designer
|
posted on 16/4/11 at 06:08 PM |
|
|
Anti roll by springs.
After your thoughts that I need some sort of anti roll springs, I have added some.
[img]Forum Code:
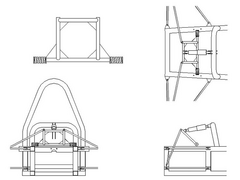 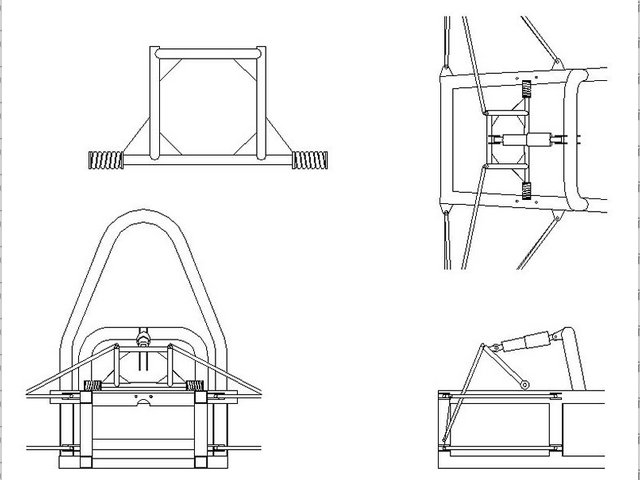 anti roll springs?
[/img]
The springs butt against the top rail mounted pillow blocks allowing the frame to float from side to side with roll.
But I don't know if there can be enough compression in the springs when mounted, if not the frame will 'clunk' from side to side.
|
|
|
v8kid
|
posted on 16/4/11 at 08:48 PM |
|
|
Belville washers
You'd be surprised how quickly the sales people at B&Q try and assist you after ignoring you for the past 15 minutes when you try and start a
chainsaw
|
|
designer
|
posted on 16/4/11 at 09:34 PM |
|
|
Don't think belville washers would work with this set-up as they cannot be pre-stressed like a spring.
|
|
britishtrident
|
posted on 17/4/11 at 11:59 AM |
|
|
One thing to watch is that when you separate roll stiffness and bump stiffness completely you also separate the damping.
In a normal setup the roll bar is damped by the main suspension damper in your setup you have zero damping in roll. What the implications of this
are beyond my barbie ( a bit like "beyond my ken" but not s sexist ;-) ).
The Beville washer idea would have at least some intrinsic damping as would rubber springs.
|
|
Sam_68
|
posted on 17/4/11 at 01:32 PM |
|
|
quote: Originally posted by britishtrident
The Beville washer idea would have at least some intrinsic damping as would rubber springs.
This is one of the reasons I'm using rubber roll springs in my similar design.
Having said which, the system is only undamped in pure roll - dive and single wheel bump movement will result in at least some damping from
compression of the main spring/damper unit. The general concensus seems to be that roll damping is less critical, because the roll loads are applied
and relaxed relatively gradually as you turn into a corner and out of it again.
With conventional systems plenty of people don't worry too much about uprating the dampers to cope with extra reaction of the ARB's, since
to do so with cheap, single-adjustable dampers means that if you make the dampers stiff enough to cope with both main springs and ARB in roll,
they'll be too stiff for the mainsprings alone, but you do hear talk of 'roll rock' where you get bounce-back from very stiff
undamped ARB's. I must admit, I've never identified this so-called 'roll rock' in any of my experience of suspension set-up,
but perhaps that's because I've always sought to minimise ARB rates, anyway.
Of course really good quality dampers allow you separate adjustment of high speed damping (to cope with the rapid deflectiions that result from road
surface imperfections) and low speed damping (to cope with the relatively slow roll movements), which allow you to isolate the ARB damping from the
road damping, anyway.
One potential problem with Belvilles (and to a lesser extent rubber springs) is that as the main rocker bridge rotates to compress the main
spring/damper, it is trying to twist the roll springs against their abutments. Designer's coil springs should accommodate this quite well, but
Bellvilles will generate a lot of frictional resistance against tehmselves and their abutments which you don't want. The designs I've seen
that use Belvilles use a roller thrust bearing at either end of the Belville stack to accomodate this rotational movement (the AXK1226/AXK1528
bearing references on the drawings, Designer), but it's an extra complication and a bit of an 'impure' solution in engineering
terms.
My design is essentially very similar to Designer's, but uses bump stop rubbers (actually polyurethane) as the roll springs and moves them
outboard of the pillow blocks. The shaft of the rocker bridge runs through the pillow blocks (using DU bearings in my case) and out though the
rubbers, which are retained by a big washer and a bolt threaded into the end of the rocker shaft. This avoids the potential problem of the sideways
'clunk' referred to by Designer, since you can easily ensure that the roll springs are slightly pre-loaded when they are assembled by
simply tightening the retaining bolts/washers down onto them.
Obviously, it's quite easy to then adjust the roll resistance by using shims between the retaining washer and the roll rubbers, which give
rising rate resistance.
|
|
dpaws
|
posted on 11/9/11 at 12:08 AM |
|
|
quote: Originally posted by Sam_68
quote: Originally posted by britishtrident
The Beville washer idea would have at least some intrinsic damping as would rubber springs.
This is one of the reasons I'm using rubber roll springs in my similar design.
Obviously, it's quite easy to then adjust the roll resistance by using shims between the retaining washer and the roll rubbers, which give
rising rate resistance.
Hi - I'd really appreciate getting in touch, it seems you have a good understanding of how the system works, I'd like to adopt something
very similar on my new build.
dpaws at hotmail dot com
Very much obliged, Steve
|
|
Sam_68
|
posted on 11/9/11 at 08:34 AM |
|
|
YHM
|
|
phelpsa
|
posted on 11/9/11 at 09:38 AM |
|
|
Using coil springs in that application could turn out to be a very expensive method. Working out exactly what roll resistance you require can be very
difficult (even more so with a trike), and mostly ends up coming down to experimentation and full scale modelling. You could go through many springs
trying to find what you're looking for.
I would be looking at moving to a system where a 'normal' style adjustable ARB provides the entire roll resistance at least then you have
a range of adjustability to play with.
|
|
Sam_68
|
posted on 11/9/11 at 09:50 AM |
|
|
quote: Originally posted by phelpsaWorking out exactly what roll resistance you require can be very difficult (even more so with a trike), and
mostly ends up coming down to experimentation and full scale modelling. You could go through many springs trying to find what you're looking
for.
I agree: this one of the main reasons that most designs use belville stacks (you can quickly and cheaply vary roll resistance by altering the stacks)
and why I'm going for rubber (the rising rate allows you to do the same thing by means of preload).
quote: Originally posted by phelpsaI would be looking at moving to a system where a 'normal' style adjustable ARB provides the
entire roll resistance at least then you have a range of adjustability to play with.
I'd strongly urge against this: you're abandoning one of the main advantages of the 'traditional' monoshock arrangement (that
the anti-roll function works the other way round to a 'traditional' ARB, in that a bump at one side forces the other opposite wheel
down against the tarmac, increasing its load/grip, instead of trying to pick it up). All traditional ARB's are a compromise, and
particularly with a trike monoshock - where the ARB would need to be stiff enough to provide all the roll resistance for the whole vehicle -
this arrangement would be a bad idea.
[Edited on 11/9/11 by Sam_68]
|
|
phelpsa
|
posted on 11/9/11 at 10:12 AM |
|
|
quote: Originally posted by Sam_68
quote: Originally posted by phelpsaWorking out exactly what roll resistance you require can be very difficult (even more so with a trike), and
mostly ends up coming down to experimentation and full scale modelling. You could go through many springs trying to find what you're looking
for.
I agree: this one of the main reasons that most designs use belville stacks (you can quickly and cheaply vary roll resistance by altering the stacks)
and why I'm going for rubber (the rising rate allows you to do the same thing by means of preload).
quote: Originally posted by phelpsaI would be looking at moving to a system where a 'normal' style adjustable ARB provides the
entire roll resistance at least then you have a range of adjustability to play with.
I'd strongly urge against this: you're abandoning one of the main advantages of the 'traditional' monoshock arrangement (that
the anti-roll function works the other way round to a 'traditional' ARB, in that a bump at one side forces the other opposite wheel
down against the tarmac, increasing its load/grip, instead of trying to pick it up). All traditional ARB's are a compromise, and
particularly with a trike monoshock - where the ARB would need to be stiff enough to provide all the roll resistance for the whole vehicle -
this arrangement would be a bad idea.
[Edited on 11/9/11 by Sam_68]
This may be true (depending on what roll and heave rates you end up with), but it still works. Its going to be a compromised design whichever way you
go, my suggestion is that the conventional ARB might turn out to be an easier system to get right.
|
|
Sam_68
|
posted on 11/9/11 at 01:01 PM |
|
|
quote: Originally posted by phelpsaIts going to be a compromised design whichever way you go, my suggestion is that the conventional ARB might
turn out to be an easier system to get right.
I'd suggest that the 'shuttle' type arrangement used by monoshock systems to give roll resistance is less compromised than a
conventional ARB, though, for the reason explained above: using a torsion bar stiff enough to provide all the vehicle's roll resistance,
in such a way that it tries to lift the opposite wheel off the ground in single wheel bump is not going to do much good in terms of available grip.
Belville stacks are just as easily and repeatably adjustable as a conventional ARB, I think. Using shimmed rubbers is certainly a bit more
complicated, but the prospect of rising rate roll resistance offers some interesting opportunities.
|
|
phelpsa
|
posted on 11/9/11 at 01:12 PM |
|
|
quote: Originally posted by Sam_68
quote: Originally posted by phelpsaIts going to be a compromised design whichever way you go, my suggestion is that the conventional ARB might
turn out to be an easier system to get right.
I'd suggest that the 'shuttle' type arrangement used by monoshock systems to give roll resistance is less compromised than a
conventional ARB, though, for the reason explained above: using a torsion bar stiff enough to provide all the vehicle's roll resistance,
in such a way that it tries to lift the opposite wheel off the ground in single wheel bump is not going to do much good in terms of available grip.
Belville stacks are just as easily and repeatably adjustable as a conventional ARB, I think. Using shimmed rubbers is certainly a bit more
complicated, but the prospect of rising rate roll resistance offers some interesting opportunities.
Again, it really does depend on what roll and heave stiffness you intend to run. The least compromising of competition cars run torsion bars supplying
all the roll stiffness, so that says something.
|
|
Sam_68
|
posted on 11/9/11 at 01:40 PM |
|
|
quote: Originally posted by phelpsa The least compromising of competition cars run torsion bars supplying all the roll stiffness, so that says
something.
Which would those be, then?
Conventional ARB's always degrade grip... the stiffer they arew, the more they degrade the grip. I can't imagine any situation
where very stiff ARB's would be beneficial, if an alternative system can be used to avoid them.
Enlighten me?
[Edited on 11/9/11 by Sam_68]
|
|
phelpsa
|
posted on 11/9/11 at 02:04 PM |
|
|
quote: Originally posted by Sam_68
quote: Originally posted by phelpsa The least compromising of competition cars run torsion bars supplying all the roll stiffness, so that says
something.
Which would those be, then?
Conventional ARB's always degrade grip... the stiffer they arew, the more they degrade the grip. I can't imagine any situation
where very stiff ARB's would be beneficial, if an alternative system can be used to avoid them.
Enlighten me?
[Edited on 11/9/11 by Sam_68]
They are commonly used in F1 as the friction in the system is reduced, keeping damping in the dampers where it can be controlled properly.
Your system will place a force on the opposite wheel through the heave side of the system where a torsion bar system will transfer it through the roll
side and hence will reduce grip in a similar manner. It is not a particularly big advantage.
|
|
Sam_68
|
posted on 11/9/11 at 02:25 PM |
|
|
quote: Originally posted by phelpsaThey are commonly used in F1 as the friction in the system is reduced, keeping damping in the dampers where
it can be controlled properly.
Do you have any pictures? I am not aware of any F1 system where conventional torsion bar ARB's provide all of the roll resistance on the
car? Separate torsion bars for pitch/heave and roll, certainly, but that's a different thing entirely.
quote: Originally posted by phelpsa
Your system will place a force on the opposite wheel through the heave side of the system where a torsion bar system will transfer it through the roll
side and hence will reduce grip in a similar manner. It is not a particularly big advantage.
It's not 'my' system; it's the system used by all successful monoshock arrangements I've encountered.
The difference, as I've tried to explain previously, is that a shuttle type arrangement will transfer the force of a single wheel bump across
the car in such a way that it presses the opposite wheel harder against the ground, tending to increase grip at that wheel, whereas a
conventional ARB will transfer the force of a single wheel bump in such a way that it tries to lift the opposite wheel up off the tarmac,
reducing grip.
In all mechanical (non-active) systems I've come across, single wheel bump is partly reacted by the roll mode and partly through
pitch/heave mode... that you can't isolate the two is the great, unresolveable limitation of all non-active systems.
|
|
phelpsa
|
posted on 11/9/11 at 02:46 PM |
|
|
quote: Originally posted by Sam_68
quote: Originally posted by phelpsaThey are commonly used in F1 as the friction in the system is reduced, keeping damping in the dampers where
it can be controlled properly.
Do you have any pictures? I am not aware of any F1 system where conventional torsion bar ARB's provide all of the roll resistance on the
car? Separate torsion bars for pitch/heave and roll, certainly, but that's a different thing entirely.
quote: Originally posted by phelpsa
Your system will place a force on the opposite wheel through the heave side of the system where a torsion bar system will transfer it through the roll
side and hence will reduce grip in a similar manner. It is not a particularly big advantage.
It's not 'my' system; it's the system used by all successful monoshock arrangements I've encountered.
The difference, as I've tried to explain previously, is that a shuttle type arrangement will transfer the force of a single wheel bump across
the car in such a way that it presses the opposite wheel harder against the ground, tending to increase grip at that wheel, whereas a
conventional ARB will transfer the force of a single wheel bump in such a way that it tries to lift the opposite wheel up off the tarmac,
reducing grip.
In all mechanical (non-active) systems I've come across, single wheel bump is partly reacted by the roll mode and partly through
pitch/heave mode... that you can't isolate the two is the great, unresolveable limitation of all non-active systems.
I can't go into too much detail on the F1 front sorry, you're just gonna have to trust me on this one.
I know its not your system, i've been involved in manufacturing, setting up and running that system previously, hence I am very much in tune
with the positives and negatives.
In the shuttle system the heave mode transfers a lifting force onto the opposite wheel rather than the roll. With the torsion anti roll system the
heave side 'presses' the opposite wheel into the floor. As you have already pointed out, it is a combination of the two that will dictate
what load is placed on the opposite wheel, and therefore it depends on your heave and roll rates.
I still maintain the the separate torsion bar method will prove much easier to set up correctly.
|
|
Sam_68
|
posted on 11/9/11 at 03:02 PM |
|
|
quote: Originally posted by phelpsa I can't go into too much detail on the F1 front sorry, you're just gonna have to trust me on
this one.
Sorry, I don't trust anyone or anything without evidence to back up their assertions. I'm agnostic. quote: Originally posted by
phelpsa In the shuttle system the heave mode transfers a lifting force onto the opposite wheel rather than the roll.
Yes, that I understand and accept.
quote: Originally posted by phelpsa With the torsion anti roll system the heave side 'presses' the opposite wheel into the
floor.
This I don't understand. We're talking about a monoshock system, but using a free-floating (instead of belville sprung) shuttle (or
similar mechanism to allow lateral deflection of the pushrod pickups) to permit roll movement, but then providing roll resistance separately by means
of a conventional ARB?
In this case, the heave element reacting a single wheel bump would still be trying to lift the other wheel (ie. the pushrod at the bump side
will, via the rocker, be trying to compress the monoshock and lift the other wheel from the tarmac)?
quote: Originally posted by phelpsa I still maintain the the separate torsion bar method will prove much easier to set up correctly.
Can you explain why everyone uses belvilles, then?
[Edited on 11/9/11 by Sam_68]
|
|
phelpsa
|
posted on 11/9/11 at 03:10 PM |
|
|
We appear to have got our wires crossed here. I'm talking about a system where the spring and damper act across the two sides like so... (the
only pictures I could find).
The ARB then takes over all roll resistance.
|
|
phelpsa
|
posted on 11/9/11 at 03:14 PM |
|
|
quote: Originally posted by Sam_68
quote: Originally posted by phelpsa I still maintain the the separate torsion bar method will prove much easier to set up correctly.
Can you explain why everyone uses belvilles, then?
[Edited on 11/9/11 by Sam_68]
Yes. It is a much lighter and simpler when were are ultimately looking for almost 100% roll stiffness which is inevitably how almost all of those
systems end up. Have a read up on David Gould's explanations to understand that.
With this setup on a trike you definitely won't be looking for anywhere near 100% roll stiffness.
|
|
Sam_68
|
posted on 11/9/11 at 03:20 PM |
|
|
Ah, I thought we were still talking about the 'conventional' (at the front) monoshock arrangement posted by Designer at the top of this
thread.
In fairness, you did say:
quote: Using coil springs in that application....
(my bold)
I've used the 'transverse' monoshock arrangement you picture at the rear, where negligible roll resistance is required, but I
wouldn't entertain it at the front, with all roll resistance being provided by a conventional (torsion) ARB.
I don't know of any instances where it has been so used, do you?
[Edited on 11/9/11 by Sam_68]
|
|
phelpsa
|
posted on 11/9/11 at 03:27 PM |
|
|
quote: Originally posted by Sam_68
Ah, I thought we were still talking about the 'conventional' (at the front) monoshock arrangement posted by Designer at the top of this
thread.
In fairness, you did say:
[quote=phelpsa]Using coil springs in that application could turn out to be a very expensive method. Working out exactly what roll resistance
you require can be very difficult (even more so with a trike), and mostly ends up coming down to experimentation and full scale modelling. You could
go through many springs trying to find what you're looking for.
I would be looking at moving to a system where a 'normal' style adjustable ARB provides the entire roll resistance at least then you have
a range of adjustability to play with.
(my bold)
I've used the 'transverse' monoshock arrangement you picture at the rear, where negligible roll resistance is required, but I
wouldn't entertain it at the front, with all roll resistance being provided by a conventional (torsion) ARB.
I don't know of any instances where it has been so used, do you?
Sorry, I had ideas running round in my head and failed to actually write them in the post... oops!
Yes, I used to have quite a few pictures of a couple of hillclimb single seaters running it. IIRC Allan Staniforths terrapin ran this system for a
while to good effect.
It all comes down to what heave and roll rates he wishes to run. The fact he wished to use coil springs there gave me the impression that he wished to
have a reasonable low roll rate, as I would have thought of a road going trike.
|
|
phelpsa
|
posted on 11/9/11 at 03:30 PM |
|
|
Here's the setup on the front of a trike:
|
|
Sam_68
|
posted on 11/9/11 at 03:34 PM |
|
|
quote: Originally posted by phelpsaYes, I used to have quite a few pictures of a couple of hillclimb single seaters running it. IIRC Allan
Staniforths terrapin ran this system for a while to good effect.
At the front?! I don't recall that, and I spent a fair amount of time lurking round the paddock at Harewood bothering Mr Staniforth with stupid
questions when I was younger (and debating with him when I started to get the hang of it myself!).
All of Allan's cars, upto and including his final Megapin, were conventional dual spring/shock arrangements, I thought?
If you have pictures, I'd be most interested.
|
|
phelpsa
|
posted on 11/9/11 at 03:34 PM |
|
|
Here's another interesting setup, transverse monoshock with a damper anti roll torsion bar.
Wonder if it was ever built!
|
|
Sam_68
|
posted on 11/9/11 at 03:43 PM |
|
|
quote: Originally posted by phelpsa
Here's the setup on the front of a trike:
Interesting; I assume there's a small ARB 'driven' by secondary puchrods off the rockers, hidden in that photo?
Did it work?
And what's the engine... I thought it was a BMW motorcycle engine at first glance, until I counted the cylinders!
quote: Originally posted by phelpsaHere's another interesting setup, transverse monoshock with a damper anti roll torsion bar.
No immediately obvious and simple way to adjust the roll stiffness on that one, though, except perhaps to vary the distance between the ARB pushrods
and the centre of the torsion bush?
Looks rather overcomplicated, too, which defeats one of the main reasons I'd want to use a monoshock (weight).
|
|