britishtrident
|
posted on 17/3/05 at 08:57 AM |
|
|
quote: Originally posted by MikeR
whats the westfield camel hump - have you got any pictures?
The drawing came from somewhere out on the web my own verson is different in that "O" isn't angled.
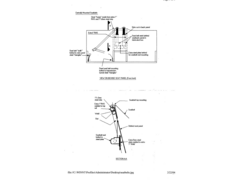 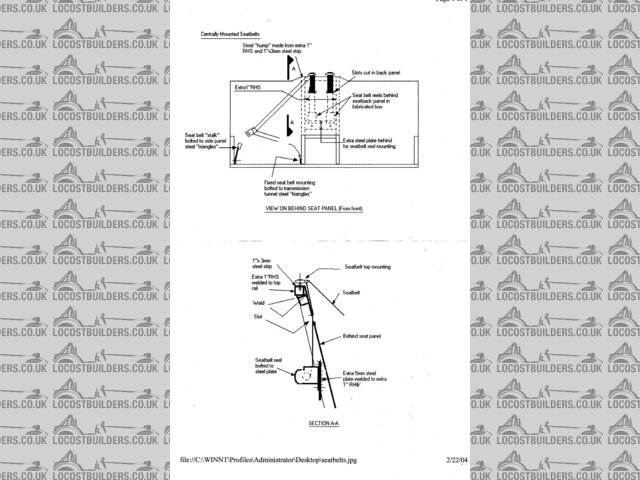 Rescued attachment camel.jpg
|
|
|
ned
|
posted on 17/3/05 at 09:52 AM |
|
|
so the hump is simply a bit of steel welded onto the top bar and profiled to give extra height for the seatbelt mount..?!
Ned.
beware, I've got yellow skin
|
|
britishtrident
|
posted on 17/3/05 at 11:41 AM |
|
|
Yes apart from height it adds bending & torsional stiffness to "O"
|
|
MikeR
|
posted on 17/3/05 at 11:49 AM |
|
|
not sure about bending. the seat beld is now anchored further away from the verticals that hold O in place, thus acting as a lever to bend O
|
|
britishtrident
|
posted on 17/3/05 at 12:53 PM |
|
|
quote: Originally posted by MikeR
not sure about bending. the seat beld is now anchored further away from the verticals that hold O in place, thus acting as a lever to bend O
Thats going to happen with any mounting of this type and one of the reasons I switched 2mm wall tube for "O" because it has a much
greater ressistance to buckling type failure than 1.5. The centre of "O" is also braced to the tunnel by 2 vertical goal posts .
|
|
clbarclay
|
posted on 17/3/05 at 04:55 PM |
|
|
What about the alternative used by luego for example, which is to have a lower tube in the roll bar which has the seat belt bolted to it.
Does this design have any particular draw backs if you need higher seat belt mountings?
|
|
ned
|
posted on 17/3/05 at 10:38 PM |
|
|
Just been over to a friends workshop this evening and he so happens to have a lathe, drills and 7/16" unf tap.
Only problem now is that the rod we started turning down and tapping turned out (no pun intended!) to have a seam through the middle of it, so we came
to the conclusion that (the old shuttering pin we were using) must be rolled somehow in construction and hence wouldn't be up to the job once
turned down to the right size
Problem i have now is sourcing a foot or so of 16mm + rod. it can be larger diameter as i have the ability to turn it down, but i can't get
anywhere as i work in london and am away this weekend.
can anyone help? i can't see the point in paying for the threaded tube when i can make it myself but you can't buy a 12" piece from
a stockist as there will be a minimum length and delivery etc so it becomes unfeasable.
suggestions?
Ned.
beware, I've got yellow skin
|
|
MikeR
|
posted on 17/3/05 at 11:23 PM |
|
|
Ned, i'm formulating a cunning plan ...... send me a U2U telling me how quickly you want these mounts - I might be able to get you the steel but
it will cost you 8 1" mounts and postage back
(this is assuming the steel and postage to you costs less than 8 mounts from Darren)
[Edited on 17/3/05 by MikeR]
|
|
Mix
|
posted on 18/3/05 at 07:21 AM |
|
|
Why not buy 16mm bolts and fabricate the tubes from them?
Mick
|
|
Hornet
|
posted on 18/3/05 at 08:03 AM |
|
|
Ned.... Quote- the plate and nut idea is a good one (though i only have nylocks which will melt during welding!) as it could be hidden by a tonneau
style boot cover, will have to see.
I have used plate welded with bolt and nyloc nut. I am of the belief this will pass. There is no need to weld the nut on?
J
|
|
MikeR
|
posted on 18/3/05 at 08:34 AM |
|
|
Welding the nut on just makes things a lot easier, you put the seat belt anchor through the plate and don't have to worry about getting a
spanner in behind.
Also by making the threaded part as large as possible (i think) youre making it safer as there is more steel to counteract the bending force.
Although if a single bolt on a suspension mount is acceptable on a production car this is probably a non issue.
|
|
ned
|
posted on 18/3/05 at 09:53 AM |
|
|
Mix,
We thought about using bolts, but has most are coated/hardened we thought it might cause problems when cutting on the lather and damaging his bits.
I'm planning on making the threaded tube and welding it through the top chassis rail, not behind it as this should be strongest. If necessary
I'll make a top hat/sleeve to raise the belt if necessary for Sva.
MikeR,
That sounds like a good arrangement. I'd like to get the mounts made by the end of next week as I'm hoping to complete my chassis for
powdercoating over the easter weekend. Check out the postage cost and let me know (I'll need a longer length to do yours as well obviously, prob
nearer 2' so bear this in mind.
I was working on 7/16 unf tap and turning the od down to approx 14mm on the tube, to make drilling through the chassis rail as easy as possible. 13mm
won't leave enough meat round the thread and will probably lead to distortion when welding.
Ned.
[Edited on 18/3/05 by ned]
beware, I've got yellow skin
|
|
Mix
|
posted on 18/3/05 at 09:56 AM |
|
|
BZP 8.8 bolts will turn fine and won't dasmage the lathe or tooling
Mick
|
|
ned
|
posted on 18/3/05 at 10:11 AM |
|
|
Thanks for the info mix, would be good if I had any bolts big enough, but don't think anything i have has 14mm+ shank. will wait and see if
miker and i can sort something out.
Miker,
thinking about postage costs, it must be cheaper to send me some steel bar/rod than pay darren £23 + postage for his tubes.
royal mail standard parcels is about £10 for upto 10kg iirc, that would cover it surely..
Ned.
Ned.
[Edited on 18/3/05 by ned]
beware, I've got yellow skin
|
|
MikeR
|
posted on 18/3/05 at 10:12 AM |
|
|
Ned, need to cost postage but i can get two 15mm mild steel bars 30cm long from metal supermarket. one for you, one for me for £3. I'm guessing
worst case postage is £7.20..........
so return postage back to me shouldn't be more than 7.20.
I think its worth it, so are you interested?
[Edited on 18/3/05 by MikeR]
|
|
ned
|
posted on 18/3/05 at 10:16 AM |
|
|
Mike,
agreed, will u2u my address..
Ned.
ps if you could get me an extra 30cm bar and i'll reimburse you the difference + any extra postage cost that'd be well handy.
[Edited on 18/3/05 by ned]
beware, I've got yellow skin
|
|
MikeR
|
posted on 18/3/05 at 04:11 PM |
|
|
u've got u2u Ned and don't worry about the extra bar, it was something like 1.50 ex vat.
|
|
ned
|
posted on 18/3/05 at 04:20 PM |
|
|
u2u backatcha..
beware, I've got yellow skin
|
|
ned
|
posted on 29/3/05 at 07:57 PM |
|
|
Just to bring this one back up, here's a pic of how I sorted my top mount out inthe end and gained a bit of extra height that i needed...
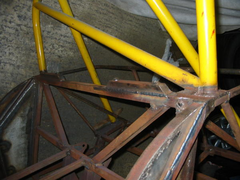 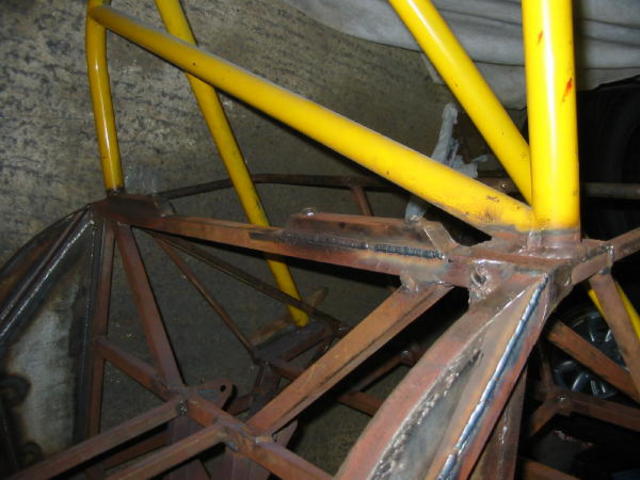 top harness mount
Ned.
beware, I've got yellow skin
|
|
MikeR
|
posted on 29/3/05 at 09:09 PM |
|
|
Thanks for the post ned, youve just answered something thats been bothering me for a while. I can run a hoziontal bar along my roll bar next to the
chassis top rail with the diagonal feeding to the top of that and it will clear where i'll be putting the seat belt mounts.

|
|
ned
|
posted on 29/3/05 at 09:19 PM |
|
|
I was going to weld into the top tube, but due to the diagonal on the underside of the outer mounting points I wouldn't have been able to weld
around the bottom of the inserted threaded tube. The addition of another tube made most sense as it raised the height of the mount, hence killing two
birds etc.
I may also add another vertical member below the top chassis rail inline with the inner mounts to reduce the stress on the top member from the
twisting motion which is now exagerated as the harness mounts are higher hence giving more leverage to twist the top chassis rail under braking/weight
on top harness mounts (hope you're still with me..)
Ned.
beware, I've got yellow skin
|
|