Cita
|
posted on 25/1/05 at 08:01 PM |
|
|
RHS bend
Hi guys,
i need to have a section of RHS 20 x 1.5 bend half a circle with radius 80 mm.
Any suggestions-idea's other than impossible please?
|
|
|
Lawnmower
|
posted on 25/1/05 at 08:09 PM |
|
|
Does it have to be strong/structural?
If not you could cut slits into one side and bend it, then weld it back together.
What part is it for.
|
|
Mark Allanson
|
posted on 25/1/05 at 08:53 PM |
|
|
It would be stronger to make up 2 'C' shaped bits of plates used as the upper and lower, and bend some 1" strap to make the sides. I
don't think you could bend down to such a tight raduis without some serious bulges/splits.
If you can keep you head, whilst all others around you are losing theirs, you are not fully aware of the situation
|
|
Cita
|
posted on 25/1/05 at 08:55 PM |
|
|
  
|
|
JoelP
|
posted on 25/1/05 at 08:57 PM |
|
|
80mm is a very tight bend cita... doing it marks way wouldnt be that hard either.
|
|
David Jenkins
|
posted on 25/1/05 at 08:57 PM |
|
|
Professional fabricators use a special bending tool that neatly collapses the sides, allowing the piece to bend. Have a look at a stacking chair made
of square steel to see what I mean (if it's got nice rounded bits, that is! )
David
|
|
nick205
|
posted on 25/1/05 at 09:21 PM |
|
|
Hi Cita,
Why don't you try Martin Keenan @ MK Engineering. He's pretty handy at bending tube and box
section. The Indy and GT chassis both feature some nicely bent box sections.
HTH
Nick
|
|
Peteff
|
posted on 25/1/05 at 09:25 PM |
|
|
It's a fair old trek to MK from Belgium.
yours, Pete
I went into the RSPCA office the other day. It was so small you could hardly swing a cat in there.
|
|
Mark Allanson
|
posted on 25/1/05 at 10:05 PM |
|
|
quote: Originally posted by David Jenkins
Professional fabricators use a special bending tool that neatly collapses the sides, allowing the piece to bend. Have a look at a stacking chair made
of square steel to see what I mean (if it's got nice rounded bits, that is! )
David
Its usually done by pre collapsing the inner wall to prevent the bulging problem
If you can keep you head, whilst all others around you are losing theirs, you are not fully aware of the situation
|
|
Rorty
|
posted on 26/1/05 at 05:45 AM |
|
|
80mm is doable for that size of tube with a square upsetting die, but the only problem is, 80mm is not a standard size; 75 is the closest.
If you have a tube bender, then you could turn a temporary die for it out of maple or beech which would last for quite a few bends.
You may be able to find an engineering works that could do it for you. As David Jenkins hinted, a steel furniture maker may be a good starting point.
Cheers, Rorty.
"Faster than a speeding Pullet".
PLEASE DON'T U2U ME IF YOU WANT A QUICK RESPONSE. TRY EMAILING ME INSTEAD!
|
|
907
|
posted on 27/1/05 at 09:03 PM |
|
|
Hi All,
As Mark suggests, make them from sheet.
I'v used 8 off 90deg bends on my chassis.
4 for the rear corners, 4 for the scuttle.
I made 2 rings, and after welding & cleaning up,
cut each ring into 4.The advantage of welding a
ring is that it does't distort out of shape.
Paul G
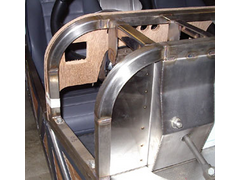 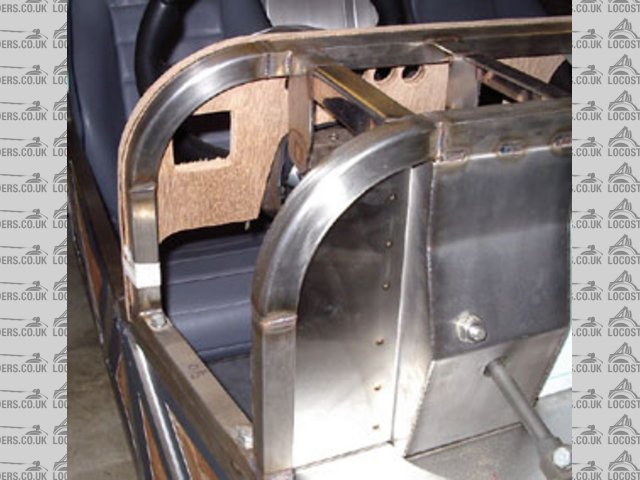 Rescued attachment RHS bend 005s.jpg
|
|
Rorty
|
posted on 27/1/05 at 09:33 PM |
|
|
quote: Originally posted by 907
Hi All,
As Mark suggests, make them from sheet.
I'v used 8 off 90deg bends on my chassis.
4 for the rear corners, 4 for the scuttle.
I made 2 rings, and after welding & cleaning up,
cut each ring into 4.The advantage of welding a
ring is that it does't distort out of shape.
Paul G
That's as nice a bit of Locosting I've seen for a while.
Cheers, Rorty.
"Faster than a speeding Pullet".
PLEASE DON'T U2U ME IF YOU WANT A QUICK RESPONSE. TRY EMAILING ME INSTEAD!
|
|
907
|
posted on 27/1/05 at 10:14 PM |
|
|
Thank you Rorty.
Paul G
ps You have just made me think of a new signature.
|
|
MikeRJ
|
posted on 28/1/05 at 11:41 AM |
|
|
That is a very nice bit of work, I'd be dead proud of that!
|
|
Cita
|
posted on 28/1/05 at 04:38 PM |
|
|
Bloody hell!!! (sorry guys)
Paul THAT is a nice bit of metal working!!!
I never can get to that with my skills so instead i will try to bend the tube...probably without succes.
|
|