Alan B
|
posted on 5/7/07 at 04:49 PM |
|
|
Using the lathe for tube notching
Not rocket science, nor probably even original, but worth sharing.....was easy to do, fairly cheap and worked well. Should be self explanatory. I do
use a holesaw and notching fixture for most of these, but this was beyond it's range (20 degrees)
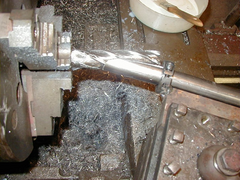 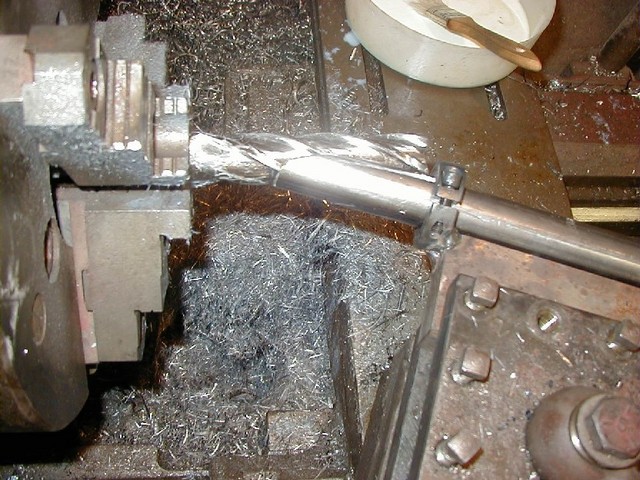 Tube mill
[img][/img]
|
|
|
nitram38
|
posted on 5/7/07 at 04:56 PM |
|
|
Alan, always nice work!
|
|
John Bonnett
|
posted on 5/7/07 at 05:11 PM |
|
|
Alan, a great technique. Any angle can be cut exactly and not only does it look good the frame must be stronger and of course, welding is then a
doddle.
John
|
|
Alan B
|
posted on 5/7/07 at 05:21 PM |
|
|
Nitram..Cheers
John....Thanks, yeah the topslide already being marked in degrees makes accuracy a doddle...
|
|
Maradona
|
posted on 1/8/07 at 02:27 PM |
|
|
great excelent technique !!
Thanks for shearing with us
Cheers
maradona
|
|
Syd Bridge
|
posted on 1/8/07 at 03:24 PM |
|
|
The exact same way I've been doing it for far too long to remember, and my grandad did and taught me.
I use a fixture in the adjustable toolpost, to get the height exactly spot on.
Also, I use an 'end and side' cutter'. Bring the workpiece in so that the end cuts, not the long flutes. It doesn't make those
needles so readily. Lots of cutting fluid as well.
Watch out for those little needles when you clear the swarf, they give a nasty bite!
Chyeers,
Syd. 
|
|
NS Dev
|
posted on 3/8/07 at 02:04 PM |
|
|
Yep, same here, except I lent my jig to somebody and never got it back so the last wishbones I did were done with a carbide burr in the die grinder
instead.
I, as syd said, also use a slot drill (end and side) rather than end mill (side cut) and drive the toolpost towards the chuck rather than across
it.
Does the same job though, very nice indeed
Retro RWD is the way forward...........automotive fabrication, car restoration, sheetmetal work, engine conversion
retro car restoration and tuning
|
|