pocket rocket
|
posted on 5/1/09 at 11:08 PM |
|
|
how do people make there engine mounts?
a bit ahead of my self i know (iv only just sorted fitting the engine iv got) but im keen to try either a BEC conversion or fit a 3sgte engine/box
from an mr2 after the summer and i was just wondering how people make there engine mounting points for the chassis???
From what i gather most are made of plate steel (please correct me if im wrong )
Do you need to find somewhere that will laser cut them and bend them to shape for you or is there a more DIY way of doing it?
I figured if i can bend it in the garage with a hammer then its not strong enough to take an engine 
|
|
|
zilspeed
|
posted on 5/1/09 at 11:13 PM |
|
|
My own mounts are 1.5mm thick ERW, 3mm steel plate, a hammer, a welder and a vice.
The only bent bits are few bits where I put a flange in here and there - it was hard work even with the vice and the hammer. I have no doubt
whatosever about the strength of what I have built.
I craned the engine in, picked the final position then got the measuring tape and hacksaw out. Not really as much of a deal as I had feared.
|
|
pocket rocket
|
posted on 5/1/09 at 11:27 PM |
|
|
is it possable to heat plate steel with a welder to help bend it to shape...
iv attached a pic of the mounts on the chassis at the mo, they look to solid to bend with just a hammer.
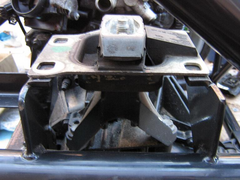 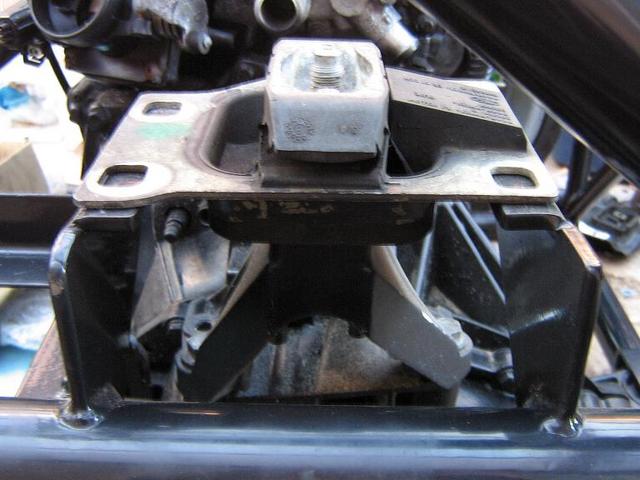 Rescued attachment mounting plate for loco.JPG
|
|
Mark Allanson
|
posted on 6/1/09 at 07:47 PM |
|
|
How I did it
If you can keep you head, whilst all others around you are losing theirs, you are not fully aware of the situation
|
|
C10CoryM
|
posted on 7/1/09 at 12:00 AM |
|
|
A few years ago someone showed me what is imo the easiest and best way to do engine mounts.
Basically what you do is get 4x suspension bushings. Mine were these ones just because thats what were laying around. Came with inner sleeves
too.
http://store.summitracing.com/largeimage.asp?part=ENS-7-3105G&Prod=Energy+Suspension+Rear+Control+Arm+Bushing+Sets&img=ens-7-3105g_w.jpg .
Then what you do is go to your local metal supplier and find a tube that fits snug on the outside. Cut the tube so that your inner sleeve is barely
shorter than the 2 bushings in the tube.
Those are my tubes that the bushings fit into. Ignore the doodling on the picture.
For the part that bolts to the engine make a flat plate. Then make 2x plates that weld to the plate, and have holes for a bolt to go through the
bushing sleeve.
Hard to explain. I will try to get pics of my mounts tommorow. I have to weld something to one anyhow.
Not sure if it helps you, but it's what I have found to be the easiest way. Use rubber if you want as even with rubber the mounts will be
stiff. Mine are poly which make it pretty much solid.
Cheers.
[Edited on 7/1/09 by C10CoryM]
"Our watchword evermore shall be: The Maple Leaf Forever!"
|
|
t.j.
|
posted on 7/1/09 at 12:57 PM |
|
|
I use the Sierra one's.
They are angled, so bit more work. And the steering shaft could be a problem...
Maybe the rubber parts are too flexy so maybe they need further on to be replaced by Land Rover ones.
[Edited on 7/1/09 by t.j.]
Please feel free to correct my bad English, i'm still learning. Your Dutch is awfull! :-)
|
|
pocket rocket
|
posted on 7/1/09 at 08:34 PM |
|
|
Cool, thanks for the help and the pics
whats ERW???
|
|
Alan B
|
posted on 7/1/09 at 09:12 PM |
|
|
quote: Originally posted by pocket rocket
Cool, thanks for the help and the pics
whats ERW???
"Electric resistance welded" tubing..the main stuff we use for chassis....the type with seam on one side.
|
|
pocket rocket
|
posted on 7/1/09 at 09:17 PM |
|
|
ha ha thanks... i really need to get a welder!
iv told the other half that if i get a welder il weld the washing mashine to the fridge... she doesn't seem that keen lol
|
|
Cheffy
|
posted on 10/1/09 at 03:39 PM |
|
|
Hi,
I did my Zetec mounts similar to how Mark did his above.
Link to Zetec mount pics
Pics near the bottom of the page. Not completed in the pics but finished since. I'll get some more pics up shortly.
I'm also building a V8 and this is how I made the mounts for it:-
Link to V8 mounts
About 3/4 the way down the page.
HTH,
Mart.
[Edited on 10/1/09 by Cheffy]
Farts are like Rock'n'Roll. You love your own but you hate everybody else's. Lemmy, Motorhead.
|
|
Valtra
|
posted on 10/1/09 at 07:01 PM |
|
|
have a gander at the mounts in the donor make a few measurements then fabricate similar on your chassis shouldn't be too much bending involved
. I fitted a steady bar between engine and top rail as well to cut sideways wobble on the soft old Fiat engine mounts
"If it looks like it works and it feels like it works, then it works"
|
|
pocket rocket
|
posted on 11/1/09 at 05:25 PM |
|
|
good idea
to the people that have made there own mounts - did you have some one cut the plate steel into shape for you or did you do it your self, and if so
how?... do you need a plasma cutter?
|
|
Valtra
|
posted on 11/1/09 at 06:30 PM |
|
|
3mm plate should be fine then use a hacksaw for the basic shape and then an Angle grinder to take off bigger lumps and a file to fettle . if you have
a plasma cutter fine use that but unless you are setting up to manufacture engine mounts it's hardly worth the bother , and likewise if you
have access to a profile cutter lucky you , but it's not worth driving more than a mile or two to access one just for a couple of engine mount
plates . quicker to fettle-em
"If it looks like it works and it feels like it works, then it works"
|
|
pocket rocket
|
posted on 11/1/09 at 06:58 PM |
|
|
thats what i wanted to hear
its good to know that something as major as fixing the engine in place can be done with a saw, grinder and a bit of thought and hard work.
i don't have a plasma cutter.... but i really want one... although im not sure why ha ha
|
|
Valtra
|
posted on 11/1/09 at 07:06 PM |
|
|
quote: Originally posted by pocket rocket
thats what i wanted to hear
its good to know that something as major as fixing the engine in place can be done with a saw, grinder and a bit of thought and hard work.
i don't have a plasma cutter.... but i really want one... although im not sure why ha ha
I could actualy sell you a new one but you won't want to hear the price
Have fun
"If it looks like it works and it feels like it works, then it works"
|
|
C10CoryM
|
posted on 11/1/09 at 09:28 PM |
|
|
Ok, I finally got to the shop today.
Not sure if it helps, but I find this a really easy and good way of doing mounts.
Like I said in my previous post you just get some rubber or poly bushings and find a tube to fit over top.
For the part that bolts to the engine, make a cardboard template of the flat part (use grease pencil on the block to find out where the holes go on
template). Get some flat stock. Mine are just 3.5" wide flat stock cut to shape using a cutoff wheel in my 4.5" grinder. Then using some
more of the same flat stock, cut two pieces for the "ears" that the bolt goes through. Drill holes in ears, then position engine in
place. Bolt ears to bushing/tube then tack in place to the engine plate. Once that is done you can add whatever support you need to get your chassis
to that tube.
Notes:
- I used a piece of 2x2" tube, drilled a hole through it with a holesaw the same size as my bushing tube, then cut the 2x2 tube in half to get a
perfect fit.
-these mounts will be very stiff even with rubber bushings. With poly they will be pretty much solid. I don't want my heavy engine crashing
around much anyhow.
-don't light your bushings on fire when tacking . Remove them when doing any welding.
-buy good quality cut off wheels for your hand grinder. The make life much easier for all cutting. I've gone through about 5 of them on my
chassis so far. Cut like butter and hold a straight line.
Anyhow, hope this helps someone.
Cory.
"Our watchword evermore shall be: The Maple Leaf Forever!"
|
|
C10CoryM
|
posted on 11/1/09 at 09:32 PM |
|
|
two more notes
Add some boxing on the ears to stiffen them. Do this after you have your other tubes in place.
And also leave yourself some room to play with otherwise it can be difficult to get the engine in after final welding. I had to file the holes in the
ears a little to re-align them. Also had to hit with a hammer to spread the ears a little. Nothing to major though.
"Our watchword evermore shall be: The Maple Leaf Forever!"
|
|