v8kid
|
posted on 23/8/07 at 07:15 PM |
|
|
Engine to gearbox alignment
Aligning the gearbox to the engine is straightforward but repetitively boring – at least this way it is.
I made up a 19mm thick alloy plate to fit between the gearbox and engine and drilled it to suit the respective bolt holes. Even this was initially
more difficult than it sounds cos the bolt holes appeared at first sight to be randomly placed. I did it by standing the engine on its nose, roughly
lining up the adaptor plate and drilling one hole. I then made up a number of studs with a conical point on them, screwed them into the remaining
holes, and loosely bolted the adaptor plate on to the one hole already drilled.
By smartly striking the plate opposite the conical studs I was left with a series of centre punch holes corresponding to the remaining bolt holes.
Drill them out to size.
You can imagine my surprise when the plate lined up and bolted on to the block straight and square.
Repeat the sequence for the gearbox mounting holes and you have an adaptor that is, very roughly right.
It has to be very much better than roughly right though. According to Quartermaster it has to be a max of 6 thou run out (+-3 thou) and according to
Tilton 10 thou run out (+-5 thou). As an engineer the way Tilton word their specifications gives me more comfort but I fairly easily managed a
repeatable +-1.5 thou so it’s a bit academic.
First remove the flywheel and make sure the gearbox mounting holes have plenty clearance to allow you to adjust the alignment. Make up a bracket to
hold the dial gauge as shown in my photo archive under crank nose (how do you do that linky thing????)
Note the photo shows the spigot bearing in place just to support the dummy first motion shaft for the photo ‘cos I can’t gets the camera in when the
bellhousing is in place. You do not want the spigot bearing in place for these measurements or the result will be, as they say in Glasgow, mince. This
may be a good time to mention that the spigot bearing has to be extended by the thickness of the adaptor plate to support the first motion shaft. In
this instance it is slightly less ‘cos I was fitting a twin plate clutch. This required extra clearance anyhow.
Back to the dial gauge. It has to bear on the crank nose not the spigot bearing ‘cos they might not be absolutely concentric.
Look at the picture in my archive – dial gauge on input shaft – (I need to know how to do that linky thing!!!) to see how it will look just before you
assemble the box to the engine.
Careful when mating them as you could trap the dial gauge – I used a bit of thin cardboard as a ramp to ease the nose of the dial gauge over the crank
nose.
From now on it’s easy peasy. Rotate the first motion shaft through four positions 90 degrees apart and adjust the alignment until there is no, or as
near as no variation in the dial gauge reading.
Watch out for parallax. There are a limited number of openings in the bellhousing to observe the dial gauge and if observing from an acute or oblique
angle it is easy to misread it. I drilled 12mm holes in the bellhousing opposite my reading points so I was reading it square on.
When you are satisfied tighten all the bolts and recheck. If still the same drill at 3 equally spaced points through the bellhousing, adaptor plate
and block and insert alignment pins. I drilled with a 9.5mm drill and the holes were actually 9.65mm which required me making up pins to suit on my
lathe. If you don’t have these facilities get better drills than I.
Take it apart, reassemble and check. If you are as neurotic as I you will do this a few times.
My initial readings were +-0 my worst readings were +-1.5. Perhaps I’m not neurotic after all.
|
|
|
v8kid
|
posted on 23/8/07 at 07:38 PM |
|
|
.jpg)
|
|
v8kid
|
posted on 23/8/07 at 07:38 PM |
|
|
Damn modern technology
|
|
mark chandler
|
posted on 23/8/07 at 07:51 PM |
|
|
Pretty much the same as me then except I made my adapator by cutting off the front of and old RV8 bellhousing and welding onto the front of my Audi
box.
Again I used a bit of 16swg ali and a ball pein hammer to identify the middle of the crank on the engine then transfered this to the
gearbox.
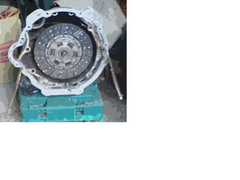 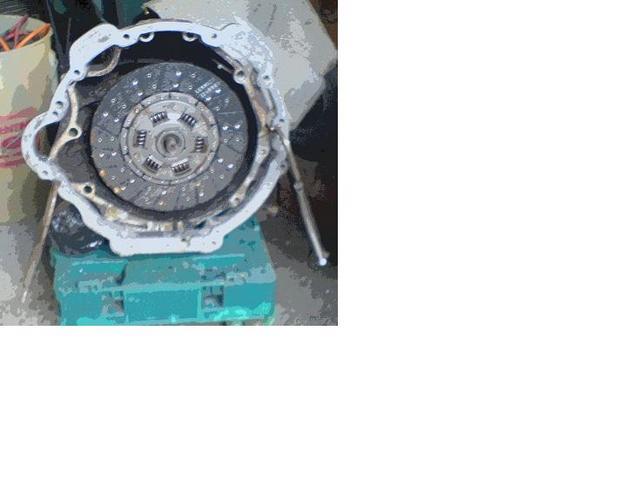 Rescued attachment Gearbox_adaptor_small.JPG
|
|
SeaBass
|
posted on 23/8/07 at 08:13 PM |
|
|
Interesting reading and indeed a good technique. I don't think you can be actually reading the run-out here though as the box input shaft would
be supported in the spigot bearing affecting the readings as the dial gauge fixture is attached to the input shaft - hence why they were pretty low. I
may have the wrong end of the stick?
Cheers
|
|
Mansfield
|
posted on 23/8/07 at 08:25 PM |
|
|
I thought exactly the same as you SeaBass, but rereading it the bearing was not in place for the measurements.
Unsupported my type 9 has about 0.75mm run out, maybe that gearbox has a more secure input shaft though.
|
|
nasty-bob
|
posted on 23/8/07 at 08:29 PM |
|
|
Out of interest, what engine and box are you trying to mate? (aimed at v8kid)
I'm going the cnc route myself- you can usually find drawings on t'internet for bellhousings or if not get it CMM'd.
Fair play for getting a decent result your way, I know from experience that this can be a ball-ache.
[Edited on 23/8/07 by nasty-bob]
|
|
v8kid
|
posted on 23/8/07 at 08:36 PM |
|
|
Sorry I should have said its a Rover V8 to an UN1 transaxle. The input shaft to the UN1 has been changed to a 1 piece shaft which makes alligning
easier. When I had the original 2 piece input shaft I alligned the clutch bearing guide tube to the crank nose but I was always wary about it
although, to be fair, it did not fail
|
|
nasty-bob
|
posted on 23/8/07 at 09:08 PM |
|
|
I've got co-ordinates for the later renault box (don't know the code). If its any use you can have to compare.
|
|