on.
You can click on the 'WWW' button below to see how it turned out...
cheers,
David
[Edited on 30/1/07 by David Jenkins]
|
|
JAG
|
posted on 30/1/07 at 08:37 AM |
|
|
Mine was bent around my knee
.........very very carefully.
I had planned on using a local telephone/telegraph pole but found it much easier with my knee. The best bit is you don't do all of the bend in
one go hence you can adjust the line of it as you work along the length of the bonnet.
Pictures in my archive will show how it worked out
Justin
Who is this super hero? Sarge? ...No.
Rosemary, the telephone operator? ...No.
Penry, the mild-mannered janitor? ...Could be!
|
|
scutter
|
posted on 30/1/07 at 08:40 AM |
|
|
I used a piece of floor vinyl for the template, it droops when heated and the forms the curves when cold.
ATB Dan.
The less I worked, the more i liked it.
|
|
steve m
|
posted on 30/1/07 at 08:50 AM |
|
|
Mine was bent on the car with the scuttle, and nose cone supported with so as to avoid distortion, my Dad lay on the bonnet, while i went each side
and vary carfully bent the 2 "wings" downwards, by using a piece of wood to spread the load, I had taken the carb off, ass the hole can be
left till last,
i only managed to crease one bit, and over the years, this crease has been mostly polished out
this bending process only took a couple of hours
|
|
mark chandler
|
posted on 30/1/07 at 10:19 AM |
|
|
Bit of old 2" plastic drain pipe for me !
I measured the middle of the curve from scuttle to nosecone and marked on the ali sheet (oversize) then bent around the pipe.
Next was to lay it on the bodywork and mark out the cut for the scuttle & nosecone, I cut the scuttle edge first then the nose cone so I had a
snug fit.
Next was to strap the bonnet down tightly and mark out the body line bends, the using some box tube and clamps align with my line and bend over (I
used a lump of 2"x 2" wood as a hammer to not mark anything), then just trimmed.
Louves are stamped in, I knocked a tool up out of scrap to do this. its the lump of metal on the scuttle.
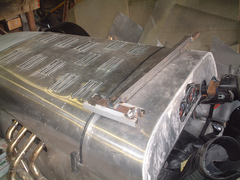 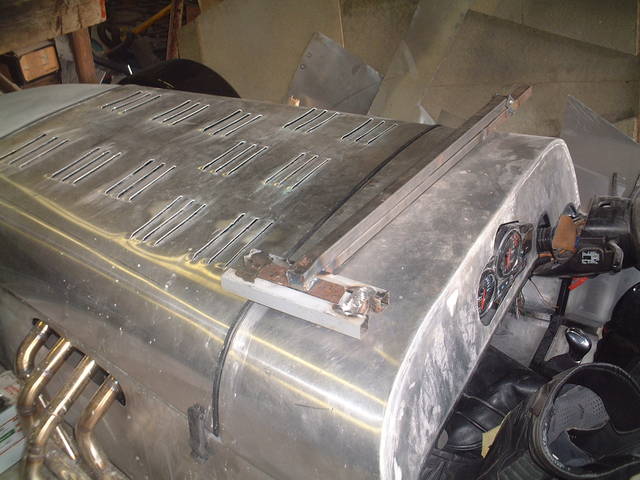 Rescued attachment louves stamper.JPG
|
|
James
|
posted on 30/1/07 at 11:39 AM |
|
|
Plotter paper template.
With 1" returns bent on the edges.
Drew the bend lines on the ali (peel- off vinyl covering) then bent it around a long length of 2nd hand (yuck!) 4" waste pipe clamped in the
workmate.
HTH,
James
------------------------------------------------------------------------------------------------------------
"The fight is won or lost far away from witnesses, behind the lines, in the gym and out there on the road, long before I dance under those lights."
- Muhammad Ali
|
|
907
|
posted on 30/1/07 at 05:19 PM |
|
|
Hi.
When bending metal there's always a certain amount of spring back, so it needs to be bent
round something smaller than the finished rad required.
It also needs to be bent more than 90 deg.
You need also to get the middle of the bend right as the ends will follow. It's easy to "unbend"
but it's harder to get more bend in, if you follow, but don't over do it.
So when you over bend, you can then gently pull the edge of the sheet back, till the radius and angle
comes right, again get the middle right first and the ends will follow.
Practice with a piece of scrap. A foot square or so.
Depending on the hardness of the material you will get a different amount of spring back.
I started with a sheet that was too big and trimmed it to size after bending.
Not sure if you can get hold of a cardboard carpet tube like I did. I think it's a case of use what you can.
Hth
Paul G
|
|