Lotusmark2
|
posted on 23/7/05 at 05:51 AM |
|
|
Cutting arcs in the ends of round tube
HI, I am going to be adding a couple of additional tubes to my chassis but I need to use round tube, it will be welded at an angle on to the side of
other round tube so considering how to cut the arc in the end of the tube to get a good close fit before welding.
Does anyone know a source for a grinding bit or tool to make this easier?
Cheers
Mark
|
|
|
Mix
|
posted on 23/7/05 at 06:41 AM |
|
|
Do a search for a shareware program called tubemiter, very good for marking the tubes and then easily ground out with an angle grinder and tidied up
with a file.
Mick
|
|
Deckman001
|
posted on 23/7/05 at 07:49 AM |
|
|
Or you could get your self a 'Bird mouth' cutter, try looking on E-bay U.S. for them
Jason
|
|
Avoneer
|
posted on 23/7/05 at 09:07 AM |
|
|
Get tubemiter.
Cut a two 45 degree cuts with your hacksaw and fileout.
Pat...
No trees were killed in the sending of this message.
However a large number of electrons were terribly inconvenienced.
|
|
Avoneer
|
posted on 23/7/05 at 09:08 AM |
|
|
And the instructions:
No trees were killed in the sending of this message.
However a large number of electrons were terribly inconvenienced.
|
|
Avoneer
|
posted on 23/7/05 at 09:28 AM |
|
|
I think someone should make something like this and do it for everyone at a small fee:
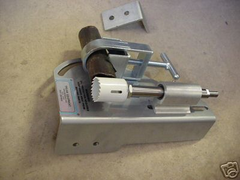 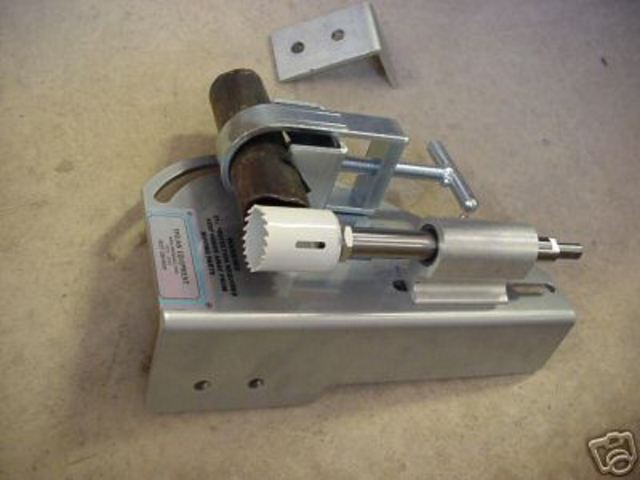 Rescued attachment d1_1.JPG
No trees were killed in the sending of this message.
However a large number of electrons were terribly inconvenienced.
|
|
mangogrooveworkshop
|
posted on 23/7/05 at 10:06 AM |
|
|
quote: Originally posted by Avoneer
I think someone should make something like this and do it for everyone at a small fee:
The cage people who went bust recently charged £138 quid for those.
mmmmmm
|
|
mangogrooveworkshop
|
posted on 23/7/05 at 10:08 AM |
|
|
quote: Originally posted by Deckman001
Or you could get your self a 'Bird mouth' cutter, try looking on E-bay U.S. for them
Jason
think you mean FISH MOUTH search blind chicken racing
http://www.blindchickenracing.com/Tools/Tube%20Notcher/Tubing%20Notcher.htm
[Edited on 23-7-05 by mangogrooveworkshop]
|
|
Deckman001
|
posted on 23/7/05 at 10:22 AM |
|
|
Maybe, I don't have one, a friend told me about them, so maybe the name got lost in tranlation from waddon to South Croydon !!
Jason
|
|
the JoKeR
|
posted on 23/7/05 at 03:16 PM |
|
|
Here's a low-cost alternative, if you've got a drill press. Looks like it'd take a little bet of setup, but then you could quickly
cut out the ends as needed.
http://texaslocost.homestead.com/Suspension.html
__________________________
Jeff
http://www.midwestwelding.com
http://www.locostusa.com/forums/
|
|
Lotusmark2
|
posted on 23/7/05 at 05:00 PM |
|
|
Thanks for all the ideas guys
|
|
mark chandler
|
posted on 23/7/05 at 05:59 PM |
|
|
I used my Piller drill with a hole saw, ended up bending the morse taper that held the chuck when it snagged. I failed to grip the tube firmly enough,
mind you its was 2" scaffold pole. Take care and use lots of lubricant.
|
|
jolson
|
posted on 23/7/05 at 06:36 PM |
|
|
Don't mess around... just use tubemiter or similar, make a paper wrap, glue it on (3M spray adhesive works a treat), and whiz it out with the
angle grinder. A 1.6mm disc can cut remarkably close to the line.
I build cycle frames for a living and do a couple dozen joints like this every week. Hole saws are difficult to use, tend to rip the thin walled
tube, and involve too much setup for just a couple of joints. We've tried jigs like the one Avoneer showed, but holding the hole saw steady
enough for a nice clean hole is difficult. They're just not meant for this sort of application, but they work well on heavy walled pipe. A big
lathe with a milling cutter can work, but it's even more effort to set up and cutters aren't cheap. The proper machine for the job is a
tube/pipe notcher like this:
(we just got one at work) but you need to do a few hundred joints to make it worthwhile.
Cheers
John
|
|
Lotusmark2
|
posted on 23/7/05 at 07:04 PM |
|
|
Yeah, will be going that route, just a bit more control than the hole cutter.
Cheers
|
|
Rorty
|
posted on 28/7/05 at 05:20 AM |
|
|
quote: Originally posted by Deckman001
Or you could get your self a 'Bird mouth' cutter, try looking on E-bay U.S. for them
Jason
Birds mouths are what you cut in rafters where they join the wall plate.
Fishmouths are what you cut in tube.
Here are plans to make a hole saw type tube notcher
Cheers, Rorty.
"Faster than a speeding Pullet".
PLEASE DON'T U2U ME IF YOU WANT A QUICK RESPONSE. TRY EMAILING ME INSTEAD!
|
|
NS Dev
|
posted on 28/7/05 at 07:35 AM |
|
|
I mark the ends of the tube and then put the form on with a die grinder with a carbide cutter in it.
|
|
timf
|
posted on 28/7/05 at 07:41 AM |
|
|
the chopsaw/cutoff saw method
The chop saw method, if understood, is a science. With known tube size and joint angle, tube can be notched with great accuracy. The notch is achieved
by cutting two opposing angles on one end of a piece of tube, to form a point. The cross-section of this cut will be an elliptical cut due to the
shape of the tube. Changes in both of the two angled cuts must be made for the intersection angle and the size of the two tubes being joined. The only
real limitation is the max angle of the chop saw.
You start with what I call the base angle. This is the angle of both cuts if the joint was 90*. For an example, I am fitting Two tubes together that
are both 1.75", at an 90* joint. The base angle, or the angle of both cuts is 28*. These two cuts must meet at a point, and the point must also
be centered on the tube.
What if I want a 15* joint with my 1.75" tube???? You must start with your base angle, which was 28* for 1.75"(remember above), and
subtract 15* from one cut, and add 15* to the other cut to form a perfect notch. So now I must make a 13* cut and an 43* cut with the point centered
on the tube. Perfect coped joint, with no grinding.
Remember your base angle will change with the tube being cut and the tube that you are fitting to.
Here are a few examples of base angles...
2.0" to 2.0" tube, base angle of 30*
1.75" to 1.75" tube, base angle of 28*
1.5" to 1.5" tube, base angle of 26*
1.25" to 1.25" tube, base angle of 22.5*
1" to 1" tube, Base angle of 20*
Now to fit different size tubes together
1.75" to 2" tube, base angle of 25*
1.75" to 1.25" tube, base angle of 45*
1.25" to 1.75 tube, base angle of 20*
1" to 2" tube, base angle of 12*
|
|
Mix
|
posted on 28/7/05 at 07:58 AM |
|
|
Thanks Tim
One for the future
Mick
|
|
johnjulie
|
posted on 31/7/05 at 07:01 PM |
|
|
A good quality round grinding wheel of the same or smaller diameter as the curve required will do the trick! As already mentioned remove as much as
you can with a saw or angle grinder, and finish off with the wheel.
Cheers J&J
|
|