C10CoryM
|
posted on 23/4/08 at 08:36 PM |
|
|
Pushrod ratio calculation help
Hey guys,
Playing with my front suspension and need some help. Some basic specs (some assumptions) are:
1800lbs total weight with driver (ya, ya, I know. Heavy)
50/50 F/R weight.
Push rod F suspension.
Bike shocks. 525lb/inch. 2" of shock travel before bump stop.
Required wheel travel 4" total.
18" lower control arm (push rod at 15" from pivot).
push rod at 40 degrees from vertical
So, lets say 450lb corner weight, 225lb desired wheel weight (estimated freq is 120cpm).
wheel rate * (ratio of push rod angle * ratio of control arm leverage)
225*(1.32*1.2) = 356
So 356lbs at the rocker, with 525lbs on the other end is a 1.5:1 ratio.
Firstly, did I get that right?
And second, if that is right that means that I only get a little over 3.5" total wheel travel which is not enough. I need at least 4"
with more preferred. If I run a rocker ratio of 2:1 I will get my wheel travel, but will require a 712lb spring.
So, you guys think I should just build a rocker at 2:1 and see what happens?
Or did I miss something and those numbers are pointless .
Thanks for any help.
Cory
"Our watchword evermore shall be: The Maple Leaf Forever!"
|
|
|
C10CoryM
|
posted on 23/4/08 at 08:41 PM |
|
|
Here is a pic of things somewhat layed out just because people like pictures . Bottom coil over point is not fixed, but thats probably where it
will end up.
Cheers.
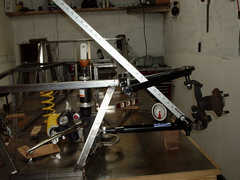 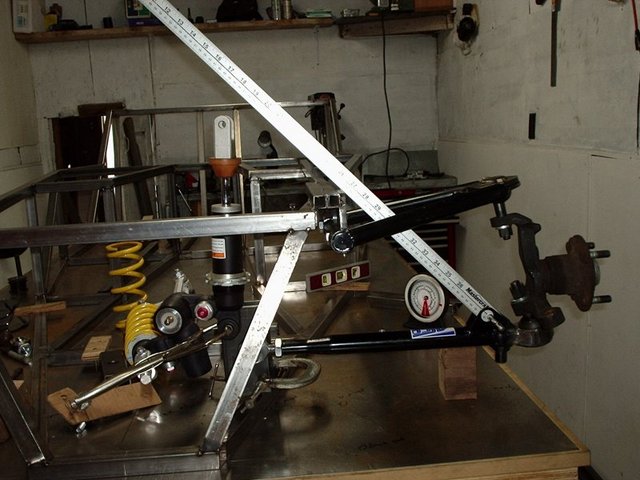 Rescued attachment coil.jpg
"Our watchword evermore shall be: The Maple Leaf Forever!"
|
|
Schrodinger
|
posted on 23/4/08 at 08:51 PM |
|
|
I must say that I can't see how your suspension rocker/push rod is going to work. I'm not saying anything is wrong just that I can't
see it.
Keith
Aviemore
|
|
C10CoryM
|
posted on 23/4/08 at 09:00 PM |
|
|
Fine, apparently people don't like pictures
I suppose it isn't very clear though.
Try this lovely doodle instead.
Green are pivots
Blue is rocker
Yellow is rocker to frame bracket
Brown is pushrod.
Obviously things arent lined up yet.
Cheers.
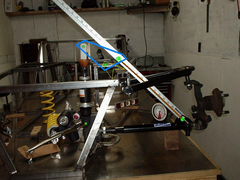 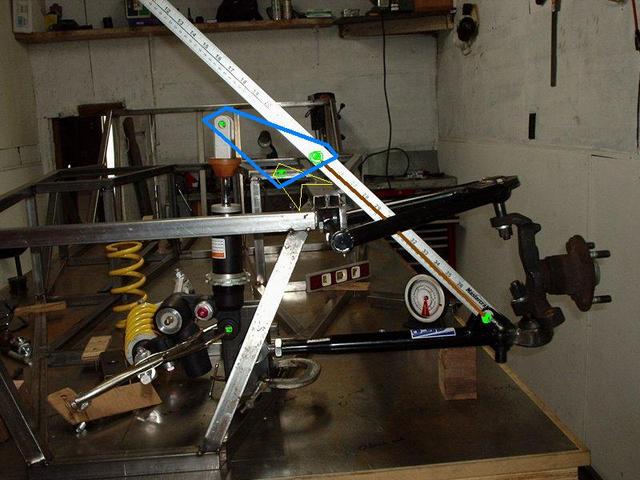 Rescued attachment coiled.JPG
"Our watchword evermore shall be: The Maple Leaf Forever!"
|
|
nitram38
|
posted on 23/4/08 at 09:14 PM |
|
|
You are confusing weight and shock travel to start with.
You need to treat them as two different entities.
For the shock travel to work, the wheel has to move up and down max 4" and the shock 2", is that right?
If so you need a cam ratio of 2:1.
The cam ratio will affect your spring rates as by the levarage priciple you have changed the loading.
If you use a 2:1 on the cam then likewise the spring rates will be a 2:1 ratio.
My best advice is to build your car with the correct shock travel and replace your shocks with a solid rod.
Make adjustable pushrods to adjust your ride height.
When you have finished the car, add all your planned weight etc and then borrow a corner weight gauge and measure each wheel.
Using the 2:1 ratio, you can then calculate your spring rates. You should also allow a bit more for the springs to soften and this will come down to
your own best guess.
You will probably end up changing the springs after driving the car, but at £25 a pair it is not a big deal.
I am on my second pushrod inboard car so I have a little bit of experience, but I prefer standard car coil over shocks for my car because I can
adjust the shock rates. You might find bike shocks are far too soft for your car, but I might be wrong.
[Edited on 23/4/2008 by nitram38]
|
|
82 Locost
|
posted on 23/4/08 at 09:32 PM |
|
|
Make it simple for future adjustment. Allow sufficient adjustment (mounting points) to adjust from anywhere between 1:1 and 2:1 and you'll
always be happy.
|
|
Tralfaz
|
posted on 23/4/08 at 11:49 PM |
|
|
I think he is trying to design a system that uses the bike shocks WITH the original bike springs.
While I agree with the majority of the cautions expressed that if you use bike shocks you need to consider the fact that the valving is set for a
certain rate spring, I also think that they may well perform acceptably with a somewhat lighter spring.
In other words they might be ideal at 525 but still quite decent at say 425-450, just not 200.
Given that a bikes overall weight can fluctuate wildly depending on the weight of the rider and or passenger the rates/frequency must have some
flexibility.
Or am I stupid?
|
|
leto
|
posted on 24/4/08 at 05:55 AM |
|
|
To make nitram38's post a little more specific. 2:1 in in travel ratio makes 1:2 in force ratio. So your 450 lbs in corner weight will be 900
lbs at the spring. With ride hight at half the shock's travel (=1”), spring rate so support the car will be 900 lbs/inch.
Edit:
And you have to take account of the angles at the rocker arm in your calculations too.
[Edited on 08-4-24 by leto]
“I'm gonna ride around in style
I'm gonna drive everybody wild
'Cause I'll have the only one there is a round”. (J. Cash)
|
|
britishtrident
|
posted on 24/4/08 at 06:54 AM |
|
|
To put it another way you have to multiply the desired wheel rate by the square of the motion ratio to find the required spring rate.
Think of it it terms of the energy stored in the spring.
Energy = force x distance
Inboard shocks are hassle for nothing only real advantage is aerodynamic
[Edited on 24/4/08 by britishtrident]
|
|
nitram38
|
posted on 24/4/08 at 07:36 AM |
|
|
Not always for aerodynamics.
I have air spring suspension on the MotaLeira and I need to adjust ride height in a 6" range whereas the shocks only have a 3" working
range.
A 2:1 cam will give me more.
|
|
MikeCapon
|
posted on 24/4/08 at 08:34 AM |
|
|
Morning all,
There seems to be a bit of confusion regarding wheel rates, ratios and spring rates.
Firstly wheel rate is not simply the weight on that corner. It is the resistance to movement seen at the wheel. For example a wheel rate of 150 lbs/in
means that if a weight of 150lbs is added to the corner (in roll or braking for example) the wheel will move one inch.
The ratio is simply the wheel movement divided by the shock movement. So a 4" wheel movement giving a 2" shock movement is a 2:1 ratio.
The angles of shocks/pushrods etc are not needed for this calculation.
The spring rate is also expressed in lbs/in (or kg/mm for those who like me enjoy keeping things simple) and a 525 lbs/in spring will compress one
inch when a weight of 525lbs is placed on it.
As for the calculation of a spring rate from a wheel rate the formula is:
Wheel rate X ratio² = spring rate
With the above numbers: 150 x 2 x 2 = 600lbs/in
This last bit can be difficult to get your head around as the most people imagine that it is just the wheel rate x the ratio.
Going back to the same example with a weight of 150lbs applied to the corner the wheel will move one inch. The rocker at the shock attachment point
will double the 150lbs to 300lbs. But at the same time the shock will only close by half an inch. So force 300lbs over half an inch of movement = 600
lbs/in.
Suspension systems with rockers of this type have a number of advantages. Aerodynamics, the ability to have a progessive movement (that is a softer
wheel rate at first getting harder towards full bump), packaging or the ability to put the shocks where we want them to be, choice of ratio and hence
piston speed, possibility of swapping rockers to very quickly change ratios/progression etc. That's probably not all of the advantages but as
you can see most of these are only of interest to racecar types.
For a Locost they are certainly not the most practical option but they do have a maximum of racecar bling about them! If you want to be practical
maybe you'd be driving a Sierra anyway 
www.shock-factory.co.uk
|
|
Fred W B
|
posted on 24/4/08 at 09:07 AM |
|
|
Good discussion re spring rates in this thread
rate thread
Cheers
Fred W B
You can do it quickly. You can do it cheap. You can do it right. – Pick any two.
|
|
C10CoryM
|
posted on 25/4/08 at 02:09 AM |
|
|
Thanks for the input guys.
The reason I am looking into this setup is because it gives me a 3x adjustable shock for about 1/10th the cost of the equivelant car shock. If things
aren't going to work, I may as well spend the money on some good shocks. Either way, I want to know what my options are. I need the 4"
of wheel travel so to use these shocks, I need a 2:1 cam. If I use a 2:1 cam it reduces my effective wheel rate which is why I was mentioning both at
the same time.
Mike, Any idea why it is squared? And do you square the overall ratio (including arm leverage, shock angle etc) or just the rocker ratio?
I believe you are correct, but it seems strange to me as it means the little formula cars here are running 1000lb+ springs. Seems odd.
Either way Im tempted to just build a 2:1 rocker, and reduce my coilover angle as much as possible and deal with it from there. I do intend to run a
softer setup, with a swaybar VS just stiffer springs. Just had not intended to be that soft. [edit] also had not intended for my car to be so heavy
either . I just couldn't resist more power though!
Thanks again.
Cory
[Edited on 25/4/08 by C10CoryM]
"Our watchword evermore shall be: The Maple Leaf Forever!"
|
|
MikeCapon
|
posted on 25/4/08 at 12:57 PM |
|
|
Hi Cory,
Yes I am sure that the ratio is squared and that is the ratio of wheel movement to shock movement.
Do not try and separate the various components in your calculations. All you are worried about is what the shock sees/feels as a result of what the
wheel sees/feels. Of course the angle of the pushrod has an influence as does all the geometry of your linkage system but finally all you need to know
is x mm of wheel movement = y mm of shock movement.
I did try and explain why the ratio is squared in my last post. Here's another example.
Firstly the wheelrate. This is expressed in lbs per inch. For example 120 lbs per inch. This means that if that corner of the car is loaded by 120 lbs
it will descend one inch.
Now the ratio. For example 3:1. This means that if the wheel moves 3 inches, the shock will move one inch.
Now if 120 lbs is loaded onto the corner of the car the car will drop (or the wheel will rise if you like) by one inch.
The ratio being 3:1 means that the force of 120 lbs is multiplied by 3. (3 X 120 = 360 lbs).
At the same time the one inch of wheel movement is reduced by a factor of three. In other words the shock will close one third of an inch.
As a result, you have a force of 360lbs for one third of an inch of movement. So, the spring rate expressed in lbs per inch will be 3 times the force
of 360 lbs. (3 x 360 = 1080 lbs per inch)
So wheelrate (120 lbs/in) X ratio (3:1) squared. 120 x 3 x 3 = 1080 lbs/in.
As for the single seaters you mention what makes you think they are running 1000 lb/in springs? It's possible they are! Ground effect F1 cars
were running springs in the 5-6000 lbs/in bracket! Their tyres were more compliant than their shocks. Also some single seaters run some odd ratios.
Often, the shock movement is greater than the wheel movement. This was to have enough shock movement to create reasonable damping with very small
wheel movements.
Have you checked out the spreadsheet in the link Fred gave you? By playing around with the numbers in the input boxes you should be able to determine
a ratio to get your bike shocks to work. Just make sure you put the entire shock stroke including the bumpstop. They do compress you know!
A last bit of advice. Do not make anything yet, at least not out of metal! Make a wooden or even stiff card rocker to make sure of your numbers before
you make the final items.
Cheers + good luck,
Mike
www.shock-factory.co.uk
|
|
C10CoryM
|
posted on 26/4/08 at 02:08 AM |
|
|
Thanks for that Mike. I'm on the same page now (finally ).
We will see where I bumble along to. I'm starting to get the feeling I'm going to do it the right way and wait until I have the car
complete before picking shocks. Probably won't include rocker arms if that's the case.
Thanks again guys.
Cory
"Our watchword evermore shall be: The Maple Leaf Forever!"
|
|