Julian B
|
posted on 23/6/03 at 04:35 PM |
|
|
De-Deon How to?
Hi all
I wonder if anyone can shed some light on how to construct a De-Deon back axle assembly using a sierra diff or maybe even a Rover SD1 LSD. I have seen
various post regarding this system but none that show a fool like me how to go about the construction and the materials one might require.
Thanks again in advance
Julian Brewer
|
|
|
Julian B
|
posted on 25/6/03 at 08:41 AM |
|
|
Well i have had a think about this and sketched a fag packet drawing. Is this in essence a de deon system. I take that it will still require a pan
hard rod at one side but would you think only one is required?
With reference to the de deon tube itself has anyone any idea on the material type and sizes.
Thanks again
Julian Brewer

|
|
Alan B
|
posted on 25/6/03 at 11:49 AM |
|
|
Julian, that is a good representation of a DeDion system.....other than the fact (as you say) you need some some lateral loctation......panhard rod
typically...
Without out any sideways location the axle can float left and right by using up the the spare travel on the splines (not good.. )
Typically I've seen De Dion tubes around 2.5"/3" x 16g...in regular mild steel tube......maybe someone can measure one...?
HTH,
Alan
|
|
Noodle
|
posted on 25/6/03 at 12:00 PM |
|
|
Check this out. The P6's De-dion setup.
http://forum.locostbuilders.co.uk/xmb/photos/cgi-bin/showpic.pl?p6_de_dion.jpg
I (used to) have some pictures of the setup used by MK Engineering somewhere. I can dig them out if you want.
ATB
Neil.
|
|
craig1410
|
posted on 25/6/03 at 12:12 PM |
|
|
Hi,
Check out my website for pictures of my MK engineering based de-dion setup. I think the de-dion tube is 50mm with a 2.5mm wall as someone else asked
me to measure it. I will check tonight for you. I also use a panhard rod bolted to a double shear bracket welded to the back of one of the de-dion
"ears". I think it is an excellent setup and would be happy to provide any dimensions or photographs (I have a digi camera) or advice that
anyone would like. Just ask and it shall be done!!
I think that more people should use de-dion as it is a very simple way to convert a live axle car to use Sierra rear running gear. All you need is a
pipe bender and a few bits of metal cut from a pattern and welded to form the ears and hub carrier mounts. Much easier than IRS and with equally good
handling qualities and better traction by all accounts.
You can also make it to suit any width of car by simply extending the de-dion tube which would make it very flexible for those using wider
chassis'
Hope this helps,
Craig.
|
|
Julian B
|
posted on 25/6/03 at 01:25 PM |
|
|
Thanks guys for the information and i would be very grateful if you could send me as many pics of the De deon that you all have to hand.
I have yet to take my v8 sd1 to bits and i don’t know if i can utilise the rear diff but i hope its possible. I don’t think its the same as the older
p6 but i am hoping it is a lsd diff.
Thanks again for all the help
Julian Brewer
Email Julian@fsdv3.com
|
|
andyps
|
posted on 25/6/03 at 09:24 PM |
|
|
Does anybody have pictures/drawings of the de-dion system used by cat..ham? That would surely provide a useful starting point.
Andy
An expert is someone who knows more and more about less and less
|
|
sgraber
|
posted on 3/7/03 at 09:14 PM |
|
|
Although my build is mid engine, I fabricated a deDion systyem that may give you some ideas. I used 3" round 16ga with a single bend at the
center to clear the diff. Check out the 'Engine Cradle' link in the Gallery section of my website.
I am in the process of converting from Panhard bar into a Watts Link. But the website still shows the Panhard bar.
Graber
This post should have a 'www' button at the bottom.
Steve Graber
http://www.grabercars.com/
"Quickness through lightness"
|
|
Crowley
|
posted on 3/7/03 at 09:25 PM |
|
|
De Dion
Can anyone help with drawings, pictures details on the de dion rear end. I'd like to get my head round it, but haven't really seen a
decent picture or drawing. 
|
|
craig1410
|
posted on 3/7/03 at 09:27 PM |
|
|
Steve,
I'm curious, why go for the watts link instead of the ubiquitous panhard rod? I'm not trying to be funny or anything btw, I'm
genuinely curious what the differences are?
One other thing, how do you use a watts link when the diff is fixed to the chassis and not to the live axle. I've never seen a watts link on a
non-live axle car. Have I missed something?
Cheers,
Craig.
|
|
blueshift
|
posted on 3/7/03 at 10:02 PM |
|
|
Ah cool, someone's asking the de-dion questions. I was going to get in touch with you soon craig, and pick your brains..
if you can send pictures, dimensions etc my way as well, that would be great.
my co-builder and I are working on a CAD model of a mcsorley 7+4 with dedion, cymtriks mods to take a rover v8, in consultation with jim mcsorley. now
seems as good a time as any to start figuring out the dedion
rather than hijack this thread I will start another about diffs..
|
|
sgraber
|
posted on 3/7/03 at 10:07 PM |
|
|
Crowley, I have tons of photos on my website. It functions like a live axle, but the diff is bolted to the frame.
Craig, Actually, I would have simply kept the Panhard had the dang thing not been going across the only place I could route the stock exhaust for my
transverse mid-engine. It was either fabricate a completely custom exhaust header or use a watts link.
I am very, very close to finishing the Watts Link. I promise to post some photos of how it attaches to the DeDion and to the frame.
 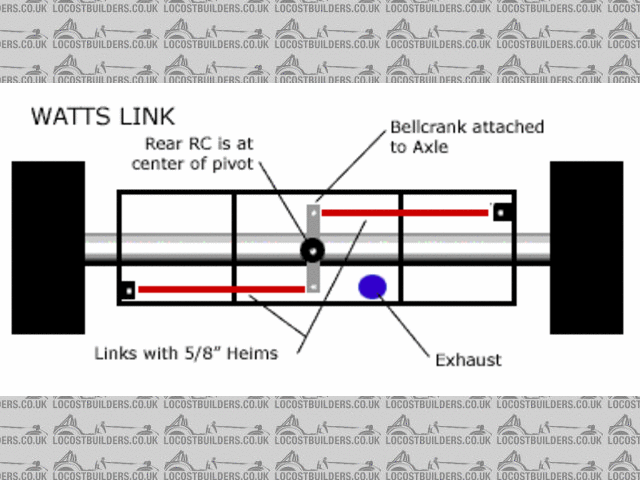 Rescued attachment WattsLinkBala.gif
Steve Graber
http://www.grabercars.com/
"Quickness through lightness"
|
|
Spyderman
|
posted on 3/7/03 at 10:09 PM |
|
|
There has been a lot of discussion about various rear axle locating on http://autos.groups.yahoo.com/group/Locost_Theory/
Have a look. There are some useful discussion and links.
Terry

Spyderman
|
|
craig1410
|
posted on 3/7/03 at 10:13 PM |
|
|
Steve,
That makes sense now.
Of course you can attach the watts pivot to the de-dion tube itself... Doh!
Thanks for the diagram.
Craig.
|
|
paulf
|
posted on 4/7/03 at 09:36 PM |
|
|
The SD1 has a live axle located by a watts link and torque tube.The axle would be to wide and is also rather heavy, I had an SD1 and it did handle
very well for the size of the car but i dont think any of the rear end could easily be used in a Locost.
Paul.
quote: Originally posted by Julian B
I have yet to take my v8 sd1 to bits and i don’t know if i can utilise the rear diff but i hope its possible. I don’t think its the same as the older
p6 but i am hoping it is a lsd diff.
Thanks again for all the help
Julian Brewer
Email Julian@fsdv3.com
|
|
sgraber
|
posted on 7/7/03 at 08:29 PM |
|
|
Photo of my Just finished Watts Link/deDion
I mentioned earlier in this thread that I would post a photo of the Watts link I am building. Well, it's finished. I have posted many more
photos of it on my website. Go to the Diary and follow the link off the latest entry dated 7-7-03
Graber
You may note that my deDion tube is 3" 16ga.
[Edited on 7/8/03 by sgraber]
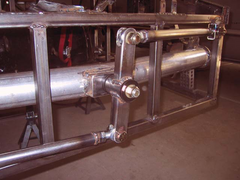 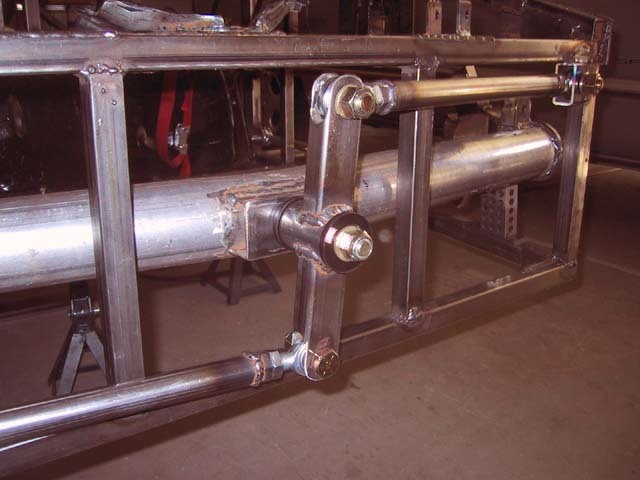 Rescued attachment Bala07-07-03 009.jpg
Steve Graber
http://www.grabercars.com/
"Quickness through lightness"
|
|
cymtriks
|
posted on 8/7/03 at 09:59 PM |
|
|
Deon tube sizes
I would not advise using less than 2.5 inch diameter or less than 2mm/14 gauge wall thickness for the tube.
I have measured a Caterham tube OD and it is 2.5 inches.
For a Deon tube resistance to bending is much more important than axial stress so diameter is more important than the cross sectional area of metal
For a 20000inchlb bending torque the stresses are-
2.0-16g 109500psi
2.0-14g 89800psi
2.0-12g 74000psi
2.0-10g 61500psi
2.5-16g 68800psi
2.5-14g 56100psi
2.5-12g 46000psi
2.5-10g 37900psi
3.0-16g 47100psi
3.0-14g 38300psi
3.0-12g 31300psi
3.0-10g 25700psi
As poor steel yeilds at about 50000psi and decent steel at about 70000psi I'D advise chrome moly for the tube as oppose to any old stuff.
The 20000inchlb moment is a guess at what the maximum might be. It is down to you to determine if this suits your car as this is getting a bit like
guess work. How big is a pothole or a bump?
I seriously doubt if most kit makers even think as far as the above calcs. Some kit parts I've seen look as if they were just made up on the day
without any real thought at all. I would advise that you copy the competition with care!
|
|
craig1410
|
posted on 8/7/03 at 10:49 PM |
|
|
Cymtriks,
Any chance of a diagram 'cause I'm having trouble visualising the force vectors and moments. My de-dion system designed by MK Eng uses
2" 2.5mm wall tubing and "intuitively" it looks sturdy enough for the application. I am wondering if stress depends on where your
springs are attached and the distance between the axle centre and de-dion tube centre.
I'm not doubting your figures but I find it hard to visualise without further info.
Cheers,
Craig.
|
|
Alan B
|
posted on 9/7/03 at 01:21 AM |
|
|
Cymtriks,
A few points/questions...
1 - Where did you get the 2000 inlb bending moment figure from? I don't dispute your stress figures...I'd just like to know why you chose
2000 inlb
2 - I agree about the stiffness (resistance to bending) being more important....so why suggest Chromoly? when it's stiffness is similar to mild
steel......I can't imagine anyone (other than a racer) having a chromoly DeDion tube...
BTW, I'm just trying promote further discussion and understanding, not nit-picking or anything..... 
|
|
Alan B
|
posted on 9/7/03 at 01:25 AM |
|
|
Ooops sorry, I see you did explain the 2000 figure ......
|
|
Rorty
|
posted on 9/7/03 at 01:58 AM |
|
|
I agree with Alan. The diference in stiffness between MS and CroMo wouldn't warrant the use of CroMo in this situation, never mind the
additional hassles of cost/welding.
I've made deDion tubes from 57.2mm X 2mm ( 2 1/4" X .078" ) MS tube, for cars weighing around 1100kg, and believe me, they saw some
severe abuse.
On a slightly different tack, I've also made perfectly good ARBs from plain old ERW tube too.
I don't dispute your figures either, I just have a good handle on what works and what doesn't.
Anyone care to chop up a Rover (or a more similarly weighted car to a sevenesque) deDion tube for a comparrison?
Cheers, Rorty.
"Faster than a speeding Pullet".
PLEASE DON'T U2U ME IF YOU WANT A QUICK RESPONSE. TRY EMAILING ME INSTEAD!
|
|
blueshift
|
posted on 9/7/03 at 11:46 AM |
|
|
I don't have a good grasp of the forces involved in a dedion tube, but with the shocks mounted near the wheels it doesn't seem,
intuitively, that it would have to resist a particularly great bending force. Just need to rotate the opposite wheel when one bounces up and down.
Feel free to enlighten me. I speak maths and physics, by the way.
|
|
sgraber
|
posted on 9/7/03 at 03:05 PM |
|
|
All I can say is that my deDion tube feels very light (lite as air compared to a live axle eh?) and it is 3" 16ga.
Blueshift - I lived in St. Albans for 2 years as a young child. I still remember the St. Albans cathedral and the large lake where I once fell in...
Steve Graber
http://www.grabercars.com/
"Quickness through lightness"
|
|
craig1410
|
posted on 9/7/03 at 08:00 PM |
|
|
Blueshift,
Yes that is exactly what I meant by "intuitively" seeming sturdy enough. I would love to see a force diagram showing where the bending
forces come from and the relative magnitudes. I also have a great deal of respect for MK Eng. and if they designed my de-dion axle then I am pretty
sure that it is up to the job!
C'mon Cymtriks, you've got us all worried now...
Cheers,
Craig.
|
|
cymtriks
|
posted on 9/7/03 at 10:01 PM |
|
|
More Deon
The 20000inch lbs is a guess at what the worst bending load may be.
I have assumed that a lateral load in cornering may be up to 3g. This includes bumps before anyone says it looks a lot for cornering! By the way 3g is
pretty close to what some colleagues of mine actually measured in a real car being given a spin round a fairly grotty area of tarmac. I suppose it
could still be argued that sensors inside the car do not see what the suspension does but 3g as good as my real data gets.
I've also assumed that the corner weight is 385lbs. That's one quater of a total weight of 1540lbs (700Kg) composed of car plus two
occupants. Another guess but not too far out for most sevens.
For a Deon beam 11.5 inches above the ground that gives 385 x 3 x 11.5 = 13282inchlbs.
I added a safety margin of 50% giving 20000 inchlbs. I know that 50% isn't that big for a safety margin but this seems to give reasonable
results compared to actual Deon tubes.
For the tube sizes given by Rorty and Craig the stresses are-
2.0 12g (2.6mm) 74000psi
2.25 14g (2.0mm) 70000psi
The reason I suggested chrome moly is that it has a higher yield strength than cheaper steels. I've seen lots of figures quoted for steel and
standard mild steel seems to be in the range 50000 to 70000psi depending on the exact steel in question. As the stresses I calculated are at the top
of this range I suggested going to chrome moly as this usually lies above 70000psi for yield.
I am interested in what you all think of this approach and I am aware that it seems to err on the strong side. Does anyone actually know what the
yield strength of typical chassis tube steel is?
|
|