David Jenkins
|
posted on 20/1/07 at 03:28 PM |
|
|
Lathe shifting
I'm working really hard to sort out my garage, as it's been a real tip lately, I'm running out of space and I can never find anything.
I'm doing quite well so far, with 2 new shelf units and some serious throwing out of rubbish, but I have one remaining problem.
Currently my Colchester Student lathe is backed up against the wall. Very convenient to use, but maintenance is impossible and there's a lot of
wasted wall space behind it. I want to turn it so that the tailstock end is to the wall, and the headstock goes to the middle of the garage (I have
no problem with space there).
The problem is its weight - 1400lbs, or 635Kg - which is heavier than my Locost! It was originally put in place by me, my son and the bloke who
delivered it; he had a hoist, levers and "roller skates" designed for moving heavy machinery. He also had decades of experience! I've
only got a good lever...
It's way beyond the capacity of my engine hoist, and I don't have any strong beams overhead.
Any helpful suggestions will be gratefully received. My drive belt is starting to slip so I need to get this sorted soon!
cheers,
David
 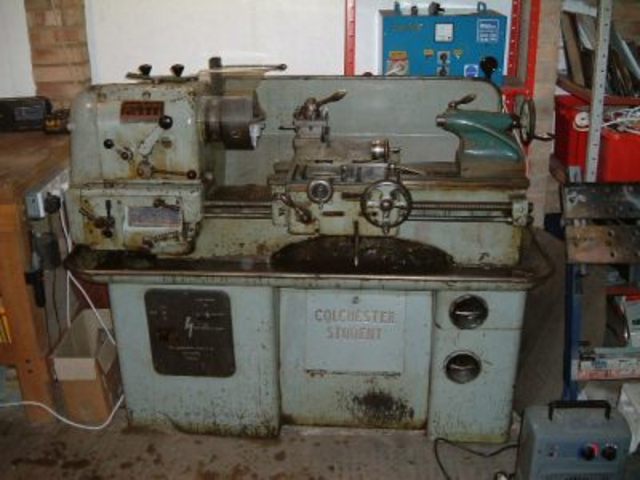 Rescued attachment DSCF0034.JPG
|
|
|
stevebubs
|
posted on 20/1/07 at 03:34 PM |
|
|
Borrow an engine hoist that will cope with the weight?
|
|
scottc
|
posted on 20/1/07 at 03:36 PM |
|
|
Large rope attached to one side and the other end tied to the tin top. pit some washing up liquid on the floor?
|
|
owelly
|
posted on 20/1/07 at 03:38 PM |
|
|
Use lumps of bar or tube (scaffold tube?) to use as rollers. You can use wedges/jacks to get it high enough to get the rollers under. Or slide lumps
of sheet metal underneath and slide it.
You could always bolt some bits of angle iron onto the bottom of it to enable you to get a couple of trolley jacks under.
[Edited on 20/1/07 by owelly]
[Edited on 20/1/07 by owelly]
http://www.ppcmag.co.uk
|
|
Wadders
|
posted on 20/1/07 at 03:45 PM |
|
|
Hi david
i frequently move my harrison around on my own (similar size & weight). if you put a bottle jack or trolley jack under the lip of the coolant
catch tray, lift one end and slip something like 20mm round bar under for rollers, i use 3 lengths, uou'll find it whizzes round really
easily.
ATB
Al.
|
|
Jon Ison
|
posted on 20/1/07 at 03:45 PM |
|
|
quote: Originally posted by scottc
Large rope attached to one side and the other end tied to the tin top. pit some washing up liquid on the floor?
This method plus jack it up a little too get some metal sheets under it will work, we have used shovels in the past, they make great skids.........
|
|
pathfinder
|
posted on 20/1/07 at 03:45 PM |
|
|
I’ve got exactly the same problem with my student at the moment. 3 big blokes don’t stand a cat in hells chance of shifting it (we have tried and
failed) An engine hoist wont be any good for moving the complete unit either its to big and awkward, we are going to split it in half and move the
base by hand (its still bloody heavy with that steel joist in it) and move the top half with an engine hoist (legs straddling the front and rear of
the base).
Our other option was to use the front end loader on a mini digger and move it in one piece but our sealing height is a bit low for that. Colchester
lathes are an awesome bit of kit and I couldn’t do without it, moving them is a total pain in the arse tough!
|
|
907
|
posted on 20/1/07 at 04:02 PM |
|
|
Hi David,
Big tyre levers (or wrecking bar) to get it high enough to slip pipe under.
I've got bitumen backed carpet tiles under mine to take up irregularities in the concrete.
I think it helps reduce noise transmission through to the house.
If you need a hand, give us a shout.
Atb
Paul G
[Edited on 20/1/07 by 907]
|
|
David Jenkins
|
posted on 20/1/07 at 04:05 PM |
|
|
The only way an engine hoist is going to be any use is if it can lift the weight when fully extended - my hoist can only manage 185Kg in that
configuration. It'll have to be a hell of a hoist to lift that weight when extended right out!
Sheet metal's a thought, but that's quite a mass of iron to get sliding.
I'll have to see if I can rig up some rollers - it's actually quite easy to lift the lathe a few inches, by using a long lever into one of
the slots at the end and a pivot a short way away. It doesn't take much effort downwards to raise the lathe, when you've got a 20:1
ratio!
My problem is at the tailstock end, where there's not enough room to get a lever in to shuffle it into place. I might be able to lift it enough
to get rollers in, though. Unfortunately I need to turn the lathe, rather than move in one direction, so rollers are limited.
cheers,
David
[Edited on 20/1/07 by David Jenkins]
|
|
907
|
posted on 20/1/07 at 04:08 PM |
|
|
Rollers go in at 45 deg.
|
|
David Jenkins
|
posted on 20/1/07 at 04:13 PM |
|
|
Smart-arse!
You're almost certainly right though...
|
|
Jon Ison
|
posted on 20/1/07 at 04:15 PM |
|
|
Know anyone with a quad ?
Ours comes in handy for pulling all sorts of things about.
It will slide on sheet steel, all we ever used in 15 years of moving heavier stuff than that about underground in tight spots.
|
|
907
|
posted on 20/1/07 at 04:20 PM |
|
|
Sorry. Only trying to help.
Six months ago we installed a 10ft x 3/8" Sedgewick folder at work.
The overhead crane is only 10 tonne so it wouldn't even look at it.
Paul G
|
|
David Jenkins
|
posted on 20/1/07 at 04:40 PM |
|
|
Ignore me Paul - just me being tactless as usual - your input IS appreciated.
I've just had a look in the garage and I do have a few bits of pipe... helping DaveFJ with a bit of machining tomorrow morning, so I might have
a tentative play in the afternoon. I'm not going to try and do it in one mad rush - it'll happen over a few days, as I try this and that,
VERY slowly and cautiously.
I like the idea of bitumin-backed carpet tiles - makes a lot of sense, so I may well try that as part of the shifting process. How many did you use
in the stack?
cheers,
David
PS: regarding the suggestions of pulling with a car or quad - the lathe is at the top end of a double-length garage, on one side. Just enough room to
swing a large cat!
[Edited on 20/1/07 by David Jenkins]
|
|
Peteff
|
posted on 20/1/07 at 04:56 PM |
|
|
Jack it up a bit and get a couple or three greased broom handles under it and use your lever to manoeuvre it when it's not got such a large
contact area with the ground.
[Edited on 20/1/07 by Peteff]
yours, Pete
I went into the RSPCA office the other day. It was so small you could hardly swing a cat in there.
|
|
907
|
posted on 20/1/07 at 05:17 PM |
|
|
Forgot to mention, the most important thing with the carpet tiles is colour co-ordination.
You'll note how the silver of the lathe blends nicely with the dark grey of the carpet backing.
The contrast of the orange pile leads the eye to the subtle shades of the concrete.
The accumulated dust gives a "well used" feeling.
Paul G
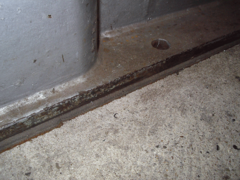 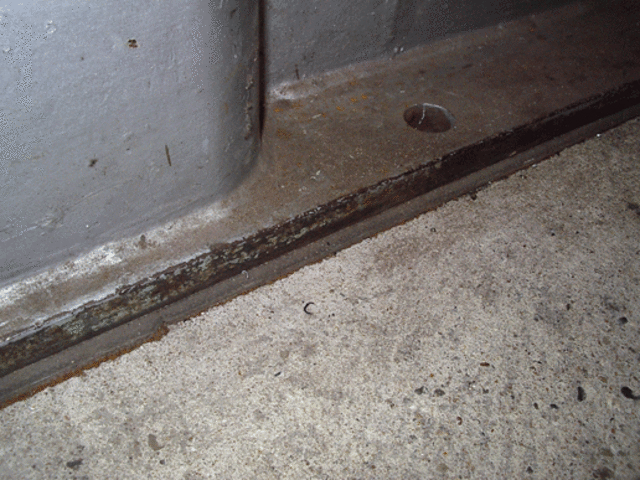 Rescued attachment IMGP1606s.gif
|
|
Peteff
|
posted on 20/1/07 at 05:25 PM |
|
|
What amazes me is that there are bolt holes in it to hold it down, as if it's going anywhere in a hurry
yours, Pete
I went into the RSPCA office the other day. It was so small you could hardly swing a cat in there.
|
|
David Jenkins
|
posted on 20/1/07 at 05:28 PM |
|
|
My lathe has bolt holes - but the manual states that they should only be used when really necessary, e.g. in a ship's workshop! Probably a good
idea, as a 1/2 ton lathe sliding around the deck doesn't sound very safe...
[Edited on 20/1/07 by David Jenkins]
|
|
DEAN C.
|
posted on 20/1/07 at 09:01 PM |
|
|
HI,I have a student as well and I have moved it a couple of times as well.
I agree with some of the other statements,I use my 1metre snap on pry bar to shuffle it and 5ft old pry bar to lift it clear to put some short
scaffold tubes under it to roll.When you lift it you need something to pivot the pry bar with to gain the height you need.
Didnt some one say:if you have a long enough lever you can move the world!
Mine needs moving back against the wall tonight as I have just moved it to gain access to the motor belts as well.
Just noticed that you have the same transwave inverter in the picture that I have,weird. Good taste though!
[Edited on 20/1/07 by DEAN C.]
Once I've finished a project why do I start another?
|
|
David Jenkins
|
posted on 20/1/07 at 10:01 PM |
|
|
quote: Originally posted by DEAN C.
Just noticed that you have the same transwave inverter in the picture that I have,weird.
Do you manage to start the lathe at the top speed? I can do it in the summer when the oil's thin, but it doesn't want to go in this cold
weather!
DJ
|
|
Browser
|
posted on 20/1/07 at 11:30 PM |
|
|
quote: Originally posted by DEAN C.
Didnt some one say:if you have a long enough lever you can move the world! [Edited on 20/1/07 by DEAN C.]
Archimedes:
"Give me a lever long enough and a place to stand and I will move the Earth". Yeah, and a rather solid fulcrum as well mate!
Reading the above makes me soooo glad all I bought was a 10" model F Atlas lathe. It might be a lot smaller and thus be able to do less stuff,
but it'll be a HELL of a lot easier to move
|
|
David Jenkins
|
posted on 22/1/07 at 04:59 PM |
|
|
Yippee! Done it!
In the end, it wasn't as hard as I thought it would be...
Using a selection of ideas from this topic, I used some levers to raise each end a centimeter or so, and slid some steel sheet under to save damaging
my concrete floor. Then I used the lever and pivot to "walk" or "row" the lathe a couple of centimeters at a time - first one end,
then the other - until it ended up where I wanted it. Took me a few hours, but I wasn't rushing - slow and safe was the plan.
Haven't managed to find some orange carpet tiles yet Paul - they do have to be orange, don't they?
cheers,
David
 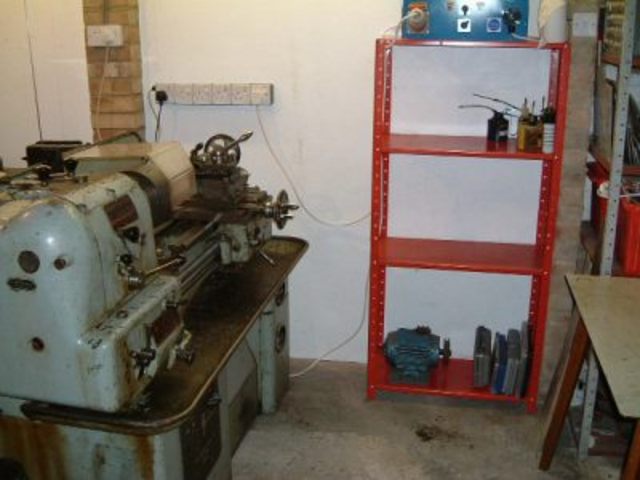 Rescued attachment DSCF0036.JPG
|
|
NS Dev
|
posted on 22/1/07 at 06:35 PM |
|
|
quote: Originally posted by David Jenkins
I'm working really hard to sort out my garage, as it's been a real tip lately, I'm running out of space and I can never find
anything. I'm doing quite well so far, with 2 new shelf units and some serious throwing out of rubbish, but I have one remaining problem.
Currently my Colchester Student lathe is backed up against the wall. Very convenient to use, but maintenance is impossible and there's a lot of
wasted wall space behind it. I want to turn it so that the tailstock end is to the wall, and the headstock goes to the middle of the garage (I have
no problem with space there).
The problem is its weight - 1400lbs, or 635Kg - which is heavier than my Locost! It was originally put in place by me, my son and the bloke who
delivered it; he had a hoist, levers and "roller skates" designed for moving heavy machinery. He also had decades of experience!
I've only got a good lever...
It's way beyond the capacity of my engine hoist, and I don't have any strong beams overhead.
Any helpful suggestions will be gratefully received. My drive belt is starting to slip so I need to get this sorted soon!
cheers,
David
Can speak from experience on this one, as I moved my Colchester Master 40" lathe 10 miles with one mate to help!
The short moving I did with a VERY big prybar, the one in the middle in this pic, from Machine Mart
you can pry the lathe up at one end with it, and shuffle it around surprisingly easily.
(we also moved my mate's 4 tonne power guillotine this way!!!! )
To move it further I pry the end up and slip scrap steel shims under it, then pry again and so on until I can get blocks under, then pry from a block
etc etc until a jack will go under then jack until bigger blocks will go under etc, one end then the other, actually doesn't take long to do.
I then use the base of a supermarket carriage thing, the things to goods are delivered to the supermarket in. I coped and widened mine so it would go
on a car trailer. I got the lathe high enough to get it under, slid it under, jacked the lathe down onto it and lightly tack welded the lathe cabinet
onto it.
Then we winched the whole lot onto a tilt bed car trailer (my mate's one) and moved it to my new house, then did the whole lot in reverse.
The final moving in the workshop was done on roll cage tubing offcuts.
its not as bad as you think it will be!
Retro RWD is the way forward...........automotive fabrication, car restoration, sheetmetal work, engine conversion
retro car restoration and tuning
|
|
NS Dev
|
posted on 22/1/07 at 06:36 PM |
|
|
ok so, I was a bit late there, but you did it the same way!
Retro RWD is the way forward...........automotive fabrication, car restoration, sheetmetal work, engine conversion
retro car restoration and tuning
|
|
NS Dev
|
posted on 22/1/07 at 06:37 PM |
|
|
ps David you don't know of any 4 jaw chucks going cheap for a roundhead do you?
Retro RWD is the way forward...........automotive fabrication, car restoration, sheetmetal work, engine conversion
retro car restoration and tuning
|
|