NS Dev
|
posted on 12/5/07 at 10:18 AM |
|
|
Tig welding ally
Right, had a go at running some beads on ally again last night, as I am imminent need of making 2 dry sump tanks, a rad header and a fuel tank!
I am really strugging, (despite, for those unfamiliar with me, being able to make lovely welds on stainless and mild steel) but after about 20 minutes
I managed to feel that i was exercising at least some control over what was going on!
To the ally experts on here, does this sound about right................
1) I have to hold a very short arc length, and torch nearly vertical, or I just blow the end of the rod away unless i pull it out of the gas shroud
(in which case I get soot on the next dip)
2) I have to use a surprisingly low current, and wait for the pool, so that when I get the pool it stays clean. I can get and hold a pool at much
higher current but then it doesn't clean up before I have to dip and move on
3) The electrode doesn't ball up like all the books say, it seems to stay pointed. I'm using grey (ceriated?) electrodes which my welding
man reckons are do it all electrodes, and will do the job of white and red ones. I tried a white one and it was just the same.
4) what gas flow should I be using, at the mo I am using "18" but i'm not sure if its cfh or lpm
Retro RWD is the way forward...........automotive fabrication, car restoration, sheetmetal work, engine conversion
retro car restoration and tuning
|
|
|
Moorron
|
posted on 12/5/07 at 11:24 AM |
|
|
i dont have my own tig set yet, but the ones i use at work are mostly the same.
it sounds like your not setting up your tungsten corrently, if u cant get it to ball up then you will never be able to weld the alloy.
To get your tungsten to ball up set the 'balance' on the tig set to 0. as you do for welding stainless, but using the AC setting for
alloy. turn up the amps and weld for a few seconds, it should ball up the tungsten, too much amps or to long on the trigger and your tungsten will
burn away. But if it manages to ball up the tungsten then its working.
After you do this (after every touch down too) check the gas jets arnt blocked up as bits of the tungsten can block them up.
Remeber to turn the balance back up to 6 (or 60) to start welding the alloy.
a pic of your set might help me to id which knob is controlling the balance as i only use the shop floor water cooled ones at work.
[Edited on 12/5/07 by Moorron]
Sorry about my spelling, im an engineer and only work in numbers.
|
|
MikeR
|
posted on 12/5/07 at 02:45 PM |
|
|
Seem to recall the welding bloke at my place reconmended running the gas at a really high rate, it helps cool the work peice so you don't burn
through.
|
|
oadamo
|
posted on 12/5/07 at 03:25 PM |
|
|
what welding set do you have or what controls are on it
adam
|
|
nitram38
|
posted on 12/5/07 at 04:25 PM |
|
|
Round off your tungsten before you start. Don't use a pointed one!
Also sink it further back into the ceramic.
[Edited on 12/5/2007 by nitram38]
|
|
907
|
posted on 12/5/07 at 07:15 PM |
|
|
Hi Nat
I believe you are a lover of the foot pedal, so to form your balls ( ) whack the amps up to about 200
and arc up on a thick piece of scrap. Steadily increase the current with the pedal till a ball end forms.
Obviously the current required will depend on the size of your tungsten, and the size of the balls you require. ( )
It's normally accepted that when welding thin ally that you use a filler rod a size bigger than the sheet thickness.
i.e. 1.5mm sheet, use 2 or 2.4mm rod. Dip into the front edge of the pool, not under the tungsten.
I have a feeling that you don't have the pos/neg balance set right. Do you get an area either side of the
finished weld that has a white frosted appearance? How wide is it?
This is the area that the cathodic action of the arc is cleaning the oxide off the surface of the sheet.
Gas flow required is 10 to 14 lpm. Double this figure for cfh. Don't rely on the round gauge on the regulator.
They work on pressure, not flow, so they can be inaccurate. Use a flow meter, i.e. ball in a glass tube.
Is your tungsten still silver after welding?
It's better to have slow moving gas through a large ceramic than a jet of gas from a small ceramic.
If you haven't a diffuser in the head then pack a ring of wire wool up inside the lens.
Hth
atb
Paul G
|
|
Gav
|
posted on 13/5/07 at 08:33 AM |
|
|
One thing that i found was i had to clean the electrodes with some stainless wire wool first, otherwise they just wouldnt run into the weld, id just
get big blobs that wouldnt melt which i suspect was that the oxide layer from the electodes not letting it run.
|
|
NS Dev
|
posted on 13/5/07 at 11:50 AM |
|
|
quote: Originally posted by 907
Hi Nat
I believe you are a lover of the foot pedal, so to form your balls ( ) whack the amps up to about 200
and arc up on a thick piece of scrap. Steadily increase the current with the pedal till a ball end forms.
Obviously the current required will depend on the size of your tungsten, and the size of the balls you require. ( )
It's normally accepted that when welding thin ally that you use a filler rod a size bigger than the sheet thickness.
i.e. 1.5mm sheet, use 2 or 2.4mm rod. Dip into the front edge of the pool, not under the tungsten.
I have a feeling that you don't have the pos/neg balance set right. Do you get an area either side of the
finished weld that has a white frosted appearance? How wide is it?
This is the area that the cathodic action of the arc is cleaning the oxide off the surface of the sheet.
Gas flow required is 10 to 14 lpm. Double this figure for cfh. Don't rely on the round gauge on the regulator.
They work on pressure, not flow, so they can be inaccurate. Use a flow meter, i.e. ball in a glass tube.
Is your tungsten still silver after welding?
It's better to have slow moving gas through a large ceramic than a jet of gas from a small ceramic.
If you haven't a diffuser in the head then pack a ring of wire wool up inside the lens.
Hth
atb
Paul G
I had worried about this........as far as I know my machine has no balance control on it.
Its an ESAB DTA ACDC 200 Squarewave
Will give it a bootful and melt the end of the tungsten then, that sounds feasible!
There is a white frosty bit either side of the weld, and I can see it forming as i weld.
I use a gas lens body with gauze diffuser in it for everything, I found these much better than the normal collet bodies with gas holes in even on
steel and stainless, much neater welds.
I think the ball end bit is probably the biggest issue, as the arc did seem very unstable!
It is worrying that I have no balance control, but then the machine is obviously designed for welding ally as well so must be ok I guess???
The Murex equivalent machine which appears to share the same innards is the Murex ACDC 205, but this machine does have balance control!
Retro RWD is the way forward...........automotive fabrication, car restoration, sheetmetal work, engine conversion
retro car restoration and tuning
|
|
907
|
posted on 13/5/07 at 03:35 PM |
|
|
Hi again.
I Googled your set model and couldn't find a mention of a balance either.
We can only assume that it's preset.
The Lincoln I use at work has a 1 to 10 switch with the word "balanced" against the figure 3.
It also has a position 11 which is marked "Auto Balance", which is where I normally have it set.
My Miller at home can be set anywhere.
If you grind a 2.4 tungsten to a point you should be able to get it to ball to the size to suit the job.
I like a 1.5 dia end for welding up to 16swg and bigger for thicker stuff.
Go put the pedal to the metal.
Good luck
Paul G
|
|
NS Dev
|
posted on 13/5/07 at 04:19 PM |
|
|
Right, the tig is good an warm now!!
Been working all afternoon practicing......................
First of all, the tungstens I am using don't ball up!!! I have now done a little reading in a miller guide thingy I printed out and they suggest
some of the tungsten types don't ball up, and I guess mine must be these! I put a point on a 2.4mm grey tungsten, and hit it with 190 amps on AC
onto a piece of steel as I had no thick ally. It rounded the point a little but just made the whole tungsten go nearly white hot, the end remained
less than 0.8mm as a guess!!!!!
I only have grey and white tungstens, and have forgotten what they actually are now, other than that the welding chap said that the grey ones were
"universal" whatever that means!!??
I will buy a load more and see.
I actally started to get to grips with it though. I ground a point then touched the linisher onto the tip to put a flat on it, and have now run 20
decent beads on some flat 1.5mm ally. ok they aren't "stacks of dimes" but they are nicely dipped and free of contamination.
I've mastered getting the puddle clean and keeping it clean.
A problem which has now arisen, and I guess its the tungsten type again, is that I can't get the arc to strike up once the tungsten has been
used........????
I grind it, ti strikes up fine on the HF. Then I stop welding, and go to restart, and the HF fires away merrily but I can't get the arc to
start??? If I regrind the tungten, it will start fine again!!
Any ideas?? On DC it starts fine every time. If I rub the tip of the tungsten on the ally to pick a smudge up on the tip then try it it fires up
ok.
My bloody belt linisher has also now packed in!!!
Retro RWD is the way forward...........automotive fabrication, car restoration, sheetmetal work, engine conversion
retro car restoration and tuning
|
|
907
|
posted on 13/5/07 at 05:49 PM |
|
|
Hi yet again Nat
It is an earth problem. Not earth as in return lead, but earth as in ground.
Welders tend to be mounted on rubber wheels or feet and parts of your workshop won't be earthed properly.
(I keep meaning to earth my galv roof.)
Your welding bench just sits on the concrete floor with no proper earth; am I right?
So, static builds up while welding and needs to be released to earth before it will let the HF restart the arc.
If you look carefully at the tungsten when you touch it on the metal, without your mask, you will see a tiny spark.
I get this about every 6th start but it becomes second nature to touch down, lift off, then start up.
Regulations have cut the power of HF circuits to a point where we now have this problem.
20 years ago I had a BOC that would cut out the internal phones at work.
These things are sent to try us.
Atb
Paul G
p.s. The white ones are for ally.
[Edited on 13/5/07 by 907]
|
|
NS Dev
|
posted on 14/5/07 at 07:08 AM |
|
|
ahhhhhhhhhhhhhhhhhhhhhhhhhhhhhhhhhhhhhhhhhhhhhhhhhhhhhhhhh!!!!
yep, bench straight on the floor with no extra earth!
That would make sense as i did get the odd tingle through my arm yesterday at the bench, and if it was the HF doing it I guess it would have been more
than just a tingle!
Bench top is also melamine, I weld on an 8mm plate on top of that, so no real earth route other than the earth lead, and the machine has no extra
ground other than the normal mains one.
Retro RWD is the way forward...........automotive fabrication, car restoration, sheetmetal work, engine conversion
retro car restoration and tuning
|
|
omega 24 v6
|
posted on 14/5/07 at 11:30 AM |
|
|
Been following this one with interest and wondered now are we saying that the earth to the workpiece is NOT enough. If welding on top of a wooden
bench with a steel/alloy or any other conductive plate on it does this need to be seperately earthed??
If it looks wrong it probably is wrong.
|
|
907
|
posted on 14/5/07 at 06:44 PM |
|
|
Hi,
I know we all refer to the return lead as the "earth" but it isn't.
The return lead completes the circuit from the work, back to the welder.
The "earth" is just a slang term that us welders use, and after a period of time,
becomes the accepted terminology.
Below is a diagram taken from the Miller Dynasty 200 owners manual.
It's in the Maintenance & Troubleshooting section.
It applies to HF welders only.
Can I say that some of it seems a little OTT in my opinion, and that a starting point
would be to earth the welder case and the metal bench, and therefore the workpiece.
This would solve most problems IMHO.
Paul G
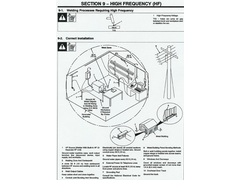 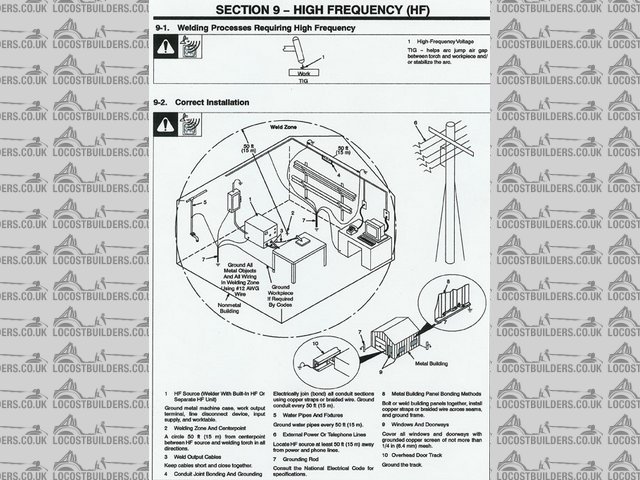 Rescued attachment Miller-O-Man-TS-HF-s.jpg
|
|
NS Dev
|
posted on 14/5/07 at 08:37 PM |
|
|
Hi again Paul,
been doing a bit more this evening.
Don't think its the static stopping the arc unfortunately. Sometimes no matter how much i touch the tungsten to the work it still wont start the
arc, I have to basically do a lift start to get it to start. It will hold an HF arc 1.5 inches long but even with only 1mm gap won't start the
arc.
As soon as I regrind the tungsten it starts instantly???
I also have a problem in that I can do a lovely weld bead for about 2 inches on a reground tungsten (ground to a point then the end flattened) and
then the arc starts to wander all over the place, usually coming out of the back of the tungsten somewhere!! I have also had it start arcing out of
the side of the tungsten about 12mm above the tip, up inside the ceramic?????!!!!!!!!!!!!!!! several times as well, on several regrinds and several
tungstens!!!!
What on earth am I doing wrong!???
Both the unstable arc and inability to restart seem to be cured by giving the tip of the fresh tungsten a really good dig on the surface of the ally
while its still codl at the beginning.
I am really confused!
I will be getting some new white tungstens in the next couple of days, but the grey and white ones both suffer exactly the same symptoms, and on ebay
a tig spares seller clearly states that the ceriated grey tungstens are a perfectly good substitute for both thoriated and zirconiated ones.
Retro RWD is the way forward...........automotive fabrication, car restoration, sheetmetal work, engine conversion
retro car restoration and tuning
|
|
907
|
posted on 14/5/07 at 09:21 PM |
|
|
3 things to try Nat.
Experiment with gas rate.
Turn it up, try. Turn it down, try again. Gas flow effects arc stability.
Clean inside your ceramic.
HF could be tracking to the spatter on the inside of the lens.
If you have a set of HF points (like CB points in a dizzy but bigger) clean and adjust the gap.
Clean the insulated block that holds them. It gets caked with grinding dust and becomes current conducting.
Does the HF buzz loudly when you fire up, with the torch away from the work? It should do.
Some sets, I'm not familiar with ESAB, have a HF switch, off, start, or continuous.
For AC welding set to continuous.
On others it's automatic when switched from DC to AC.
(Wild stab in the dark this one. )
Don't give up
Paul G
|
|
NS Dev
|
posted on 14/5/07 at 09:28 PM |
|
|
cheers again paul!!
The dirty ceramic thing is a good point, I have had the same one on through all the hassle, and come to that I can't remember the same trouble
before I swapped over to this one (a number 8, upped to it from a 7 to get a batter gas spread)
On my machine the HF is continuous on AC mode, yep it buzzes a lot when you arc up in mid air!!
The machine does have a spark plug inside it for its air gap, do you mean clean and regap this??
Retro RWD is the way forward...........automotive fabrication, car restoration, sheetmetal work, engine conversion
retro car restoration and tuning
|
|
907
|
posted on 14/5/07 at 11:01 PM |
|
|
quote: Originally posted by NS Dev
cheers again paul!!
The dirty ceramic thing is a good point, I have had the same one on through all the hassle, and come to that I can't remember the same trouble
before I swapped over to this one (a number 8, upped to it from a 7 to get a batter gas spread)
On my machine the HF is continuous on AC mode, yep it buzzes a lot when you arc up in mid air!!
The machine does have a spark plug inside it for its air gap, do you mean clean and regap this??
Yup, clean it.
I had trouble with one machine and found that over the years the fan had sucked in dust and the arcing of the unit
had "welded" the metal dust onto it, allowing the HF to track down the side to the machine frame.
This halved the power of the HF circuit.
Is a number 8, 8mm? If so this seems small for ally.
I did a weld tonight to measure the width of the cathodic cleaning area. A 6mm wide weld (on 1.5 sheet) had 4mm
of cleaned area either side. That's 14mm wide that the gas has to cover. My ceramic is 12mm i.d.
Size does matter.
Paul G
|
|
Doug68
|
posted on 17/5/07 at 07:48 PM |
|
|
I think the numbers are the diameter in 1/16ths of an inch a number 7 measures 11mm across for example.
So an 8 would be 1/2" or 12.7mm
Can anyone confirm?
|
|
NS Dev
|
posted on 17/5/07 at 09:18 PM |
|
|
sounds about right, not measured but I think the 8 cup looks about 1/2"
Retro RWD is the way forward...........automotive fabrication, car restoration, sheetmetal work, engine conversion
retro car restoration and tuning
|
|
oadamo
|
posted on 17/5/07 at 10:18 PM |
|
|
pmsl at this thread
put earth lead in welder onto your work or bench you dont need 200 leads lol
use a white tungsten 2.4mm
use a 7 or 8 ceramic doesnt matter what one you use. have the tungten 5mm out of the ceramic and keep the tip with in 10mm of the alloy that you are
welding
if your welding prob 3-5mm use about 80 amps you need a lot of power to break the top surface. when you start it might look black but should clean you
when you start doing a run
if you are still having probs after that its your welder
disconnect the pedel then try again
then if your still have shit
turn power off. take side of welder off there should be a block with 2 what look like motor bushes if you turn your power on and push the botton you
will see the solinoid connect the 2 bushes together.
turn power off then take bush things out and clean them when you put them back in make sure the gap is about 1mm. this is the hf solinoid. this is
what starts playing up and gives you poo when you try to ark up.
if your still having probs your welder needs fixing
adam
[Edited on 17/5/07 by oadamo]
|
|