TTK77
|
posted on 10/2/05 at 09:54 PM |
|
|
Pedals
If you have done brake and clutch pedals by yourself, what kind of material have you used? Im planning to do floormounted pedals and material
thickness is the issue at this moment..
http://www.aar.fi
|
|
|
erwe
|
posted on 11/2/05 at 05:21 AM |
|
|
http://locostbuilders.co.uk/viewthread.php?tid=22060&page=2
Just steel 3 mm plate laser cut.
I can sell them in different stages, as a kit (unwelded) about 140 euro (90 pounds)
welded incl nylon bushes 180 euro (120pound) or welded with alu plates 196 euro (130pound)
The balance bar is from Ralley design (20 pounds)
I have to send it from the Netherlands, i can look up that price if you are interested, drop me a mail at sevennl@hotmail.com
|
|
JAG
|
posted on 11/2/05 at 08:50 AM |
|
|
I used 8mm thick Aluminium alloy plate.
Hand cut/filed etc... took bloody ages
The pads (for your feet) were made from 3mm thick plate screwed on - the more I think about it the more time I seem to have spent on the little
buggers.
[Edited on 11/2/05 by JAG]
Justin
Who is this super hero? Sarge? ...No.
Rosemary, the telephone operator? ...No.
Penry, the mild-mannered janitor? ...Could be!
|
|
Marcus
|
posted on 12/2/05 at 11:06 AM |
|
|
If you want basic pedals, i'd go for 4mm steel. You don't want the brake pedal bending in an emergency!!
Marcus
Marcus
Because kits are for girls!!
|
|
flak monkey
|
posted on 12/2/05 at 11:35 AM |
|
|
I would recommend taking a look at the commercial ones and seeing what proportions the pedals are in - thickness to depth. As it is a combination of
these measurements that gives the pedals the necessary second moment of area to resist bending when you stamp on them in an emergency! If someone can
post some estimated maximum forces i may be able to do a few calculations to get a thickness to depth ratio...
David
Sera
http://www.motosera.com
|
|
flak monkey
|
posted on 12/2/05 at 12:08 PM |
|
|
Well you can work it out im sure...heres the formula:
td^2 = 6Fx/yeild strength
Where:
t = pedal material thickness (in metres!)
d = pedal depth (in metres!)
F = maximum force on pedal (in Newtons [1kg = 9.81N)
x = distance from force application point, to master cylinder pivot (in metres!)
yeild strength is just what it says for whatever material you use. (in Pa)
There are of course some generalisations here...
the main one being that all the bending occurs between the end of the pedal and the master cylinder pivot (fair enough i think).
the other is that you stamp squarely on the pedal.
So if you use the formula to calculate the thickness and depth...add a saftey factor (engineers love em )
Doing a quick check calulation the answers dont seem to be far out. With a max force of 1000N (~100kg), steel pedal, distance to master cylinder
150mm. A 6mm pedal would have to be 26mm deep. Doesnt seem too unreasonable to me... have a play and see what you get.
BTW this formula is only for plate pedals....not box section or anything else!
Cheers,
David
PS the formula comes from M/I=stress/y if anyone wants to check it
[Edited on 12/2/05 by flak monkey]
Sera
http://www.motosera.com
|
|
Fred W B
|
posted on 12/2/05 at 06:19 PM |
|
|
So my thumbsuck in the garage this afternoon of 6 x 30 flat bar to make pedals was not for out!?
Fred WB
|
|
flak monkey
|
posted on 12/2/05 at 06:28 PM |
|
|
It would appear you werent far out...as long as my maths is good... . Assuming your pedal is steel then it should be ok (10% saftey factor as is
usual)...
Of course the maths is only theory, so isnt exact in practice...would be interesting to see what manufacturers pedal dimensions are...
David
Sera
http://www.motosera.com
|
|
TTK77
|
posted on 12/2/05 at 09:09 PM |
|
|
thnx
Thanks every1
http://www.aar.fi
|
|
JoelP
|
posted on 12/2/05 at 09:32 PM |
|
|
i just used inch square ERW, 16g. too simple?
|
|
Rorty
|
posted on 13/2/05 at 02:31 AM |
|
|
I would say anything thinner than 5mm is too thin because the pressure is seldom applied directly in line with the pedal blade if you actually think
about it. Just look at the wear on any rubber pedal pads.
I use 6mm plate for my laser-cut pedals, but cut some lightening holes in them which doesn't detract too much from their strength.
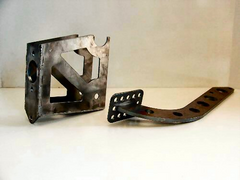 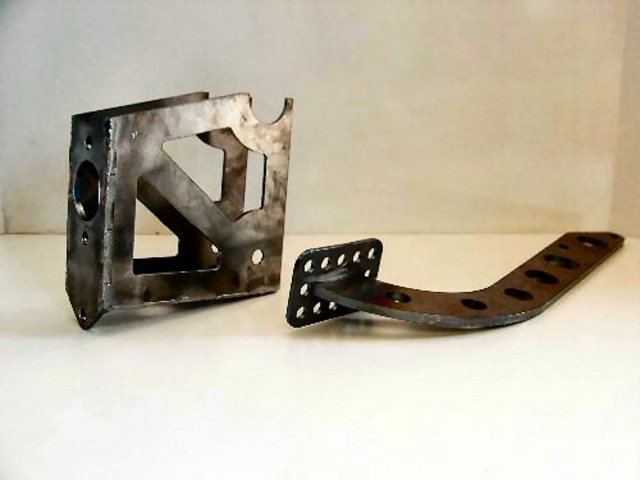 Rescued attachment pedal_&_box_02.jpg
Cheers, Rorty.
"Faster than a speeding Pullet".
PLEASE DON'T U2U ME IF YOU WANT A QUICK RESPONSE. TRY EMAILING ME INSTEAD!
|
|
TTK77
|
posted on 16/2/05 at 08:25 PM |
|
|
They r ready
I did them like this... Clutch pedal 8mm thick and break 9mm, stainless steel ofcourse..
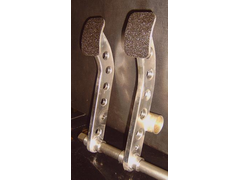 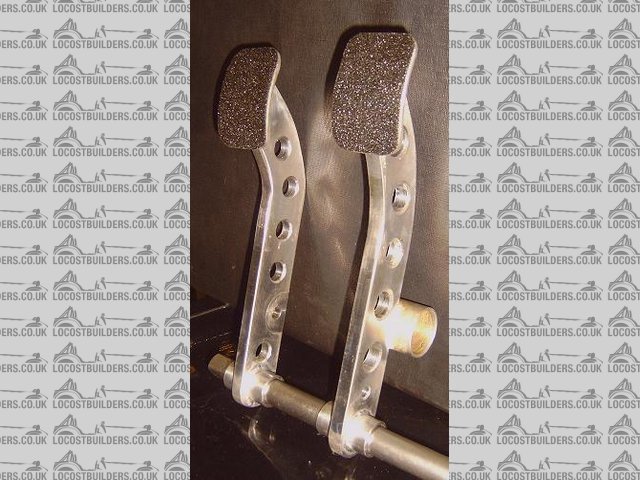 Rescued attachment pedals1.jpg
http://www.aar.fi
|
|
clbarclay
|
posted on 16/2/05 at 08:51 PM |
|
|
Personally i think erwe has the right idea (like most comercial ones i've seen), which is to use 2 or more plates of thinner steel.
If done properly you don't need anything like the mass of steel that single plate ones use (just look at comercial pedals, there pressed 16swg
or lighter)
|
|
britishtrident
|
posted on 16/2/05 at 08:54 PM |
|
|
quote: Originally posted by JoelP
i just used inch square ERW, 16g. too simple?
really not adequate -- it either has to be thicker or a deeper section it also depends on the layout of the pivot -- I used 40x20 16g -- I
worked on a design load of at the pedal of 150kg.
|
|
TTK77
|
posted on 16/2/05 at 09:02 PM |
|
|
Weight is not issue to me, as long as they strong enought and shiny
http://www.aar.fi
|
|
flak monkey
|
posted on 16/2/05 at 09:30 PM |
|
|
We are just told 10% safety factor, though of course it is dependant on the application. Non critical parts need a lower safety factor. However the
safety factor you need is also determined by the detail of the analysis. Obviously accurate FEA allows you to cut down safety factors considerably.
Safety factors basically come down to a bit of common sense...
David
Sera
http://www.motosera.com
|
|
britishtrident
|
posted on 16/2/05 at 09:46 PM |
|
|
Thing about pedals is you have to allow for the drivers thrust on the pedal x the deceleration
So if you have a very heavy driver say 100kg and an instantaneous peak stopping of say 1.5 g you get 1.5 kn exerted on the pedal, then allow a
decent factor of safety anywhere from 2.5 upwards twice that or more if welds are involved..
Those of us with more grey hair than we admit remember the Clay Regazonni Ensign accident at Long Beach 1980 in which the brake pedal snapped.
Most likely the pedal in the Ensign would have been adequate for a road car or race cars of previous decades but by 1980 tyre grip level had
increased so much that the G force contributon to brake pedal effort had eroded its design safety margins -- result the driver was almost killed.
[Edited on 16/2/05 by britishtrident]
|
|
britishtrident
|
posted on 16/2/05 at 10:04 PM |
|
|
quote: Originally posted by Rorty
I would say anything thinner than 5mm is too thin because the pressure is seldom
snip snip
Very true -- two schools of thought on pedal design either solid or a "section" of some sort.
For a solid pedal 5 or 6 mm sounds right to me -- 3 mm just isn't stiff enough in torsion or sideways bending. Of course care must be
taken not to put lightening hole in the wrong place
For pedal made of a steel section 1.6mm should be thick enough provided the depth and width are deep enough to provide beam stiffness and
strength .
|
|