Bob C
|
posted on 19/4/05 at 12:01 PM |
|
|
stress analysis using FEA in solidworks
I had a go with COSMOSexpress at the weekend, wanted to check if I'd gone OTT drilling holes in my brake pedal to lighten it.
Bottom line - it's 30% lighter and 10% weaker. So just about worth it.
Main point - if you have solidworks try the FEA package - it's dead easy to use &draws a picture of where you've messed up your design
(actually it makes a movie of it....). Very easy to add webs etc. to get your desired strength & checkout the results. I'll post pictures
later.
Bad bits -
1)restraint specification overspecifies restraint, effectively putting an infinitely stiff invisible external structure round the part's
mountings
2)output is an avi file - I can't print it! (but I'll find a way)
cheers
Bob
PS I reckon brake pedal is most highly srtessed part of car! I've assumed 1000N pedal force
|
|
|
adam_moore
|
posted on 19/4/05 at 12:05 PM |
|
|
Just a thought on the pedal force you are using. I think 1000N is about right (effectivly a 100kg person standing on it) but the Ford (road car)
specification for a pedal test is 2000N with a max displacement of 10mm and no more than 1.5mm permenant set.
I'd go for 1500N to be safe. I think thats what i used for the analysis I did on a concept aluminium design (see photo archive).
|
|
scoobyis2cool
|
posted on 19/4/05 at 12:12 PM |
|
|
quote: Originally posted by adam_moore
The Ford specification for a pedal test is 2000N with a max displacement of 10mm and no more than 1.5mm permenant set.
Hi Adam, what exactly do you mean by 10mm displacement and 1.5mm permanent set? Do you mean the pedal should flex by 10mm under that amount of load?
Is it acceptable to have such a large amount of flex or have I missed the point?
Cheers,
Pete
[Edited on 19/4/05 by scoobyis2cool]
It's not that I'm lazy, it's that I just don't care...
|
|
bigandy
|
posted on 19/4/05 at 12:14 PM |
|
|
Aye, COSMOSexpress is pretty good for individual parts. the analysis doesn't give you much control over the simulation, but it does provide a
fairly reliable "look-see" to give you an idea of what will happen.
As you have found, the constraints are pretty limiting, mainly because the limit control you have over them. on the other hand it does simplify the
process somewhat!
Cheers!
Andy
Dammit! Too many decisions....
|
|
scoobyis2cool
|
posted on 19/4/05 at 12:17 PM |
|
|
Has anyone tried ANSYS? I've got a copy of that which I think will work will SolidEdge (got that too), but I haven't tried it out yet.
Pete
It's not that I'm lazy, it's that I just don't care...
|
|
JonBowden
|
posted on 19/4/05 at 12:25 PM |
|
|
I am short and skinny. I weigh 60kg
That means that if I stand on something I apply 600N force.
My leg is not stressed lifting my weight. I could easily support twice my weight on one leg.
Thus I guess I could apply more than 1000N to a brake pedal.
Now, take someone strong - they could apply more than twice that.
I would go for at least 3000N before the pedal breaks
Jon
|
|
bigandy
|
posted on 19/4/05 at 12:38 PM |
|
|
Ansys is pretty damn good. that is the weapon of choice where I work (both workbench which integrates partially with Solidworks, and the more fully
featured version). I'm still picking up Ansys through questioning the more experienced stress guys at work, but from what i can tell, it
simultes stuff really well.
It all depends on how you set the analysis up though. crap in = crap out and all that!
As for brake pedal force, then how about me as an example. My mass is 129kilos (as of last saturday.. maybe less now, i had salad for lunch, and am
still rather peckish!). that means me standing on a pedal, gives around 1290N force. I play prop forward in a rugby team, and due to injury I ended
up with a braken toe, which meant one legged Squats in the gym. I can happily lift around 70 kilos on one leg, So that is around a 700N force. that
means i could easily exert nearly 200N on a brake pedal.
Now take an emergency application of the brake pedal, where I am fast approaching a wall. I would more than likely find a few more newtons of
strength from somewhere, which could easily take me up to around 2500N.
taking a factor of safety of 2, to allow for, well, saftey, then that puts it up around 5000N!
Of course, you could take this to the extreme, and make the pedal impossibly strong, to cope with a theoretical situation, and factor of safety. or,
you could look at it in the way I did. I'm a fairly perceptive driver and i can sense when the wheels have locked up. I'm hazarding a
guess that the wheels would lock up well before someone could apply 2000N to a brake pedal, so why design them any stronger? (okay allow a margin for
safety)
Juat thinking out loud!
cheers
Andy
Dammit! Too many decisions....
|
|
scoobyis2cool
|
posted on 19/4/05 at 01:17 PM |
|
|
Would it be worth doing an analysis on a current pedal design (for example the MK pedal, very simple design), to get an idea of how much force they
can take? I've never heard of one of their pedals snapping so presumably they're strong enough, might be a starting point for your
design.
Pete
It's not that I'm lazy, it's that I just don't care...
|
|
adam_moore
|
posted on 19/4/05 at 01:17 PM |
|
|
You are reading correct. We have done some stress analysis recently on pedals for a Ford vehicle and with a static 2000N load, a displacement of 8mm
(not what i originally said) is acceptable and a perminant set of 1.5mm maximum. This implies that an amount of plastic bending is allowed to take
place...?!
I used Ansys at University and its a good package. I use software called Altair Optistruct (or MSc Nastran) at work for static analysis.
|
|
tom_loughlin
|
posted on 19/4/05 at 01:40 PM |
|
|
Havent used ansys for analysuis, but i haver used it a lot, both workbench and ice-m for generating meshes for my aero dissertation. i reckon ice-m is
by far the best for my type of problem. a lot of people swear by NASTRAN.
Tom
|
|
liam.mccaffrey
|
posted on 19/4/05 at 04:24 PM |
|
|
like ansys used it in uni
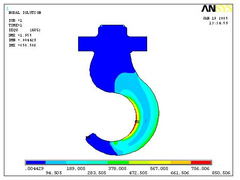 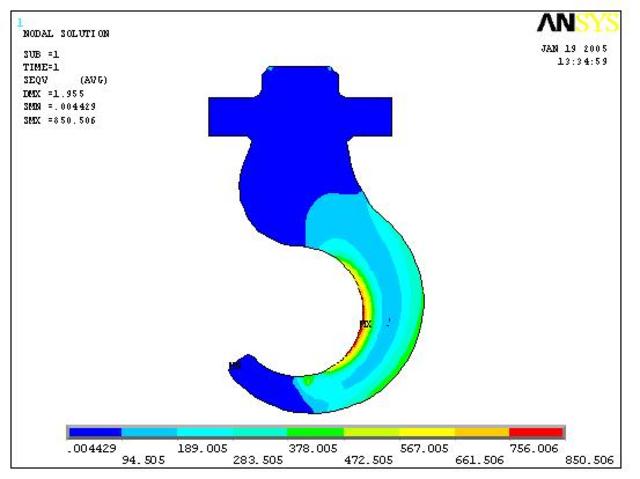 ansys hook
solidworks cosmoss express is pretty useful. i have the student edition which has cosmoss proper but not had a chance to use it. (student edition
with cosmoss £100 quid odd not bad)
Build Blog
Build Photo Album
|
|
Rorty
|
posted on 20/4/05 at 05:17 AM |
|
|
5000N! Steady on chaps! It's going up all the time.
Before getting too wild with pedal analysis, take a look at the clevis and clevis pin to see what they will withstand.
It's all very well having a pedal that could pry the turret off a Chieftan, but if the clevis (or any other part in the chain) is substantially
weaker, then the pedal strength is moot.
Cheers, Rorty.
"Faster than a speeding Pullet".
PLEASE DON'T U2U ME IF YOU WANT A QUICK RESPONSE. TRY EMAILING ME INSTEAD!
|
|
Bob C
|
posted on 20/4/05 at 11:57 AM |
|
|
The 1000N figure was indeed one I just made up - based on my weight(!). I also reckon I could press much harder than that, but wouldn't because
300N will theoretically lock the wheels....
This figure is the highest stress in a tiny bit of the pedal, a "yeild" here would transfer a higher stress to a larger region and result
in a permanent "set". However my mistake was in building the pedal out of bits of scrap - means I had to use the most useless steel in the
model (ANSI304 from memory). I actually used soft "black" mild steel so it's almost certainly fair enough!
I'll get the pictures on here when I get a chance to work out how to do it. Next job is to stick extra metal on until I get to 1500N -
that'll do me.
If the pedal collapses in a head-on crash it might just mean my ankles won't!
cheers
Bob
|
|
scoobyis2cool
|
posted on 20/4/05 at 02:43 PM |
|
|
quote: Originally posted by Bob C
If the pedal collapses in a head-on crash it might just mean my ankles won't!
That's the spirit!
Pete
[Edited on 20/4/05 by scoobyis2cool]
It's not that I'm lazy, it's that I just don't care...
|
|
greggors84
|
posted on 20/4/05 at 06:36 PM |
|
|
I know the point of this topic isnt just the weight saving, but is there any point trying to save 30% of your pedal weight if it is going to
compromise its strength.
30% of your pedal is nothing really, maybe have a haircut before you go out for a drive or maybe drive naked! You would save some weight doing
that.
All that said FEA is very interesting and gives a useful graphic representation of stress and strain. Like rorty said try modelling your whole
linkage, and maybe the firewall or what ever your pedal boxes mounts to, then you are removing some of the points of infite rigidity, i guess however
much you model though its got to be mounted somewhere, so you will never get rid of it.
Chris
The Magnificent 7!
|
|