robertst
|
posted on 11/5/07 at 06:54 PM |
|
|
help... opinion needed!
i've partly finished making the de-dion axle and i wanted your opinion to see if its okay up to now. it still needs touching up (filing, tureing,
etc). do you see any problems with it? i include a pic of it mounted on the car.
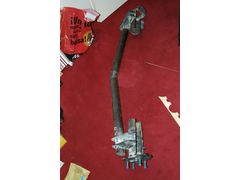 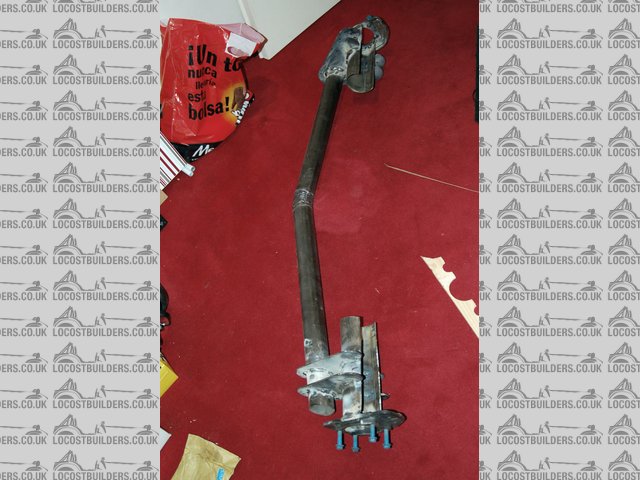 Description
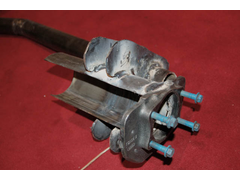 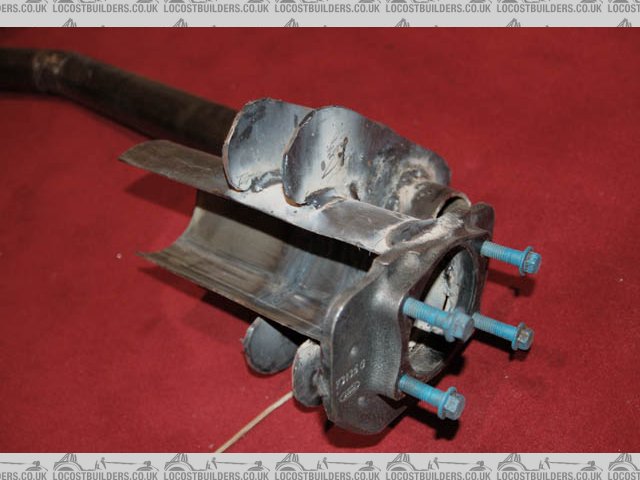 Description
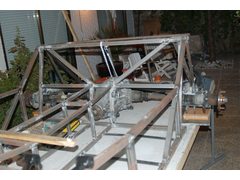 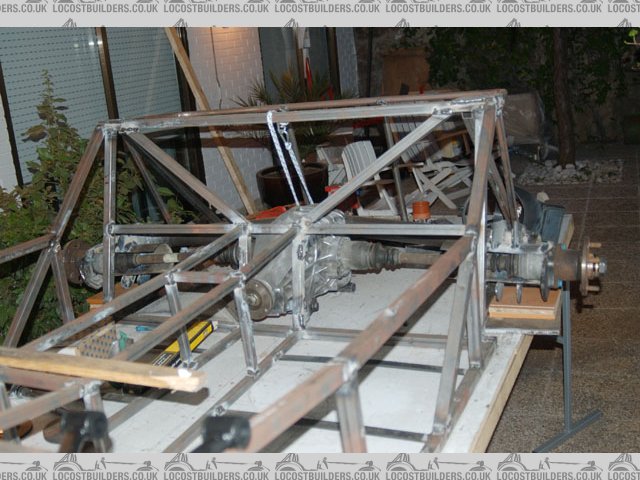 Description
please i need all the input you can give me to see what i need working on.... the hub tubes are like that as i didnt have the correct diamter tube at
the time so i used that. looks fine to me... what do u think?
thanks!
[Edited on 11/5/07 by robertst]
Tom
|
|
|
DIY Si
|
posted on 11/5/07 at 07:19 PM |
|
|
Have you cut and welded the middle bit of the de-dion? If so, any concerns over the strength? Also, the other bars I've seen have full tubes at
the hubs ends, so don't know what that'll do stiffness wise. I may be talking poo on those bits though. Otherwise looks good!
“Let your plans be dark and as impenetratable as night, and when you move, fall like a thunderbolt.”
Sun Tzu, The Art of War
My new blog: http://spritecave.blogspot.co.uk/
|
|
andyharding
|
posted on 11/5/07 at 07:45 PM |
|
|
I won't be having a ride in your car thanks. I don't think that DeDion is up to the job.
My DeDion is loads stronger than that and still flexes a bit.
I know I sound like a twat but if it stops you going throught a hedge I don't care.
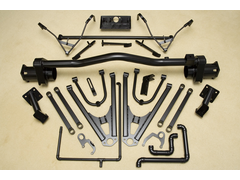 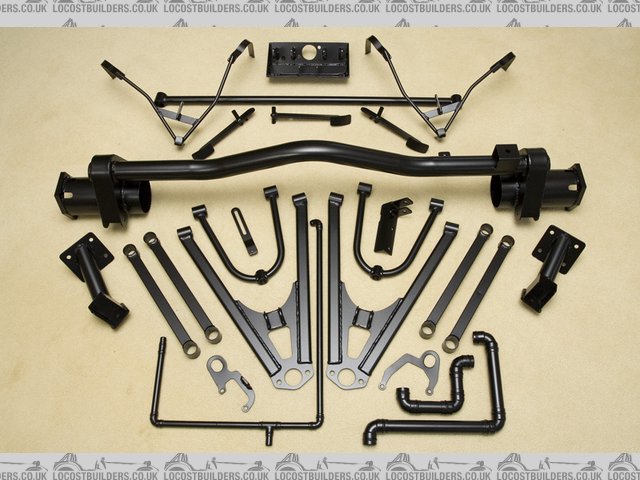 Powder Coated Parts
[Edited on 11/5/07 by andyharding]
Are you a Mac user or a retard?
|
|
JoelP
|
posted on 11/5/07 at 07:53 PM |
|
|
you cant really compare them without knowing materials used. Theres nothing inherently wrong with a welded axle that i know of, some people argue that
bent is the bad way to do it. I would be tempted to fillet and brace it here and there though.
|
|
oadamo
|
posted on 11/5/07 at 07:54 PM |
|
|
just test it then if it gos pair shaped just bodge it. thats what iam gonna do anyway lol
adam
|
|
JoelP
|
posted on 11/5/07 at 07:55 PM |
|
|
quote: Originally posted by oadamo
just test it then if it gos pair shaped just bodge it. thats what iam gonna do anyway lol
adam
a man after my own heart 
|
|
Mansfield
|
posted on 11/5/07 at 08:10 PM |
|
|
Can you show some close up pictures of the welds around the split tube to hub back plate. I think these welds need to be really good, but I may be
talking out of my back side. I am not sure that joint is an easy thing to weld well as the sections (and materials?) are very different.
Also close ups of the tube cut and shut may help judge your work.
|
|
ecosse
|
posted on 11/5/07 at 08:27 PM |
|
|
I'd be most concerned about the lack of support at the hub end to be honest, maybe you could add another plate at the end of DeDion tube, so you
would have 3 brackets connecting the tube and the hub carrier?
Does that make sense?
Cheers
Alex
|
|
tks
|
posted on 11/5/07 at 08:37 PM |
|
|
Mhhhh
Wy did you didn't curve that tube? instead of welding???
If you compare both pictures you see that
the plates in the good picture are unioned with sheet metal. making the plates look like a closed/solid part.
You will need that to on yours it will add allot of stiffness (horizontal way) vertically i see no problem if everything is fully welded sheet
thickness 3mm each minimum i guess...
Later on i would cut of some more pieces of sheet to brace the inner plate on both sides just 2 triangles shaped sheet should be enough.
Also some horizontal ribs on the tube weld with 20mm high will add allot put them on vertically for a bump on the road..
if you don't untherstand it just pm.
Tks
The above comments are always meant to be from the above persons perspective.
|
|
robertst
|
posted on 11/5/07 at 09:11 PM |
|
|
quote: Originally posted by tks
Mhhhh
Wy did you didn't curve that tube? instead of welding???
If you compare both pictures you see that
the plates in the good picture are unioned with sheet metal. making the plates look like a closed/solid part.
You will need that to on yours it will add allot of stiffness (horizontal way) vertically i see no problem if everything is fully welded sheet
thickness 3mm each minimum i guess...
Later on i would cut of some more pieces of sheet to brace the inner plate on both sides just 2 triangles shaped sheet should be enough.
Also some horizontal ribs on the tube weld with 20mm high will add allot put them on vertically for a bump on the road..
if you don't untherstand it just pm.
Tks
many thanks for the replies. i'm sorry i didnt mention it but you must understsand its not finished. obviously i'll finish joining the
plates with 3mm steel and will make and weld a triangle for the bendy part, i also have to finish more welding, so the axle is not finished.
i just wanted your opinions on the hub carriers and that split tube i did.
i made the axle following many guidelines from the forum. IIRC some people did the exact same procedure as mine to bend the tube (i.e. cut fillets,
bend, weld and reinforce with triangle shaped plate).
of course... dont for one moment think i'm not regarding safety, but i'm being forced to build my own axle due to the impossibility to get
one from the uk...
|
|
DIY Si
|
posted on 11/5/07 at 09:23 PM |
|
|
The middle of the tube, where you've welded can be made acceptable by welding in extra fillets above and below the tube. The main bit I'd
be concerned about is the split tubes at the ends, as this are the parts that transmit most of the force into the tube, so can't really move
much.
“Let your plans be dark and as impenetratable as night, and when you move, fall like a thunderbolt.”
Sun Tzu, The Art of War
My new blog: http://spritecave.blogspot.co.uk/
|
|
gazza285
|
posted on 11/5/07 at 10:03 PM |
|
|
quote: Originally posted by andyharding
I know I sound like a twat but if it stops you going throught a hedge I don't care.
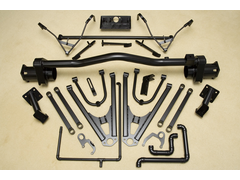 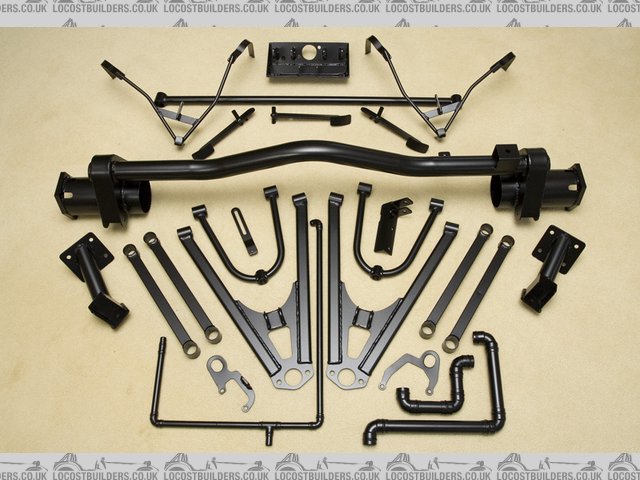 Powder Coated Parts
Well yours looks like exhaust pipe! To quote Joel "you cant really compare them without knowing materials used". Doesn't look too bad
to me, at least it's been done with a proper welder.
Some people on here seem to worry that a welded joint can not be as good as a bent joint, but I presume that is because they do not know what they are
talking about.
DO NOT PUT ON KNOB OR BOLLOCKS!
|
|
robertst
|
posted on 11/5/07 at 10:31 PM |
|
|
Tom
|
|
gazza285
|
posted on 11/5/07 at 11:05 PM |
|
|
What's this?
DO NOT PUT ON KNOB OR BOLLOCKS!
|
|
oliwb
|
posted on 12/5/07 at 07:50 AM |
|
|
Well done that man (gazza), if you look back into any welding books or even try to destruction test a "good" weld you'll find that
the parent metal gives up before the join. After all you are melting to bits of metal to form one and by adding filler your making it thicker and
therefor stronger! I would have no quams about welding the joint on a de-dion (and have). If anything it should be stronger if done right (even
without any gussets or braces).
For the original question, did you make a jig of the old axle to make it? The camber in the photo of it fitted to the car looks like its positive
rather than negative....could be a trick of the eye but I'd double check if I were you, unless you like coming off roundabouts backwards. Oli.
If your not living life on the edge you're taking up too much room!
|
|
andyharding
|
posted on 12/5/07 at 09:11 AM |
|
|
quote: Originally posted by gazza285
I stamped each trailing arm to indicate their positions when refitted.
Are you a Mac user or a retard?
|
|
Bob C
|
posted on 12/5/07 at 02:57 PM |
|
|
Just thought I'd share the thing that I would be most concerned about - you seem to have arc welded to cast parts (the outer flange thing)
Most other dedions cut this bit out of a piece of 10mm or 12mm steel plate.
I would further point out that that is the weld that's going tp get the most hammer out on the street.....
As above I don't know the materials & I'm probably wrong, but you did ask for opinions....
the rest looks fine - the sort of structure that will bend rather than break ;^)
Bob
|
|
tks
|
posted on 12/5/07 at 06:08 PM |
|
|
yupsz he is deffo right...
if thats cast iron then you better can cut the flange out of iron with water jet or with laser. If you need help pm me
Tks
The above comments are always meant to be from the above persons perspective.
|
|
oadamo
|
posted on 12/5/07 at 06:31 PM |
|
|
the flanges are welded to the arms anyway so i cant see a prob with cutting them off and welding them back on. i was thinking of doing it but there
looked like a lot off grinding so i gave it a miss. if anything just use 312 rods
adam
|
|
gazza285
|
posted on 12/5/07 at 06:51 PM |
|
|
More likely to be forged items, so welding not a problem.
DO NOT PUT ON KNOB OR BOLLOCKS!
|
|
tks
|
posted on 12/5/07 at 07:31 PM |
|
|
quote: Originally posted by oadamo
the flanges are welded to the arms anyway so i cant see a prob with cutting them off and welding them back on. i was thinking of doing it but there
looked like a lot off grinding so i gave it a miss. if anything just use 312 rods
adam
mhhh i know you can weld it with a high grade nikkel rod but i wouldn't recommend it to suchs a part.
Tks
The above comments are always meant to be from the above persons perspective.
|
|
oadamo
|
posted on 12/5/07 at 09:40 PM |
|
|
quote: Originally posted by tks
quote: Originally posted by oadamo
the flanges are welded to the arms anyway so i cant see a prob with cutting them off and welding them back on. i was thinking of doing it but there
looked like a lot off grinding so i gave it a miss. if anything just use 312 rods
adam
mhhh i know you can weld it with a high grade nikkel rod but i wouldn't recommend it to suchs a part.
Tks
312 for Dissimilar metals we use this at work for this type of thing so it should be ok it will be stronger then the mild steel rods
adam
|
|
robertst
|
posted on 12/5/07 at 11:23 PM |
|
|
that was a big worry at the time, a buddy of mine told me if it was cast iron, then i should forget to weld it as it would soon come apart.
whatever the case, i welded it and it went like any other metal i have welded as far as now.
im glad u pointed this out as i dont know anybody who has used the sierra hub adapters hence why i think they may not be suitable...
but then again i have found it impossible to make my own hub adapter and cut that bloody 80mm hole in 12mm thick iron! i went through two drills, and
three circular crowns and didnt even manage to finish the hole...
[Edited on 12/5/07 by robertst]
Tom
|
|
oadamo
|
posted on 13/5/07 at 09:08 AM |
|
|
if it was cast iron you could hear it crack when it starts cooling down
[Edited on 13/5/07 by oadamo]
|
|
robertst
|
posted on 13/5/07 at 04:58 PM |
|
|
dont remember hearing it crack when i welded it... does it crack visually too?
Tom
|
|