Avoneer
|
posted on 8/7/05 at 07:20 PM |
|
|
Panhard rod end fixing idea????
Hi,
To make thing easier etc, can anyone see any problems with me fixing the end of my panhard rod like this:
The bolt will be welded to the chassis.
Pat...
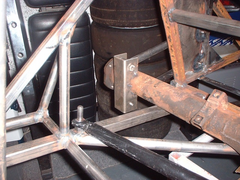 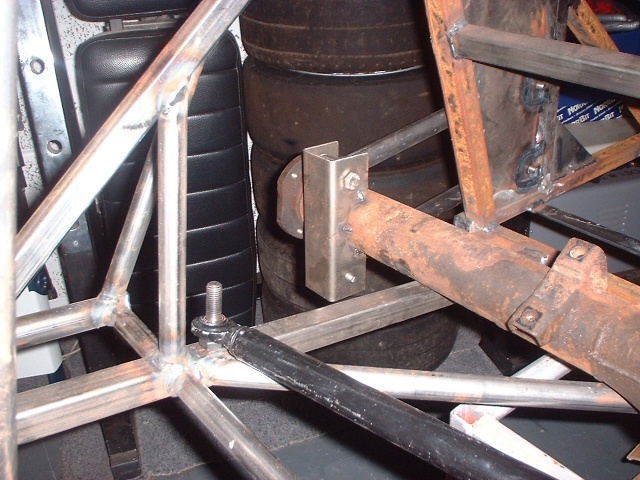 Rescued attachment DSCF0050.JPG
No trees were killed in the sending of this message.
However a large number of electrons were terribly inconvenienced.
|
|
|
Avoneer
|
posted on 8/7/05 at 07:21 PM |
|
|
And another pic:
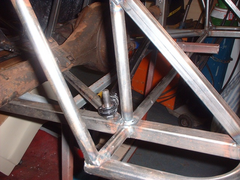 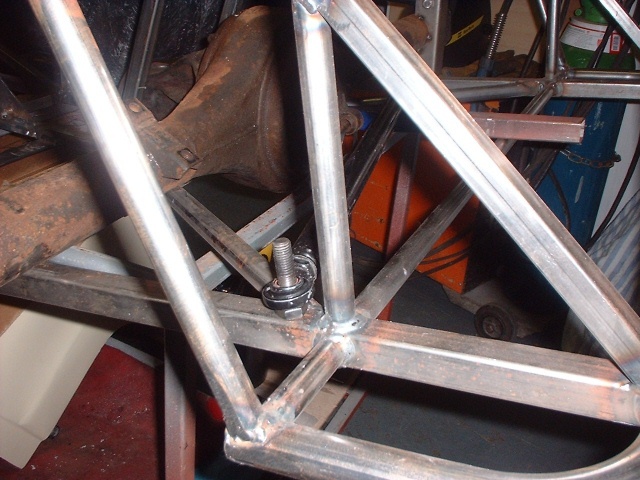 Rescued attachment DSCF0051.JPG
No trees were killed in the sending of this message.
However a large number of electrons were terribly inconvenienced.
|
|
JoelP
|
posted on 8/7/05 at 07:26 PM |
|
|
its not ideal, but i wouldnt know exactly how unideal it is. Probably safe, but is that good enough? Is there a reason for not putting the bolt all
the way through, and having a crush tube?
|
|
mookaloid
|
posted on 8/7/05 at 07:26 PM |
|
|
doesn't look strong enough to me
|
|
Avoneer
|
posted on 8/7/05 at 07:32 PM |
|
|
This is how Jon Ison fixed the other end and he had no probs, so this should be fine shouldn't it???
I can do the crush tube thing if necessary.
Pat...
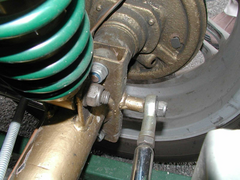 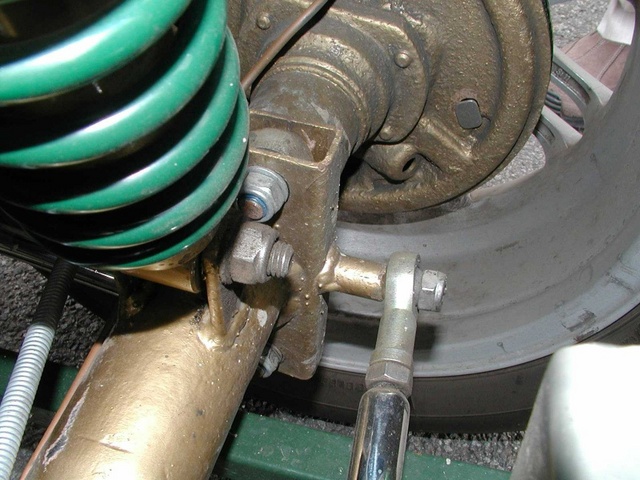 Rescued attachment rearpanard.jpg
No trees were killed in the sending of this message.
However a large number of electrons were terribly inconvenienced.
|
|
JoelP
|
posted on 8/7/05 at 07:34 PM |
|
|
on my chassis ive only welded a bolt on twice - one to hold a brake pipe T piece, and one as the main engine/starter earth point. In fact, thinking
about it, even the latter one was drilled through and then welded!
i think jons bolt still goes all the way though there anyway.
[Edited on 8/7/05 by JoelP]
|
|
Triton
|
posted on 8/7/05 at 08:35 PM |
|
|
Pat,
Use a 'bone bracket.....welding a bloody great big bolt like that too thin wall tube isn't strong enough....might have a spare one banging
about i will have a butchers for you.
Mark
|
|
kb58
|
posted on 8/7/05 at 09:00 PM |
|
|
You really need that in double-shear. That means both ends of the bolt need to pass through the chassis. Yes single shear will work (as you have it)
but it must be built over-strength to keep it from breaking. I don't trust it as is since the tube it's welded to is far smaller in
thickness then the bolt.
Mid-engine Locost - http://www.midlana.com
And the book - http://www.lulu.com/shop/kurt-bilinski/midlana/paperback/product-21330662.html
Kimini - a tube-frame, carbon shell, Honda Prelude VTEC mid-engine Mini: http://www.kimini.com
And its book -
http://www.lulu.com/shop/kurt-bilinski/kimini-how-to-design-and-build-a-mid-engine-sports-car-from-scratch/paperback/product-4858803.html
|
|
Avoneer
|
posted on 8/7/05 at 10:04 PM |
|
|
Thanks Mark.
I have a normal bracket, but now that I have put two short uprights in to support the fuel tank, it won't fit.
Looks like I'll have to cut it out and work out another way of doing it.
Pat...
No trees were killed in the sending of this message.
However a large number of electrons were terribly inconvenienced.
|
|
Avoneer
|
posted on 8/7/05 at 10:26 PM |
|
|
Ok, so if I mount the "normal" bracket flat on the chassis, I can just get away with getting a bolt through it - sorted.
With regards to the bracket on the other end, should it be with the bolt the same horizontal orientation, or with the bolt vertical - or should I use
a rod end on that end instead?
Pat...
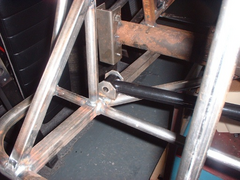 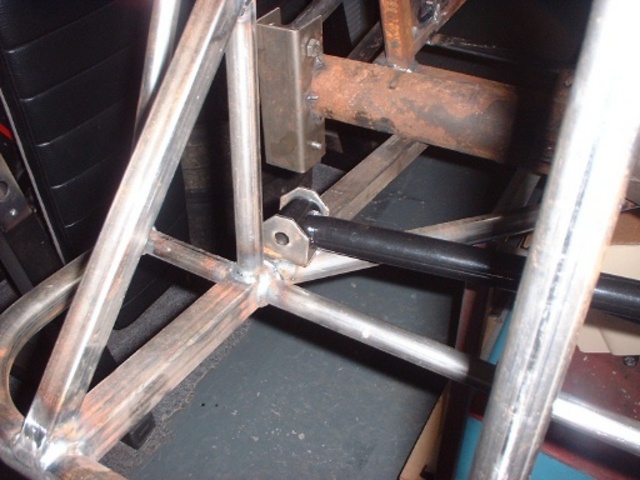 Rescued attachment Phan.JPG
No trees were killed in the sending of this message.
However a large number of electrons were terribly inconvenienced.
|
|
Jon Ison
|
posted on 8/7/05 at 10:45 PM |
|
|
are track rod ends in "double shear" ? just a thought, Ive seen plenty of rose jointed suspension with the bolt passing thru the joint and
for want of a better term screwing into the chassis in single shear, IMHO the 1st pic would be fine provided a crush tube was used. Alez stuffed the
car in the pic sideways with impact on the rear wheel, enough too bend a half shaft, the panhard rod survived and lives on too this day.
|
|
Avoneer
|
posted on 8/7/05 at 11:23 PM |
|
|
So easiest and probably best way (for this end) is to mount it as per the last pic with a "normal" bracket???
Pat...
No trees were killed in the sending of this message.
However a large number of electrons were terribly inconvenienced.
|
|
kb58
|
posted on 9/7/05 at 01:26 AM |
|
|
Let's say your car can corner at 1.0G. If there is, oh, 600lbs on the rear suspension at rest, that means when you're cornering at 1.0G,
there is 600lbs on that joint. Now imagine hitting a pothole half way through that turn that generates a spike of an additional 1.0G for an instant.
That means for that instant there is 1200lbs hitting that joint. So picture how that bracket will hold up if you park the car next to a wall, place a
jack between the bracket and the wall, and apply 1200lbs to it. Will it hold?
Mid-engine Locost - http://www.midlana.com
And the book - http://www.lulu.com/shop/kurt-bilinski/midlana/paperback/product-21330662.html
Kimini - a tube-frame, carbon shell, Honda Prelude VTEC mid-engine Mini: http://www.kimini.com
And its book -
http://www.lulu.com/shop/kurt-bilinski/kimini-how-to-design-and-build-a-mid-engine-sports-car-from-scratch/paperback/product-4858803.html
|
|
Cita
|
posted on 9/7/05 at 08:15 AM |
|
|
That's a hefty bolt used in the first picture so where exactly would it break?
At the weld? I doubt this and to shear the bolt itself you would need a bit more than 1200 lbs I guess.As long as the momentum arm on the bolt is kept
as close to the chassis rail as possible I dont think there will be any problem.
All INMHO without any engineering backup!
|
|
NS Dev
|
posted on 9/7/05 at 08:29 AM |
|
|
Technically mounting it in double shear is much better, but in the real world, it will be just fine!
I have the rear compression links of the double wishbones on the front of my grasser mounted on single shear stubs, and I have now hit the barrier,
other cars, broken chunks out of my wheels etc, and the stubs are still perfectly intact.
I didn't like the single shear mounts but they made the job much easier and neater, and they have worked fine.
Most production car panhard rods are mounted on a single shear stub at the axle end.
|
|
Triton
|
posted on 9/7/05 at 09:16 AM |
|
|
The bolt won't snap but as it is only welded to 1.6mm wall tube it will tear a chunk out of the tube...because that's the weakest part.
|
|
JoelP
|
posted on 9/7/05 at 06:14 PM |
|
|
would it be at the edge of the heat affected zone? cant remember if thats the weak point, or just the edge of the discolouration.
|
|
Peteff
|
posted on 9/7/05 at 08:22 PM |
|
|
it’s the Dwarven way, right Joel. It would be more affected by the heat needed to weld the thick bolthead to the thin tube in a relatively confined
area I think.
yours, Pete
I went into the RSPCA office the other day. It was so small you could hardly swing a cat in there.
|
|
Cita
|
posted on 9/7/05 at 10:08 PM |
|
|
You will need alot of force to rip a chunk out of that area I guess.
Weld a 3 mm plate on top and bottom of the rail (to spread the load) ,drill a hole through it and put the bolt from underneath through the hole.Weld
the bolthead on the bottom plate and the shank on the top plate.
Should give a strong and simple solution.
Cheers Cita.
|
|
drmike54
|
posted on 13/7/05 at 12:22 AM |
|
|
I like Cita's mounting idea. Simple, cheap and strong
Started Welding the chassis!!!!
|
|
Rorty
|
posted on 13/7/05 at 04:15 AM |
|
|
There's nothing intrinsically wrong with a single shear mount just as long as it's strong enough for the job.
Quite often the bolt used has to be up-sized to retain sufficient strength and the size of the attached rod end grows accordingly, making it a much
more expensive joint than a well designed double shear joint.
Don't be fooled into using a very high tensile bolt for added strength, because the HAZ will likely reduce it to a fairly low grade fastener.
The best sort of single shear attachment is a muchroom shaped stud with a large head to take the weld heat away from the stud itself and also to
spread the load.
A hex bolt will work OK though, but weld it fairly close to the corner of the RHS tube to take advantage of the inherent strength in that area. If you
weld the bolt in the middle of the RHS the thin steel could well flex and the bolt could end up tearing the surrounding area out of the tube.
As a belt and braces approach, weld a lozenge shaped "pad" of thicker steel (than the tube) to the RHS first and then weld the stud or
bolt to that.
Cheers, Rorty.
"Faster than a speeding Pullet".
PLEASE DON'T U2U ME IF YOU WANT A QUICK RESPONSE. TRY EMAILING ME INSTEAD!
|
|
NS Dev
|
posted on 13/7/05 at 07:28 AM |
|
|
Yup, on the grasser chassis the compression links are en16t machined to a "mushroomed" root (then sawn off the the angle needed for
welding to the chassis) and welded to "rhombus" shaped pads in turn welded to the rhs of the chassis. Certainly haven't broken yet
even with the muppet driver (me) hitting stuff on a regular basis!
|
|