andyps
|
posted on 13/12/05 at 01:00 PM |
|
|
Triangulation
Hopefully will make a start on the triangulation this weekend and was contemplating the best way to cut the ends of the tubes. The options seem to be
as below, is any one of them preferable? My own thought is that A would be best, but most complex. If it makes any difference to the answer, my choice
is to double triangulate (making a cross) using 13mm square rather than the usual single diagonal round section.
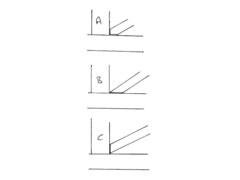 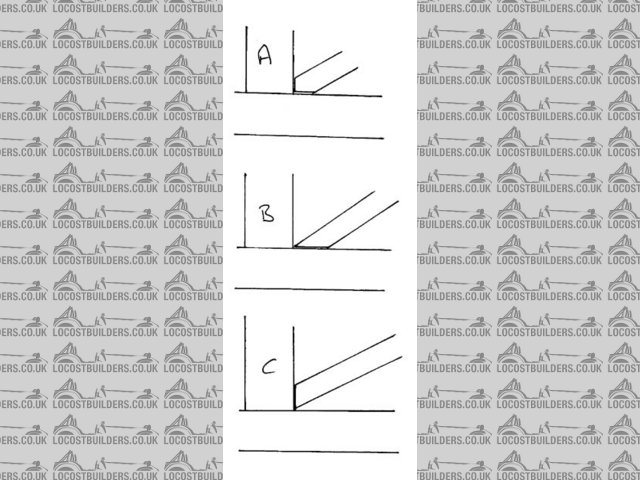 Rescued attachment triangulation.jpg
Andy
An expert is someone who knows more and more about less and less
|
|
|
Dieguez
|
posted on 13/12/05 at 02:33 PM |
|
|
triangulation
The A option is the best.
Dieguez
|
|
Johnathan
|
posted on 13/12/05 at 03:56 PM |
|
|
A is the best, and makes more sense ...
Why make a cross though? Your not really going to need it, and will make your chassis heavier. Once you have a tube welded properly and securely
inside any of the square /rectangular shapes on your space frame, it will lock it up and strengthen it anyway.
Seems like a waste to me
www.LogicalTuning.com
|
|
mark chandler
|
posted on 13/12/05 at 04:14 PM |
|
|
'A' is best, 'C' passes MSA roll bar design specs, 'B' does not !.
Regards Mark
|
|
andyps
|
posted on 13/12/05 at 05:15 PM |
|
|
quote: Originally posted by Johnathan
A is the best, and makes more sense ...
Why make a cross though? Your not really going to need it, and will make your chassis heavier. Once you have a tube welded properly and securely
inside any of the square /rectangular shapes on your space frame, it will lock it up and strengthen it anyway.
Seems like a waste to me
Mainly because I like the idea of it and think it should look good. It has been done before - Mark Allanson did it, but I don't know why he
chose that.
Weight increase shouldn't be too much though.
Andy
An expert is someone who knows more and more about less and less
|
|
JoelP
|
posted on 13/12/05 at 07:28 PM |
|
|
ditto 'A', with load spreading fillets if you really want to get carried away!
|
|
mike4444244
|
posted on 13/12/05 at 07:33 PM |
|
|
hi
the round bar is used for the triangulation because its cross section makes it more resistant to side impact, on the chassis this is the triangulation
down each side, box section will deform much easier on side impact,
HTH
Mike
110 Defender
|
|
andyps
|
posted on 13/12/05 at 11:12 PM |
|
|
Is it weaker even if I fully weld the point at which the two tubes cross? I would have thought that would create a kind of net effect which can be
pretty strong.
Andy
An expert is someone who knows more and more about less and less
|
|
Nisseven
|
posted on 14/12/05 at 10:19 AM |
|
|
I'm not an expert but I was told by someone who should be that the tubes whether round or square are much stronger in tension than compression.
It is just as good to go in one direction only so long as you put the tube so that the load causes it to be in tension.
Bruce
|
|
andyps
|
posted on 14/12/05 at 11:16 AM |
|
|
On that principal, if you have a rectangle with a cross in it, for a load applied to any corner one of the cross tubes would be in tension and the
other in compression so would you have the best of both worlds?
Andy
An expert is someone who knows more and more about less and less
|
|
02GF74
|
posted on 14/12/05 at 11:40 AM |
|
|
without doubt A is the stongest.
What profile of tubing are you welding to what? i..e. round tube to round tube or square section tube?
If you are welding round tubes, there is a program that by entering diameters, angles, etc: prints on paper the fishmouth profile you need. You cut
the paper and stick it on your tube then cut the notch in the metal. Now someone is going to ask where to find this program........ 
|
|
iank
|
posted on 14/12/05 at 12:22 PM |
|
|
quote: Originally posted by 02GF74
...
If you are welding round tubes, there is a program that by entering diameters, angles, etc: prints on paper the fishmouth profile you need. You cut
the paper and stick it on your tube then cut the notch in the metal. Now someone is going to ask where to find this program........
There is one here (along with lots of other useful bits and bobs):
http://locost7.info/mirror/tools.php in TubeMitre.zip (never tried it myself though) 
|
|
andyps
|
posted on 14/12/05 at 12:56 PM |
|
|
So far it is all square section tubing. The round comes later for a few other bits.
Andy
An expert is someone who knows more and more about less and less
|
|
britishtrident
|
posted on 14/12/05 at 01:08 PM |
|
|
quote: Originally posted by 02GF74
without doubt A is the stongest.
What profile of tubing are you welding to what? i..e. round tube to round tube or square section tube?
If you are welding round tubes, there is a program that by entering diameters, angles, etc: prints on paper the fishmouth profile you need. You cut
the paper and stick it on your tube then cut the notch in the metal. Now someone is going to ask where to find this program........
"A" introduces a nasty triaxial stress system --- designing 3 welds to meet gives bad fracture mechanics avoid where possible.
|
|
Mark Allanson
|
posted on 14/12/05 at 10:10 PM |
|
|
Triaxial stress systems were yet to be invented when I did my apprentiship!
The theory taught in the 1980's was that a single stress point was used to line up the tubes. The bisected lines are on the centreline of the
horizontal tube and the centreline of the vertical tube, and the triangulation would be added so it 'points' to the cross in the 2 lines,
so A is the nearest to the ideal. It also adds to the bracing of the 2 other tubes.
[Edited on 15/12/05 by Mark Allanson]
If you can keep you head, whilst all others around you are losing theirs, you are not fully aware of the situation
|
|
clbarclay
|
posted on 15/12/05 at 10:38 PM |
|
|
quote: Originally posted by mike4444244
hi
the round bar is used for the triangulation because its cross section makes it more resistant to side impact, on the chassis this is the triangulation
down each side, box section will deform much easier on side impact,
HTH
Mike
????
Unless i've miss under stood the reasons for what your saying, they teach the opposite when calculating bending stresses at uni.
Square section RHS is stronger in bending (higher second moment of area) compared to round tube of the same mass per meter, not diameter.
In bending square sections have a greater max bening stress, but round sections can withstand higher (margianly) max torque.
|
|
02GF74
|
posted on 16/12/05 at 09:52 AM |
|
|
quote: Originally posted by clbarclay
Square section RHS is stronger in bending (higher second moment of area) compared to round tube of the same mass per meter, not diameter.
is that right? I don't believe it. The strongest shape for the same mass per meter has to be round surely? Millions of years of evloution
shows that animal bone cross sections are round not square.
|
|
britishtrident
|
posted on 16/12/05 at 10:40 AM |
|
|
quote: Originally posted by clbarclay
snip
????
Unless i've miss under stood the reasons for what your saying, they teach the opposite when calculating bending stresses at uni.
Square section RHS is stronger in bending (higher second moment of area) compared to round tube of the same mass per meter, not diameter.
In bending square sections have a greater max bening stress, but round sections can withstand higher (margianly) max torque.
You misunderstood for a framed structure round tube is more efficient per unit mass.
|
|
clbarclay
|
posted on 16/12/05 at 06:18 PM |
|
|
quote: Originally posted by britishtrident
You misunderstood for a framed structure round tube is more efficient per unit mass.
Is that to do with energy absorbtion then, rather than the bending moments?
|
|
MikeRJ
|
posted on 17/12/05 at 10:23 PM |
|
|
quote: Originally posted by clbarclay
quote: Originally posted by britishtrident
You misunderstood for a framed structure round tube is more efficient per unit mass.
Is that to do with energy absorbtion then, rather than the bending moments?
No, if you think about it, for the same mass per unit length (assuming the same gauge materal), a round cross section will have a larger diameter than
square and hence stronger in bending.
For the case where the round tubes diameter = distance accross flats of the square section, the latter will be the heaviest and strongest.
|
|
gazza285
|
posted on 17/12/05 at 10:32 PM |
|
|
Not forgetting that square section is only strong in two planes, apply a force at 45 degrees to a flat section and it will collapse with much less
force.
DO NOT PUT ON KNOB OR BOLLOCKS!
|
|
birdii
|
posted on 20/12/05 at 08:45 AM |
|
|
If using option A is it better to weld the two tubes in the corner then grind the weld and then fit the triangulation, or should the triangulation be
fitted without welding the corner that it will be covering?
This isn't a problem with option B or C because non of the joints are covered by the triangulation.
So weld and grind, or dont weld just fit the triangulation over the joint?
Cheers.
|
|
JoelP
|
posted on 20/12/05 at 09:17 AM |
|
|
weld and dont grind. You might have to take a little top and bottom, but in the middle it will fit snugly inside the tube. If a resulting angle ends
up too tight to weld inside, take a wedge of tube and weld it over it.
|
|
Alan B
|
posted on 20/12/05 at 02:18 PM |
|
|
quote: Originally posted by Mark Allanson
Triaxial stress systems were yet to be invented when I did my apprentiship!
The theory taught in the 1980's was that a single stress point was used to line up the tubes. The bisected lines are on the centreline of the
horizontal tube and the centreline of the vertical tube, and the triangulation would be added so it 'points' to the cross in the 2 lines,
so A is the nearest to the ideal. It also adds to the bracing of the 2 other tubes.
[Edited on 15/12/05 by Mark Allanson]
Bingo...intersecting centre lines is the key....
|
|
JoelP
|
posted on 20/12/05 at 03:33 PM |
|
|
ive been spending hours recently in the garage grinding 50x50x3 square tubes to fit in style A, and coincidentally, it is the centrelines that line
up! I'll chuck up a picture soon, as it will make a nice example being in large tube. Plus you can all ridicule my welding
|
|