pbura
|
posted on 29/7/04 at 12:31 PM |
|
|
My concern with the loose tube is that the grease would likely work out through the gaps between crush tubes and brackets, while road dirt could enter
the joints.
[Edited for gratuitous flippancy]
[Edited on 30/7/04 by pbura]
Pete
|
|
|
stephen_gusterson
|
posted on 29/7/04 at 01:14 PM |
|
|
as a kid I had a soapbox cart that used a single bolt as the main steering axis.
It was fine.
The biggest problem was the 'mechanical backlash' in the rope that formed the steering system.
In the 2 -3 miles of so it covered in its lifetime there was no problem with the bolt.
atb
steve
ps - which goes to show that APPLICATIONS count. What might be OK in one case, may not be in another.
[Edited on 29/7/04 by stephen_gusterson]
|
|
Dale
|
posted on 29/7/04 at 02:36 PM |
|
|
All my front suspension and inboard shock rockers on bronze oiltite bushings on ground shoulder bolts. Just have to make shure that the brackets are
a perfect fit--make the arms up and attatch the brackets to the arms and then weld the brackets to the frame and they line up nicely.
Very cheap and easily replaced when they where out.
Dale
|
|
andkilde
|
posted on 29/7/04 at 02:53 PM |
|
|
Syd, I can only disagree with you.
I challenge you to show me some industrial machines that use a small bearing surface, steel-on-steel interface with the sort of cyclical loading
we're putting on a suspension joint.
Your conecting rod analogy is amusing -- even given its much larger bearing surface -- try running your engine without the lovely film of high
pressure lubricant for a few minutes and see what happens.
The joint interface in our case has two substantial stress raisers when installed with the bolt not properly tightened. The pivot points become the
holes in the tabs - the bearing surface of each pivot is roughly 1/8 of a square inch, which gets less with wear or if, god forbid, you're
pivoting on the threads. Any lubricant present will be forced out immediately, because of the joint's tiny bearing surface, and the bolt will
gall on the holes in the tabs.
One of two things will occur, the bolt will saw its way through the mild steel mounting tab or the scarred alloy-steel bolt will shear off in a
fatigue failure.
Seems a huge risk to expose yourself to when the alternative is to install the same components "as designed".
Cheers, Ted
|
|
Cita
|
posted on 29/7/04 at 03:29 PM |
|
|
Why not weld a nut to one side of the bracket.Run a correct part treathed bolt through the polybushes and lock the bolt with a counter nut against the
welded nut.No more crush tube to worry about-no more metal on metal rubbing.
|
|
andkilde
|
posted on 29/7/04 at 08:48 PM |
|
|
quote: Originally posted by Cita
Why not weld a nut to one side of the bracket.Run a correct part treathed bolt through the polybushes and lock the bolt with a counter nut against the
welded nut.No more crush tube to worry about-no more metal on metal rubbing.
Much better than a loose bolt Cita, you may still get "fretting" on the head end of the bolt if it can wiggle inside the tab.
The standard, poly bushes with separate crush tube is already an excellent and robust design though -- works a treat if fitted carefully.
Cheers, Ted
|
|
planetester
|
posted on 29/7/04 at 09:44 PM |
|
|
I only wanted a yes or no,my experience is that you dont let the metal to metal work unless you put grease nipples to force lubrication in, you wont
remember morris 1000 front pivots falling off thro lack of it, any way, I think the crush tube should be locked solid in the chassis bracket & the
poly bush should rotate on it, I just want someone with experience to tell me how easily it should rotate, at the moment I have pressed the crush
tubes in with grease & when mounted to the chassis they are very stiff
thanks all
|
|
pbura
|
posted on 30/7/04 at 01:16 AM |
|
|
quote: Originally posted by Dale
All my front suspension and inboard shock rockers on bronze oiltite bushings on ground shoulder bolts. Just have to make shure that the brackets are
a perfect fit--make the arms up and attatch the brackets to the arms and then weld the brackets to the frame and they line up nicely.
Very cheap and easily replaced when they where out.
Dale
Dale, I found this very interesting as a means to economize on rod ends. I read a bunch of stuff online and came away with the impression that they
are better than nylon bushings and worse than rod ends in their ability to take side loads. They get high marks for dealing with oscillating motions
than rod ends, which can wear more unevenly and also allow lubrication to work out of the bearing surfaces.
It seems that oilites are generally used in fairly clean environments, so maybe dust boots would be a good idea.
Thought this tech sheet was interesting, especially about the type of shaft to be used:
http://www.hpceurope.com/vgb/fichtech/guidagerotation/coussinetoilite.html
Don't know if I'm adventurous enough to use them as much as you have, though they seem to be the hot ticket for control arms in R/C cars
 I'll definitely use them for bellcrank pivots.
Pete
Pete
|
|
Cita
|
posted on 30/7/04 at 08:58 AM |
|
|
Ted,if you use a reamer to get the perfect fit for the bold and it is tightened with the locknut how could that bold be fretting?
I dont know if a loose bold is worse than a bolt which is used as a spring as would be the case with the welded nut and a to large bracket hole on
the bolt head side.That "fretting" bolt will snap all of a sudden while a loose bolt wil start to rattle and shake more than enough to
warn you.
All IMHO offcourse.
|
|
andkilde
|
posted on 30/7/04 at 01:53 PM |
|
|
Cita: The bolt as captured by the welded in nut arragement you mentioned would have no troubles at the nut-end, at the head-end it's still free
to rub on the bracket -- worst case, the head might break away and you'd still be left with a stud.
Your idea is far more workable and (in the unlikely occurence that it did fail) fails more gracefully and safely than Syd's loose bolt.
Syd: I am eternally grateful that I am separated by an entire ocean from you and any vehicles you can touch or otherwise bodge.
Everybody Else: The plastic bushed joint with a crush tube works, and works well, as designed. Any problems experienced will go down to ill fitting or
improperly installed parts. If they don't fit properly send them back for replacement or dress them to size with a file or reamer --
re-engineering a part to solve a fitment issue is silly.
-Assemble with Moly grease.
-The crush tube should fit tightly between the brackets and be locked in place by the bolt & nut.
-The ID of the crush tube and the holes in the brackets should be a tight fit on the bolt.
-The bolt's shank should be unthreaded where it passes through the crush tube and chassis brackets. You should have a flat washer at the outside
of each end and use a Nylock or other self locking nut.
-The bushes should be a tight fit in the suspension arm and should swivel freely about the crush tube with no slop.
-If you "preload" the bushes as Rorty suggests (the thrust surface "brims" of the tophats being slightly too big to be a slip
fit between the mounting brackets so that they are compressed a little bit during installation) make certain that once assembled the joint swivels
freely (light hand pressure) about the crush tube.
Once fitted they should be entirely trouble free. I would check the bolts for tightness and perhaps disassemble and regrease occasionally.
Cheers, Ted
[Edited on 30/7/04 by andkilde]
|
|
Cita
|
posted on 30/7/04 at 02:40 PM |
|
|
Thanks for the explanation Ted and as far as i understand it now:by tightening up the crushtube inbetween the bracket you prevent the bolt from any
movement at all,am i correct?
So if we could develop a method of keeping that bolt from any movement we would not need a crushtube?
Forgive me my ignorance but i'm willing to learn.
|
|
stephen_gusterson
|
posted on 30/7/04 at 03:28 PM |
|
|
all gather in the playground lads, looks like we are gonna have fight.
I will look out for teacher
atb
steve
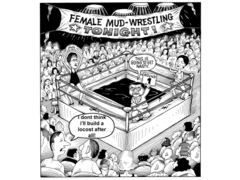 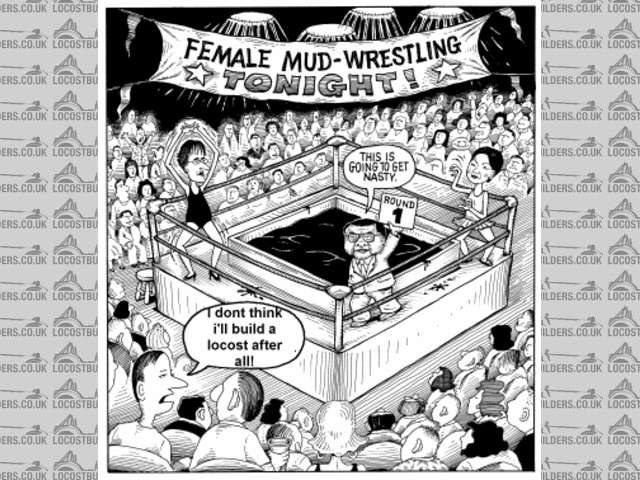 Rescued attachment mud.gif
|
|
Dale
|
posted on 30/7/04 at 04:44 PM |
|
|
No crush tube would be nessesary if you use an apropriate shoulderbolt with a thrust washer at each side of the bushing. Although a locking mechanism
to keep the bolt from turning under stress would help as well (flat edged washer with a placement pin maybe)
Dale
|
|
stephen_gusterson
|
posted on 30/7/04 at 05:14 PM |
|
|
yeah
I nearly mentioned (on the oceans apart thing) that you had a boat
atb
steve
|
|
JoelP
|
posted on 30/7/04 at 11:10 PM |
|
|
great. we all agree on so much! all anyone disagrees on is whether the crush tube should be slightly shorter, longer or the same as the bush! by less
than a mm either way! and even that wasnt a clear cut disagreement, cos rorty never said it should be tight enough to lock up...
if you follow most of the advice on here, you cant go much wrong really. i think this one has been hammered to a conclusion...
|
|
pbura
|
posted on 31/7/04 at 12:17 AM |
|
|
Until next time?
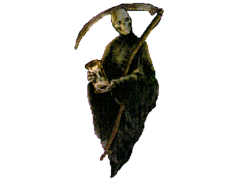 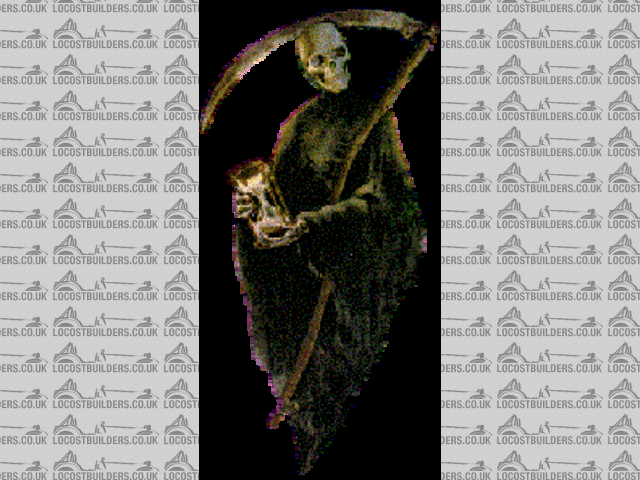 Grim avatar
Pete
|
|
Hugh Jarce
|
posted on 6/8/04 at 03:47 AM |
|
|
Ted you have my support. Syd is barking up the wrong tree. Sure there are metal on metal soints in all sorts of industries but they are all exactly
toleranced and made from suitable material. A metalastic bush has only got a bit of ERW tube up the inside of it and at best would be a loose fit on a
bolt.
Syd argues a bolt is a shaft. Well unless it is a aircraft (such as AN) quallity it will not even be round. Again unless the bolt is AN it will
probably have threads exposed inside the assembly which everyone knows is a disaster waiting to happen.
I spoke to a class 1 scrutineer (just below F1 standard) and described Syds theory. He laughed and asked if Syd was still at school.
The pay isn't very good , but the work's hard.
|
|
andkilde
|
posted on 6/8/04 at 01:07 PM |
|
|
quote: Originally posted by Syd Bridge
Just to ponder the problem further, What is the difference between a ground,(or precision) bolt, fixed from rotation, with the tube rotating on it;
and a 'crush' tube with the poly bush rotating on it; and a metal-metal rodend. All used in the same application, say on a racecar.????
Answers of more than three words fail to grasp the basic engineering principles.
[Edited on 6/8/04 by Syd Bridge]
Redundancy in failure...
i.e. if the bearing surface of your plastic bush or crush tube fail, you've still got the bolt to hold the wheels on. If the ball breaks out of
a rose joint (and you've mounted it in double shear or with a big backing washer) the suspension arm is still held in place -- though if the
housing fails, you're screwed, one reason I would argue against rose joints on a road car.
Sorry Syd, I realize in hindsight that this, unfortunately, became more of a debate than a rational discussion.
For the most part, the folks on this forum are trying to make the most with the least. The chances of finding a precision ground shoulder bolt on your
average Locost are slim at best.
Yes, there is absolutely more than one way to skin a cat -- but for those of us with limited funds using the inexpensive parts "in hand"
properly fitted is likely the best option.
Cheers, Ted
|
|