Dale
|
posted on 15/7/04 at 05:27 PM |
|
|
18 gauge ?
Its been disscussed alot but has anyone used 18 awg for the floor sheeting and do you have a problem with oil canning/ popping when you get in and out
of the car.
Thanks
Dale
|
|
|
derf
|
posted on 15/7/04 at 07:14 PM |
|
|
Just from my limited experience, I get that with a 16 guage floor, fully welded, not bad, but it does make a slight pop sound once in a while when I
get in/out, I'm sure it would be worse with an 18 gauge floor. The weigt difference shouldnt be too much eith, maybee a few pounds, 10-15?
|
|
pbura
|
posted on 15/7/04 at 07:33 PM |
|
|
If you have lengthwise beads rolled into 18 awg, you should have no drumming.
Was looking for a thread to refer you to, but am having no luck with the 'search' button today. Hopefully, someone who has done this will
pipe up 
Pete
Pete
|
|
Ben_Copeland
|
posted on 15/7/04 at 07:38 PM |
|
|
Cant remember what guage i used, but i braced it with 10mm square tube
Click Me
Ben
Locost Map on Google Maps
Z20LET Astra Turbo, into a Haynes
Roadster
Enter Your Details Here
http://www.facebook.com/EquinoxProducts for all your bodywork needs!
|
|
Mark Allanson
|
posted on 15/7/04 at 07:54 PM |
|
|
I used 18g, braced underneath and angled to make sure there were no symetrical areas of steel left to harmonise with certain engine revs - I HATE that
metallic rasp of vibrating sheet steel.
I used 13mm ERW 16g box to brace
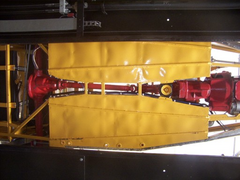 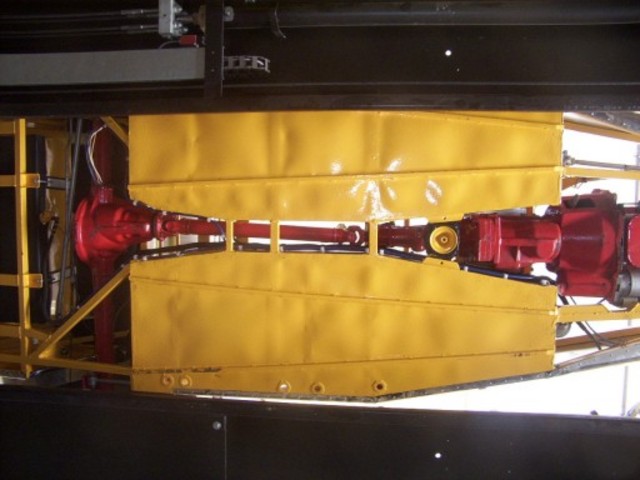 Rescued attachment Underneath.jpg
If you can keep you head, whilst all others around you are losing theirs, you are not fully aware of the situation
|
|
James
|
posted on 15/7/04 at 08:32 PM |
|
|
quote: Originally posted by pbura
If you have lengthwise beads rolled into 18 awg, you should have no drumming.
Was looking for a thread to refer you to, but am having no luck with the 'search' button today. Hopefully, someone who has done this will
pipe up 
Pete
I've done it that way! :-D
18 gauge or possible thinner- can't remember.
I ran two swages down each one and then fully welded it.
No pics to show you though.
|
|
kiwirex
|
posted on 15/7/04 at 10:52 PM |
|
|
Round bits on Mark's bottom (ooh err)
Mark, in your photo of the floor of your car showing your bracing, what are the round bits near the side for??
|
|
locost_bryan
|
posted on 16/7/04 at 12:33 AM |
|
|
just don't use a 12 guage - you'll blow your nuts off!     
Bryan Miller
Auckland NZ
Bruce McLaren - "Where's my F1 car?"
John Cooper - "In that rack of tubes, son"
|
|
Dale
|
posted on 16/7/04 at 12:28 PM |
|
|
Thanks for the info, being I am 245lbs 16 gauge may be more suitable with the bracing as well., I plan on welding in the tunel sides as well. What
are the opinions on how 18-16 gauge will hold up to broken or propshaft or exploding transmission. I have seen the pics of the damage on one done in
alloy, and that did not make me feel very safe as I should eventually be pushing somewhere between 225-300hp.
Thanks
Dale
|
|
andkilde
|
posted on 16/7/04 at 01:21 PM |
|
|
Hmmn, the Locost racers have to add an additional diagonal to protect themselves from a potentially flailing prop -- seems a good idea to me (as well
as a mirrored tube to protect the passenger in a road car). A prop wagging about would make a marvelous "can" opener and steel sheet,
regardless of guage, is not terribly resistant to tearing.
On the other hand, if your prop tears one cheek off you'll be able to hang out with all of the gimps at the motorcycle races...
Cheers, Ted
|
|
Ben_Copeland
|
posted on 16/7/04 at 06:14 PM |
|
|
quote: Originally posted by kiwirex
Mark, in your photo of the floor of your car showing your bracing, what are the round bits near the side for??
Look like drain holes to me
Ben
Locost Map on Google Maps
Z20LET Astra Turbo, into a Haynes
Roadster
Enter Your Details Here
http://www.facebook.com/EquinoxProducts for all your bodywork needs!
|
|
Mark Allanson
|
posted on 16/7/04 at 07:27 PM |
|
|
Yes, they are drain holes, M20 heavy washers continuously welded into the floor in the corner of every sealed area. having no roof I expect the car to
leak a bit !
If you can keep you head, whilst all others around you are losing theirs, you are not fully aware of the situation
|
|
James
|
posted on 17/7/04 at 09:08 AM |
|
|
Hmmm, you've made me worried I need to go drill some holes in my floor now!
One reassuring thing though Mark- your floor is a ripply as mine! It took me ages to get that special aerodynamic effect though!
James
|
|
Dale
|
posted on 17/7/04 at 01:18 PM |
|
|
For welding in the floor, have most gone for stitch welding it in first and then full weld the entire thing in or to drill the floor similar to
riviting it in but then plug weld it in by welding through the holes?
Thanks again.
Dale
|
|
JoelP
|
posted on 17/7/04 at 01:46 PM |
|
|
i stitched mine, then did it full. I like the idea of using thin guage with creases in it. mine is 16g, the sides 22g. with fully welded transmission
tunnel sides.
|
|
Mix
|
posted on 17/7/04 at 04:05 PM |
|
|
M20 heavy washers continuously welded into the floor
Is global warming really having that much effect down your way ??
I'll go for 3mm holes in the floor, rain up here is quite thin, if persistant. 
Mick
|
|