derekbruceyoung
|
posted on 14/9/21 at 04:13 PM |
|
|
And now for something completely different... LeafZX bike engine augmented hybrid
Hello BEC Locosters!
I am working on something pretty different, but it shares a lot in common with your mid-engined BEC builds.
Starting with a $5k 2013 Nissan leaf with a pretty sad battery (~40 miles range), I'm keeping all the EV componentry in place while adding a
little ICE boost in the form of a 2009 ZX10R engine powering the rear wheels, creating a 300hp AWD DIY hybrid with a 13K redline and sequential box of
course. I completely understand that this isn't to everyone's taste and the Nissan Leaf is objectively an ugly non-performance car. But
this is being done as a proof of concept build for future projects using a similar hybrid drivetrain and MAY be one of the easiest ways to get a BEC
on the road (in California at least). Reverse: solved (via EV powertrain), no need for a big bore 'busa motor or off the line torque/clutch
torture (again because EV), emissions (what emissions?), quiet when you're driving through neighbourhoods (nice!).
To make this work mechanically, I'm taking a complete Gen2 Lexus IS rear subframe, and will be mounting the engine on it directly above a Quaife
chain drive differential (using a Honda Civic based one). Because of this arrangement the chainline is more complex than your average BEC build.
To help with the design I followed the lead of one of my favorite youtubers and fellow mechanical egineering & BEC enthusiast Superfastmatt and
started with 3D scans of all the components. This has been a revelation and has allowed me to spend a bunch of time figuring out things in advance
before cutting any metal.
I've designed a cradle from laser cut 3/8" 6061 that supports the front corner of the engine and manages the chainline and supports the
differential. This will bolt up to the rear subframe that will have welded structure to support the engine in 3 other spots. I've run FEA
based on expected peak chain loads and everything is looking pretty good with >4X factors of safety and minimal deflection.
The output sprocket is a 5/8" offset 15T, the idler is 18T with dual 25mm bore bearings riding on a hollow 25mm shaft, the output sprocket is
and aluminum 56T and rides on 40mm bore 80mm bearings which are in machined bearing mounts that are spaced out from the main plates. The final
sprocket is a tensioner to take up slack -- 15T on single 17mm ID bearings cantilevered off an idler mount made of a pair of 3/8" 6061
plates.
https://imgur.com/6vbZ6NQ
https://imgur.com/h89xlyg
https://imgur.com/OkZc9XW
Now on with the questions:
1) Any glaring gotchas from this design?
2) The 5/8" offset sprocket has me a little worried about loads on the engine output shaft, although the vendor (PBI sprockets) didn't
seem to think I should be worried. I considered designing a support bearing, but as I'm trying to make it easy on my self, the car probably
won't see a ton of miles (and have a spare engine available if things go really wrong), I'm currently feeling like taking the risk.
3) Hybrid halfshafts -- is there a way around having scratch built custom axles made? Have people successfully cut-and-welded two different CV
halfshafts together (in this case Lexus outer + honda inner) in 1000cc bike engine applications? The internet has mixed feelings on this. I'm
almost willing to risk it, but I'd have to have someone do the welding anyway so maybe I should just do it right the first time with custom
splined axles.
I will be posting more about this project as things develop, but I'd love to hear experienced peoples thoughts on what I'm up to! Happy
to answer other questions about the build as well, as this ICE engine driveline portion is just a small part of it!
If you want to see it all, I have an active google photos album that I just dump everything relevant into as I go along.
https://photos.app.goo.gl/hBUezQtiCVuvTPQ99
|
|
|
HowardB
|
posted on 14/9/21 at 08:28 PM |
|
|
That is certainly different.
I like the design before cut approach.
My questions would be how far back does the ev battery pack go and will the subframe need more space than the previous rear arms?
Otherwise... Good luck and welcome to the home of some really knowledgeable people.
Howard
Fisher Fury was 2000 Zetec - now a 1600 (it Lives again and goes zoom)
|
|
derekbruceyoung
|
posted on 14/9/21 at 09:05 PM |
|
|
quote: Originally posted by HowardB
That is certainly different.
I like the design before cut approach.
My questions would be how far back does the ev battery pack go and will the subframe need more space than the previous rear arms?
Otherwise... Good luck and welcome to the home of some really knowledgeable people.
Thanks!
The pack ends at the end of the rear seats, and I'm keeping well away from it -- this is a reason the Leaf was chosen over say a Fiat 500e,
which while more sporty and better looking has batteries in the trunk. I had thought about having the bike engine further forward but I don't
want the exhaust anywhere near the batteries for obvious reasons. The rear unibody will need extensive rework as two of the Lexus' 5 links does
foul the structure -- and the shocks are in a completely different locations than the Leaf units. The piece of angle that intersects the yellow
subframe is there to clear portions of the Leaf structure. The pink portions of the scan are the stock Leaf twist beam arms, which I intend to graph
onto the lexus subframe so that the stock front mounting points can be reused.
You can see the location of the battery in this cross section:
https://imgur.com/CJXvKvQ
[Edited on 14/9/21 by derekbruceyoung]
|
|
bi22le
|
posted on 14/9/21 at 10:11 PM |
|
|
Welcome to LCB. I love your ideas and it's great to see. Like the old good days when people were mad haters in their sheds. I hope you keep up
the enthusiasm to the end!
Most kit cars have some sort of cut down or hybrid half shafts. Mine for example are shortened stock Ford ones.
I broke one of them on a track day. While in the pits I took the car apart to get the shaft out, took it to a local agricultural welder and for £10 he
welded it back together on a bench the best he could. It's been fine since.
I would say to give it a go on the cheap. Keep the budget and head ache for somewhere else in your project. If you get everything going and working
with just your half shafts to be remade more sturdy, you have done bloody well!
Sleeve and cross pins are the way to go, that way if they do break they dont cause lots of damage.
Track days ARE the best thing since sliced bread, until I get a supercharger that is!
Please read my ring story:
http://www.locostbuilders.co.uk/forum/13/viewthread.php?tid=139152&page=1
Me doing a sub 56sec lap around Brands Indy. I need a geo set up! http://www.youtube.com/watch?v=EHksfvIGB3I
|
|
adithorp
|
posted on 15/9/21 at 07:24 AM |
|
|
Interesting project. How are you planning to tie in the bike engine throttle to the Leaf/EV controls?
"A witty saying proves nothing" Voltaire
http://jpsc.org.uk/forum/
|
|
russbost
|
posted on 15/9/21 at 08:57 AM |
|
|
A couple of negative comments, intended to be constructive - not criticism!
The height of the bike engine is going to give a higher CoG, whether it's enough to affect handling significantly I don't know & from
experience with chain drives the relatively complex setup you have with idler etc. may give you grief, only one way to find out really! I doubt the
5/8 on the output will give too much problem as you'll be reducing torque on that from the electric launch - once the battery has gone flat
don't be brutal with standing starts!
I made my own driveshafts on my original twin engined Furore build, cut the driveshafts to length, set them up between centres on a lathe with some
larger dia tube already slid over the shaft, tacked it up & checked for out of line rotation, once happy with that continued to weld opposite
sides until the vee I'd created was weld filled, then slid the tube over & seamed up each end - never damaged a shaft done that way &
that was using 2 x ZX10 1000cc engines one on each wheel (I did twist up an early shaft I'd used a kart axle on, the keyway was an obvious weak
spot allowing it to twist). The way I did it cost next to nothing & a few hours work, if you're paying someone else to do the setup &
welding it may not be much cheaper than custom shafts? Worth investigating?
Good luck with the project, will be interesting to see how it turns out
I no longer run Furore Products or Furore Cars Ltd, but would still highly recommend them for Acewell dashes, projector headlights, dominator
headlights, indicators, mirrors etc, best prices in the UK! Take a look at http://www.furoreproducts.co.uk/ or find more parts on Ebay, user names
furoreltd & furoreproducts, discounts available for LCB users.
Don't forget Stainless Steel Braided brake hoses, made to your exact requirements in any of around 16 colours.
http://shop.ebay.co.uk/furoreproducts/m.html?_dmd=1&_ipg=50&_sop=12&_rdc=1
|
NOTE:This user is registered as a LocostBuilders trader and may offer commercial services to other users
|
adampage
|
posted on 15/9/21 at 09:21 AM |
|
|
Love it!
Great idea, love to see different ideas, like some of the others have said, best of luck.
One other concern might be the current Leaf wiring. I assume it has ECUs everywhere, might it not have a sensor on the rear wheels (wheel speed, ABS,
etc) and if you take all that out and replace with a whole new end, that might cause an error or warning in the Leaf electronics, might be hard to
solve...
Related - I assume you'll have your own 12v battery to start the bike engine, so hopefully no issue there of 'contamination' between
the 2 systems, and like the earlier question - how do you synchronise throttle pedal(s) etc?
I'll watch this one!
Ad

|
|
Mr Whippy
|
posted on 15/9/21 at 09:26 AM |
|
|
Your going to chain drive a leaf? That's a lot of weight. Plus a bike engine, rad, new subframe etc. Jeez the things going to weight at least 2
tonnes. Can't help thinking you have been better buying a Prius and tuning it.
How are you going to deal with the throttle? The leaf just has a electronic one, I'm assuming the bike engine is cable. This definitely a
completely mad project which I can't see any benefit from but whatever floats your boat. Yeah the back of the leaf is very empty (spare wheel
well would have been nice) so loads of room to fit another power plant. You could even charge the battery pushing it along with the engine while the
motors on regen... See what explodes first lol
Btw I like the styling, it's novel and functional.
You could just buy a second hand later battery and swap it out. You'd end up with a good EV that's worth something.
[Edited on 15/9/21 by Mr Whippy]
|
|
russbost
|
posted on 15/9/21 at 09:35 AM |
|
|
quote: Originally posted by adampage
Great idea, love to see different ideas, like some of the others have said, best of luck.
One other concern might be the current Leaf wiring. I assume it has ECUs everywhere, might it not have a sensor on the rear wheels (wheel speed, ABS,
etc) and if you take all that out and replace with a whole new end, that might cause an error or warning in the Leaf electronics, might be hard to
solve...
Related - I assume you'll have your own 12v battery to start the bike engine, so hopefully no issue there of 'contamination' between
the 2 systems, and like the earlier question - how do you synchronise throttle pedal(s) etc?
I'll watch this one!
Ad
Most modern EV's have a 12V battery for systems like lights, wipers etc. I assume the Leaf has a separate 12V system? If so just don't
connect the bike alternator as that could confuse things. If it has wheel sensors that could create a problem if it sees faster wheelspeed at the rear
(wheelspin) than at the front, you could just double up on front sensors so they would all record same speed.
There's no need to "synchronise" throttles, the Leaf is fully auto, so the bike engine would simply be assisting - I imagine the
Leaf electronics would simply "see" this as going down a steep hill?
I no longer run Furore Products or Furore Cars Ltd, but would still highly recommend them for Acewell dashes, projector headlights, dominator
headlights, indicators, mirrors etc, best prices in the UK! Take a look at http://www.furoreproducts.co.uk/ or find more parts on Ebay, user names
furoreltd & furoreproducts, discounts available for LCB users.
Don't forget Stainless Steel Braided brake hoses, made to your exact requirements in any of around 16 colours.
http://shop.ebay.co.uk/furoreproducts/m.html?_dmd=1&_ipg=50&_sop=12&_rdc=1
|
NOTE:This user is registered as a LocostBuilders trader and may offer commercial services to other users
|
Mr Whippy
|
posted on 15/9/21 at 11:47 AM |
|
|
Hmm I wouldn't describe the leaf as an automatic. It is in a way like driving one but it brakes using regen, holds on hills with the motor. Keep
in mind too that the motor is always engaged, if the front wheels turn so does it. Push it along and it's going to generate electricity and
that's got to go somewhere, like into your dodgy battery. This is what happens when you brake or go down hills. It's just a rolling
computer and how would it react to being shoved along by a 200bhp engine in the back it doesn't know about, well the results could be
interesting, maybe even with lots of flames.
However the main reason i wouldn't take on a project like this is that after all the time, effort and at least 6k, the car would be completely
worthless.
But hell if you want to do it, go for it. It will be very educational.
[Edited on 15/9/21 by Mr Whippy]
|
|
adampage
|
posted on 15/9/21 at 04:13 PM |
|
|
Thanks Russ
Good point on the syncing throttles, "like driving down a hill", of course...
|
|
derekbruceyoung
|
posted on 15/9/21 at 04:34 PM |
|
|
Thanks for the feedback russbot -- exactly what I'm after!
Regarding the CoG -- totally get that the engine placement is not ideal, but keep in mind there's an 640lb battery pack inches off the ground in
this car, and in the spirit of the build I'm trying to 1) not let perfect be the enemy of good enough, and 2) and use as many of the bike parts
as possible, so no low profile sumps or side exit exhausts for now that would allow me to lower the engine more. I'm willing to accept some
hits in the driving dynamics area here -- as mentioned this car will weigh close to 4000lbs (blasphemy in these circles I know). It'll be like
driving with two large dogs in the boot
Great ideas on the half shafts. That process is similar to others I've read about but feel more confident having heard it done successfully.
I'd love to do it without having to disassemble the CV joints, but that may be a bridge too far. I'm a competent machinist but a very
novice welder, so I will likely do all the fab work short of final welding. I was thinking of adding an additional non-structural thin outer sleeve
to act as a retention loop if the half shaft breaks in half to stop it from flailing around, but maybe I'm over thinking it.
Thank you for the reassurance on the 5/8" offset. I agree that it's the least weird thing about the chainline. I am a little concerned
with the chain angle over the single shear single bearing tensioner sprocket causing too much load on it under engine braking, but I don't know
what sort of negative torque I'll be dealing with to do any analysis.
As for the questions:
The only electrical interfaces to the leaf will be tapping off of it's 12V system and the throttle.
The bike's battery and alternator connection will be eliminated and the system will be supplied power directly from the leaf's 12V battery
through an 80A contactor. The leaf 12V is charged by an onboard DC-DC converter that uses the HV battery. The starter motor will be retained, but
eventually I'd like to do stop-start bump starting so it doesn't idle at zero speed. Digging through leaf forums this set up is
electrically similar to jump starting another ICE with your Leaf which people have done without issue.
The leaf throttle is a modern electronic dual analog signal hall effect unit, and I will be intercepting these two signals with an Arduino micro
controller, which will then process them (along with signals from the bike ECU) and depending on the driving mode (full EV, full power, charge) it
will decide what analog values to send along to the leaf ECU, and what to ask the ICE to do. The ICE throttle is run by a 1/4 scale hobby servo.
You can see that in action here:
https://photos.app.goo.gl/butgdaMgYsyXqD2X9
I also hope to use this electronic throttle control to pull back on upshifts so that I can do flat footed quickshifting.
The "Charge" mode would have the leaf throttle fully cut out once the car is rolling and have ICE pushing the car along while the front EV
performs regenerative braking (as if it was coasting down a hill). Not terribly efficient (going through 2 drivetrains and 2 sets of tires!), but
it'll get the job done. OEM vehicles with similar layouts (BMW i8, Acura NSX) have a starter-generator on the ICE doing direct energy
production to recharge the hybrid pack, and only do the road-coupled regen in edge cases, but that would be a huge technology lift for me to perform.
The leaf has 3 settings, Neutral (0 kw regen), D (15kw) and B (30kw) so there are some options.
Great note about the speed sensors too adampage. I'm going to be looking into the ABS tone rings in the Lexus hubs to see what I have to do to
get that to talk to the leaf -- may require another micro controller to spoof the signal to look more leaf-like.
As for the motivation for this project, I totally understand that few people would take something like this on. And I definitely get the appeal of
super light sports cars -- in the 1990s my father built a Caterham 7 which he still owns. I've both tracked it and rode as navigator in at
Targa Newfoundland (scary!), so I see how a 4000lb hybrid doesn't exactly fit with the spirit of this community. I myself have done a few car
projects in the past (built a Datsun 510 rally car and couple of circuit racing Hondas for the 24h or Lemons), but what I was really after was a
project to satisfy a few of my desires:
1) a bike engine powered car -- something I've always wanted, the sound, the shifting, something we can all agree on
2) a technology and design focused build. I love solving novel problems and this is full of them. I pretty much do the same thing at work all day
building robots, but apparently I can't get enough.
3) creative re-use of old EVs -- California will be full of outdated low-range EVs very soon and creative reuse of them is something that people
aren't really thinking about yet -- I am hoping to have it drivable in December to take it to an EV car show in Los Angeles (stretch goal!). I
think I might get some emotional responses there
4) a small enough scoped project to actually complete. I'm not building a bespoke car here. In fact, as long as the rear wheels can roll, the
car should be able to drive around -- with air conditioning, Bluetooth and the whole bit. I have a 1 car garage that is also my wife's COVID
gym so I'm trying to do as much pre-building and then do the install into the car as quickly as possible in another location (likely a
friend's shop with a lift). This is another reason the engine is directly on top of the subframe -- trying to build as much as possible into
that one unit.
5) something I can park on the street -- again, I have 1 car garage/gym, so this car is going to live on the street. Starting with a very normal car
makes this easier
6) something weird enough to be a conversation piece for any sort of car gathering, meet like minded people for professional networking and other
future fun.
If this project goes well, I will look to building a similar system into a lighter more performance focused base car with a bespoke battery pack and
more custom EV stuff. That said, I've worked in the EV space before and know how much work it is to build a safe and reliable system, hence
starting with a stock EV. Mostly I'm just trying to keep focused on my current project.
I've also done non-car projects that are even dumber -- I am a former competitor on Battlebots (American version of Robotwars). I am lucky
enough to have a supportive spouse and the funds to complete this. Worst case the whole thing gets parted out (including the battery -- which even at
reduced capacity has value in other applications) and the hacked Leaf shell gets scrapped.
The process is really the point here, using cool technology and my skills to build something novel.
And if it is successful in some regards, I don't know about it being worthless -- that all depends on the buyer! I've seen a youtube of
an admittedly crude (no firewall!) moto-engine SmartCar where the current owner showing the car didn't build it, so there's a lid for
every pot.
[Edited on 15/9/21 by derekbruceyoung]
|
|
ReMan
|
posted on 15/9/21 at 05:39 PM |
|
|
I'm loving the concept and enthusiasm and the skill and design going into this and the fact that its very different and a brilliant engineering
and elctricalling project.
I just worry its going to make all the right BEC noises , but be disappointing,on performance or range or both
Looking forward to seeing the progress
www.plusnine.co.uk
|
|
Mr Whippy
|
posted on 15/9/21 at 06:16 PM |
|
|
Maybe lower it too as despite the battery weight it's hardly a great handling car, maybe the roof is very heavy. It's a bit of a boat
compared to my Fiesta. I don't know why they made the ride height so high.
|
|
derekbruceyoung
|
posted on 15/9/21 at 06:18 PM |
|
|
Range will be limited by tank size -- it'll be short initially as I plan on using the stock bike tank, but fuel refilling is faster (and more
accessible) than recharging. Performance wise, some very basic analysis makes it look like it should accelerate like a WRX STI with a ~5s 0-60. Not
a 7 for sure, but it shouldn't be slow. Handling will likely be "interesting" with the stock suspension front and IS rear bits.
Again, something to address once it's up and running.
|
|
derekbruceyoung
|
posted on 16/9/21 at 07:17 AM |
|
|
Ok here's another couple BEC questions for my new friends here:
What is your shifter lever throw? What is too short? Where's the right balance for stiffness and feel? For the design I'm pursuing for
the shift lever, I'm trying to have the mechanism exit through the change dish and make its way forward via a 4-bar linkage to position the
shift knob in a pleasing location. My current design has ~35mm of travel from center in either direction, that drives a M6 threaded push-pull cable
rearwards towards the engine.
https://photos.app.goo.gl/3J4gh8s4M883krvC8
You can also see the (adjustable) location of the micro swift as an upshift sensor for the quickshifter. I know the $$ commercial ones use a load
cell, but I've read of DIY moto builds with switches. Any experience in this regard?
BTW, I just scanned through the users commenting on my thread and noticed how long you've all been here. I thank you for being welcoming to
this newb and his weird project.
[Edited on 16/9/21 by derekbruceyoung]
|
|
ReMan
|
posted on 16/9/21 at 07:35 AM |
|
|
Thats not a design, its a masterpiece of engineering and manufacturing!
Mines a bit of steel pipe welded to a steel pivot tube with a bit of flat bar underneath that the cable clevis slots on to!
TBH 35mm from centre seems a bit long, I recon mine is probably 20-25mm at the top of the knob!
To get the best you need to be able to shift fast for smooth clutchless changes
www.plusnine.co.uk
|
|
russbost
|
posted on 16/9/21 at 08:01 AM |
|
|
"Thats not a design, its a masterpiece of engineering and manufacturing!" - or, looked at another way, it's massive overkill for
what is a very simple job. Mine is a simple lever on a pivot, with the cable operation taken between the top & the pivot
This is mine
[img]
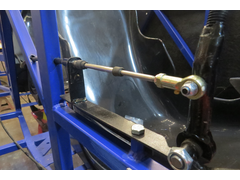 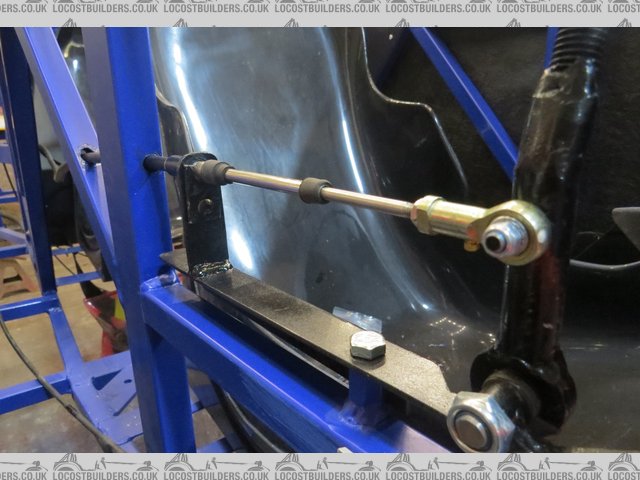 Description
[/img]
What's important is the ratio of the 2 parts above & below the cable, I'd say once my lever knob is in place that's around 2:1
which gives adequate leverage & a short throw, I've never measured it but I'd guess it's aroun 40 - 50mm at the top of the lever
I no longer run Furore Products or Furore Cars Ltd, but would still highly recommend them for Acewell dashes, projector headlights, dominator
headlights, indicators, mirrors etc, best prices in the UK! Take a look at http://www.furoreproducts.co.uk/ or find more parts on Ebay, user names
furoreltd & furoreproducts, discounts available for LCB users.
Don't forget Stainless Steel Braided brake hoses, made to your exact requirements in any of around 16 colours.
http://shop.ebay.co.uk/furoreproducts/m.html?_dmd=1&_ipg=50&_sop=12&_rdc=1
|
NOTE:This user is registered as a LocostBuilders trader and may offer commercial services to other users
|
derekbruceyoung
|
posted on 16/9/21 at 04:33 PM |
|
|
No doubt there is some mechanical wankery going on here -- I will not deny it, but that's where much of the fun of this build lies for me. The
reality is that the leaf does not have space where a simple pivot should exist (the stock shift blob and supporting structure are there) and placing
the pivot elsewhere but keeping the knob where I want it gives the shifter too much up and down motion.
One of my design philosophies is that CAD time is essentially free and I would rather spend a few hours at the screen on my couch making things able
to bolt-in rather than bodging stuff in the car. I'm also trying to retain the finish quality of the interior in the front of the car (which is
actually in very nice shape) -- keeping as much stock as possible and making the integration require the fewest modifications. Having the shift mech
exit through an existing hole above existing sturdy mounting points (in this case the airbag modules 3x M8). Fabrication is also trivial (aside from
extra $$) as it's all laser cut plate again.
Now back the the actual question -- the shift lever on the bike is a Qa after market part that's 38mm long and the short end of the shifter is
37mm -- the long end is 190 giving a 5:1 ratio, with the 71mm total travel creating the 12.5mm travel at the bike. Sounds like I can shorten that up
which is good news -- I can make the lower pivot adjustable to tune it for the right feel.
Thanks guys, very helpful!
|
|
ReMan
|
posted on 16/9/21 at 08:48 PM |
|
|
You go for it man!
i raise you my bent metal
 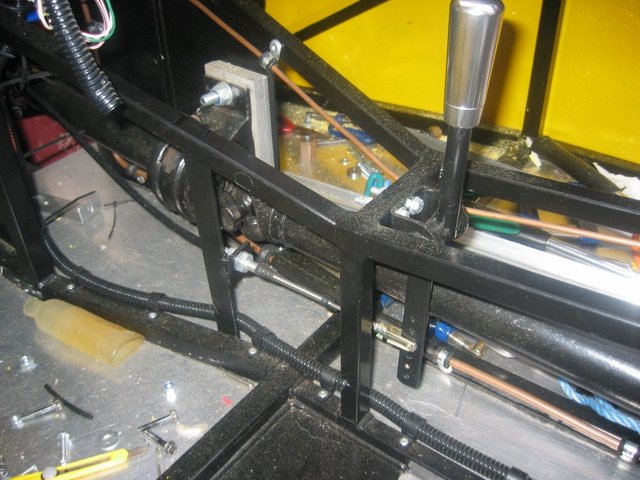 Rescued attachment g2.JPG
www.plusnine.co.uk
|
|
derekbruceyoung
|
posted on 29/9/21 at 04:24 PM |
|
|
Hi guys -- I made my major laser cut part order and parts landing tomorrow -- exciting times! Photos of everything are being stuck in my Google
Photos album here -- which I have also annotated if you're unsure as to what you're looking at.
https://photos.app.goo.gl/hBUezQtiCVuvTPQ99
Now, a BEC question -- I'm using a sealed Quaife unit for a Honda which uses special M10X1 left hand threaded bolts which I have. Honda says to
torque them to 101Nm, but that's on a hardened steel ring gear and not an aluminium alloy sprocket. A regular coarse thread 12.9 M10 torque
specs is more like 65Nm. I started to tighten these up last night and even 65Nm felt like a lot. Anything more than that and I am afraid of yielding
the underlying aluminum. I'm leaning towards leaving them at 65Nm. I also used loctite 243 and can paint mark and inspect them regularly
(unlike a sealed diff).
I've contacted Quaife to ask them but I'd love to hear your opinions.
[Edited on 29/9/21 by derekbruceyoung]
|
|
motorcycle_mayhem
|
posted on 29/9/21 at 06:39 PM |
|
|
Race car uses the QDF7ZR, where the alloy (T6) sprocket is held on with M10 std thread 8.8 bolts with nylocs.
I just nip them up, standard length 17mm spanners. The bolts have never come loose.
The sprocket gets changed regularly for different circuits, the nylocs get changed infrequently.
Thing is, where can the sprocket go? If you had a split sprocket I'd be more concerned, but it's solid as pictured. Those K-nuts
won't move...
|
|
derekbruceyoung
|
posted on 28/12/21 at 07:46 AM |
|
|
BEC locosters!
I thought I'd give you guys an update -- I've been doing a photo dump of everything related to this project which can be found here:
https://photos.app.goo.gl/hBUezQtiCVuvTPQ99
All functionally required systems are in the car -- and I drove it for the first time today under full hybrid power! I did a short 3 mile loop on a
divided 4 lane road near my house, where I got into full throttle for the first time. I don't think I made it to redline (but def in the 10K+
rpm range) and I touched 70mph indicated. The power was great the sound was insane. Still lots to do -- getting air to the radiator, filling in the
firewall, alignment, etc -- but today was a triumph for me in this project.
https://photos.app.goo.gl/h6wa9XdfgcnNYRgw8
Air intake mocked up in the passenger rear window -- this will feed the radiator
https://photos.app.goo.gl/2qw9Avy1DSCoN5rJ9
The hatch is heavily vented -- bit of a rally-cross feel to it.
https://photos.app.goo.gl/rqfcq3BVHBV3QWi99
Interior has a simple switch panel along with a video feed of the bike gauge from the hatch
https://photos.app.goo.gl/VBdFajceKUtAQBQo9
[Edited on 28/12/21 by derekbruceyoung]
|
|
derekbruceyoung
|
posted on 28/12/21 at 07:49 PM |
|
|
Useless without video, right? I managed to revive my old gopro to get highway onramp footage. You can see I'm ready to short shift -- I need
to get used to that 13k redline.
https://photos.app.goo.gl/xLqRKXPUne53TWjTA
|
|
ReMan
|
posted on 28/12/21 at 08:17 PM |
|
|
Wow that’s looking good. Some tidy engineering in the trunk/frunk boot/froot too!
[Edited on 28/12/21 by ReMan]
www.plusnine.co.uk
|
|