Dean m
|
posted on 9/6/16 at 10:57 AM |
|
|
Opinions on my weld
Hi,
Before I start tacking together my chassis I would like a second opinion on my weld.
Had a play with some box section and the two photos show ( what I think ) is about the right setting on my welder.
Does it look like I've got the power setting and wire speed about right?
The next power setting up blows holes in the end of the box section really easily.
Thanks Dean
[img]
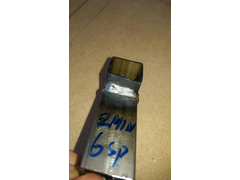 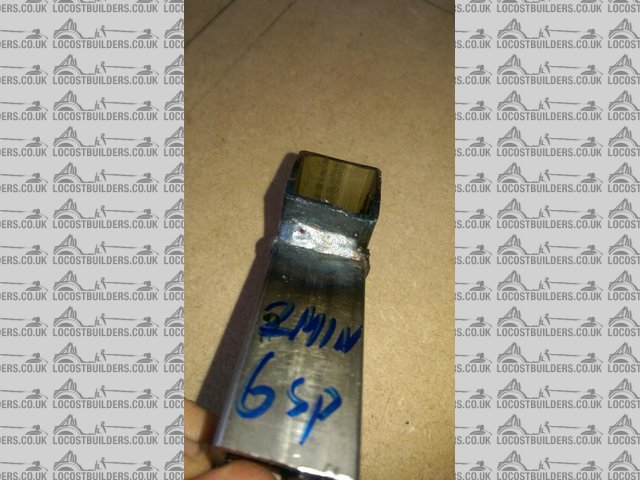 Weld
[/img]
[img]
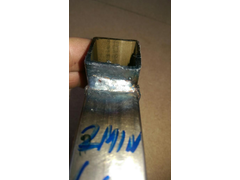 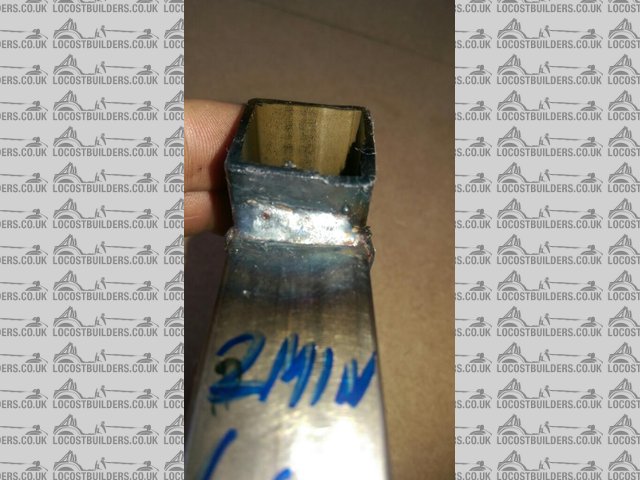 Weld2
[/img]
|
|
|
ken555
|
posted on 9/6/16 at 11:00 AM |
|
|
Cut it at a 45 degrees thru the weld and look at the penetration
|
|
John Bonnett
|
posted on 9/6/16 at 11:28 AM |
|
|
quote: Originally posted by Dean m
Hi,
Before I start tacking together my chassis I would like a second opinion on my weld.
Had a play with some box section and the two photos show ( what I think ) is about the right setting on my welder.
Does it look like I've got the power setting and wire speed about right?
The next power setting up blows holes in the end of the box section really easily.
Thanks Dean
[img]
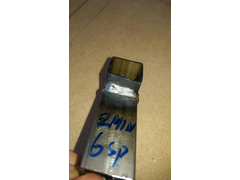 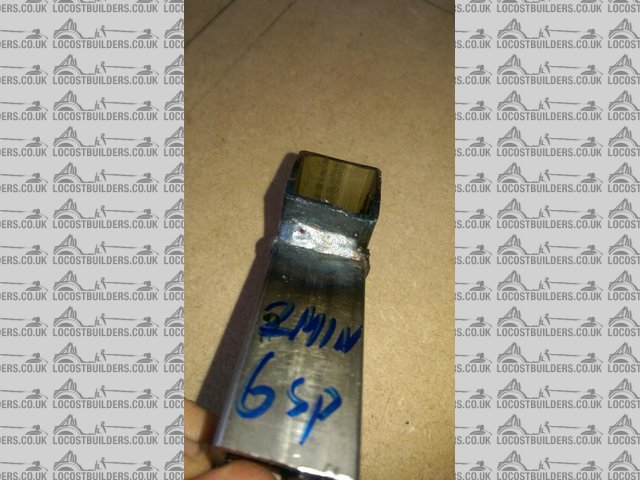 Weld
[/img]
[img]
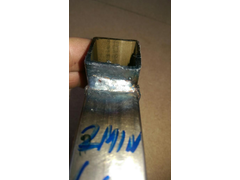 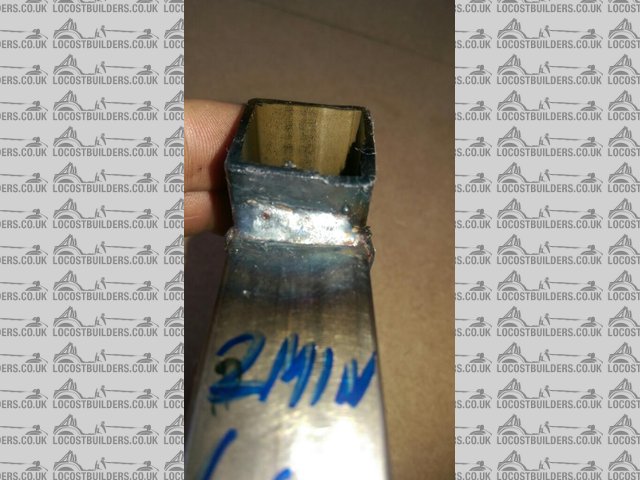 Weld2
[/img]
907 will provide the definitive answer but I'd be pleased with that.
|
|
40inches
|
posted on 9/6/16 at 11:35 AM |
|
|
I would be more than happy with that 
|
|
loggyboy
|
posted on 9/6/16 at 12:27 PM |
|
|
As Ken said. Cut it and check penetration. A good looking weld on the outside is a good idea of how good it is, but no guarantee.
Mistral Motorsport
|
|
MikeR
|
posted on 9/6/16 at 12:35 PM |
|
|
ideally you space the tube a mm away form the other one to help ensure pentration (it also means you can then see the pentration easily looking down
the short tube). With 1.6mm (or 2mm in your case) tube hobby welders are powerful enough to weld without the gap in theory.
Weld does look ok - but the proof is in the cutting open.
An alternative approach is to cut through just over half the weld and start hitting the thing with a hammer - see what lets go first, the weld or the
tube. If the weld goes and the tube is smooth you've not got penetration.
(nb this test was easier when i did my city and guilds 16 years ago as we used 5mm steel).
What does it look like looking straight down the open top tube?
|
|
Dean m
|
posted on 9/6/16 at 01:51 PM |
|
|
Thanks for the replies.
Looking down the tube there is only slight penetration,
And cutting in half shows most of the weld sat on top.
I also cut open one of my other test welds on the next power up setting and the weld was slightly more on the inside.
|
|
907
|
posted on 9/6/16 at 02:33 PM |
|
|
quote: Originally posted by John Bonnett
quote: Originally posted by Dean m
Hi,
Before I start tacking together my chassis I would like a second opinion on my weld.
Had a play with some box section and the two photos show ( what I think ) is about the right setting on my welder.
Does it look like I've got the power setting and wire speed about right?
The next power setting up blows holes in the end of the box section really easily.
Thanks Dean
[img]
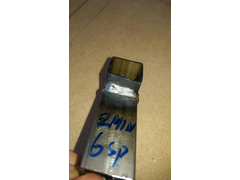 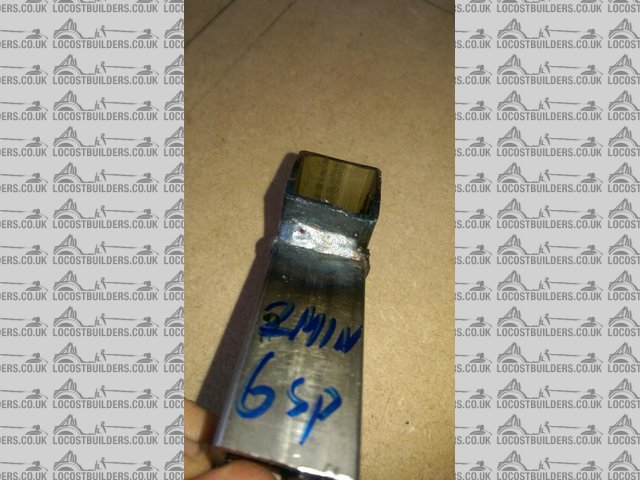 Weld
[/img]
[img]
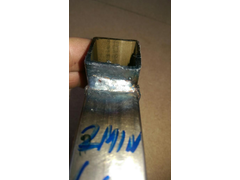 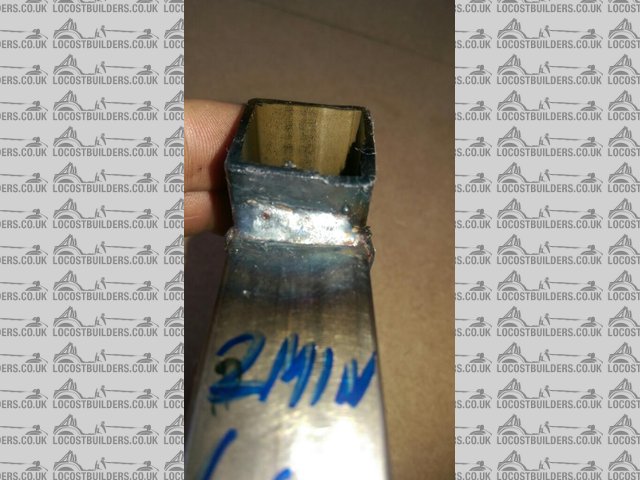 Weld2
[/img]
907 will provide the definitive answer but I'd be pleased with that.
Who ?
On a more serious note I know nothing about hobby welders.
There is no such thing as "power" settings; only volts and wire speed.
If I'm given the volts, wire speed in m/min, wire diameter, and type of gas
I can replicate this on my own machine, otherwise I'm lost.
If I were to comment I would say that the speed of travels too slow,
allowing a huge build up. The weld leg length looks massive in comparison to
the material thickness.
Also if your welding 25 box the weld should be 25mm long. Practice starting
at the beginning and finishing at the end.
My advice is get an experienced welder to show you the basics; then practice.
There. Now everybody hates me for being honest.
Paul G
[Edited on 9/6/16 by 907]
|
|