SteveWallace
|
posted on 16/6/16 at 11:31 AM |
|
|
Improving fit of a splined shaft
I'm currently restoring the rear axle of my 1949 MG TC (I'll get around to setting up more of a build thread soon). The hubs are mated to
the half shafts via a tight splined fit using a press. The other end of the half shaft is a push fit spline into the diff. You can see the half shaft
and hub in the attached picture.
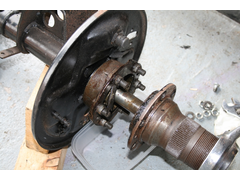 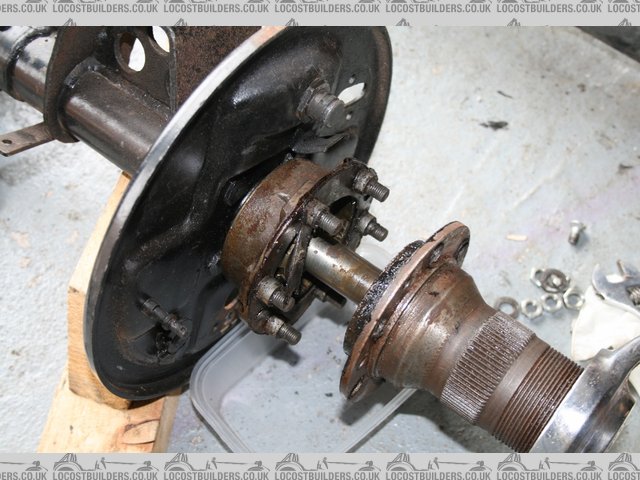 Description
My problem is that for one of the hubs/half shafts, the fit is not tight and can be pulled out by hand. This would mean that the half shaft would be
free to slide laterally a little along the splines when in use. I guess that the lateral load is not huge so the as-new press fit required pressure
of 140kN is not really needed and that all I really need to do is to ensure that its reasonably tight.
Does anyone have any advice on how I can make the fit tighter without having to buy a new half shaft and hub?
My thoughts are
I) Use high strength thread lock as its a gap filler as well as a 'glue'
ii) use a combination of filler powder and superglue (I've seen this used elsewhere and if done correctly is almost like a weld!)
iii) wrap the half shaft splines in a bit of thin shim metal and press it together (however, even thin shim metal might be too thick as the current
fit is not slack).
iv) bin the lot and spend ca. £200 on a new half shaft and hub (I don't know if its slack due to the hub or the half shaft)
Thoughts please?
[Edited on 16/6/16 by SteveWallace]
|
|
|
Rosco86
|
posted on 16/6/16 at 11:48 AM |
|
|
how about a little bit of damage on the male shaft? maybe a few center punch marks here and there? bit of a bodge i know
My Build Thread
|
|
coyoteboy
|
posted on 16/6/16 at 12:22 PM |
|
|
Better to try a uniform growth procedure - some form of vapour deposition process? Maybe an anti-friction coating of ~30 microns.
Can't assess exactly how it works but looks like a botch would be a safety risk?
|
|
obfripper
|
posted on 16/6/16 at 12:31 PM |
|
|
Stud grade threadlock may be sufficent, the proper stuff for the job is loctite 660, but it is 30 quid for a little tube and will bridge up to a 0.5mm
gap.
I think the activator spray may be required to allow thicker amounts to cure.
It is quite likely that the shaft and hub will be inseparable without heat once cured.
Dave
|
|
MikeRJ
|
posted on 16/6/16 at 12:40 PM |
|
|
You can buy a 50ml tube of Loctite 660 for about a Loctite 660 Quick Metal Repair Compound, Press Fit, Gap Repair, 50ml , and
it's the correct stuff to use for this situation.
|
|
SteveWallace
|
posted on 16/6/16 at 02:17 PM |
|
|
quote: Originally posted by MikeRJ
You can buy a 50ml tube of Loctite 660 for about a Loctite 660 Quick Metal Repair Compound, Press Fit, Gap Repair, 50ml , and
it's the correct stuff to use for this situation.
Good spot. It seems to be 1/3 the price of what it normally costs.
|
|
britishtrident
|
posted on 16/6/16 at 03:03 PM |
|
|
Quite a common problem the later design of T type axle axle also suffered from it. If there is slop it is likely to result in halfshaft breakage at
the end of the coarse splines.
Loctite make a grades specially for this type of problem it forms a permanent bond, this shouldn't be a problem as next time round you can
replace both worn parts. I would try try Loctite 638 or 660
[I] “ What use our work, Bennet, if we cannot care for those we love? .”
― From BBC TV/Amazon's Ripper Street.
[/I]
|
|
britishtrident
|
posted on 16/6/16 at 03:12 PM |
|
|
quote: Originally posted by coyoteboy
Better to try a uniform growth procedure - some form of vapour deposition process? Maybe an anti-friction coating of ~30 microns.
Can't assess exactly how it works but looks like a botch would be a safety risk?
All it is likely to happen is loss of drive --- the coarses splines at the wheel end of the shaft were a weak point, most MG T-type owners will
experience a snapped halfshaft at some point. One of the reasons an Escort axle conversion is a popular mod.
[I] “ What use our work, Bennet, if we cannot care for those we love? .”
― From BBC TV/Amazon's Ripper Street.
[/I]
|
|
nick205
|
posted on 16/6/16 at 03:16 PM |
|
|
Another way if you can would be to fit the hub and drill a small hole through the hub and half shaft and knock in a pin to prevent lateral movement in
use.
|
|
steve m
|
posted on 16/6/16 at 05:19 PM |
|
|
Probably not the "right option" but on my old MG midget with wire wheels, I was told by an elderly neighbour, to paint the inner spline on
the wheel with an enamel paint, leave to dry for a couple of days, grease the spline, slide the wheel on, and the fit will be tight
wear will only be an issue if the surfaces can move around
steve
Thats was probably spelt wrong, or had some grammer, that the "grammer police have to have a moan at
 
|
|
SteveWallace
|
posted on 16/6/16 at 05:24 PM |
|
|
I tried some of the standard high strength red loctite bearing/thread lock that I had in the garage as an experiment just before I started this
thread. I've just checked and I cannot separate the parts now - at least with a reasonable amount of persuasion, not in a press. I guess that
its got a lot of surface area to work on compared to the thread of a bolt and the original fit was snug rather than sloppy anyway.
I think that I'll assemble like that for the time being and when I eventually get the car on the road I'll check for play after a few
hundred miles and then try the 660 or get a new one if it hasn't held. As mentioned, its not a safety issue as the hub is firmly bolted to the
carrier which in turn is firmly fixed to the axle with a 50mm hub nut and bearing.
I should probably have held off until I had the wise advice from here.
|
|