britishtrident
|
posted on 15/4/04 at 10:56 AM |
|
|
The bigger=better idea seems to have caught hold of too many Locost builders who apply it to everything in sight. The original Lotus 7 chassis was
mainly designed around two very different different engines the Ford 100e sidevalve with a 3 speed Ford gearbox and the 1220cc Coventry-Climax with a
BMC A series gearbox. The side valve produced 37 hp and the Climax in race tune about 100 bhp on a good day.
Both engine gearbox combinations weighed a lot less than a Pinto or even an Xflo the Climax with BMC gearbox was about half the weight of a 2 litre
Pinto engine with type 9 box..
What made the original 7 fun to drive was good reponsive handling and very light weight
In some areas the Locost/Westfield chassis is better than the Lotus one but in others poor detailing lets it down the wishbones being a prime
example. Another is the ridiculous ammount of bumpsteer that dictates the suspension be bone hard rather than the relatively soft ride of the original
Lotus built 7.
It is quite interesting to read comparative road test of various Lotus and Caterham Sevens one thing that comes out is that once they get past the
sheer blast power of the latest top of the range big engined Caterhams most road tester s seem to preffer the more nimble handling smaller engined
models and rate the narrow tyred softer sprung original Lotus models as more rewarding to drive than the latest Caterhams.
The problem these days is lack of suitable engines and gearboxes which are cheap to buy and install as a result the average Locost builder is
dropping oversized over weight engines into the chassis without regard to any of the implications..
Taking a leaf from the book of the 750MC racers of old Chapman, Broadley, Terry and Mallock who found that once power and weight started to increase
beyond about 140 bhp the simple 7 style spaceframe needed a rethink -- just look at the evolution of the chassis of the Mallock U2 class cars between
the first and the last A class car.
My personal solution is a cop out -- My car has relative low power small engine (a 1600 CVH) and fairly minor chassis and suspension mods along the
lines of those used by builders in Australia.
Other improvement like getting rid of bump steer and reducing the unsprung weight will give me winter lay up jobs in future years.
[Edited on 15/4/04 by britishtrident]
|
|
|
stressy
|
posted on 15/4/04 at 11:14 AM |
|
|
Total agreemnt
I agree with you completely, you need a bloody good chassis to fully exploit 150 bhp on either road or track.
Ive been a passenger in a superlight r300 (160 bhp) around a track and it was awesome. Having tried a couple of 140bhp caterham there superb (and i
have driven a couple of 190(claimed)hp westfields and alike as comparison.
K series, 4age, thats what you want. modern, light, 140bhp reliably...
|
|
Bob C
|
posted on 15/4/04 at 11:30 AM |
|
|
Just add to stressy's description of wishbone strut compression - consider the wheel end as a lever with the braking force acting at the
contact patch pivots at bottom BJ and top BJ. If bottom BJ is 8" up and top BJ 16" up (guesses) and 1000N braking force applied to the
contact patch - leverage says that will be 1000N pushing forwards on top BJ. So there MUST be 2000N pushingbackwards on bottom BJ. It's because
the brakes are trying to spin the upright forwards with the wheel. THAT's why I brought up compression loading on the back tube.
I also agree the 7 is supposed to be a light simple car- but I fully understand the lure of a big V8 engine!
Cheers
Bob C
PS 1000N braking force is NOTHING..... say 0.2G..
|
|
NS Dev
|
posted on 15/4/04 at 04:13 PM |
|
|
Quote:
For those who "feel" the failure was due to brake reaction forces may I point out that the front tube of the lower wishbone is under
tension when the brakes are applied and the failure is clearly not a tensile failure.
In addition a tensile failure would be more likely to occur on the lower wishbone in the weld between the front tube and the pivot bush tube.
[Edited on 15/4/04 by britishtrident]
Unless I am optically challenged it is the rear tube that has failed isn't it? Or am I being stupid?
|
|
NS Dev
|
posted on 15/4/04 at 04:20 PM |
|
|
quote: Originally posted by britishtrident
The plate isn't a reinforcing plate it actually weakens the wishbone, making it more generous may weaken the wishbone more making it more
likely to fail.
The plate should taper off very graually as on the GTS example. As someone pointed out way back ideally it should be welded on to the wishbone tube
centre lines not forming a lump the top again in this respect the GTS wishbone follows best practice.
The finish of the weld ends is particularly important -- ideally they should be ground as smooth as possible using a "Dremmel" or Die
Grinder to a void causing a sharp edged stress raising feature.
[Edited on 15/4/04 by britishtrident]
[Edited on 15/4/04 by britishtrident]
Sorry to keep picking on you but cleaning up the end of the weld will do very little, the heat affected zone is the significant stress raiser, not
only the change in section. This is why in my area of industry, companies like JCB extend their welds away from the end of a gusset or bracket and
onto the nearby relatively unstressed structure, so separating the section change from the heat affected zone at the end of the weld. (take a look at
a JCB rear boom, around the pivot pin reinforments, the welds trail off at an angle onto the flat boom plate to move the end of the HAZ)
|
|
cymtriks
|
posted on 15/4/04 at 08:31 PM |
|
|
Quote from earlier post
"Caterham have used 3/4" tube for 30 years with few failures, yet further up the thread a "calculation" showed that these
would bend at 3g accel on the wishbone, I just don't buy this. If it were right then all westfields, Caterhams plus all the locosts would have
broken!!!!!!!!!!"
And if they had been designed along the lines of the Lowcost wishbone a lot of them WOULD have broken. A 3g bump is roughly the upper limit for normal
road use. The calculation is telling the truth. The Lowcost book wishbone isn't up to the job, especially if you're going to give it some
serious use.
If you look at a Caterham wishbone you'll see that the spring is mounted much closer to the wheel upright which greatly reduces the bending
forces on the wishbone.
Another quote
"If you consider the lower shockabsorber mounting position for a moment, if it were positioned at the lower balljoint position then the lower
wishbone would have zero bending stress on it, it would be purely tension/compression."
Correct. Do I detect a basic knowledge of beam theory here???
"The shocker is mounted very close to the lower balljoint, the stress in bending is not that great..."
It isn't. It's mounted much further from the lower ball joint than a Caterham.
"the stress under braking however, is very great! Curbs on most tracks have the ability to bend even tough suspension components if you clip
them with the wheels loaded up (rather than unloaded as is the case with the inside wheels when "curb-hopping" "
....Maybe. The rear arm of the lower front wishbone is often the most highly stressed part of a car suspension.
I take the point that longitudinal, as opposed to vertical, forces may be the culprit. My calculations still show the relative strengths of the common
tube sizes. I'd recommend using 1 inch diameter tube for a Lowcost book wishbone.
|
|
NS Dev
|
posted on 15/4/04 at 08:44 PM |
|
|
Yes, you do "detect a basic knowledge of beam theory"!!!! I do have a little, having designed and built from scratch a few vehicles over
the past few years.
|
|
jcduroc
|
posted on 15/4/04 at 09:11 PM |
|
|
quote: Originally posted by jcduroc
quote: Originally posted by jcduroc
OK guys don't laugh because I'm really not gifted for drawing on PaintShop.
This is how I'm making my lower wishbones (Should be completed next saturday).
These are made for the Austin Maxi balljoints (Quinton Hazel QSJ602BLU) and the "things" to the left are the coilover mountings, going down
at 45º from the plane of the wishbone; these are intended to be as close as possible to the balljoint "action" point.
The tubes (that thing in red) come as convergent as possible to the same point and are made of 25 mm w/ 2 mm wall thickness (instead of the available
20 x 2.6); as someone said increase the diam. not the wall (moment of inertia).
I'd appreciate your (ponderate) comments on this design.
It would also be very pleasant to see some real calculations on all those bending, torsion, tension and compression loads (strains?) in the
"shi...est" situation described: braking (at 1G), taking the bend (1.2 G cornering, please) and hitting a bump (3G vertical?); come on guys,
share your skills!...
João
[Edited on 15/4/04 by jcduroc]
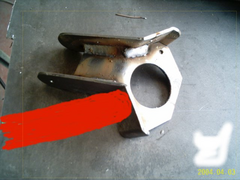 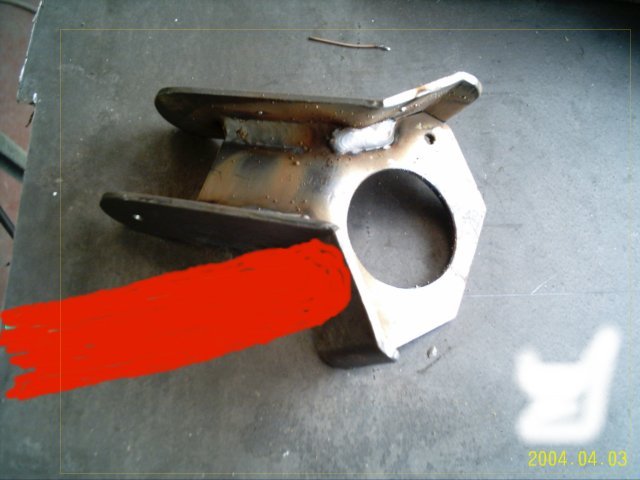 Rescued attachment Img_0067A.jpg
JCM
|
|
Bigfoot
|
posted on 15/4/04 at 09:52 PM |
|
|
I'm not trying to start an arguement here, but it is a forum.
Nsdev: The pictures would suggest that it is the rear tube which is failing, this is under compression, not tension. This has been established
earlier in the thread
Cymtriks: The size of the tube is not the issue, subtle changes in the angles of the tube relative to each other, rienforcing, and the applied
loads make a huge difference, if you were to copy the 3/4" Caterham part you mentioned, exactly, it would be fine on the V8 powered car.
Bobc : The alloy RV8 is no heavier that the pinto and other cast iron engines.
There is a lot of phseudo-engineering going on here, there is no mystery, it is just a badly designed wishbone.
Bigfoot (Bigmouth??) :-))
|
|
NS Dev
|
posted on 15/4/04 at 10:10 PM |
|
|
Nicely summarised Bigfoot!!
|
|
Bigfoot
|
posted on 15/4/04 at 10:36 PM |
|
|
Thanks mate, I might leave it alone now before I offend someone.
Cheers
|
|
NS Dev
|
posted on 15/4/04 at 10:37 PM |
|
|
Think I better had leave it now too!!
|
|
Bob C
|
posted on 15/4/04 at 11:03 PM |
|
|
I don't see an argument brewing, just a reasonably informed set of opinions on an important topic. That bottom wishbone always looked like the
dodgiest bit of the whole car & I'm pleased as punch that the debate is happening just before I make mine! FWIW I only remember agreeing
that the RV8 is very light (approx 150lbs lighter than a 5litre mustang engine!) & I believe anything cymtriks says!
JCduroc that looks like a very nice peice of construction; putting the spring/damper bolt in line with the balljoint will remove the beam/bending
stress from the wishbone tubes, but will probably increase the angle of the suspension unit from the vertical leading to a worse "reducing
rate" issue under bump. Design is all about compromise..!
Your design is clearly quite different from the book design in this respect so cymtriks analysis won't apply. Unfortunately my mechanical
engineering is qualitative beased on experience rather than quantitative based on thorough knowledge of the application of structural analysis so
I'm just glad cymtriks is on hand to give authoritative nuggets of wisdom when he does!
Wow long post, all b******t - ain't boddies good stuff! Use inch diam - you know it makes sense......
Bob C
|
|
craig1410
|
posted on 16/4/04 at 12:04 AM |
|
|
Hi,
I'm coming into this a bit late and I agree with the vast majority of what has already been said. However, for what it's worth I reckon
that having the spring wound up so far on the platform must put it close to bind-up under heavy braking/cornering. Could the spring be binding up
before the bump stop gets a chance to absord some energy? This would cause a big "spike" in the aforementioned bending loads and could
easily cause such a failure.
I'd strongly recommend that you get springs of a higher rating so that you can achieve the same ride height without needing the platforms wound
up so far.
Just my thoughts...
By the way, I have a set of Lolocost wishbones and I must say that they are very sturdy indeed and the welding is excellent. The level of
"finish" is poor granted and there are other issues which I won't bore you with here but I'd say they are structurally very
sound. IIRC they use 22 or 25mm x 2 or 2.5mm wall tubing. I'll check tomorrow.
Cheers,
Craig.
|
|
undecided
|
posted on 16/4/04 at 12:28 AM |
|
|
Surely it is better to bugger a wishbone than bugger a chassis. In racing wishbones are expendable items that break/bend rather than bugger an
expensive chassis.
Does make you wonder though i must admit as regards what we are actually buying from some places.
|
|
Bigfoot
|
posted on 16/4/04 at 03:02 AM |
|
|
I just couldn't stay away, could I? :-)
You are quite right BobC, it is an important issue, and should be discussed, I didn't really see it as an arguement, it's just that I am
fairly new around here and I didn't want to get off on the wrong foot. My typing style doesn't always come off as friendly as I would
like.
These safety issues worry me a bit though, I am a development engineer these days, but years ago I worked in the motor trade and have advanced trade
qualifications. I was also a vehicle inspector, you see some frightening things inspecting cars, and no-one ever thanks you for refusing to sign off
an unsafe vehicle. I couldn't help thinking of the consequenses of it letting go at 70+mph in heavy traffic.
Time to go, I am starting to sound a bit too establishment here.
Cheers
|
|
NS Dev
|
posted on 16/4/04 at 06:58 AM |
|
|
ah Bigfoot, another development engineer, me too!!
|
|
britishtrident
|
posted on 16/4/04 at 07:56 AM |
|
|
quote: Originally posted by craig1410
Hi,
snip
I'd strongly recommend that you get springs of a higher rating so that you can achieve the same ride height without needing the platforms wound
up so far.
snip
Trouble with fitting harder springs to the front it will or at least should cause gross understeer, using longer springs and adding more bump stop
rubbers may be another approach.
However consider the fact that most builders already use springs that are much higher a rate than normally sensible for the weight of the vehicle
and the handling balance of the Locost appears from reports to be quite unresponsive to large changes in spring rate at one end --- in one Locost
build diary I came across a builder who had change the fronts from 180lbs/i to 380lbs/i to (I quote) "cure bad understeer" !!!??
The extreme angle at which the front springs are mounted dosen't help but I suspect a lot is down to flexing of the front wishbones and spring
attachment points.
Yonks+ages ago I used to race Imps and Davrians cars of a similar weight range to the Locost, I found that even a 10lb/in change in the spring rate
at either end would alter the handling balance --- good evidence the chassis and wishbones were more than stiff enough. For race springs on the
Davrian we ran 190 lb/i on the front 240 lb/in on the rear.
[Edited on 16/4/04 by britishtrident]
[Edited on 16/4/04 by britishtrident]
|
|
britishtrident
|
posted on 16/4/04 at 08:09 AM |
|
|
jcduroc --
I like where the bottom of the damper mounts it brings the line of action of the force close to the ball joints centre line.
You could cut/grind away quite a bit of metal as the vertical plates approach the ball joint centre line without affecting the the
strength/stiffness.
Add a couple of nicely chamfer webs down from the wisbone tube to the damper mount and it looks good.
(also nice welding !)
|
|
JoelP
|
posted on 16/4/04 at 08:12 AM |
|
|
that is one benefit of the maxi ball joint over the cortina one, due to it being smaller you can get the shocker closer to it. I made mine so close
that the spring nearly hits the upper wishbone in droop! but i think thats because my top mounting point is quite far out. With a maxi ball joint you
could have the points in line nearly, if you follow my drift.
BTW, how many of you dreamed about failing wishbones last night!?!?!? i certainly was pushing the car home in a dream...
|
|
craig1410
|
posted on 16/4/04 at 05:12 PM |
|
|
I suppose what this goes to show is that perhaps we should all consider a track day, and subsequent inspection, as an essential post-SVA (or even
pre-SVA if allowed?) test of the car and its integrity. It's also perhaps a good test of our own driving skills too as many/most folk probably
haven't ever driven a powerful rear wheel drive vehicle and as we who have know, it's a bit different from your average 100BHP FWD
car...
If nothing fails or bends after a hard blast around the track then it should handle anything that the road throws at it, and if anything does fail on
the track then it's bound to be safer than a similar failure on the road. Obviously a progressive approach to testing would be wise before very
high speeds are involved...
Cheers,
Craig.
|
|
blueshift
|
posted on 16/4/04 at 06:03 PM |
|
|
mackie and I plan to take ours on a track day as soon as we get it finished, as much because of fear of the handling and 200bhp going through the back
wheels, as mechanical worries.
|
|
craig1410
|
posted on 16/4/04 at 07:24 PM |
|
|
Blueshift,
The only thing I'd perhaps get checked before any serious mileage is the wheel alignment as otherwise it might tend to eat the tyres...
Obviously with the de-dion rear end the alignment is fixed but mine is fitted with adjustable length trailing arms so I need to make sure that the
footprint is square.
Apart from that, hit the track and see what falls off...
Have you guys started building your chassis yet then?
Cheers,
Craig.
|
|
NS Dev
|
posted on 16/4/04 at 09:59 PM |
|
|
Just to throw yet more petrol on the bonfire!! Just been looking at some Westfield wishbones and the shocker mounting point looks the same as the
"book" locost one (without the benefit of a ruler)
Also just put the deposit on my Stuart Taylor IRS chassis/body set.
|
|
blueshift
|
posted on 16/4/04 at 11:20 PM |
|
|
craig, not quite.. but I have gathered the materials for the build table and starting the chassis is the next thing on the todo list. I've been
busy the last couple of weeks, and bashing my road car in the spare time (see thread in "anything else" - it's buggered)
one day 
|
|