JohnN
|
posted on 25/2/04 at 09:24 PM |
|
|
Fully welded seat belt anchorages
I'm welding in place, triangles of 3mm plate for seat belt anchorages. SVA says that they must be fully welded in place.
This means not stitch welded, I know.... but does anybody know for sure if this means both sides, back and front or just one side.
Thanks John
|
|
|
Staple balls
|
posted on 25/2/04 at 09:26 PM |
|
|
personally, i'd weld as much as you can. it might save your life...
|
|
JoelP
|
posted on 25/2/04 at 09:35 PM |
|
|
i did both sides on mine, theres no point leaving an easy place for it to start tearing/splitting.
|
|
craig1410
|
posted on 27/2/04 at 12:10 AM |
|
|
I suppose if you are getting full penetration then it shouldn't matter but that said, I will be doing both sides!
Craig.
|
|
Simon
|
posted on 27/2/04 at 01:05 AM |
|
|
John,
Something like this - welded both sides, except mine are 6mm plate - I doubt 3mm plate will be up to much.
http://www.locostbuilders.co.uk/photos.php?action=showphoto&photo=10000059.jpg
Same reasons as have already been mentioned.
ATB
Simon
|
|
craig1410
|
posted on 27/2/04 at 01:07 PM |
|
|
Simon,
Unusually I'd have to disagree with your suggestion that 3mm steel is not sufficient for the seatbelt mounts. I'd have thought that 3mm
steel will take more load than the webbing which the seatbelt is made from! Also, I don't see the point in welding 6mm steel plate onto 1.6mm
tubing unless you have a much greater weld area than you appear to have as the 1.6mm tubing will surely tear before the 6mm(or 3mm) plate gets
anywhere near maximum load.
Remember that it is a requirement (IIRC) that the seat belt mounting bolts must be working in shear and not tension and thus you are pulling sideways
through the steel and not trying to pull the captive nut through the steel directly.
Cheers,
Craig.
|
|
locoboy
|
posted on 27/2/04 at 02:46 PM |
|
|
Craig,
Can you clarify the last bit about shear and tension again for me (thicko!)
I was planning on just welding in a triangle and having the eye bolts come out at 90 deg to the triangular plate, is that ok?
ATB
Locoboy
|
|
ned
|
posted on 27/2/04 at 03:13 PM |
|
|
question on similar lines, do you just drill a hole and put he bolt through with nut on the other side of the plate or does the hole need to be
threaded with a locknut or nylock on the back?
Thanks,
Ned.
ps my harnesses arrived today, at last! woohoo!
beware, I've got yellow skin
|
|
jonti
|
posted on 27/2/04 at 03:29 PM |
|
|
May be a muppet question but..if your tubes are made from 2mm steel can you just drill though and bolt direct to the rail ie x2 2mm = 4mm thick
effectively
OFROK
|
|
locoboy
|
posted on 27/2/04 at 03:36 PM |
|
|
Jonti,
I think that would create a big hole in the in relation to the size of the tube itself rendering it a very weak point in the chassis.
Maybe im wrong though?
ATB
Locoboy
|
|
Simon
|
posted on 27/2/04 at 09:17 PM |
|
|
Craig,
I'm not going to argue with your thinking, in fact I'd go along with what you are saying - production car belts are bolted into little
more than 16swg with a nut on the back
However, the reason I've gone for 6mm is (bearing in mind the SVA book comment in Section 5 - Annex 1 refers to "In a severe accident, the
seated(?) occupants can exert huge loads ..... iro 1.5 tonnes...for 75 kg person..) not the tearing of the load bearing chassis rails, but the
derformation of the fillets themselves.
According to SVA quote above you could have 375 kg of shear through 3mm. My problem here is twisting of fillett followed by pull through of bolt.
Might be ok, better with 6mm though.
When I ordered my harnesses they came with (drilled & tapped) 5mm steel plate to be welded to chassis
Any structural engineers on here care to comment - please!
Anyway, this may interest you -
I drove car out of garage today
ATB
Simon
|
|
Mark Allanson
|
posted on 27/2/04 at 09:32 PM |
|
|
I made my inboard mount from 3mm steel with 10mm square tapped block, they are welded into the triangulated transmission tunnel apperture, the
outboard ones are similar block, triangulated with 13mm ERW against the standard chassis tubes
 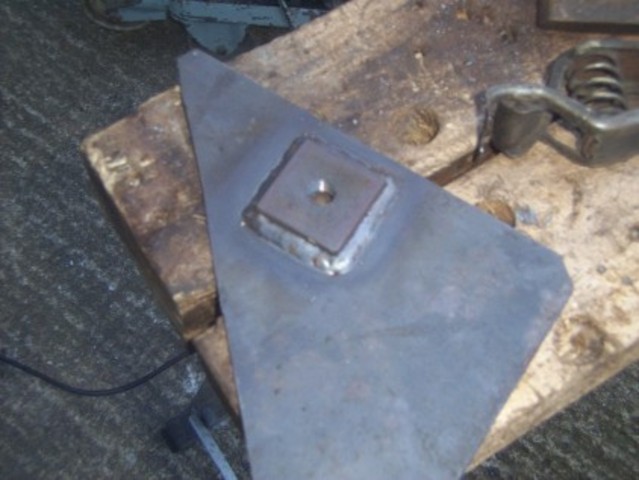 Rescued attachment Inner Belt Mounts.jpg
If you can keep you head, whilst all others around you are losing theirs, you are not fully aware of the situation
|
|
flak monkey
|
posted on 27/2/04 at 11:19 PM |
|
|
I would make the seat belt mounts as strong as you like. 3mm plate minimum though. As you say thicker plate will deform less if you do hit something.
Simple as that. Your limit should surely come when the chassis rails that the plate is attached to will deform or fail.
You could work this out approximately with a bit of maths. But its too late for me to do it, and no doubt someone can think of a better way of solving
it.
This is the way i would go about solving it;
You need to take your chassis rails and seat belt mount, model it with a force at the approximate angle the belt would pull at. Work out the shear
through the mounting plate, translate this to a force in the chassis tubes....and see which fails first. Sounds simple probably isnt! We have only
just been taught this sort of maths, so i dont trust my calculations on this. Anyone care to model it with FEA? Could be interesting.
Just a (rather long) suggestion
David
Sera
http://www.motosera.com
|
|
craig1410
|
posted on 28/2/04 at 12:11 AM |
|
|
Simon,
Yes I remember reading that in the SVA regs although I couldn't remember the figures they quoted. I went on the basis of a 20G deceleration
which would make a 75Kg person exert a total force of about 1500Kg's (or approx 15000 Newtons to be more correct) - Yes I know G isn't
10ms/s^2 before anyone says it. It's about 9.81 depending on where on the earth you are.
Anyway, with 4 harness mountings that is as you say about 375Kg's each mounting although I'd expect higher loads in the two upper
mountings due to torso and head mass. However, this load is only for a very short duration and I'd expect any tearing of the mountings to happen
progressively rather than suddenly.
What is perhaps more likely to happen is for the metal within the heat affected zone of the chassis tubes onto which the plate is welded to fracture
and for the mounting to break away. I don't want to scare you Simon but this MAY be MORE likely with 6mm plate welded to 16swg chassis rails due
to the higher amps used to weld it and thus the extra heat. Also, it may be better for a small amount of tearing or distortion in the thinner 3mm
plate to take place which may absorb some of the energy of the collision and avoid the catastrophic failure decribed above.
I'm not sure that FEA would be practical or accurate for what is quite a complex interaction, I'd be more interested in seeing some
race/rally car harness mounts after severe frontal collisions.
Mark, I like your solution as it gives a much larger area behind the mount than a simple nut which should help to avoid pull-through. Can I ask
though, does the 10mm steel plate comply with the "high-tensile" requirement for the seat belt mounting regs? I have heard it said that
some SVA testers require proof that the 7/16" nuts used are in fact high tensile and wondered how this would apply to a tapped piece of steel.
Did you perhaps use a grade of steel equivalent to 8.8 ton nuts?
To answer the question about shearing versus tension loads, tension would be where you are trying to pull the bolt directly out of the threaded hole
whereas shearing loads are where you are pulling "across" the bolt. I think as long as the seat belt mountings are far enough back then
you can't help but be apply shearing loads which is fine. As the lower mountings are moved forward then the shearing loads start to change into
tension loads and I guess there will be a point where the SVA tester will draw the line.
Cheers,
Craig.
|
|
craig1410
|
posted on 28/2/04 at 12:14 AM |
|
|
Simon,
Sorry I forgot to congratulate you on driving the car out of the garage! Well done that man!! I've had virtually no progress lately due to
problems with my road car but this weekend should see a bunch of loose ends tied up. My pedal box arrangement is causing me grief at present...
Cheers,
Craig.
|
|
Simon
|
posted on 28/2/04 at 01:35 AM |
|
|
Craig,
Agree small tearing may actually be desirable, so long as it's controlled.
Anyway, I left school with an O level in French, so I'm not got start getting all technical. 'Cos I probably won't understand it.
You, I reckon, did a bit better
But I'm still not changing my seat belt mountings
Off topic, thanks - it was quite good to have it actually move under it's own power, though it was very very slowly, and even more carefully
(see posting re clutch bleeding - still not sorted).
Still got one hell of a lot of work to do, even though the list goes something like:
finish and paint bodywork (make n/s engine panel/bonnett)
finish electrics (sort hazard and tidy wiring)
sort plumbing (fit exp tank and stop leaks).
fit new disc/calipers.
I was hoping to have all this done by now, but seems to be that for every hour of actual work done on the car, about 4 hours of thinking time is
involved.
I've just popped some more piccies in the archive, including the pedal box. It may or may not be of help. U2U me if you need dimensions etc.
ATB
Simon
PS - I'll get me email sorted soon!!!!!!!!!!!
[Edited on 28/2/04 by Simon]
|
|
britishtrident
|
posted on 13/3/04 at 07:53 AM |
|
|
With an automatic belt where the belt passes throught a loop at the top mounting t he force on the mount is effectively doubled , because it acts
like a pulley.
|
|
craig1410
|
posted on 13/3/04 at 11:00 AM |
|
|
I don't get that one, can you explain further please?
Cheers,
Craig.
|
|
JoelP
|
posted on 13/3/04 at 11:45 AM |
|
|
he means on reel belts, where it is bolted onto the floor and goes thru a bracket at the top, like in 'normal' road cars. you would have a
pulley effect on the top schmia. (technical term...!)
not relevant to most of us cos i think most are using harnesses, but worth remembering if you use the donor belts or equivalent!
|
|