Bob C
|
posted on 23/8/04 at 09:19 AM |
|
|
Welding halfshafts (driveshafts)
Hi folks,
I need to shorten some (mx5) halfshafts. I propose to cut out he middles & replace with CDS tube, say 30mm diam, 6 or 7mm wall, with conical
mating surfaces (see pic below).
Anyone done similar - was it a disaster?
Should I weld the very end?
Should I grind flats in the halfshaft stub where the MIG "spot" weld holes are?
Any comments welcome
Cheers
Bob C
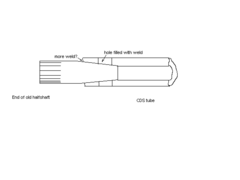 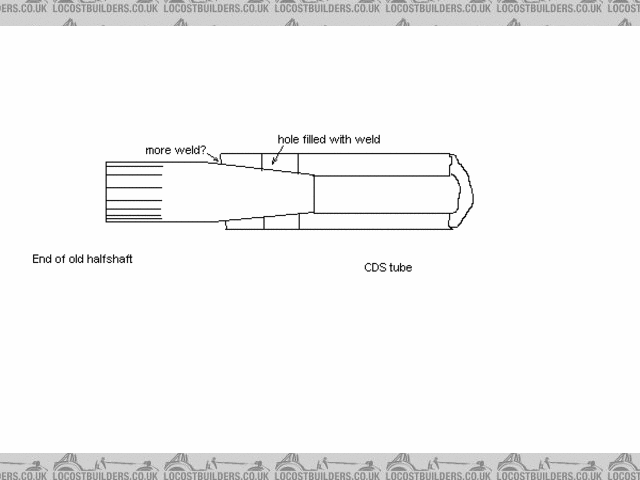 Rescued attachment half shaft.GIF
|
|
|
Peteff
|
posted on 23/8/04 at 10:26 AM |
|
|
When I was planning something similar I was going to do it like this but the idea was shelved for a simpler live axle chassis.
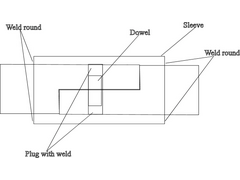 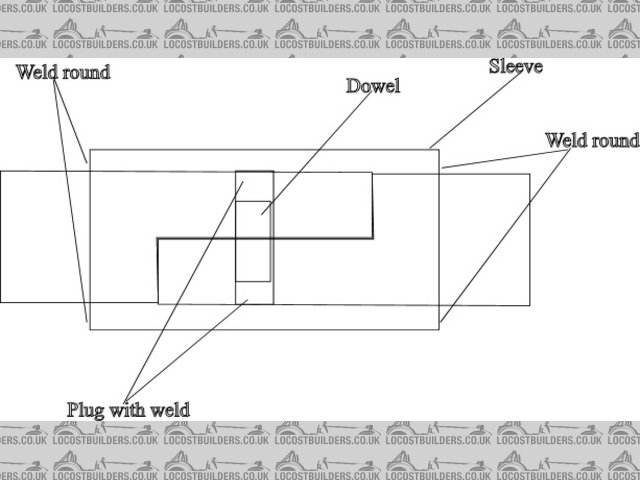 Rescued attachment joint.jpg
yours, Pete
I went into the RSPCA office the other day. It was so small you could hardly swing a cat in there.
|
|
James
|
posted on 23/8/04 at 11:04 AM |
|
|
Rorty's written a guide for lengthening axles where you just sleeve the join.
Here's the link:
http://www.rorty-design.com/content/axles.htm
Scroll down to the bit about re-joing them.
Hope that helps,
James
|
|
chriscook
|
posted on 23/8/04 at 05:10 PM |
|
|
I got my sierra driveshafts friction welded by Drivelink. It was only a fiver more than getting them sleeved and mig welded per shaft and a much
better way of doing it - mig welding heat treated steel isn't exactly best practice! I sent them my old shafts and within a week I had them back
cleaned, shortened and painted. They can also supply the old shafts if you don't have them, make new ones to your length or make up
'odd' shafts (eg one end form one car the other from another).
http://asp.drivelink.com/index_content.cfm
No connection just very happy with the service they provided me with.
|
|
Jon Ison
|
posted on 23/8/04 at 05:18 PM |
|
|
depending on cost, or if your doing it yourself, (much less cost) may be worth having new shafts made, i had 4 one off's made for the GT1, (2
spares) for under £80,
check out local machine shops ?
|
|
Bob C
|
posted on 23/8/04 at 05:54 PM |
|
|
I had new shafts made for my mx5 & that was rather expensive. I like the friction welding idea & will look into it. I know that's how
they put train wheels on so it must be quite good.....
Thanks
Bob C
|
|
chriscook
|
posted on 23/8/04 at 06:47 PM |
|
|
Friction welding is also one of the ways OE hollow driveshafts are made - Two solid splined ends are welded onto a tubular centre section. The other
main method for tubular shafts is rotary swaging (aka hammer forging) and that's not in the slightest bit low cost (www.rotaryswaging.com if you
are interested)
|
|
JB
|
posted on 24/8/04 at 11:49 AM |
|
|
Welding
Try not to weld in a complete round. This puts a weak spot in one place on the shaft. It is far better to put a slash cut on the end. This gives more
weld area plus avoids the stress raiser in one place.
elding into a hole (rossette weld / plug weld) is a very good idea.
Pre heat the work to dull red and allow to cool slowly.
Welding shafts is generally not a good idea due to the high grade of steel used.
Another option is to sleeve and silver solder or sleeve and use a high strength retainer sush as Loctite 638. You will have to work out the shear area
and strength.
John
|
|
NS Dev
|
posted on 24/8/04 at 11:58 AM |
|
|
bear in mind that made to length "unbreakable" shafts with Ford splines are available for £70 each from GB engineering in Nantwich. This
is what I use on my grasser with locked diff and no problems, they twist rather than break.
The £70 each sounds expensive but if you break a shaft the damage can be expensive!!! (one of my fellow competitors smashed his gearbox to pieces when
a welded shaft broke on his trasverse vauxhall setup) Look at it as a one off £140, you will not have any worry after that!!
(it also looks much neater than welded shafts)
|
|