big_wasa
|
posted on 28/5/06 at 11:17 PM |
|
|
Spherical bearing question please ?
If I was making my own wishbones to use rose bearings I would pick 1/2".
Ace sports cars use m10 joints on theirs.
Q) Are these up to the loads placed on them by a 600kg Locost doing 100mph down some nice twisties. This has been bugging me.
Over to you experts  Image deleted by owner
|
|
|
indykid
|
posted on 28/5/06 at 11:25 PM |
|
|
i'm no expert, but i suppose it depends on the quality of joint.
as staniforth says in RARCS, a better quality joint of the same size is often stronger than going up a size to one of comparable quality.
without numbers, it's hard to quantify which would be better.
m8 would worry me for a road car, but m10 are probably boderline ok.
tom
|
|
nitram38
|
posted on 29/5/06 at 12:07 AM |
|
|
I have used 1/2" unf.
Finer threads give finer adjustment than metric. Also they are stronger. Probably why seatbelt fixings are fine threads. Go for the best quality that
you can afford.
|
|
Triton
|
posted on 29/5/06 at 08:55 AM |
|
|
Top quality imperial thread everytime
My Daughter has taken over production of the damn fine Triton race seats and her contact email is emmatrs@live.co.uk.
www.tritonraceseats.com
www.hairyhedgehog.com
|
|
flak monkey
|
posted on 29/5/06 at 09:18 AM |
|
|
Correct me if I am wrong (again) but the loads on the inboard joints of a wishbone are purely tensile and compressive. If this is the case M10 is
plenty big enough.
I coulnt find much data on rod end material or loads, and I have no catalogue here to look at so, using an 8.8grade bolt as a comparison. The UTS of
the bolt is about 800N/mm^2. Area of a M10 bolt is 56mm^2 (using a core diameter of 8.5mm). So the Tensile strength of an 8.8 bolt is about 4.5tonnes.
The shear strength is around a third of that.
As far as I am aware rod ends are made of a higher grade steel than 8.8 bolts. But even so:
You have 4 per corner, each with a tensile strength of 4.5 tonnes. So you could hang 18tonnes off one corner or about 6 tonnes in shear.. Plenty me
thinks!
David
Sera
http://www.motosera.com
|
|
nitram38
|
posted on 29/5/06 at 09:23 AM |
|
|
If you think that they won't break read this:CLICK
[Edited on 29/5/2006 by nitram38]
|
|
flak monkey
|
posted on 29/5/06 at 09:30 AM |
|
|
I posted a thread about rod ends in suspension a while back when we broke the FS car. This was due to being loaded in bending, which is not a good
thing at all...!
The best thing to use in suspension is spherical bearings. You have to build in your adjustment in other ways though.
David
Sera
http://www.motosera.com
|
|
Syd Bridge
|
posted on 29/5/06 at 09:36 AM |
|
|
I've put this a few times...
Most broken rod ends that I've seen, have done so because of excessive tightening of the locknuts. This can cause breakage without even going on
the track, just from overstressing the section between the locknut and wishbone body.
A 10mm rodend, of mediocre quality, will hold up 3 or more Locosts on its own. So, for wishbone ends are more than adequate.
Cheers,
Syd.
|
|
nitram38
|
posted on 29/5/06 at 09:48 AM |
|
|
Sorry, still prefer 1/2" UNF.
Wishbones do suffer side loads as well as the up and down movement, when you accerlerate, brake etc. 10mm seems a bit small to me.
If you look at the ariel atom they look like 1/2" rod ends.
I also recommend the use of safety washers if the bearing is not held within a bracket incase the ball race fails.
These are not sold in the UK, but can be made or bought from Pegasus racing in the US.
[img][/img]
|
|
big_wasa
|
posted on 29/5/06 at 12:28 PM |
|
|
Thanks for all the replies.
The Ace bones are already sat in my garage.
If I was making them I would go with the 1/2" unf just for piece of mind.
I didnt ask when I got them as I just asumed for strength and cost they would be 1/2". I got them at a great price ( thanks Zil )so I want to
use them.
What Syd says makes sense so unless a beter set of bones pops up or I make some I will use them.
Coming to think about it there must be hundereds of locost's out their that have the rubber bushes and 3/8" (9mm ish) bolts. Holding it
all together.
How can I tell the quality of the joints used ?
I can always up the quality before it goes on the road.
[Edited on 29/5/06 by big_wasa]
|
|
Bob C
|
posted on 29/5/06 at 01:19 PM |
|
|
I read a recommendation from a trusted source (prob, Nick Skidmore or John Beardmore on here) that teflon lined brgs of a particular sort should be
used.
Bad news is... I've forgotten...
Recap? please?
cheers
Bob
|
|
Viper
|
posted on 29/5/06 at 01:19 PM |
|
|
quote: Originally posted by nitram38
Sorry, still prefer 1/2" UNF.
Wishbones do suffer side loads as well as the up and down movement, when you accerlerate, brake etc. 10mm seems a bit small to me.
If you look at the ariel atom they look like 1/2" rod ends.
I also recommend the use of safety washers if the bearing is not held within a bracket incase the ball race fails.
These are not sold in the UK, but can be made or bought from Pegasus racing in the US.
  Description
was this picture taken at full droop? or ride height?
|
|
nitram38
|
posted on 29/5/06 at 01:26 PM |
|
|
No wheel, therefore at droop.
Go on, say it........the bearing is rubbing!
It doesn't once it is loaded.
|
|
Viper
|
posted on 29/5/06 at 01:39 PM |
|
|
i wasnt going to say it was rubbing, just that at anymore droop and you will bend/snap that joint.
and for the record my brothers silhouette uses 3/8 and 7/16 unf rod ends on all the suspension and that runs 10" slicks....
|
|
nitram38
|
posted on 29/5/06 at 01:53 PM |
|
|
I don't think that droop will snap the rod end as the joint is not under load. (apart from hub/wheel weight etc)
My car would need to lift 4-6 inches to be in that condition
It would risk snapping if it travelled the same amount in the loaded state.
It does not go that far loaded, so no problem.
My normal suspension travel is only 25-50mm on the rears. (rear shown)
[Edited on 29/5/2006 by nitram38]
|
|
JB
|
posted on 29/5/06 at 06:26 PM |
|
|
Spherical Rod Ends
The strength of rod ends varies a lot depending on quality. I am sure I have seen some 1/4" ones that are of a comparable strength to 1/2"
(top quality compared to very low quality).
I would always use a reinforced PTFE liner on my spherical bearings and I would always go for a larger joint than a smaller one mainly because it will
last longer due to having more surface area.
Good makes are NMB, Silverline and Goldline. Aurora and some of the USA manufacturers also supply good qualit in their range.
I used 1/2" bore on the lower wishbones, 7/16" on the upper and 7/16" x 1/2" high angle on the steering arms. The steering arm
joints are top quality and cost over £60 each. I used NMB E type, Silver and Goldline.
Mr Skidmore is a good source of bearings.
You should only really load rod ends in compression or tension and not bending. This is actually harder to do than it sounds and still get adjustment.
The wishbone shown on the top of the first page loads the rod ends in bending.
Using spherical bearings in a round housing welded to tube is a good structural solution but then you need to get clever to adjust the suspension,
plus making the housings is a real pain.
Safety Washers....... If you design to mount everything in double shear (as you should) then safety washers are not required. If you must mount in
single shear then a saftey washer is a good idea but the real solution is to mount in double shear. It takes effort but is structuraly the better
solution.
The subject of rod ends has been covered before so try a search.
John
|
|
Fred W B
|
posted on 29/5/06 at 07:46 PM |
|
|
Hi Nitram
Maybe I have misunderstood you, but I wouldn't be happy with the rod end acting as the droop stop on the suspension travel. The suspension will
go that low if the car goes over a bump so as to unload the suspension completely, and in my experience if you let a rod end run out off travel it
distorts the ball retaing part and starts to bind up.
I reckon the damper should be the droop stop.
While we are being pedantic, why did you not dress the edge of the flame cut parts the upright is made from? And no flat washers under the nylocks?
One more pedantic item. You can get what are called jam nuts, or half nuts, to use as the lock nut on the rod end. Take up less space, allow more
adjustment, and reduce chance of tightening the lock nut so tight as to stress the thread, as pointed out by Syd
Cheers
Fred W B
[Edited on 29/5/06 by Fred W B]
|
|
nitram38
|
posted on 29/5/06 at 09:16 PM |
|
|
You are looking at a build photograph, so what do you expect?
As to the flamecut comment, my car is a functional item, not some prissy hotrod.
Next someone will be complaining that it is not chromed!
I fail to see the engineering problem caused by undressed steel.
I built the car from scratch and with limited funds and very little available time. Some weeks I work 84 hours.
What I will say is that it is finished, which is a lot more than I can say about a lot of cars.
As to the bump comments, if the car leaves the ground by 4-6 inches, then I am really in it. It is not a rally car.
While being pedantic, why isn't your car in your avatar finished?!!!!!!!
I also fail to see how using a half nut will prevent fractures as you can still over tighten them too. The only advantage is a couple of more
milimeters of adjustment. (half nuts arent actually half size).
If you design your wishbones properly, then an extra 2mm adjustment is not important. (like mine)
If I did use half nuts as you suggest, then more thread would be showing beyond the nut and that too would create another weak point.
What advantage would a washer give you in this situation?
The bolt is a cap head and the nut is locked against the back plate.
I see that you didn't mention the purpose made, wedge shaped spacer washer between the rod end and the flame cut plate. Maybe something is
right?
It is a good job that they do not build statues of critics, otherwise you would not be able to get out of your front door!
I tried to help, but all I get is critisism.
Next time, just go ahead and fit your 10mm rod ends!!!!!!!!!!!!!!! 
From your archive:
 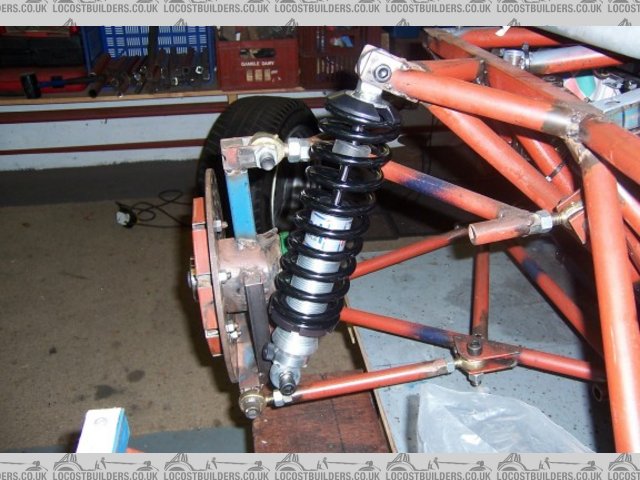 rough upright
Why have you used nuts welded on your wishbones for your rod ends? (or is it 2 nuts with 2 possible fracture points?)
Why didn't you use purpose made machined 35mm long bushes like my setup?
Oh, your threads look a bit long (must be the half nuts?)
A bit weak in my humble opion   
Why didn't you make nice cast uprights like I did instead of fabricating them?
It's not nice being critisised is it??????
[Edited on 29/5/2006 by nitram38]
|
|
MikeRJ
|
posted on 29/5/06 at 10:31 PM |
|
|
quote: Originally posted by nitram38
It's not nice being critisised is it??????
If it's constructive then it's perfectly ok by me.
Is you upright really cast? It looks fabricated in the pics above?
|
|
nitram38
|
posted on 29/5/06 at 10:57 PM |
|
|
What you can see is the adapter plate.
I made one upright design in order to only make one casting.
This means that they will fit on any corner. They have different adapters made in steel.
On the rears the plate picks up the third rod end. On the fronts the plate picks up the steering. Both steel brackets pick up the brake calipers.
Basically the adapter plates are upside down on the rears and up the right way to pick up ther steering arm.
Originally I made the uprights in LM20 but now they are cast steel with zinc plating.
Front:
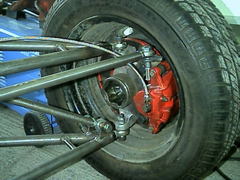  Description
Rear:
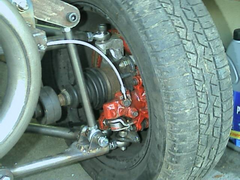 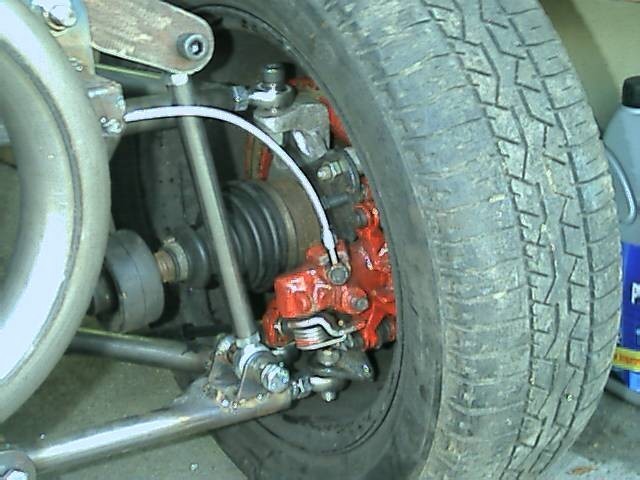 Description
You will probably notice that these are the old LM20 uprights, but also see that the rod ends do not bind in these photos!
There are also stronger webs on the pickup points (before I get flamed again!)
Here it is naked!
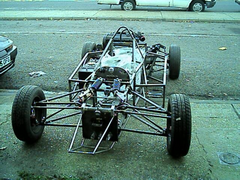 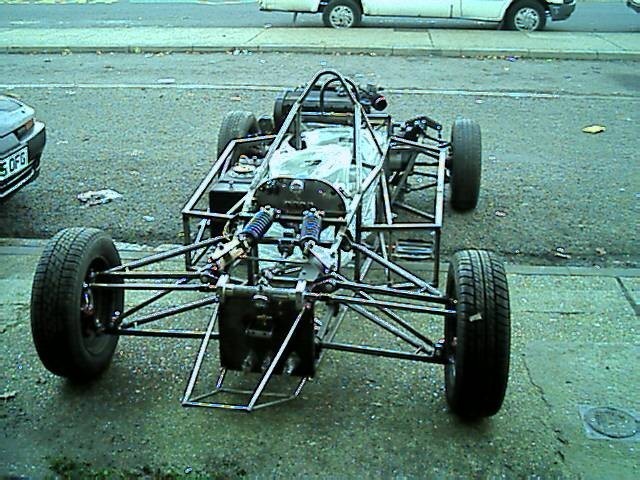 Description
[Edited on 29/5/2006 by nitram38]
|
|
locostv8
|
posted on 30/5/06 at 04:13 AM |
|
|
I know it is probably gross overkill but a rod end is the last thing I want to fail so will probably use these at least in the rear.
Krawler Joint
$30.00 Per Assembly for 3/4 Shank
$37.50 Per Assembly for 1.00 Shank
+/- 20 degrees
60,000 Pound Radial Load Capacity
8,800 Pound Axial Load Capacity
Rebuild Kits $5.00 (New Poly Races)
Fits Clevis widths of 2.375" or 2.750"
14 mm Bore
These are available from RockKrawler 518-270-9822. Gforce who are i the same building but don't have a phone # for has the same thing with a
smaller bore.
http://wrangler.rutgers.edu/gallery2/v/7slotgrille/hssss/
|
|
nitram38
|
posted on 30/5/06 at 01:01 PM |
|
|
I think that they use that size on stockrods, so it should never break!!!!!!
|
|
Fred W B
|
posted on 30/5/06 at 05:50 PM |
|
|
Dear Nitram
My apologies for the offence my comments have caused you. This forum is about exchanging information and opinions and I though we were having a
discussion. Rereading my post, I see that I could have phrased my points better, so please excuse me for that.
With regard to the questions you ask me:
Flame cut parts - To me, it is normal good engineering practice to deburr a flame cut edge that will be visible once a fabricated assembly (for a
car) is completed, purely on aesthetic grounds. Can we agree to differ? You could make a pure engineering theoretical case for the serrated edges to
be potential crack causing stress raisers, but that is not a problem in the thickness plate / load situation we are considering.
Why isn't my car finished? - Because it isn't . I've been working on it for just less than 2.5 years, and I only manage to get in about
10 hours a week at best on it. I am not working to a deadline. This is supposed to be a hobby, and I get enough stress at work.
Half nuts? - I prefer them just because they are shorter than full nuts.
Flat washer advantage? - Again, to me, this is just normal good engineering practice. Theoretically I suppose it could prevent the nut or tightening
tool damaging the protective coating on the part as the nut is tightened.
Your wedge shaped spacer washer? - Yes, it's a very nice detail. I am using machined straight spacers and separate flat washers, as shown
below.
10mm rod ends? - I have used 12mm.
With regard to your comments on the picture from my archive, that is of a very rough mockup I was using to sort out the geometry. See below for how
the uprights looked last week. I have since completed all the internal welding and tacking with MIG and they are now with a friend for the external
welds to be done with TIG.
Why have I used nuts welded on the wishbones? - That was just for the mock-up, the real wishbones will be made from 21.3od x 2.11wt Schedule 10
stainless tube, with machined inserts plug and fillet welded into the ends. You can see the detail in the pics below. I have also used this detail
inside the bottom of the uprights.
Why didn't I make nice cast uprights? - I though it would be too much trouble and expense, and I want to be able to modify the uprights if
necessary. Big respect to you for having castings made, fabricating mine from the 28 pieces is taking time.
Is it nice to be criticized? - No, but if you post pictures here you must expect comments. Further to me being a critic, if you look back to
this thread, you will see that I was amongst the first to welcome you to this
forum and compliment you on your project.
I hope we can continue to have friendly discussions on technical and other matters.
Best Regards
Fred W B.
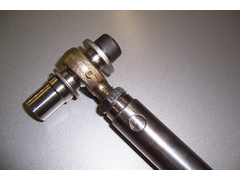 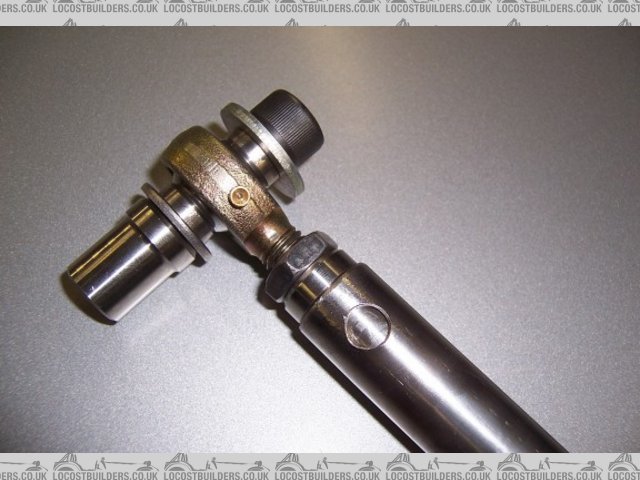 rod end detail
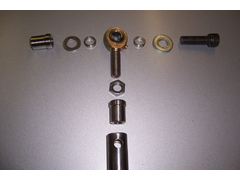 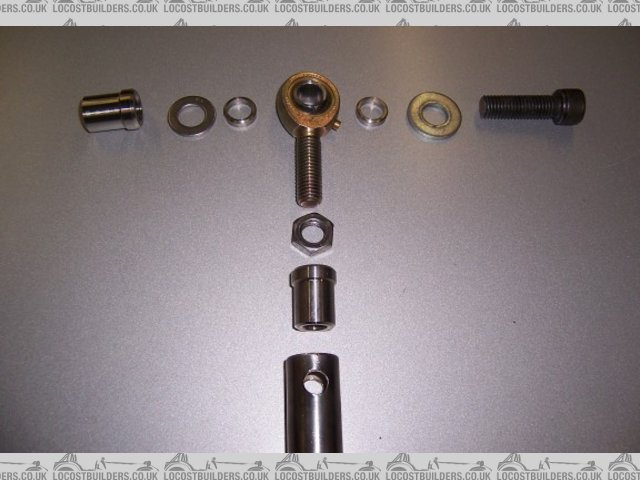 rod end exp
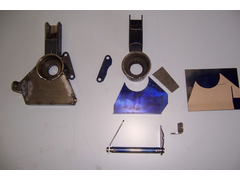 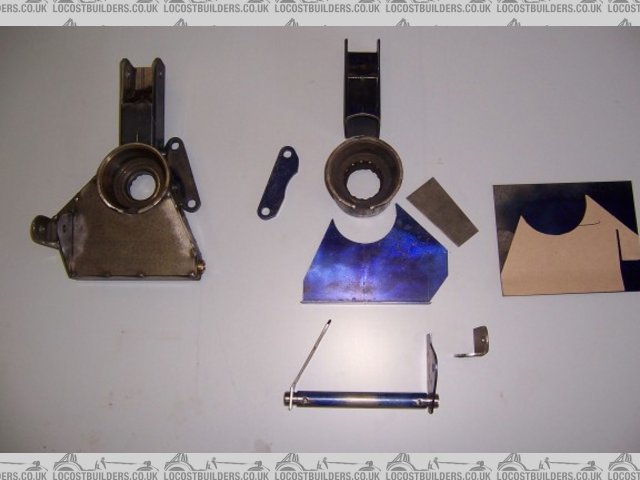 upright parts
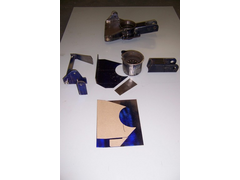 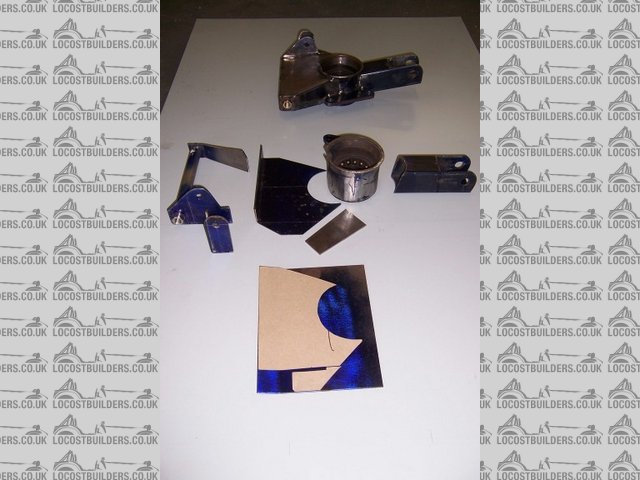 upright parts 2
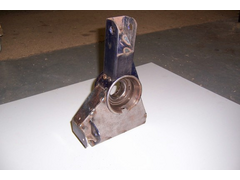 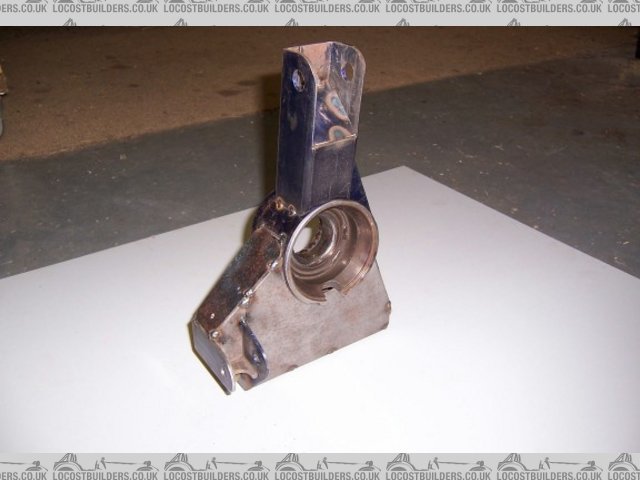 upright tack
[Edited on 30/5/06 by Fred W B]
|
|
locostv8
|
posted on 30/5/06 at 06:01 PM |
|
|
A couple of things I like is that the specs are double or better than the posted specs of others I've seen and many don't even post axial
load capacity.
They are also rebuildable and greasable.
They are a bit tricky to find on thier web site http://rockkrawler.com/
http://rockkrawler.com/spages/pages/tj_components.htm
As I said overkill but the rod ends are the last thing I want to fail.
http://wrangler.rutgers.edu/gallery2/v/7slotgrille/hssss/
|
|
nitram38
|
posted on 30/5/06 at 06:29 PM |
|
|
No problem Fred!!!!
Just ribbing you
|
|