harmchar
|
posted on 7/7/20 at 04:40 PM |
|
|
I started to dabble in the 3D printing after getting a deal on an Aldi special. A Balcho Touch. £149 iirc.
I also used Fusion 360 as it's very well supported on YouTube with helpful videos.
Problem I can see with the design above is printing the raised lip (highlighted in green). If printed as it's modelled, the internal would have
to be solid or infill. If printed the opposite way with the green highlight on the print bed, the centre with the logo/writing would be floating off
the bed, which can't be done.
Would be interested how another printer/designer would get round this.
Good luck with the project.
|
|
|
motivforz
|
posted on 7/7/20 at 05:28 PM |
|
|
I would print this in the orientation like a cup rather than a hat to minimise the use of support material. This makes the words really hard to
achieve though on the outside and because of the size of the font I'd suspect you wouldn't be happy with the resolution - i'd expect
it to look a little grainy. Generally the bolder the better.
Overhangs (such as the snap in tangs) are generally possible without support material up to an angle of 45° from vertical, but reducing the angle and
overhang by design is best where possible.
|
|
tims31
|
posted on 7/7/20 at 06:14 PM |
|
|
quote: Originally posted by David Jenkins
tims31 - you're probably starting to realise what a can of worms you're opening!
The real hard work in 3D printing is the design of the part, followed by the inevitable redesign when the part doesn't quite fit properly, or
doesn't do what it is supposed to do. This means that it is way cheaper to learn how to design your own parts, rather than pay someone to do it
for you. The actual printing is just a mechanical process that's easily learned, and that usually takes very little time. It's just a
craft - the more you do it, and the more care you take with experience, the better your end-products will become.
I'm quite pleased actually David, I know nothing about it, but it has sparked an interest and another possible hobby to dable with over the
winter months when the weather is crap.
There is some really useful information and tips coming out, the comment about the cap that has been designed with the lettering and printing up the
other way is interesting. I guess you can only print (cup down) orientation with the support printing otherwise it collapses and has nothing to print
onto. Hadn't even thought about that.
As for finish, what product gives the best smoothest finish, and can it be sanded and painted afterwards.?
Build: http://www.martinsfurybuild.co.uk/
|
|
David Jenkins
|
posted on 7/7/20 at 07:41 PM |
|
|
quote: Originally posted by tims31
As for finish, what product gives the best smoothest finish, and can it be sanded and painted afterwards.?
Most plastics can be given a nice finish as long as you're prepared to fill and paint - a lot of people do this.
Another trick with ABS is to put the piece in a container that has a puddle of acetone in the base (the piece doesn't actually touch the piece).
The vapour softens the ripples on the surface and smooths them out. There a load of videos on YouTube about this. The problem is that ABS can be a
PITA to print at home unless you've got more advanced kit, e.g. a heated chamber in which the parts are built up.
In my experience, ABS can sometimes just work and give a nice result, and on another day trying to print the same part on the same printer with the
same filament just won't work. Most of the time I stay away from it! There's another filament called PETG that's easier to print,
but needs practice to make a decent print. I don't know how weather-resistant that stuff is though, but I believe it's good.
|
|
watsonpj
|
posted on 7/7/20 at 11:42 PM |
|
|
The model i put up is to be printed in the orientation shown with infill. The reason for this is to get the best surface finish especially around the
detail which will be the Fury emblem. Printing it that way up could pose a problem so it will use a 30% infill but with either a brim or a full
elephant foot at the base of each flexure to ensure adhesion . I did try to print in abs tonight (as i had it loaded for something else) without the
brim but as expected it had a bed adhesion problem so I will swap to PETG tomorrow as its a bit better to deal with and I have that in black (abs
purple). Layer height is likely to be 0.2 so probably a 3-4hrs per part.
The part is 31g but with infill is 67g so there is a lot of infill so it over doubles the cost of the part but the extra 93p saves a lot of clean up
afterwards so is worth it .
The modeling is the easy bit trying to work out the best way to orient a part or to change the design to minimise support (time/cost) and also ensure
the cosmetic faces are tops or sides to get the best quality. sometimes its just easier to make it as more than one part which still may happen here
as then I can print the logo on a fine setting and the main body on a coarse but upside down so no infill is required.
Pete
|
|
loggyboy
|
posted on 8/7/20 at 12:04 AM |
|
|
quote: Originally posted by watsonpj
The model i put up is to be printed in the orientation shown with infill. The reason for this is to get the best surface finish especially around the
detail which will be the Fury emblem. Printing it that way up could pose a problem so it will use a 30% infill but with either a brim or a full
elephant foot at the base of each flexure to ensure adhesion . I did try to print in abs tonight (as i had it loaded for something else) without the
brim but as expected it had a bed adhesion problem so I will swap to PETG tomorrow as its a bit better to deal with and I have that in black (abs
purple). Layer height is likely to be 0.2 so probably a 3-4hrs per part.
The part is 31g but with infill is 67g so there is a lot of infill so it over doubles the cost of the part but the extra 93p saves a lot of clean up
afterwards so is worth it .
The modeling is the easy bit trying to work out the best way to orient a part or to change the design to minimise support (time/cost) and also ensure
the cosmetic faces are tops or sides to get the best quality. sometimes its just easier to make it as more than one part which still may happen here
as then I can print the logo on a fine setting and the main body on a coarse but upside down so no infill is required.
Pete
That must me some pretty dense support infill?. you could get away with 5% support infill with a support roof, with 1mm roof (8 layers at my setting
of 0.12 layer height) it should allow a good bridge to the infill. I've just done a basic cup design through Cura and 5% support only adds
7grams to a 15gram base model.
For ABS make sure the fan is turned off and keep the bed temp the same throughout the print, and use some pritstik on the bed, that should assist with
adhesion and warping.
Mistral Motorsport
|
|
AntonUK
|
posted on 8/7/20 at 02:29 PM |
|
|
I did some for the ginetta. Worked well but didn't get the retaining clip quite right and I lost one...
reminds me to print another
Build Photos Here
|
|
ken555
|
posted on 8/7/20 at 05:10 PM |
|
|
I made in a sort of top hat shape, that can't escape from the front, only the back.
|
|
Bluemoon
|
posted on 12/7/20 at 09:00 PM |
|
|
If you get a printer I am very happy with my "Ender 3", which seems a good cheap place to start printing..
I have been rather impressed with the quality of the printer for the price, very well packaged, and quality for the money has surprised me, 3D
printers have come a long way since RepRap.
Only printed PLA so far, quite impressed by what is possible.
Mine came from Amazon, seller Comgrow, had to contact their support much to my surprise they responded in 7 hrs and their advice fixed my issues other
cheaper suppliers out there but support may be patchy.
Dan
[Edited on 13/7/20 by Bluemoon]
|
|
watsonpj
|
posted on 13/7/20 at 10:49 AM |
|
|
Loggyboy yes it is quite dense and I can reduce it but when i use petg I find that it doesn't bridge well so 5% gives a very poor surface finish
above.
I was only doing this as a quick test in abs anyway so I just used a dense support and some brims to stick it to the bed which it did but then failed
see below.
That said I haven't had a successful print since (until last night) when i found that the print head cooling fan had failed so everytime I
printed the extruder would clog. This was happening 10 -20 layers into the print which was how long it took the heat to get past the heat break and
make the filament too soft to drive, obviously I didn't work this out until the 4th strip down as the fan is completely silent in operation
normally and it wasn't until then that I tried to strip it immediately rather than wait for it to cool and found a plate that is always only
warm burning my fingers.
I final got a petg test cube out last night after fixing the fan issue so I will try again tonight to get a first off wheel centre in petg.
|
|
watsonpj
|
posted on 13/7/20 at 05:17 PM |
|
|
So the trial part is hot off the machine and fits the wheel but could probably do with being a little bit tighter so I'll do with the next part
with an extra 0.5mm on the flexures or I could try building this one up by 0.1-0.2 steps in epoxy until it feels good. . The petg has been out for
other a month so probably need drying before I do the real parts which has probably lead to a few zits.
Really annoyingly its meant to be random start but simplfy3d has done all the top surface starts in a line but this will be covered over by the insert
with the Fury Logo on.
 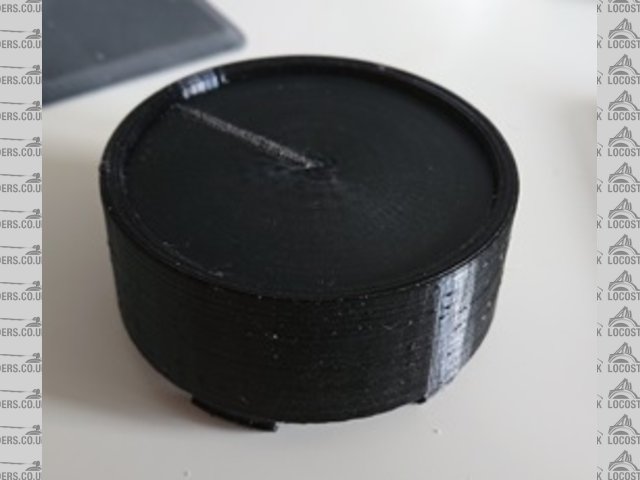 rp_wheel centre 2
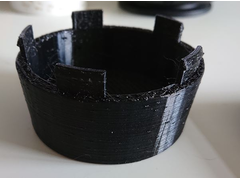 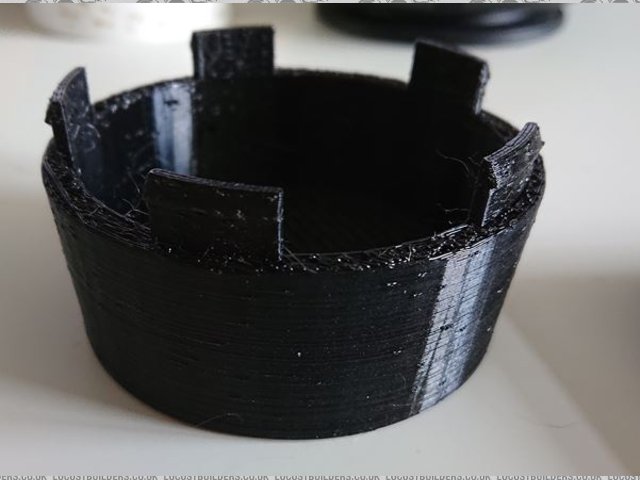 rp_wheel_centre_3
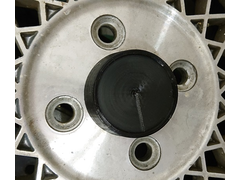 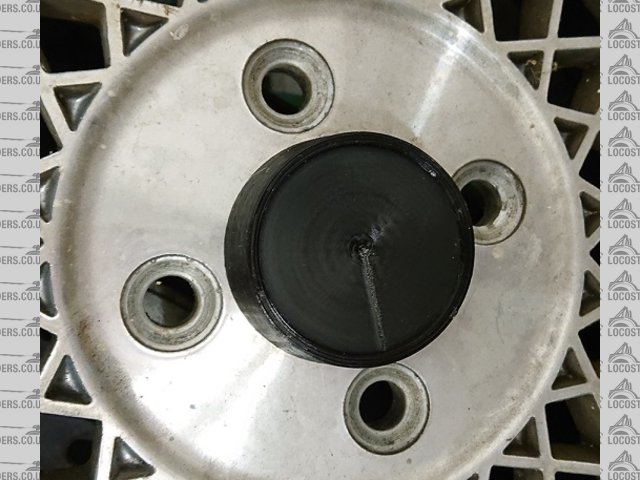 rp_wheel_centre
I went for a custom support in the end so model in a support frame and then used 15%, this used about the same material as 5% infill but had 15% to
support the roof.
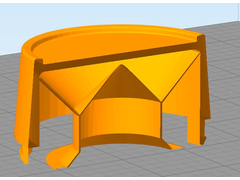 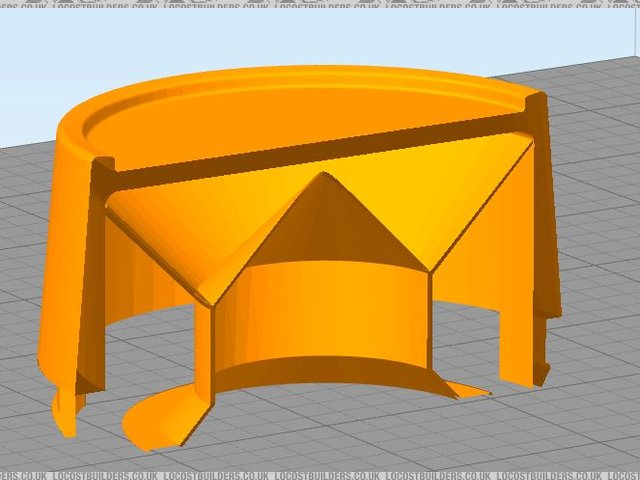 wheel_centre_custom_support
I'm going to put some holes through the top to give the adhesive something to stick to for the fury logo. Ill model the logo next
tonight/tomorrow and get it made.
Pete
|
|
steve m
|
posted on 13/7/20 at 05:28 PM |
|
|
Only an idea, and I know 100% of nothing about 3d printing, !!
If you were to have a central shaft of say 10 mm that was around 100mm long, you could spin them on a drill to clean the outside up to an acceptable
finish, and then break the shaft off ?
as said, only an idea
steve
Thats was probably spelt wrong, or had some grammer, that the "grammer police have to have a moan at
 
|
|
watsonpj
|
posted on 13/7/20 at 08:32 PM |
|
|
yep that would work but as its not a plastic moulding the inside and outside walls don't need to be parallel so i can pop it on the lathe as the
inside faces are parrallel whilst the outer ones are angled.
|
|
BenB
|
posted on 13/7/20 at 09:14 PM |
|
|
PETG sands and polishes quite nicely in my experience. Should make it look reet good.
|
|
watsonpj
|
posted on 13/7/20 at 10:54 PM |
|
|
OK centre logo is modeled now and it looks pretty good hope it prints as well.
The different colours are on different levels 0.2mm apart so should be able to paint then ok.
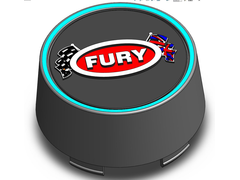 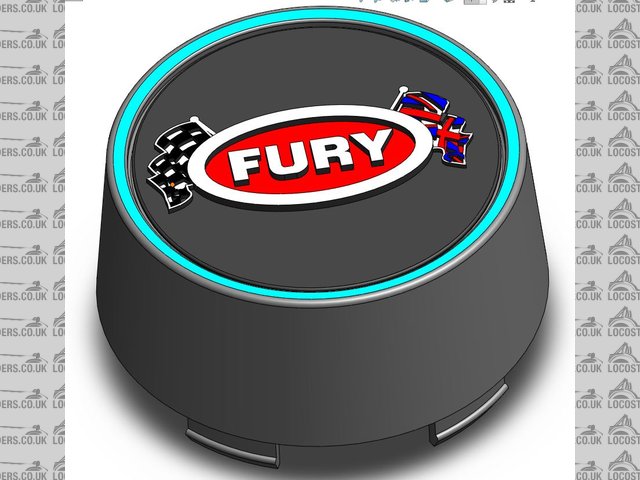 Wheel_cap_assy
will try tomorrow
|
|
tims31
|
posted on 14/7/20 at 11:16 AM |
|
|
quote: Originally posted by watsonpj
OK centre logo is modeled now and it looks pretty good hope it prints as well.
The different colours are on different levels 0.2mm apart so should be able to paint then ok.
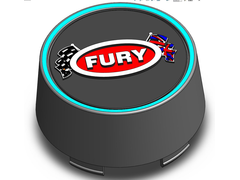 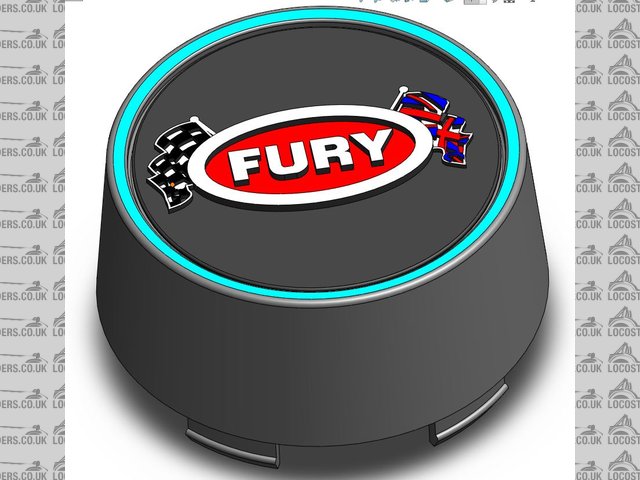 Wheel_cap_assy
will try tomorrow
Looking really good. I need to measure my wheels and get the design sorted for mine. I had a llook at the weekend and the rear center is very tight to
the washer that sits behind the nut. Could turn that down on a lathe I guess to provide some clearance. Fronts just need to be a flat cover rather
than a cap like this.
Build: http://www.martinsfurybuild.co.uk/
|
|