giel
|
posted on 20/2/04 at 09:42 PM |
|
|
what's wrong with it?
Hi everyone
I've been busy setting up a front suspension for the last weeks, I'd appreciate it if some of you want too take a glance at it and give
comments.
It's got full camber compensation, almost no track change because of the low RC, and the RC hardly moves up or down at 2 degrees. All looks very
good so far.
The only things that I'm concerned about, are the lateral movement of the RC (50 mm @ 2°) and the relative short SAL. Also the A-arms are very
inclined compared to other designs.
Most cars seem to have longer SAL and lateral RC movement is supposed to be a bad thing, but why??? Am I missing something?
BTW: the upper and lower A-arms are represented as the lines between the nodes, with the dimensions 275 and 380 attached.
[Edited on 20/2/04 by giel]
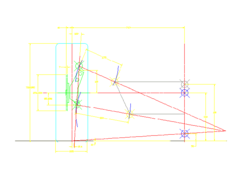 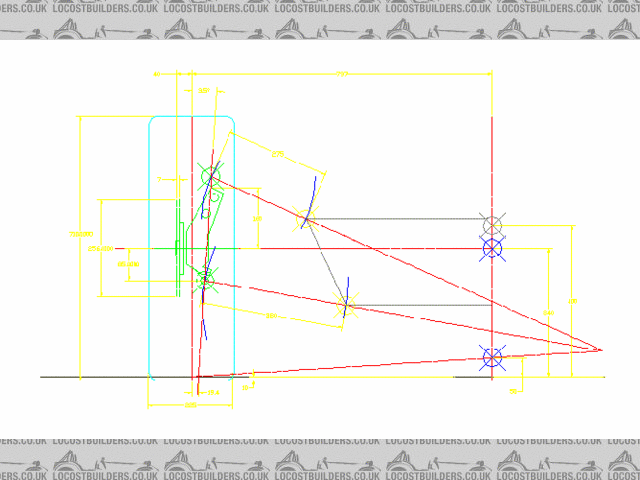 Rescued attachment susp3.gif
|
|
|
Hellfire
|
posted on 20/2/04 at 09:49 PM |
|
|
I started to read it but...
MY EYES! WHAT HAPPENED TO MY EYES???
Better colours would be appreciated...
(what's happened to my eyes?)
|
|
giel
|
posted on 20/2/04 at 10:10 PM |
|
|
sorry, this should be better...
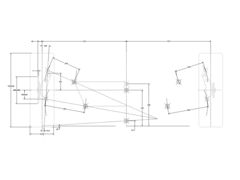 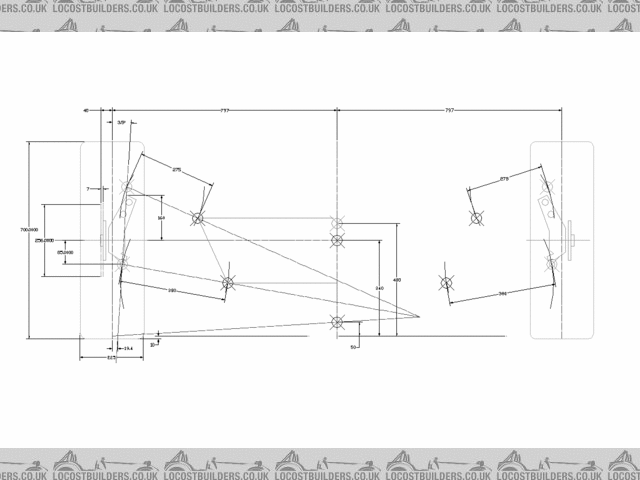 Rescued attachment susp5.gif
|
|
rontyler
|
posted on 20/2/04 at 10:17 PM |
|
|
How does it look in bump and roll?
|
|
GTAddict
|
posted on 20/2/04 at 10:26 PM |
|
|
Tyre diameter?
A 225mm wide tyre that's 700mm in diameter? To me, that's about 100mm too large.
This wouldn't matter, but it will affect the way you see your ground clearance - you'll think you've got 50mm more than you have.
To get some idea of good dimensions for your tyres, look at Toyo UK's excellent
website of Proxes T1-S sizes.
This may make you re-evaluate how much angle you have on your lower wishbone... not that I'm saying you're wrong...
Mark.
|
|
giel
|
posted on 20/2/04 at 10:34 PM |
|
|
quote: Originally posted by rontyler
How does it look in bump and roll?
I haven't checked bump+roll yet, just wanted to see if I'm on the right track. I do wonder why everybody always looks at the 1" bump
+ 2° roll situation.
to Mark: I know the tyre dimension isn't realistic, but I overlooked the fact that it's affecting my geometry. Good one, thanks.
I'll correct it.
any other comments, anyone?
|
|
rontyler
|
posted on 20/2/04 at 10:42 PM |
|
|
"I haven't checked bump+roll yet, just wanted to see if I'm on the right track."
Can't really say without at LEAST bump and roll.
I do wonder why everybody always looks at the 1" bump + 2° roll situation.
"
Partly becuase it looks like there would be significant scrub... and bump/roll will show it. Also it can show where the RC goes, swing arm length
changes, camber curves, etc.
Regards, Ron Tyler
"Nothing is ever accomplished by a reasonable man."
|
|
pbura
|
posted on 20/2/04 at 11:51 PM |
|
|
quote: Originally posted by giel
I do wonder why everybody always looks at the 1" bump + 2° roll situation.
Allan Staniforth used 1" bump + 2° roll as an acid test for evaluating a suspension with his "string computer", probably the biggest
reason.
Giel, I had a brainwave once, that if you assume an SAL and a roll center from the outset, all you then have to do is to find a spot for the upper
inboard pivot that keeps the RC steady.
Crappy drawing and explanation on my webpage
I also referred to a free suspension proggie that you can use to test out your setup:
http://www.racetechmag.com
It's wishbone.exe from the Downloads section, and you'll need Microsoft QuickBasic to run it.
In reality, one could avoid my drawing exercise practically altogether by plotting the lower chassis pivot, then 'fishing' with Wishbone
for the upper.
Hope this helps!
Pete
P.S. I have had no luck ever getting anyone else to try this, but it completely demystified wishbone suspensions for me 
Pete
|
|
ProjectLMP
|
posted on 21/2/04 at 03:10 AM |
|
|
I am certainly no expert in this area but this is what I do know. Generally you have two conflicting requirements with the suspension geometry.
Firstly, you want to keep the loaded wheel vertical (or even with some negative camber) when cornering i.e. the chassis is rolling. Secondly you want
to keep both wheels vertical when the suspension goes into bump. For the front suspension this assists under braking and for the rear under
acceleration. The problem is that the two requirements conflict with each other. Looking at your setup it looks like it will be good in the roll
situation but not so good under bump. F1 type suspensions with long swing axles optimize camber in bump at the expense of roll. However, they
don't roll much anyway so its less of an issue.
One reason the combined bump/roll situation is analysed is because this is the attitude a car takes when a car enters a corner following a brake zone
(when driven hard on the track)
Another important point to keep in mind regarding camber compenstation is that different tires have different requirements. Some like a more negative
camber (Radials) and some don't need as much (Bias-ply). Also the shape of the tire also effects this. Generally, tires with rounded edges
require more negative camber than ones with square edges. Take a look at the difference in static negative camber a Michelin F1 tire has vs a
Bridgestone.
I think the reason the lateral rollcentre location should not move too much is that it changes the degree to which the chassis will roll. Take as an
extreme case where the rollcentre is located right where the loaded tire is. In this case there would be a higher roll resistance than if it was
located at the centre of the car. So if the rollcentre moves all over the place the car may not feel progressive when cornering.
End of my ramblings. Just for info:
For my front suspension from 0 to 1 degree of roll:
Rollcenter height changes by 0.040"
Rollcenter moves 3.8"
Track changes 0.002"
Maximum positive camber (assuming 0 static camber) is 0.75 degrees.
[Edited on 21/2/04 by ProjectLMP]
Home of the Astronomicalcost Mid engined LMP project
|
|
cymtriks
|
posted on 21/2/04 at 11:34 PM |
|
|
I think that what you are missing may be that the contact patch has low stability in bump. A long SAL trades roll stability for bump stability. Making
an estimate based on camber change in bump the Elise has SALs of about 170 inches at the front and about 115 inches at the rear. From memory this is
close to a suggestion given in the Costin and Phips chassis book
[Edited on 21/2/04 by cymtriks]
|
|
Spyderman
|
posted on 22/2/04 at 05:05 PM |
|
|
Your setup can only ever give negative camber on bump and droop. Assuming wheel is setup with no camber at static.
The traditional method of having the lower wishbone level or slightly downhill from chassis is to optimise the camber change when cornering. As your
lower arm can only move outward as it moves down it is giving negative camber to the inside wheel when you ideally need positive.
Also, having the roll centres so low gives more roll leverage. Keeping the roll centres nearer to the COG will help reduce roll.
Terry
Spyderman
|
|
kb58
|
posted on 22/2/04 at 05:43 PM |
|
|
quote: Originally posted by Spyderman...Also, having the roll centres so low gives more roll leverage. Keeping the roll centres nearer to the
COG will help reduce roll.Terry
It's all a trade off. If you put the roll center the car won't roll at all! A good thing? Well, no, because you then have no way to
tune the suspension. If the car never leans, changing sway bars, springs, and shocks won't have any effect...
You need the car to lean some... which argues for placing the RC below the CG by "some amount."
|
|
rontyler
|
posted on 22/2/04 at 06:31 PM |
|
|
...and, if memory serves, high RC's made Ralph Nader famous ;-)
|
|
cymtriks
|
posted on 22/2/04 at 10:05 PM |
|
|
RC heights
Just for your interest
Elise RCs
front 30mm
rear 75mm
Experimental independent rear Caterham7 RCs
front 30 mm
rear 65 mm
I have done some analysis of suspension geometry and some odd effects appear with very low RCs and high roll. This might explain why even F1 cars
rarely go below 20mm at the front even with virtually zero roll and suspension movement.
|
|
giel
|
posted on 22/2/04 at 10:08 PM |
|
|
Thanks people, your replies have pointed some things out for me that I'll have to work on. Who said it was going to be easy, right?
Before I return to the CAD system, some remarks to a few of you:
Ron: "Partly becuase it looks like there would be significant scrub...".
There's actually very little scrub, at least up to 2° roll. I believe there will never be much scrub as long as the RC is low.
Pete: " if you assume an SAL and a roll center from the outset, all you then have to do is to find a spot for the upper inboard pivot that
keeps the RC steady "
I think I understand your method, but how do you, at the same time, keep your camber the way you want it?
ProjectLMP: "I think the reason the lateral rollcentre location should not move too much is that it changes the degree to which the chassis will
roll. Take as an extreme case where the rollcentre is located right where the loaded tire is. In this case there would be a higher roll resistance
than if it was located at the centre of the car. So if the rollcentre moves all over the place the car may not feel progressive when cornering.
"
I don't understand. How does the roll resistance get higher when the roll centre moves to the side? And would you say that your 3.8" is a
low or high migration?
Syderman: " Your setup can only ever give negative camber on bump and droop. Assuming wheel is setup with no camber at static. "
I don't agree. As long as my IC is on the inside, the wheel will go in positive camber on droop. The CAD model showed full camber compensation
on the inner as well as the outer wheel.
Anyway, it's clear to me that I'll need a compromise between cornering- and braking grip. Although a mid-engined car brakes a lot on the
rear axle too, it's something to consider. I'll get back to work and let you know what comes out. Maybe I'll start with the rear
suspension first, it might be a bit easier.
|
|
GTAddict
|
posted on 22/2/04 at 10:33 PM |
|
|
If you compress the suspension while also in roll, then you might have a problem with inner wheel camber. This probably isn't a worry for you
with the front - braking heavily under cornering isn't the best way to drive a mid-engined car if you want to stay facing the right way.
quote: Originally posted by giel
Maybe I'll start with the rear suspension first, it might be a bit easier.
However a similar design for the rear might be trickier if the inner goes into severe negative camber under acceleration. If you don't have an
LSD, you'll risk spinning away power as you go away from the apex.
This is why Mallock always stuck to his solid rear axle. An old article about linkages for solid rear
axles here, in case you're going that way.
Mark.
|
|
pbura
|
posted on 23/2/04 at 02:09 AM |
|
|
quote: Originally posted by giel
Pete: " if you assume an SAL and a roll center from the outset, all you then have to do is to find a spot for the upper inboard pivot that
keeps the RC steady "
I think I understand your method, but how do you, at the same time, keep your camber the way you want it?
It's a bit hard to tell on my drawing, but I actually drew three wheels: (1) static, (2) inboard wheel where I wanted it (no camber change) at
1" bump + 2° roll, and (3) outboard wheel (also where I wanted it with a -1° camber change) at 1" bump + 2° roll.
Note that I didn't get what I wanted in the unloaded wheel. This was physically impossible, so I went for correct camber on the loaded
wheel.
I'll confess cheating a bit, because I first drew up a book Locost suspension and found that it had an 80" SAL, so I used that. This fell
into the low end of the moderate range as opined by Allan Staniforth in his 'Race and Rally Car Source Book'.
My desired outcomes for camber change were also heavily influence by data in the Staniforth book.
I strongly recommend the (free) Wishbone program I mentioned, or the also free) Suspen program available at
http://users.erols.com/smitch/Suspen/. That way, you can step your design through bump and/or roll cycles to see how it behaves. I like
the layout of the Wishbone program myself, though you have to monkey around with steering pivot locations a bit to negate bump steer.
You'll find that short SALs give good camber control in roll, but suffer in bump, and vice versa for long SALs. Roll center locations are also
more sensitive with long SALs.
The whole process really is the epitome of compromise. 
I suggest that you design the front first, because it's the hardest to get right. Then for the rear you can just raise the RC a bit.
One more subject you might want to think over is that of weight transfer, as alluded to by Messrs. ProjectLMP and kb58. Ideally, IMO, with typical
Locost springing, you would want to limit roll to about 2° in a 1G turn. If you don't want to use anti-roll bars, this will determine where
your RC needs to be.
Some mind-expanding/blowing material here:
http://www.smithees-racetech.com.au/

Pete
Pete
|
|
kb58
|
posted on 23/2/04 at 03:39 AM |
|
|
Keep in mind that after you've analyzed this to death, figured out EXACTLY where the pickup points must go, that you'll be lucky if
they're within 1/16" of the target... and 1/8" movement during welding is extremely common.
In otherwords, don't kill yourself trying to make it perfect, there is not such thing.
|
|
Tudor (Ted) Miron
|
posted on 23/2/04 at 01:22 PM |
|
|
Hello Giel,
There are many good suggestions in this topic. I’ll try and take it more practical and add some of my thoughts.
First it would be very helpful if you give dimensions of your suspension in X, Y, Z - X (for- aft) measured from axle line (we don’t care about X for
now), Y (width) as dimensions from car centerline and Z (vertical) measured from ground plane. Obviously we need lower and upper arms inner and outer
pickup pints. Also we need track width and tire diameter. Than I’ll be happy to check it out and may be give some suggestions.
Assuming your choice of RC height = 50mm. First we want RC to move about the same as CG in bump i.e. chassis is lower 1” than RC is lower by as close
to 1” as possible.
Than we want RC to stay stable vertically in roll and than stable laterally in roll.
Now why we do bother about RC migration? First is because certain amount of sprung lateral weight transfer (WTrc) is via RC: WTrc = RCHeight: Track.
Main thing is Roll moment arm – distance between RC and CG. As this is impossible (and undesirable) to keep RC height constant with sprung mass
moving up and down it’s possible and desirable to keep this moment arm constant or closely so as this will have major effect on axle roll resistance
and dynamic weight transfer. This is why lateral RC migration can be important – if it moves considerable amount towards inner tire than moment arm
length changes increasing roll resistance and WT at this axle. This is used widely in oval track racing as major tuning tool.
If it all was so simple than our life would be much easier yet not that interesting. So once again why we do bother about RC migration and its
influence on WT? It’s because it influence the loads and forces acting on tire contact patch – the only thing that really matters. Tire is VERY load
sensitive device i.e. amount of lateral force that tire delivers vary largely with load (as well as many other things). When cornering reaction force
at the tire acts through RC. If RC is not exactly on ground plane this force will have two components vertical and lateral. In case of higher than
ground RC vertical component is “jacking” sprung mass – famous jacking effect.
(This is actually more complicated as in true forces are acting through instant centers and may be different at inner and outer wheel) This jacking
effect may have MAJOR effect on tire loads – usually bad. Explanation is long but late studies showed that its effects are not VERY significant with
relatively low RC – 2” or less. If resources are not of same level as Williams F1 and we can’t make infinite amount of simulations and on track
testing it is usually desirable to have relatively low RC so to minimize jacking effects. F1’s are playing some very strange games with RC – like
having it VERY high with huge jacking forces - they use it to support stable aero platform – very complicated and hard to get right. I prefer
slightly lower than ground front RC and little higher than ground rear. This is an easy way to get in Ball Park. Easy to set up and not very front
ride height sensitive.
Ted
|
|
pbura
|
posted on 24/2/04 at 07:38 PM |
|
|
quote: Originally posted by Tudor (Ted) Miron
I prefer slightly lower than ground front RC and little higher than ground rear. This is an easy way to get in Ball Park. Easy to set up and not very
front ride height sensitive.
Ted, out of curiosity, are you going to use anti-roll bars front and rear with that setup?
I'm also curious as to how your design's going. Please ramble on at will or set up a new topic of you like
Pete
Pete
|
|
Tudor (Ted) Miron
|
posted on 24/2/04 at 08:36 PM |
|
|
Hi Pete,
Yes I'm going to use ARB's front and rear. With all their shortcomings they ARE very valuable tuning tools - first of all fast and easy.
In single seater (and sports racer could be considered a close brother) it's common to give 40% and more of total roll resistance to
ARB's. Lower than ground front RC requires much stronger ARB but well known CART engineer says that thinking of it as a handicap is wrong.
I know one VERY succesful race car with - 0.7" front RC and NO ARB!
Also in last 4 -5 years wheel rates raised massively - at list in higher echelons of racing. This became possible as dampers internal friction was
decriesed very significantly. You'll be surprised how "soft" are current state of the art dampers (Ohlins, Penske)
Design is going nicely - Suspension modelling is done for now... I'm burried in CFD atm. It will be a true tunnel car - not a conventional
flat bottom with diffusers. It seems that full length tunnels give much less pitch/rideheight/roll sensitive results. As I planned car has 2
configurations build in. 4" ride height for street use and 2" for track use. Well there are actually 3 configs. When go from track
trim to road trim and not changing arms pickup points I get 1" front and allmost 3" rear RC. Still one has to change rack location (4
bolts) and pushrod to bellcrank - 4 more bolts (2F, 2R) Changing this will change motion ratio from 1.15 to 0.75 which changes wheel rate allmost
twice.
If one is not lasy he should proseed to change lower arm outer point and upper arms inner points and get allmost same geometry as in race config. So
there's virtually 3 cars in one. I should also mention that in race trim there is some serious downforce - requiring for much higher wheel rates
than road trim.
Sorry for messing this thread
Ted
PS: As usually - sorry for my English
|
|
Tudor (Ted) Miron
|
posted on 24/2/04 at 08:42 PM |
|
|
Hey Pete - just saw you're mantioning Dale Thompsons web site - he's a nice guy
Ted
|
|
rontyler
|
posted on 24/2/04 at 09:03 PM |
|
|
"Now why we do bother about RC migration? First is because certain amount of sprung lateral weight transfer (WTrc) is via RC"
Ted,
I've always understood the implied importance of a stable RC. What I don't get is that, traditionally speeking, damaper rates
differ dramatically with respect to rebound to compression ratio. My point? How can the geometric RC be followed when there is such a wide variance in
"wheel rate" (side to side)? In other words, during a transitional manuever, it seems that the geometric RC would have pretty minimal
influence due to the rebound rate on the inside wheel being significant and the outboard compression rate being minimal (relatively speaking). Can you
"set me straight" on my thinking?
TIA
Regards, Ron Tyler
"Nothing is ever accomplished by a reasonable man."
|
|
pbura
|
posted on 24/2/04 at 10:14 PM |
|
|
quote: Originally posted by Tudor (Ted) Miron
Hey Pete - just saw you're mantioning Dale Thompsons web site - he's a nice guy 
The Smithees site? Well, I can believe that he is, as he's put a lot of valuable stuff on his page for free. He seems to have a first-class
operation.
Thanks for the update on your project. Sounds like you're learning a lot and really going for something innovative and seriously competitive.
All the best,
Pete
Pete
|
|
Tudor (Ted) Miron
|
posted on 24/2/04 at 10:33 PM |
|
|
Ron,
First I have to say that I'm not an "expert" - all I'm saying is not nessecerally right. Lets take a simplifyed
transitional manuver car turning at decreasing radius corner at constant speed. Let's assume that at begining it wasn't cornering at max
speed and with less radius it does reach max cornering limit. While roll angle is increasing dampers add their share to dynamic WT distribution. But
we should look at car as pair of roll couples - front and rear - differense in WT distribution between F and R axles influense it's behavoir.
So it's not really matters if Rebound and bump stiffnes is different because they both work on same roll couple. Also to my understanding
dampers mostly determine not how much weight is trnsfered but how fast it is transfered. Another thing is in racing we don't usually see that
big difference in bump and rebound forces as in "normal" street car.
I'd say that here's is another reason for low RC - we may like to minimise "geometric" WT and maximise it's part that
is going through springs and bars.
Hope I didn't confuse it further
Sertanly my "English" doesn't help.
Ted
[Edited on 24/2/04 by Tudor (Ted) Miron]
|
|