blueshift
|
posted on 5/8/05 at 09:00 AM |
|
|
way to unearth an ancient topic!
|
|
|
locostv8
|
posted on 26/5/06 at 05:07 PM |
|
|
Adding fuel. This happened to someone elses car.
Construction pic.
These front control arms bent under heavy braking on the rear tubes only, causing the wheels to toe out, 13/16" each side! Not good!
I'll need to redesign and build new.
I have a couple theories why that happened. The most prominent: The
original arms had a shorter plate that the shock mount was welded to, and
it's profile was completely straight. The swaybar attachment bracket was
welded just inboard of that plate, directly on the tube, causing a
point-load on the arm under cornering. Bad idea. I underestimated the
force the swaybar would impart on the arm, and I'm pretty sure that's what
started a small amount of the bending. Add sticky tires, track pads that
finally got up to temperature one day, and under heavy braking (no cornering
involved whatsoever) the remainder and majority of the bending occured. As
that rear tube bent, it caused a severe toe out condition, which only helped
the bending along, as you might imagine.
The fix:
I made the new LCA's out of 1" DOM again, but with a .100" wall instead of
.065", I lengthened the "shock plate" such that the sway bar attachment
braket would weld to it instead of directly to the tube, and I made a gentle
curve in the plate between the tubes this time. I also added a 1" 16GA
square tube brace under the plate as far inboard as I could, which is also
directly under the swaybar bracket. No problems so far, and I think I've
pushed the car plenty hard enough since then with no issues.
My car weighs 1500lbs. and I think the arms were just not beefy enough, and
I had some bad design in there as well.
http://wrangler.rutgers.edu/gallery2/v/7slotgrille/hssss/
|
|
Liam
|
posted on 26/5/06 at 05:36 PM |
|
|
 
Blimey!! Create a stress concentration with the straight cut piece of plate, then weld an anti roll bar mount to it!! Scary engineering
decision. The plate is way too thin too - look how it's bent under the suspension loads. Nice looking design but rather minimalist on the
material. I'd worry about that bellcrank mount too.
Liam
|
|
t.j.
|
posted on 26/5/06 at 06:44 PM |
|
|
Reading all this i concluded that the Avon-book ain't that bad.
My arms will be made of 25mmx3 seamless pipe with a plate of 10 mm between them.
I don't want any ......whatever with my suspensions.
[Edited on 26/5/06 by t.j.]
|
|
craig1410
|
posted on 26/5/06 at 07:22 PM |
|
|
TJ,
I'm not sure that using 10mm plate is actually a good idea because you need the plate to flex a bit to avoid creating a stress concentration on
the wishbone tube at the end of the plate. The best designs available today try to get the shocker lower mount as close as possible to the lower
balljoint and incorporate a curve along the inboard edge of the plate to allow a bit of flex and spread out the stress along the wishbone tube. I
think they usually use 3mm plate.
I'd recommend copying the design of the likes of the GTS Tuning wishbones which seem to be highly regarded. They use oval tubing as well which
is prettier.
Cheers,
Craig.
[Edited on 26/5/2006 by craig1410]
|
|
DIY Si
|
posted on 26/5/06 at 07:27 PM |
|
|
One of the best ideas I've seen recently was at stoneleigh. Damned if I can remeber who it was, but someone had a special mount for the shocker
which bolted in the same place as the bottom ball joint. That should basically remove most of the bending moment. Just then need arms strong enough to
take the load. It would also help to have nice light little wheels, light brakes + calipers etc..
|
|
t.j.
|
posted on 26/5/06 at 07:34 PM |
|
|
quote: Originally posted by craig1410
TJ,
I'm not sure that using 10mm plate is actually a good idea because you need the plate to flex a bit to avoid creating a stress concentration on
the wishbone tube at the end of the plate. The best designs available today try to get the shocker lower mount as close as possible to the lower
balljoint and incorporate a curve along the inboard edge of the plate to allow a bit of flex and spread out the stress along the wishbone tube. I
think they usually use 3mm plate.
I'd recommend copying the design of the likes of the GTS Tuning wishbones which seem to be highly regarded. They use oval tubing as well which
is prettier.
Cheers,
Craig.
[Edited on 26/5/2006 by craig1410]
I'm confused here. The book say 10 mm.
I'm planning to laser-cut the plate so that the pipe does actually fits over the plate.
The balljoint wil as close as possible to the lower mounting of shockabsorber.
So you think it's better to make a plate for the ball-joint and one for the absorber mount?
my idea was cut everything out of one plate. Hmmm
|
|
DIY Si
|
posted on 26/5/06 at 07:44 PM |
|
|
One plate is ok, but don't fit it to the top of the tubes as per the book. This will weaken the top edge of the tube. Try to put the plate in
between the tubes as this gives the most extra strength for the least weaken by heat. Sorry if that makes little sense for the reason, but I know what
I'm trying to say.
|
|
t.j.
|
posted on 26/5/06 at 07:53 PM |
|
|
quote: Originally posted by DIY Si
One plate is ok, but don't fit it to the top of the tubes as per the book. This will weaken the top edge of the tube. Try to put the plate in
between the tubes as this gives the most extra strength for the least weaken by heat. Sorry if that makes little sense for the reason, but I know what
I'm trying to say.
Damn, wish i have my stuff around.
I want to make one plate which is holding the balljoint and the lower mount. where the pipes hit the plate i wanted to make a sticky thing about 25 mm
which goes inside the pipe. Then take the welder an welded all around. Cause the plate goes inside the pipe the whole plate will be in te middle of
the two pipe. I'm planning to make the edge of te plate 45 degr. so that the weld is flatted.
So 10 mm plate isn't a problem or schould i go back to the drawing-table?
|
|
DIY Si
|
posted on 26/5/06 at 07:53 PM |
|
|
Like this:
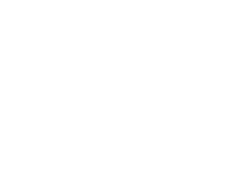 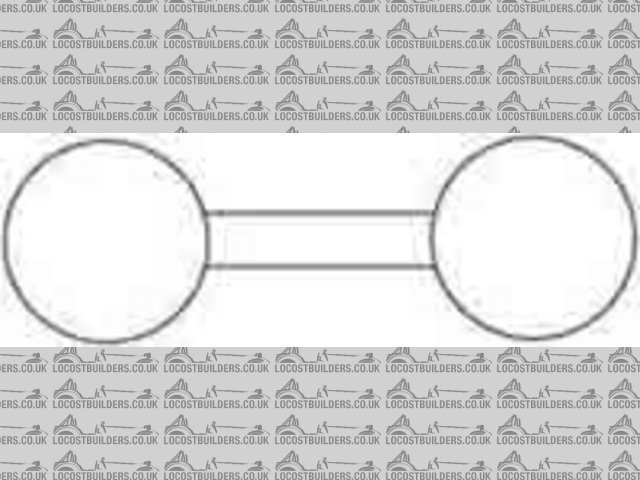 Rescued attachment Untitled-1.jpg
|
|
DIY Si
|
posted on 26/5/06 at 07:58 PM |
|
|
Arse it's not working, The plate needs to be central to the two tubes, ie in the middle vertically. The edges want to be square, but shaped to
fit the tubes.
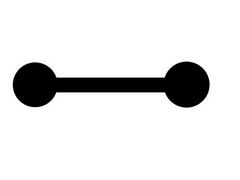 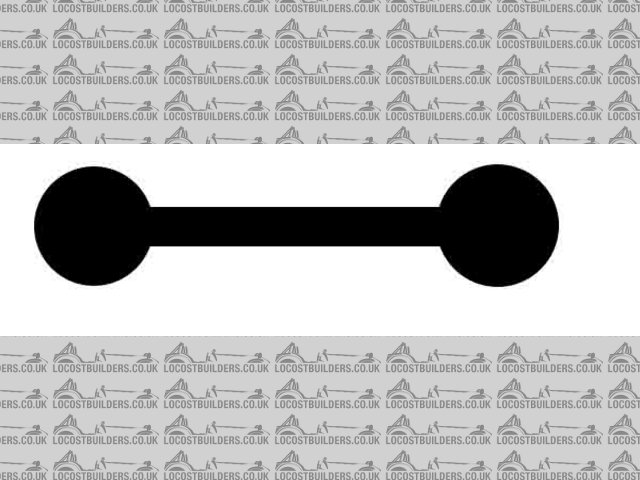 Rescued attachment 121.jpg
|
|
flak monkey
|
posted on 26/5/06 at 08:03 PM |
|
|
GTS lower wishbone:
http://gtslocost.locostsites.co.uk/images/31.jpg
Sorry about pic quality. Pre digicam!
Now this is from memory: 6mm lasercut plate welded along the neutral axis of the arms. Very simple design. The plates are available from GTS to make
your own bones from.
David
Sera
http://www.motosera.com
|
|
t.j.
|
posted on 26/5/06 at 08:13 PM |
|
|
quote: Originally posted by DIY Si
Arse it's not working, The plate needs to be central to the two tubes, ie in the middle vertically. The edges want to be square, but shaped to
fit the tubes.
Ok, that's my idea also.
Where the edges make contact i wanted to cut under 45 degr so there is room to weld. Also at the bottom.
@ david: Is 6 mm better then using the 10mm?
[Edited on 26/5/06 by t.j.]
|
|
flak monkey
|
posted on 26/5/06 at 08:19 PM |
|
|
The plates may be 8mm. I dont have them to hand to measure them. I am 95% sure they are 6mm though. I would say 10mm is seriously overkill. Theres no
harm in using it, your main problem will be getting decent pentration on a weld on 10mm plate to 2 or 3mm tube...
Sera
http://www.motosera.com
|
|
craig1410
|
posted on 26/5/06 at 09:03 PM |
|
|
Hi,
Sorry t.j. I don't mean to confuse you...
I would say that 10mm is too thick for a few reasons (weld penetration & too stiff compared to the wishbone tubing being the main ones). I'd
say that you wouldn't want to use plate any thicker than twice the thickness of your wishbone tubing to ensure effective welding and to prevent
a stress concentration appearing in the tubes.
In general, a structure is only as strong as the weakest link. However, it is possible to make a weak link even weaker by making an adjacent link
unnecessarily strong. Ideally you want the entire wishbone to bend along its entire length rather than bend at one particular point to avoid fatigue
and early life failure.
I hope this helps,
Craig.
|
|
locostv8
|
posted on 26/5/06 at 09:14 PM |
|
|
Here is maybe a bit more fuel. Anyone familiar with DAX Camber compensation & antiroll suspension? http://www.daxcars.co.uk/start.htm
http://wrangler.rutgers.edu/gallery2/v/7slotgrille/hssss/
|
|
MikeRJ
|
posted on 26/5/06 at 10:50 PM |
|
|
quote: Originally posted by locostv8
Here is maybe a bit more fuel. Anyone familiar with DAX Camber compensation & antiroll suspension?
Fairly, but it has little to do with the strength and design of the Locost bottom wishbones. Whilst a clever system, the DAX camber compensation
system does not fair so well with one wheel in bump. Look at the picture of the body in roll and then tilt it so the body is level and notice the
effect on the camber...
|
|
kb58
|
posted on 26/5/06 at 11:51 PM |
|
|
Yup, what he said ^. For all that effort it doesn't work on a one-wheel bump. I also remember reading it was really hard to set up, in fact
the factory wouldn't sell it as a kit - they have to set it up (as far as I remember.)
Mid-engine Locost - http://www.midlana.com
And the book - http://www.lulu.com/shop/kurt-bilinski/midlana/paperback/product-21330662.html
Kimini - a tube-frame, carbon shell, Honda Prelude VTEC mid-engine Mini: http://www.kimini.com
And its book -
http://www.lulu.com/shop/kurt-bilinski/kimini-how-to-design-and-build-a-mid-engine-sports-car-from-scratch/paperback/product-4858803.html
|
|
locostv8
|
posted on 27/5/06 at 03:53 AM |
|
|
I had wondered if bumps might upset it. If it works it would be great but seems like a lot of trouble to eliminate a sway bar.
http://wrangler.rutgers.edu/gallery2/v/7slotgrille/hssss/
|
|
Syd Bridge
|
posted on 27/5/06 at 09:06 AM |
|
|
Anyone ever wondered why you don't see that Dax system on topend racecars other than a few Dax's? Patents aside, as top teams would pay
the licence fee if it was worthwhile.
Cheers,
Syd. 
|
|
andyps
|
posted on 27/5/06 at 11:13 AM |
|
|
Relative to the Dax system, I have always felt that a well designed unequal length wishone set up should provide most of the benefits all the time and
does not have the problem of a one side bump.
Andy
An expert is someone who knows more and more about less and less
|
|
Uphill Racer
|
posted on 1/11/06 at 01:09 AM |
|
|
When they can make the front end react to it, it may work
|
|
onzarob
|
posted on 25/11/07 at 11:01 PM |
|
|
Wow what a long thread ( and over a long period of time!!!) and allot of technical details from knowledgeable people.
To summarise the solid points
If using a heavy engine beef up the standard locost design tube wall thickness/size.
With all lower wishbones weld the plate to the side of the tubes and NOT on top.
The Dax suspension is really a different topic and also at the other end of the car!!!
I must add that this is the sort of topic I wanted to find...I want to build something that doesn't break my neck...great stuff
|
|
britishtrident
|
posted on 26/11/07 at 07:48 PM |
|
|
Also the other main conclusion is you need a generous fillet radius on the plate.
|
|
MikeRJ
|
posted on 26/11/07 at 10:23 PM |
|
|
quote: Originally posted by onzarob
The Dax suspension is really a different topic and also at the other end of the car!!!
The Dax system is used on the front suspension, though it could be used on the rear I suppose if you can get all the linkages to clear the diff and
driveshafts etc.
|
|