Bob C
|
posted on 14/1/05 at 12:47 PM |
|
|
I'm going to have to think about the watts link now - do the ends of the longrods need to be separated in height by the length of the middle
one... duh brain hurts... I'll get back on that one.
BT - I'm sure you could use rose joints - it's just that the axle vertical movement would describe a transverse arc (radius = panhard rod
length), rose joints would allow this, no stretching or chassis bending called for as long as all the trailing arms are equal length.
|
|
|
craig1410
|
posted on 14/1/05 at 01:09 PM |
|
|
Hi,
Just read the bit about fatigue cracking resulting from having rod-ends throughout the rear suspension.
As I have exactly such a setup, can you please elaborate as I can't see why you think this will happen. My suspension moves very nice and freely
(by hand) in all permitted directions and angles. I also have adjustable lengths on all 5 links to ensure that there are no static loads anywhere. I
just can't see where the fatigue cracks would come from.
I know my suspension will transmit road noice like crazy but I was under the impression that it would perform fine and didn't envisage any
safety issues.
Cheers,
Craig.
|
|
britishtrident
|
posted on 14/1/05 at 01:14 PM |
|
|
quote: Originally posted by Bob C
I'm going to have to think about the watts link now - do the ends of the longrods need to be separated in height by the length of the middle
one... duh brain hurts... I'll get back on that one.
BT - I'm sure you could use rose joints - it's just that the axle vertical movement would describe a transverse arc (radius = panhard rod
length), rose joints would allow this, no stretching or chassis bending called for as long as all the trailing arms are equal length.
With 5 solid joints Roll + bump causes torsion on the axle
|
|
Bob C
|
posted on 14/1/05 at 01:25 PM |
|
|
Yo BT - I need to think about that, clearly one of the trailing links is ostensibly "redundant" but I had this comfortable notion that as
long as they were all the same length it was OK. I can see I'll have to check this out on solidworks...... (3D geometry is just too hard)
BTW liked the morgan story - sort of fits well in a motor with "sliding pillar" IFS. Must have made a terrible racket on the road....
Bob C
|
|
gazza285
|
posted on 14/1/05 at 02:32 PM |
|
|
quote:
With 5 solid joints Roll + bump causes torsion on the axle
Only if you don't get the trailing arm links exactly the same length. If they are all the same length and the mountings are parallel it should
not induce any torsion, but you'll have no room for error, so I do agree that at least one end of the trailing arms should be compliant. No need
for rubber in the panhard rod though.
|
|
britishtrident
|
posted on 14/1/05 at 06:53 PM |
|
|
quote: Originally posted by Bob C
Yo BT - I need to think about that, clearly one of the trailing links is ostensibly "redundant" but I had this comfortable notion that as
long as they were all the same length it was OK. I can see I'll have to check this out on solidworks...... (3D geometry is just too hard)
BTW liked the morgan story - sort of fits well in a motor with "sliding pillar" IFS. Must have made a terrible racket on the road....
Bob C
The conflict of arcs is quite tiny not significant in a Locost.
The arangement on the Lotus Seven S4 had quite a nasty conflict of arcs that made it very stiff in role but it was thought by some Lotus guys the
best handling Seven.
|
|
Bob C
|
posted on 14/1/05 at 08:35 PM |
|
|
Gazza - you and me are wrong & BT's right - I just ran a quick solidworks model and as BT says, bump + roll twists the axle.
We live and learn!
Cheers
Bob
|
|
Bob C
|
posted on 14/1/05 at 09:00 PM |
|
|
I just checked out the watts link & yes you do have to vertically separate the pivots at the ends of the long transverse links by a distance equal
to the length of the middle link.
So now you know.
Cheers
Bob C
That's enough solid modelling for me. Time for a beer..
|
|
Volvorsport
|
posted on 15/1/05 at 12:46 AM |
|
|
could have told you that - ive had one beer too many tonight
www.dbsmotorsport.co.uk
getting dirty under a bus
|
|
Avoneer
|
posted on 15/1/05 at 12:56 AM |
|
|
Back to my problem for a minute....
Would it be ok to weld a 2" solid bar sticking horizontally straight out of the back of the trailing arm bracket, tap a hole down the middle of
it and then connect the panhard rod to this bracket using a tie rod with the bolt passing through the tie rod and bolting into the end of this
2"bar?
Hope that makes sense,
Pat...
No trees were killed in the sending of this message.
However a large number of electrons were terribly inconvenienced.
|
|
Marcus
|
posted on 15/1/05 at 10:15 AM |
|
|
Britishtrident,
Whilst I agree with most of your statement regarding axle location, I feel rose joints are the way to go. They have MORE lateral movement than bushes
as they are spherical bearings. The poly bushes are the worst, being almost rigid in the horizontal plane, causing the chassis to twist and eventually
suspension bracket failure.
Marcus
Marcus
Because kits are for girls!!
|
|
britishtrident
|
posted on 15/1/05 at 12:29 PM |
|
|
quote: Originally posted by Marcus
Britishtrident,
Whilst I agree with most of your statement regarding axle location, I feel rose joints are the way to go. They have MORE lateral movement than bushes
as they are spherical bearings. The poly bushes are the worst, being almost rigid in the horizontal plane, causing the chassis to twist and eventually
suspension bracket failure.
Marcus
While a rose joint has free angular movement in a 3 axis it lacks any compliance along the direction of the axis of the link, all that is required is
a tiny amount of compliance length wise in one or more of the links, with short travel suspension it isn't really a major problem.
The works Escort rally cars go round it by using a watts linkage mounted exactly in the centre of axle
[Edited on 15/1/05 by britishtrident]
|
|
Avoneer
|
posted on 15/1/05 at 12:33 PM |
|
|
Boo hoo hoo....
No one's answering my questions.
It is my post...
I'm popping my ball and going home...
                                 
You're all a bunch of good for nothing hijackers.
[Edited on 15/1/05 by Avoneer]
No trees were killed in the sending of this message.
However a large number of electrons were terribly inconvenienced.
|
|
Peteff
|
posted on 15/1/05 at 01:01 PM |
|
|
Boo hoo.
Why not extend the bracket out from the axle and bolt your panhard straight to it Pat? I didn't understand the tierod idea, can you draw it
out?
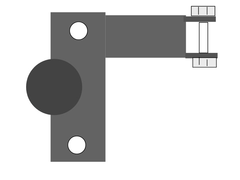 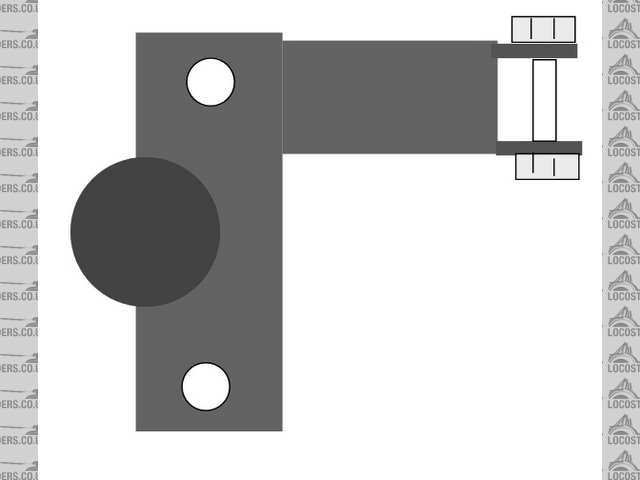 Rescued attachment hanger.jpg
yours, Pete
I went into the RSPCA office the other day. It was so small you could hardly swing a cat in there.
|
|
Avoneer
|
posted on 15/1/05 at 02:35 PM |
|
|
Hi Pete,
Excuse my crap drawings, but the idea is there - almost like yours, but with a rod end:
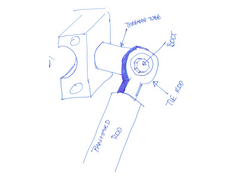 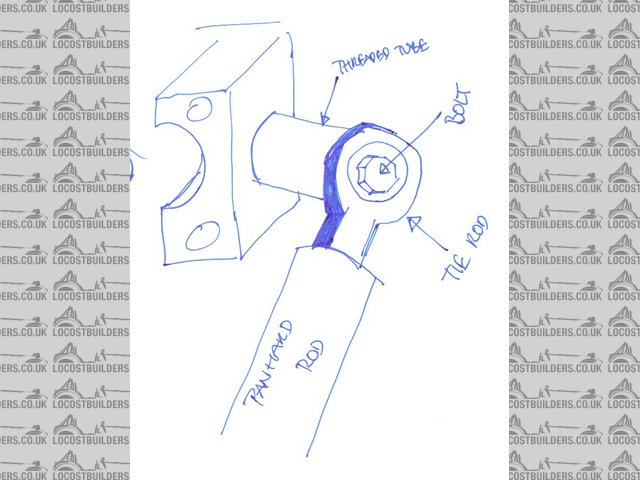 Rescued attachment 1.jpg
No trees were killed in the sending of this message.
However a large number of electrons were terribly inconvenienced.
|
|
Peteff
|
posted on 15/1/05 at 03:09 PM |
|
|
Mine uses a rod end but the other way on in double shear. You meant rod end not tie rod. You could use a square tube with a nut welded on a plate in
the end or weld a bracket to the underneath or the face.
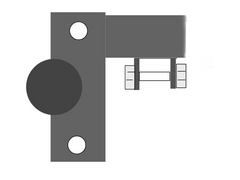 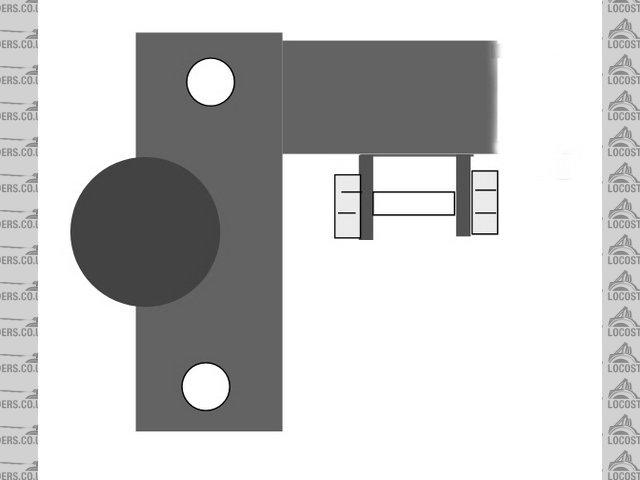 Rescued attachment hanger.jpg
yours, Pete
I went into the RSPCA office the other day. It was so small you could hardly swing a cat in there.
|
|
Avoneer
|
posted on 15/1/05 at 04:16 PM |
|
|
Just wanted to make it easy as I have a bit of threaded bar and it seemed to be the easiest solution????
No trees were killed in the sending of this message.
However a large number of electrons were terribly inconvenienced.
|
|
Jon Ison
|
posted on 15/1/05 at 04:34 PM |
|
|
this was strong enough to hold togethor and bend a half shaft when the car hit a "solid" object ????
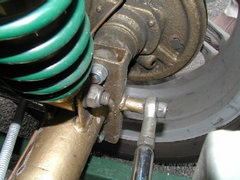 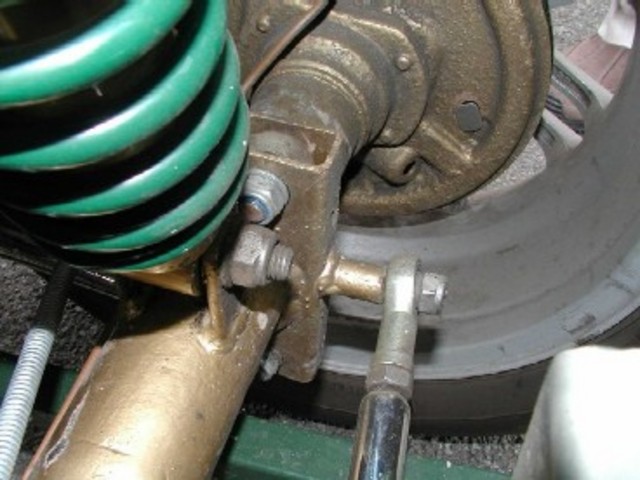 Rescued attachment rearpanard.jpg
|
|
Avoneer
|
posted on 15/1/05 at 05:41 PM |
|
|
Cheers john - wish I had known about your pic before trying to draw the bloody thing!
And if it won't fit in with the handbrake bar and cable, I'll just use a separate cable to each back plate.
Cheers,
Pat...
No trees were killed in the sending of this message.
However a large number of electrons were terribly inconvenienced.
|
|
JoelP
|
posted on 15/1/05 at 05:55 PM |
|
|
jons looks fine to me, plus he says it works well! If you were bothered, you could sleeve the threaded tube in a square bit, and triangulate it to the
axle - guaranteed not to fail then! (or at least, not to fail first!)
|
|