nitram38
|
posted on 22/8/07 at 08:11 PM |
|
|
And the bit about bigger rod ends is not valid too?
|
|
|
Lippoman
|
posted on 22/8/07 at 09:03 PM |
|
|
Oversight?
quote: Originally posted by nitram38
10% of 12,224 lbs is 1222.4 lbs or have I missed something?
I think you missed the part about a 10g jolt.
120 lb @10g ~ 1200 lbs.
lb = pound ("weight" , lbs/lbf = poundforce, I've been told, but then I'm mainly metric.
|
|
nitram38
|
posted on 22/8/07 at 09:23 PM |
|
|
OK, where does the 10g come from?
Do you mean that a force of 10g is on the joint?
Is this a guess or a proven actual force that the average road car will endure?
|
|
kikiturbo
|
posted on 22/8/07 at 10:05 PM |
|
|
hi,
I think there are some misconceptions about suspension loadings here... but let me start from the begining..
for me (and I am in the process of designing a similar suspension myself, using presseed in spherical bearings..) there are 2 questions:
1. what forces will that joint see
2. rod end / spherical in a fixed housing / ball joint dillema....
someone here said that the rod end in question will see only shock loadings that are proportional to the shock and suspended weight (i.e. weight of
the wheel... ) which is not eaxctly the right way of looking at it....
the rod end in question has 3 major forces on it..:
1. radial force towards the car, from cornering
2. radial force towards the back, from braking
3. Axial force downwards, from the reaction of the spring, since the spring is connected to the end of the A arm, via pushrod or direct...
when standing still the axial force is equal to the corner weight of the car minus the weight of the wheel/upright/brake combo. bigger problem is what
happens in bump... well, you just have to decide how tough you want to make it.. I have read from people in the industry that 5g vertical is about ok
for a road car (not production road car... ) but for the sake of argument let's say 10g....
also, you can say that you will see only 1.5 g from braking, but since you will hit potholes, you have to accont for more g's for both braking
and cornering... but let's only concentrate on bump and axila force right now, as this is where the discussion has been heading..
there are two questions right now:
a) will the spherical take it
b) will the threaded rod end take the axial force, since it is in some major bending
since the spherical bearings have axial rating of about 20-30% of the ultimate radial, the axial component is the most interesting... the spherical
that I am thinking about for the lower A arm is 14mm, has radial dinamic rating (dinamic is lower rating than static, but since the spherical will see
constant work...) of 50 000 N. This particular bearing is rated for max 30% for axial loads, but let's say, 20% or 10000 N. that would mean that
at 10G it will be ok for corner weight of 1000 N or , 100 kg... of course, you could always go for 16mm which would mean about 120 kg corner weight at
10G...
the second problem is will the rod end housing take it.... well, for some people it works, I am a bit sceptical and will go for spherical bearing
pressed in the A arm... this way I can make it much stronger since I have to connect the pushrod to the A arm...
as for the ball joints as a preffered solution.... ok, but I would like to read some technical specifications for the various ball joints... with
sphericals I at least have data available...
|
|
Uphill Racer
|
posted on 22/8/07 at 10:54 PM |
|
|
quote: Originally posted by JB
The Formula Student article sums it up very well.
The standard of design is improving at Formula Student as I witnessed this year as a Design Judge Team Leader.......
Hope it has JB when I was a design Judge the puter said yes..............stress analasis...very pretty red,yellow, green and blue 3D pics. Why did the
tent with the guy with the welding equipment have the biggest queue of cars..........has it changed, but like this thread you know people (RAC MSA)
can be fooled by pages of calcs. Ok my car has rose joints in single shear, BAD, but work well under known loads and would not use them like that on
anything other than for hillclimb and sprint, also my car is under 800lbs. In my humble opinion anyone using rod ends in singe shear in a road car has
a death wish.
[Edited on 22/8/07 by Uphill Racer]
[Edited on 22/8/07 by Uphill Racer]
|
|
britishtrident
|
posted on 23/8/07 at 08:15 AM |
|
|
Single shear isn't a problem if all the sizes are increased to an appropriate level, after all this is the way volume manufacturers use to mount
ball joints and coil spring damper units
However in most amateur constructed vehicles with joints mounted in single shear the diameters chosen are well below anything I would consider.
|
|
britishtrident
|
posted on 23/8/07 at 08:23 AM |
|
|
Mounting rod ends in a bending + shear mode is however a different issue, this really isn't a good way to do things. I have never seen a rod
end fail in this mode (except through collision) but I have seen them bend.
Remember you have to build your car to withstand contact with kerbs, potholes, drain covers bricks and anything else urban roads or chavs can throw at
you.
[Edited on 23/8/07 by britishtrident]
[I] “ What use our work, Bennet, if we cannot care for those we love? .”
― From BBC TV/Amazon's Ripper Street.
[/I]
|
|
britishtrident
|
posted on 23/8/07 at 08:26 AM |
|
|
quote: Originally posted by nitram38
OK, where does the 10g come from?
Do you mean that a force of 10g is on the joint?
Is this a guess or a proven actual force that the average road car will endure?
If anything 10g is conservative -- hitting a kerb even just brushing it is a step change in acceleration.
[I] “ What use our work, Bennet, if we cannot care for those we love? .”
― From BBC TV/Amazon's Ripper Street.
[/I]
|
|
nitram38
|
posted on 23/8/07 at 10:41 AM |
|
|
britishtrident, no bending or loosening of my rod ends after one year/2000 miles of use (and some serious potholes), so I guess that my set up is big
enough for the purpose (which is what I have said from the beginining).
Using Rod ends over sperical has one big overlooked benefit and that is adjustability.
For an amateur builder this is a necessity because no chassis is that accurate, so adjusting the suspension is easier.
I have n't hit any curbs, but that is perhaps down to being an experienced driver and also the fact that I can see both front wheels from the
driving position.
It also means that I can keep an eye on my suspension while it is in motion.
This made setting the shocks up a doddle as I can visually see bump on my wheels.
When I first drove the car, I had the front anti-roll bar connected, but this was too stiff for road use. Now it is disconnected and should only be
used if it goes on a track, but I still think that it might be overkill there.
[Edited on 23/8/2007 by nitram38]
|
|
nitram38
|
posted on 23/8/07 at 01:28 PM |
|
|
Update:
If you absolutely can't use rod ends in shear, why do they make these:
Available from Mcgill Motorsports on
ebay
|
|
Syd Bridge
|
posted on 23/8/07 at 03:43 PM |
|
|
A man could quite easily be the same way as that departed scotsman, but......deep breath and remain calm.
Dear Martin,
That rodend in the picture above is designed and made to act with a radial load.
It's the stud THROUGH the rodend that's being put in shear.
It is made specifically for putting on the end of a steering track rod, at the upright end. And does the same job as an outer track rod end. I specify
and design similar items in my work.
Without meaning offense, you are a much better welder than engineer, which you obviously are not trained at.
Stick to your strengths and do what you know best, and stop trying to outsmart the people who do this stuff for a living. There's a couple of
others on here who appear to do so, as well as myself.
The hole you are digging is getting deeper. Learn from what has been suggested, put it to good use, and move on.
Cheers,
Syd.
You'll also find those joints used on the front and back stay bars(sometimes called 'radius rods' ) on solid axles, on USA (and Aus)
circle track cars. In that application, they still have the ball joint in radial load, and the stud in shear.
[Edited on 23/8/07 by Syd Bridge]
[Edited on 23/8/07 by Syd Bridge]
|
|
nitram38
|
posted on 23/8/07 at 04:36 PM |
|
|
Syd, I am not going to discuss this anymore as you are obviously superior to me (except for welding).
At least I am willing to explore and discuss these matters and not bash people over the head with my qualifications.
Don't bother replying as I will be unsubscribing from the topic.
|
|
britishtrident
|
posted on 23/8/07 at 06:36 PM |
|
|
This going round in a Mohr's circle.
This is neat http://www.engapplets.vt.edu/Mohr/java/nsfapplets/MohrCircles2-3D/mohrcircles2-3d.htm
[Edited on 23/8/07 by britishtrident]
[I] “ What use our work, Bennet, if we cannot care for those we love? .”
― From BBC TV/Amazon's Ripper Street.
[/I]
|
|
Fred W B
|
posted on 23/8/07 at 06:48 PM |
|
|
 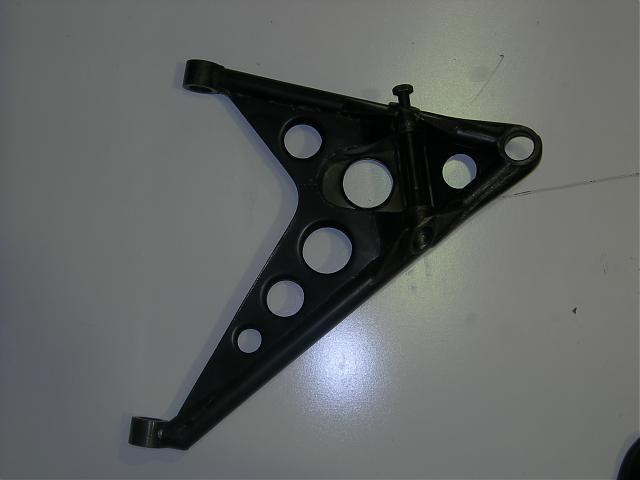 lwb
I'm convinced. I now want to do something like this for a lower wishbone
Cheers
Fred W B
|
|
Syd Bridge
|
posted on 23/8/07 at 10:16 PM |
|
|
At least one person has learnt from this, and now knows when they're on a winner, and another a loser! Funny old world, isn't it?
Cheers,
Syd. 
|
|
Tralfaz
|
posted on 23/8/07 at 11:55 PM |
|
|
It's funny how different people are. I have a 5/8" NMB Spherical bearing pressed in (with Spiral Retaining ring and Large safety washer)
that has an axial load rating of 8000 lbs and I still give it a second look... (On an 850lb Track Only BEC)

|
|
Doug68
|
posted on 24/8/07 at 03:07 AM |
|
|
I can see this discussion going on until the wheels come off it!
I've been resisting posting that for days, but in the end the urge got too much, sorry.
[Edited on 24/8/07 by Doug68]
|
|
40inches
|
posted on 24/8/07 at 01:46 PM |
|
|
Interesting read here http://www.formulastudent.de/academy/pats-corner/advice-details/article/pats-column-rod-ends-in-bending/
|
|
gazza285
|
posted on 24/8/07 at 11:41 PM |
|
|
quote: Originally posted by nitram38
britishtrident, no bending or loosening of my rod ends after one year/2000 miles of use (and some serious potholes), so I guess that my set up is big
enough for the purpose (which is what I have said from the beginining).
Having proved that they work for 2000 miles have you established the duty cycle for the joints?
Most manufacturers work on the principle that things wear out before they break, allowing them to be replaced when wear becomes apparent, are you
working to the same ideals, bearing in mind that they have access to much more testing facilities and analysis than you, or have you decided to change
them five miles before they are due to shear off?
DO NOT PUT ON KNOB OR BOLLOCKS!
|
|
turbospud
|
posted on 29/8/07 at 05:39 PM |
|
|
i wouldnt use a rod end for that type of application, i had the centre part come through the outer part,the washer that was meant to prevent it going
through didnt,its only a press fit your relying on
rod ends are only suitable for push pull loads along the stub direction as rd dave points out there are other better options
|
|
JB
|
posted on 29/8/07 at 06:18 PM |
|
|
My understanding of this discussion is it is about which way sphericals should be loaded to get the greatest strength for weight, ie the optimum
design. Many solutions work and last. However there are better ways of designing parts.
For example, single shear works but it is so much better structurally in terms of weight to use double shear.
Suspension mounts on the chassis are put into the middle of an unsupported tube.... it works but would be so much better if the mounts were into a
junction of tubes.
Bent tubes are used in chassis without supporting the bend. Again it works but the design could be improved.
Often rod ends loaded in bending work with no problems however with a change in design they can be loaded in tension and compression allowing smaller
lighter parts OR a greater saftey margin from fatique and one time overload failure.
Calculations in my mind are pretty pointless due to the problem of knowing the loads going into the system. It is better in my mind to stick to good
design (which basically means reducing stress raisers) and then use sizes that have been used for years.
My car was built this way. However I do now realise that I have some rod ends in bending on my rear uprights. I didnt know any better at the time but
because I read and was willing to take on board the knowledge of those who do know better I learnt.
John
[Edited on 29/8/07 by JB]
|
|